Your packing line feels like a black box. You know coils are moving through, but you lack real-time data. Production reports from the floor don't match the numbers in your ERP system, and this creates constant headaches. You see mismatches in inventory, you deal with unexpected shipping delays, and you spend your day chasing information instead of managing your operations. This disconnect between your physical operations and your digital planning creates chaos. Important decisions are made using outdated information. A coil that your ERP system says is ready for shipment is actually still waiting to be packed. A critical customer order gets delayed because the packing line fell behind, but no one knew about the problem until it was too late. This situation costs you money, it can damage your reputation with customers, and it puts enormous pressure on you and your team. The solution is to build a bridge between your systems. When you integrate your Enterprise Resource Planning (ERP) system directly with your coil packing line, you get real-time visibility and control. This transforms your packing process from a reactive bottleneck into a proactive, data-driven part of your factory.
ERP integration is critical for real-time control of coil packing lines because it synchronizes production data directly with business operations. This link provides instant visibility into packing status, material consumption, and output rates. It allows managers to make immediate, informed decisions that boost efficiency, reduce errors, and align production with actual business demand.

But how does this theoretical benefit translate into practical results on your factory floor? It’s about more than just connecting two systems. It’s about solving real-world problems like production delays, rising costs, and safety concerns. It’s about giving a manager like you the tools to run your plant effectively. Let’s break down exactly how this integration delivers tangible value and helps you meet your goals.
How Does ERP Integration Eliminate Production Bottlenecks?
Your packing line should be the final, smooth step in your process. Instead, it often becomes the biggest slowdown. You see your team waiting for printed work orders. You see operators manually entering data after a job is done. You see finished coils piling up, waiting for packing instructions. These small delays create a massive bottleneck that ripples backward through your entire production schedule. Every minute a finished coil sits waiting to be packed is a minute your expensive slitting or rolling machines are idle, waiting to start the next job. This bottleneck strangles your plant's total output, extends your lead