You have invested millions in your steel mill. The furnaces are roaring, and the rolling lines are producing high-quality coils. But the final step, the packaging, is a constant headache. The packaging machines, which looked great in the catalog, are constantly breaking down. They were not built for the dust, heat, and relentless pace of a Turkish industrial environment. Each breakdown stops your entire production line. This costs you precious time and money. Even worse, it can damage your reputation with customers who expect their orders on time. I have seen this exact problem many times in my career. The solution is not just buying a "stronger" machine. The solution is a coil packaging line that is designed from the very beginning for the harsh reality of a steel mill.
The most trusted coil packaging lines in Turkey are those specifically engineered with heavy-duty components, advanced automation for consistency, and robust sealing and wrapping technologies. These machines are built to withstand the extreme temperatures, abrasive dust, and continuous 24/7 operation found in Turkish steel mills. The core design principle is reliability and low maintenance, ensuring a seamless and dependable end-of-line process that protects your product and your production schedule.

It's one thing to say a machine is "built for harsh use." But what does that truly mean for your factory's performance and your financial bottom line? How does the right choice in packaging equipment help you solve real-world challenges, like volatile energy costs or the problems of aging equipment? This isn't just about wrapping steel. It is about making a smart investment that becomes a strategic advantage for your entire operation. Let's break down what really matters. I want to show you the details that separate a standard machine from a true industrial workhorse.
Why Do Standard Packaging Lines Fail in Harsh Turkish Steel Mill Environments?
You made a significant investment in a new packaging line. You expected it to perform for years. But after only a few months, it is already showing major signs of wear. The sensors are failing because of dust. The conveyor belts are fraying under the weight of the coils. The control panel overheats constantly. This is more than just a small annoyance. It has become a serious production bottleneck. You are spending far more on maintenance than you ever budgeted for, and your team is frustrated. The simple truth is that a "standard" packaging machine was never designed for the grit, dust, and heat of a real steel mill.
Standard packaging lines fail in harsh Turkish steel mill environments because they are not built to handle the unique combination of abrasive steel dust, high ambient temperatures, heavy coil weights, and the demand for 24/7 operation. Their core components, from bearings and sensors to electrical systems and structural frames, are often under-specified. This fundamental design flaw leads to premature wear, frequent and unpredictable breakdowns, and very high maintenance costs.
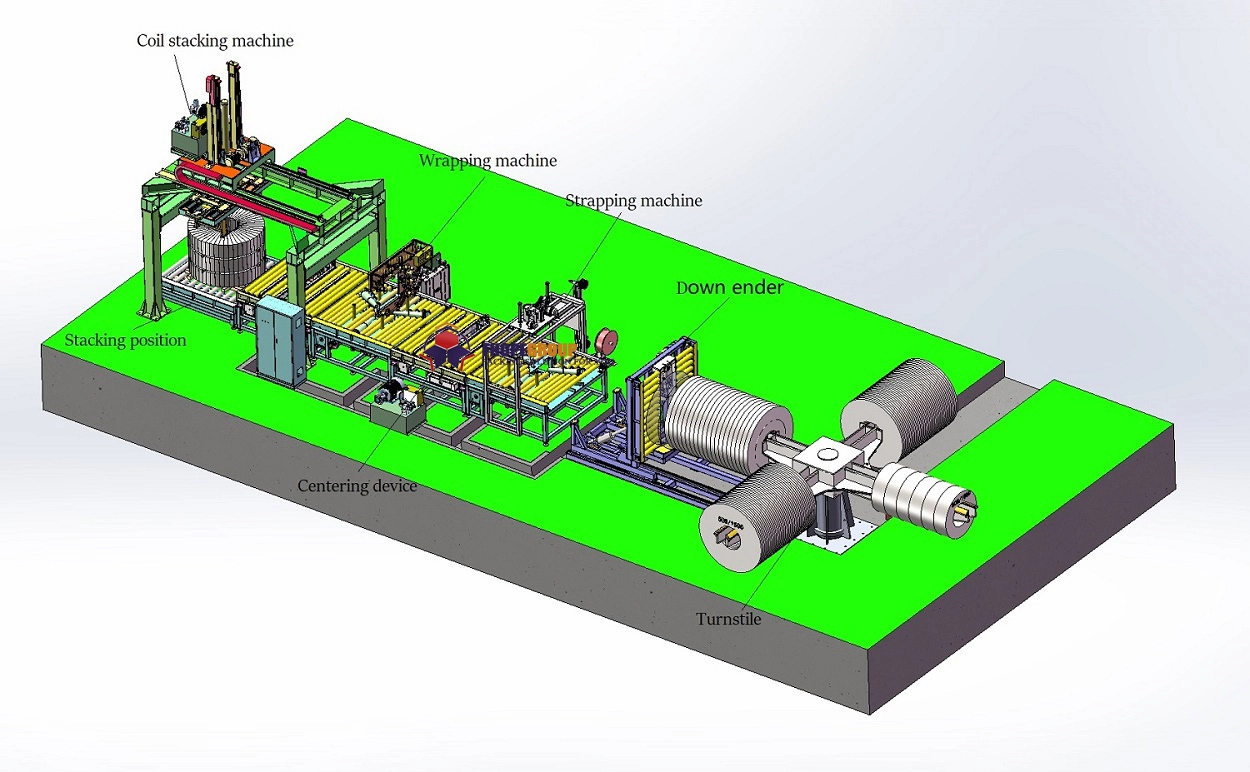
Dive Deeper: The Anatomy of Failure
When I was a young engineer, I visited a mill that had this exact problem. They bought a packaging line from a well-known brand, but it was designed for a clean, air-conditioned warehouse, not a steel plant. It failed constantly. Seeing that situation taught me to look beyond the shiny paint and focus on the fundamental engineering. Let’s dissect why these standard machines break down.
The Enemy Within: Abrasive Dust and Debris
Steel dust is not like regular dust. It is fine, abrasive, and often metallic. It gets into everything. Standard machines use components that are not sealed against this kind of invasion.
- Bearings and Moving Parts: Standard bearings often have simple rubber seals. Abrasive dust works its way past these seals and grinds down the bearing from the inside. This causes friction, heat, and eventual seizure. A purpose-built machine uses triple-sealed or labyrinth-sealed bearings that create a much more difficult path for contaminants.
- Sensors and Electronics: Photoelectric sensors are the "eyes" of the machine. When their lenses get coated in dust, they fail to detect coils, leading to crashes or stoppages. Standard electrical cabinets often have low IP (Ingress Protection) ratings, meaning dust can get inside and coat circuit boards, causing short circuits or overheating. For a steel mill, you need cabinets with a high IP rating (like IP65 or better) and sometimes even a positive pressure air-purging system.
Feature | Standard Machine | Harsh Environment Machine |
---|---|---|
Bearings | Standard ZZ or 2RS sealed | Triple-Labyrinth Sealed, Tapered Roller |
Sensors | Basic Photoelectric Eye | Dust-Penetrating Ultrasonic or Laser Sensors |
Cabinet IP Rating | IP54 | IP65 or IP66, often with air conditioning |
Cabling | Standard PVC insulation | Oil-resistant, high-temp PUR or armored cable |
The Silent Killer: Heat and Vibration
A steel mill is a hot environment. Coils can still be warm when they reach the packaging line. The ambient temperature is high. This heat silently degrades standard machine components.
- Component Degradation: Plastics used for cable tracks, guards, and connectors become brittle and crack. Standard lubricants lose their viscosity and fail to protect moving parts. Electronics not rated for high temperatures will have a dramatically shorter lifespan.
- Constant Vibration: The ground in a steel mill vibrates from the heavy machinery. This constant shaking loosens bolts and electrical connections on a machine that isn't designed for it. I’ve seen control panel doors shake open and fasteners fall out of standard machines. A heavy-duty machine uses vibration-damping mounts, stronger frames, and locking nuts (like Nyloc) on all critical connections.
Understanding these specific failure points is crucial. Choosing the right machine means you are proactively solving these problems instead of constantly reacting to them.
How Can the Right Packaging Line Directly Reduce Your Operational Costs?
Your finance team is always focused on the numbers. They point to the rising costs of electricity, spare parts, and labor. As the owner, you feel the pressure to find savings everywhere. It is easy to focus on the big-ticket items like the furnace or the rolling mill. But the hidden costs in your end-of-line packaging can be silently eating away at your profit margin. An inefficient packaging line wastes energy with every coil, requires constant manual supervision, and burns through expensive wrapping materials. I learned early in my career that building a successful factory is all about efficiency. I believe a modern packaging line is not a cost center; it is a powerful cost-reduction tool. It is specifically designed to minimize energy use, optimize material consumption, and run with very little human intervention. This directly attacks some of your biggest operational expenses.
The right packaging line directly reduces operational costs by incorporating energy-efficient motors with variable frequency drives (VFDs), minimizing the use of wrapping materials through precise tension control systems, and automating processes to lower labor requirements. Furthermore, its inherent reliability and use of predictive maintenance sensors dramatically reduce expensive downtime and spare part costs, contributing to a much lower total cost of ownership.