times, and creates frustration for both your team and your customers. You are essentially paying for production capacity that you cannot even use. Direct ERP integration acts like an intelligent traffic controller for your production line. It automates the flow of information. The packing line always knows what coil is coming next, and the rest of the factory knows the real-time status of every packed coil.
ERP integration eliminates production bottlenecks by automating the communication between production planning and the packing line. Instead of relying on manual instructions, the packing machine receives real-time orders directly from the ERP. It processes these orders and reports completion instantly. This creates a seamless, uninterrupted workflow from production to shipping.
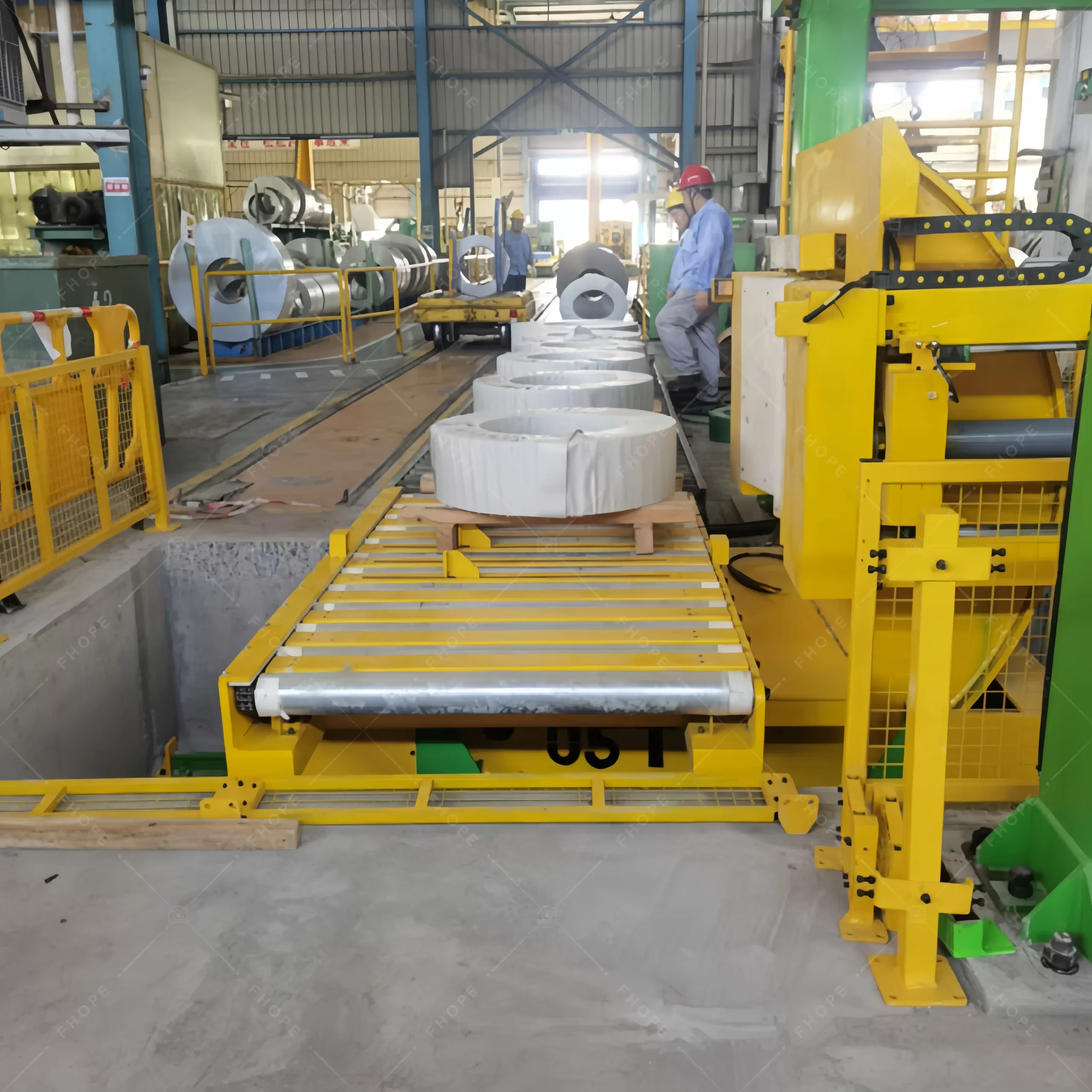
From Manual Chaos to Automated Clarity
In a non-integrated setup, information moves at the speed of people and paper. A supervisor prints a production schedule in the morning. That schedule is carried to the packing line. Operators work through the list. But what happens when a customer calls with an urgent change? Or when a priority shipment needs to be moved up? The plan changes, but the paper on the factory floor does not. This leads to the wrong coils being packed at the wrong time. This is where the bottleneck forms.
I remember visiting a client, a plant manager facing this exact problem. His team would print the daily production list, but by midday, priorities from the sales department would shift. The packing team, however, was still working off the old list from the morning. Unpacked coils for urgent orders piled up, while less important coils were getting packed and taking up space. It created confusion and inefficiency. The moment we integrated their packing line with their ERP, the change was immediate. The packing machine’s queue became a live, dynamic list that was always 100% accurate. The machine and the operators always knew the true priority. The bottleneck vanished in less than a week.
The Power of a Single Source of Truth
ERP integration creates what we call a "single source of truth." There is no more "his version" versus "her version" of the schedule. The ERP system holds the master plan, and the packing machine executes it in real-time. The machine receives the coil ID, automatically pulls the correct packing specifications (the "recipe"), and proceeds with the job. Once the coil is wrapped, strapped, and labeled, the machine sends a completion signal back to the ERP. The inventory is updated instantly. The sales team can see the coil is ready. The shipping department can schedule the truck. Everything is connected.