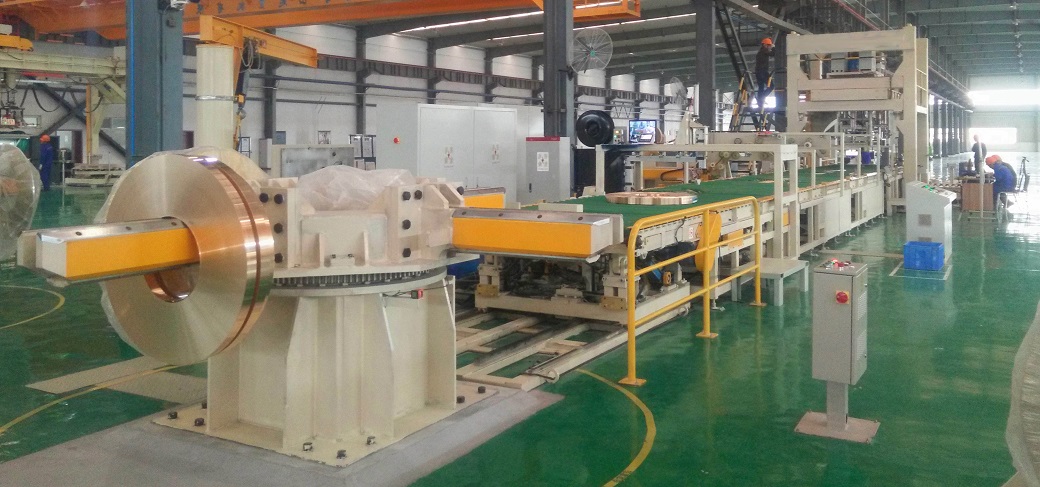
Dive Deeper: Unlocking Hidden Savings
As a business owner, you are focused on metrics like ROI and operational expenditure. A packaging line should be evaluated on the same terms. It must provide a clear return on investment by actively lowering your costs. Let’s look at the specific ways a well-designed line achieves this, moving beyond theory into practical application.
Tackling Energy Consumption Head-On
Energy is one of the largest variable costs in a steel mill. While the packaging line is not the biggest consumer, its inefficiencies add up, 24/7. This is a key area where modern design makes a huge difference.
- Smart Motor Control: Older machines often use motors that run at full speed all the time, even when the machine is waiting for the next coil. A modern line uses high-efficiency motors (IE3 or IE4 standards) paired with Variable Frequency Drives (VFDs). The VFD adjusts the motor's speed to exactly what is needed, which can cut the motor's energy use by 50% or more. During idle periods, the VFD can slow the motor to a crawl or put it to sleep, saving even more energy.
- Regenerative Braking: When a large rotating part, like a wrapping shuttle, needs to slow down, older systems use a mechanical or dynamic brake that turns the excess energy into heat. This is wasted energy. Modern systems can use regenerative braking, where the motor acts as a generator during deceleration, capturing that kinetic energy and feeding it back into the system. It's a small gain on each cycle, but over millions of cycles, it adds up.
Technology | Standard Machine | Cost-Reduction Machine |
---|---|---|
Main Drive Motor | Standard Efficiency (IE1), constant speed | High Efficiency (IE3/IE4) with VFD |
Conveyor Motors | Run continuously at full speed | Run-on-demand with VFD control |
Braking System | Mechanical or Dynamic (wastes energy as heat) | Regenerative (recovers energy) |
The Smart Use of Consumables
Wrapping film and strapping are direct costs tied to every coil you ship. Using even 10% more than necessary is like throwing money away.
- Powered Pre-Stretch: This is one of the most important features. A standard stretch wrapper just pulls the film around the coil. A powered pre-stretch system uses two rollers rotating at different speeds to stretch the film before it's applied to the coil. A good system can stretch the film by 200-300%. This means one meter of film from the roll becomes three or four meters of wrapped film. It drastically cuts your film consumption and creates a tighter, more secure wrap.
- Precise Strapping: A smart strapping head measures the coil and applies the exact amount of tension needed, without over-tightening or wasting strap. It ensures a secure load with minimum material.
These features directly address your goal of reducing overall operating costs by targeting the daily expenses of energy and materials.
What Makes a Coil Packaging Line a Strategic Asset, Not Just Another Machine?
You are looking at a quotation for a new coil packaging line. The number is significant. It is easy to view this as another major expense on your balance sheet, another machine you have to buy, maintain, and eventually replace. This mindset is dangerous. It can lead you to choose the cheapest option available. But as I learned from my own experience building a factory, the cheapest machine is often the most expensive one in the long run. I have worked hard to help my clients shift their thinking. The right packaging line is not an expense. It is a strategic investment. It is a productive asset that protects your product, enhances your brand's reputation with customers, and unlocks new efficiencies that benefit your entire production chain. It becomes a true partner in your growth.
A coil packaging line becomes a strategic asset when it integrates seamlessly with your factory's production management systems (like MES or ERP), provides valuable, actionable data for business decisions, and fundamentally improves the quality and consistency of your final product. At this point, it stops being just a machine and transforms into a critical tool for boosting operational efficiency, guaranteeing customer satisfaction, and supporting your company's long-term goals for profitability and digital transformation.

Dive Deeper: From Cost Center to Value Creator
For a forward-thinking leader like you, every piece of equipment must justify its place in the factory. It must contribute to your larger goals, such as increasing uptime, advancing digitalization, and improving profit margins. A strategic packaging line does exactly that. Here’s how.
The Guardian of Your Quality and Brand
Your brand's reputation is built on the quality of the steel you produce. That reputation can be damaged in the last mile of its journey.
- Preventing Damage: A properly packaged coil is protected from the two biggest enemies of steel: moisture and physical impact. A complete wrap with VCI (Vapor Corrosion Inhibitor) paper or film prevents rust during shipping and storage, especially for international transit. A tight, secure wrap with edge protectors prevents scratches, dents, and telescoping of the coil. When a customer receives a pristine, perfectly wound coil, it reinforces their perception of your company as a high-quality supplier. A damaged coil does the opposite.
- Consistency is Key: An automated line provides the exact same high-quality wrap every single time. This consistency is a hallmark of a professional operation. It eliminates the human variability that can lead to poorly packaged coils.
The Data Hub for Your Digital Transformation
This is where a packaging line truly becomes a 21st-century asset. It is no longer an isolated mechanical island. It is a connected data node in your smart factory. This directly supports your goal of deploying MES, IoT, and big data platforms.
- Seamless Integration: A modern packaging line's PLC (Programmable Logic Controller) is designed to communicate. It can connect directly to your MES (Manufacturing Execution System). It can receive information about the next coil (size, weight, customer specs) and automatically adjust its settings.
- Actionable Data Output: More importantly, it sends critical data back to your systems. This is not just data for the sake of data; it is information you can use to make better business decisions.
Data Point from Packaging Line | Business Insight / Action |
---|---|
Cycle Time per Coil | Track real-time throughput. A sudden increase can signal a developing mechanical issue. |
Film/Strap Consumption | Monitor material costs accurately. Compare usage across different shifts or product types. |
Fault Codes & Stoppages | Identify recurring problems. This data is essential for predictive maintenance. |
Operating Hours / Coil Count | Automate maintenance scheduling based on actual usage, not just the calendar. |
This data provides the full production visibility you are aiming for. You can see your end-of-line performance in real-time on your dashboard, allowing you to manage your factory based on facts, not guesswork. This is the foundation of digital transformation.
My Perspective: From Engineer to Owner, Here's What I've Learned
I started my career as an engineer on the factory floor. I wasn't in an office; I was next to the machines. I saw, with my own eyes, how a multi-million dollar production line could be brought to a complete stop by a single, cheap, unreliable component in the packaging area. The frustration was immense. All that power, all that production, held hostage by a machine that wasn't up to the job. That experience stayed with me.
Later, when I built my own factory, I remembered those lessons. I understood that making an investment is about more than just the initial price. It’s about total cost of ownership, reliability, and peace of mind. Your journey from a team leader to the owner of a major steel mill tells me that you understand this better than most. You carry the weight of the entire operation. You know that you are not just buying a machine; you are investing in the stability of your production, the safety of your people, and the promise you make to your customers.
The conversation about a new packaging line should never start with, "How much does it cost?" It must start with, "What problems do we need this machine to solve for the next 15 years?" We need to talk about your goals for reducing energy consumption, for integrating with your new MES platform, and for running with 95% uptime. The Turkish steel market is world-class, but it is also incredibly competitive. The companies that will thrive are the ones led by people like you, who look beyond the next quarter and invest in robust, intelligent, and efficient systems for the long term.
My goal with SHJLPACK is not just to sell machines. It is to share the knowledge I have gained over a lifetime in this industry. I want to be a strategic partner for leaders like you, helping you build more resilient and profitable operations. Let’s talk about your strategy, not just our specifications.

Conclusion
Investing in a robust coil packaging line is not a cost. It's the final, crucial step in securing your production, protecting your quality, and boosting your long-term profitability.