Process Step | Manual Method (The Bottleneck) | ERP-Integrated Method (The Solution) |
---|---|---|
Job Assignment | Supervisor prints a static list and gives it to the operator. | Machine receives the next job order automatically from the ERP. |
Get Packing Specs | Operator looks up specifications in a binder or computer file. | Machine scans the coil ID and instantly pulls the correct recipe from the ERP. |
Data Entry | Operator manually writes down completion time and materials used. | Machine automatically records all data and sends it to the ERP. |
Inventory Update | Supervisor enters the data into the ERP at the end of the shift. | Inventory is updated in real-time the moment packing is complete. |
This seamless flow of information doesn't just speed things up. It makes the entire operation more predictable and manageable.
What Are the Real-Time Data Points That Drive Down Costs?
You know you are losing money from small inefficiencies, but it is hard to track where. How much stretch film was actually used on the last shift? Why did one steel coil take 10 minutes to pack while a similar one took 20 minutes? The answers are often buried in messy paperwork or are simply lost. This lack of clear data means you cannot optimize your process. You might be over-ordering expensive wrapping film. You are certainly paying for labor that is not fully productive. And you may be suffering from product damage due to inconsistent packing, which leads to customer complaints and profit loss. When you manage without data, you are flying blind on your operational costs. An integrated system captures precise data points in real-time. It gives you the information you need to make targeted, effective cost-cutting improvements. It turns your packing line from a cost center into a source of valuable business intelligence.
The key real-time data points that drive down costs include precise material consumption per coil, cycle time for each packing job, machine downtime, and operator performance. This data, fed directly from the packing machine to the ERP, allows for accurate cost allocation, better inventory control of consumables, and clear identification of efficiency losses.

Tracking Every Gram and Every Second
Without integration, cost analysis is based on averages and estimates. You might calculate the average amount of stretch film used per month and divide it by the number of coils packed. But this doesn't tell you the whole story. It doesn't tell you if larger coils are being wrapped properly or if too much film is being wasted on smaller coils. With an integrated system, you can track everything with precision. The wrapping machine knows exactly how many meters of film and how many straps were used for each specific coil. It records the exact cycle time from the moment the coil arrived to the moment it left. It logs any downtime or errors that occurred. This detailed data is then attached to the coil's record in the ERP.
I worked with a factory in Mexico that was consistently over budget on their packing materials. Their estimates told them they should be using a certain amount of stretch film, but their monthly purchasing bills were always 15% higher. They couldn't figure out why. After we integrated their wrapping machine with their ERP, they could finally track film usage per coil. The data showed the problem immediately. The machine's tension settings were optimized for their largest coils, but they were using the same wasteful settings on smaller, lighter coils. A simple adjustment to the packing recipes, guided by the new, real-time data, saved them thousands of dollars a month. That is the power of visibility.
From Raw Data to Actionable ROI
Data by itself is just numbers. The real value comes when you use that data to make smart decisions that improve your Return on Investment (ROI).
Data Point | What It Measures | How It Reduces Cost |
---|---|---|
Cycle Time per Coil | The exact time it takes to pack each product. | Helps identify slow processes, needs for operator training, or machine maintenance issues. |
Material Consumption | Precise amount of film, straps, and labels used. | Prevents waste, allows for accurate inventory management, and enables precise job costing. |
Downtime Logs | Records every time the machine stops and for how long. | Pinpoints recurring problems, allowing you to schedule predictive maintenance and reduce unplanned stops. |
Error/Alarm Codes | Tracks specific machine errors. | Helps diagnose problems faster, reducing the time technicians spend on troubleshooting. |
When you have this level of detail, you can manage with facts, not guesses. You can confidently invest in improvements because you can measure the before-and-after impact directly on your bottom line. This is how you build a strong business case for new equipment and justify your investments.
Can ERP Integration Actually Improve Workplace Safety?
A safe plant is a productive plant, but the packing area is often a high-risk zone. You have manual handling of heavy steel coils, repetitive motions that can cause strain injuries, and the pressure to meet shipping deadlines. This combination can lead to serious accidents. Every incident means potential harm to your employees, which is the most important concern. It also means costly insurance claims, production stoppages while an investigation happens, and damage to your team's morale. The constant worry about safety is a heavy burden for any plant manager to carry. While we often think of ERP integration as a tool for data and efficiency, its impact extends directly to the safety of your people. By creating a more predictable, automated, and streamlined workflow, it reduces the chaotic and dangerous situations where most accidents occur.
Yes, ERP integration directly improves workplace safety by reducing the need for manual intervention and creating a more controlled, predictable environment. It minimizes the rushed, error-prone manual tasks that lead to accidents. It also automates material handling instructions and provides operational data that can be used to identify and mitigate risks before an incident occurs.

Reducing Haste and Human Error
Many accidents on the factory floor happen because of two things: haste and human error. When the packing line is a bottleneck, operators feel rushed. They might take shortcuts with safety procedures to try and catch up. When information is handled manually, mistakes happen. An operator might grab the wrong work order or misread a packing instruction, leading them to handle a coil in an unsafe way.
ERP integration attacks both of these root causes. Because the workflow is automated and smooth, the constant feeling of being "behind" is reduced. Operators can focus on running the process correctly and safely, rather than rushing to fix a backlog. Because the packing instructions are sent directly from the ERP to the machine, the chance of human error in selecting the wrong procedure is virtually eliminated. The machine gets the right instructions for the right coil, every time. This is especially important for things like tilt or upending stations. The system ensures the right sequence is used for the specific coil's weight and dimensions, preventing dangerous handling mistakes.
Proactive Safety Through Data
A truly safe workplace is proactive, not reactive. It identifies risks and fixes them before someone gets hurt. The data from an integrated system is a powerful tool for proactive safety management.
Safety Hazard | How Manual Process Increases Risk | How ERP Integration Mitigates Risk |
---|---|---|
Incorrect Handling | Operator has to manually look up how to handle a heavy or unusual coil. A mistake can lead to a dropped load. | ERP sends the correct handling protocol directly to the automation system. The machine follows the safe, pre-approved procedure. |
Operator Fatigue | Rushing and repetitive manual data entry causes physical and mental fatigue, a leading cause of accidents. | Automation reduces manual tasks. A smoother workflow reduces stress and the need to rush. |
Unexpected Machine Action | An operator might manually adjust a machine, causing an unexpected movement. | The machine's parameters are set by the ERP. This reduces the need for manual overrides and on-the-fly adjustments. |
As a manager, you can analyze the data to spot potential safety issues. For example, if you see that a certain type of coil consistently has a longer cycle time or generates more machine errors, it could indicate a handling challenge. You can then investigate that specific process and implement engineering controls or provide additional training. This data-driven approach allows you to focus your safety efforts where they are most needed. It helps you build a culture where safety is based on clear information, not just rules in a book. This leads to lower insurance costs, better employee retention, and a more secure, productive workforce.
From My Experience, What's the First Step to a Successful ERP Integration Project?
The idea of a major ERP integration project can feel overwhelming. You have probably heard stories of projects that go way over budget, take months longer than planned, and in the end, fail to deliver the promised results. The technical jargon from IT consultants and software vendors is enough to make any practical plant manager hesitant to start. This fear of a complex project can lead to inaction. You end up sticking with the old, inefficient, and unsafe manual system because it feels less risky than starting something new and complicated. But this means you continue to suffer from all the problems of bottlenecks, hidden costs, and safety risks. You slowly fall behind your competitors who are embracing this technology. As someone who has built a factory from the ground up and helped countless clients implement these systems, I can tell you that the most important first step has nothing to do with technology. It is all about clarity and partnership.
From my experience, the most critical first step to a successful ERP integration is not choosing the software or the hardware. The first step is to clearly and simply define the problem you are trying to solve. You must map out your current packing process, identify the specific bottlenecks and data gaps, and establish clear, measurable goals for what you want the integration to achieve.
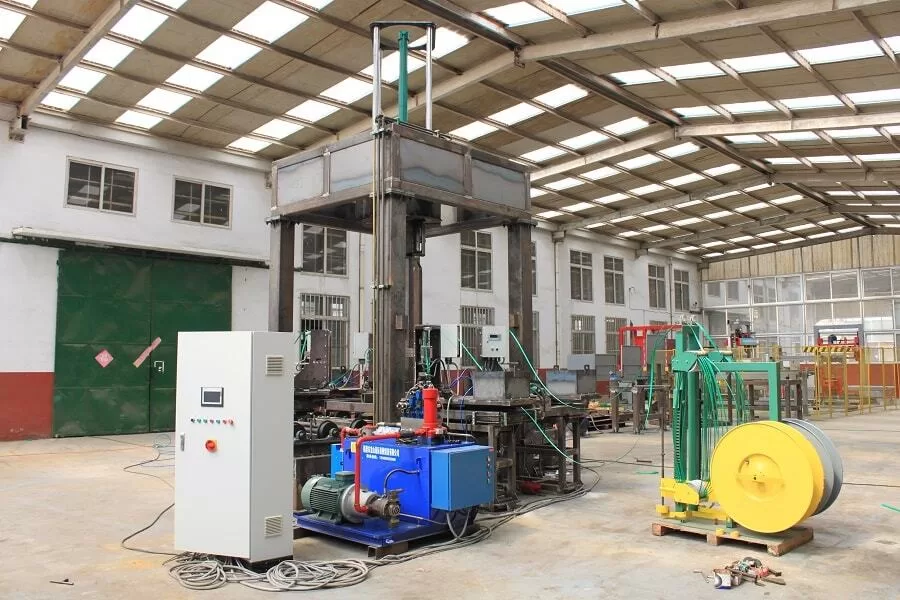
Don't Start with the Technology, Start with the 'Why'
Many companies make the mistake of starting with the technology. They get a demo of a fancy new software and then try to figure out how to use it. This is a backward approach. You must start with your own process. You need to get your team together and walk the factory floor. Draw your entire packing process on a whiteboard, from the moment a coil leaves the slitter to the moment it's loaded on a truck.
Ask these simple questions before you talk to any vendor:
- Where does the process stop? Pinpoint the exact places where coils are waiting. Is it waiting for paperwork? Waiting for an operator? Waiting for space?
- Where does information get lost? Identify the points where data has to be written down, typed in, or verbally communicated. These are your points of failure.
- What one piece of data would be most valuable? If you could have one number in real-time on your screen, what would it be? Cycle time? Material cost per coil? Real-time output versus the plan?
- How will we measure success? Define your goal with a number. For example: "We want to reduce the average packing cycle time by 15%" or "We want to reduce our stretch film waste by 10%."
Only when you have clear answers to these questions are you ready to look for a solution. Now, you are not just buying a machine; you are looking for a tool to achieve a specific, measurable goal.
Finding a Partner, Not Just a Vendor
This brings me to my final point, which is incredibly important. You need to find the right kind of supplier. Many equipment vendors are only interested in selling you a machine. They will talk about features and specifications, take your order, and disappear after installation. This is how you end up with the bad experiences that make managers cautious.
You need a partner, not just a vendor. A true partner is someone with deep industry experience, someone who has been in your shoes. When I started my own packing machine factory, I did it after years of working as an engineer on the factory floor. I know the pressure a Plant Manager is under to control costs, improve output, and keep people safe. That is why our approach at SHJLPACK is different. We start by listening. We want to understand your 'why'. We use our experience to help you map your process and define your goals. Our goal isn't just to install a machine. Our goal is to ensure that machine, integrated with your systems, solves your specific problems and delivers a clear ROI. This is the foundation of a successful project. It builds trust and ensures you get the results you need for your business to grow.
Conclusion
Integrating your ERP system with your packing line is not just a technical upgrade. It’s a strategic move for achieving real-time control, greater efficiency, and sustainable business growth.