The Italian steel industry is a cornerstone of European manufacturing, but it faces a perfect storm. I've spoken with many mill owners in Italy, and they all tell me a similar story. They are wrestling with volatile energy costs, aging equipment that's becoming a liability, and increasing pressure to meet stringent environmental standards. Planning for the future feels like trying to navigate a ship in a storm. A single large investment in the wrong kind of equipment can feel like an anchor, locking you into an inflexible process while the market shifts around you. As costs rise and efficiency drops, it becomes harder to compete. But what if your equipment could be as agile as your business strategy needs to be? What if you could invest in a packaging solution that adapts and grows with you? This is the promise of modular coil wrapping machines, a flexible answer for today's uncertainties.
Modular coil wrapping machines offer a powerful solution for Italy's dynamic steel industry by allowing mills to customize, upgrade, and scale their packaging lines in stages. This approach avoids a massive upfront investment, integrates smoothly with existing factory layouts, and adapts easily to new product types, stricter environmental rules, and future automation goals. It is a system designed to evolve with your business, not hold it back.

This idea sounds great, but how does it translate into real-world benefits for a busy steel mill? I understand that you need practical solutions, not just theories. You are focused on daily production targets, budget constraints, and long-term profitability. So, let’s move beyond the concept and break down exactly how a modular approach can solve the specific challenges you face every day on the factory floor. We will explore how this technology directly addresses costs, integrates with the equipment you already own, and prepares your operation for the future.
How Can Modular Design Tackle the Rising Costs in the Italian Steel Sector?
Every steel mill manager I know is constantly fighting a battle against rising costs. Energy prices are a moving target, raw material costs fluctuate, and the pressure to find savings without hurting quality is immense. You scrutinize every line item on the budget, looking for an edge. Traditional packaging machines often add to this pressure. They are typically large, monolithic pieces of equipment. They consume a huge amount of power, even when they aren't working at full capacity. And when they break down, maintenance can be a nightmare, requiring expensive specialists and a long wait for custom parts, all while your production line is stopped. Modular design offers a completely different, and smarter, approach to managing these costs. It allows you to build a wrapping line using only the specific components you need right now, which immediately optimizes your energy use and makes maintenance much simpler.
A modular design directly attacks rising costs in three key areas. First, it allows for phased investment, so you don't need a huge amount of capital upfront. You can start with the core function and add more capabilities later. Second, it cuts down on energy waste because you only power the modules that are actively being used for a specific job. Third, maintenance becomes cheaper and faster. Individual, standardized modules can be repaired or replaced quickly, often without stopping the entire packaging process.
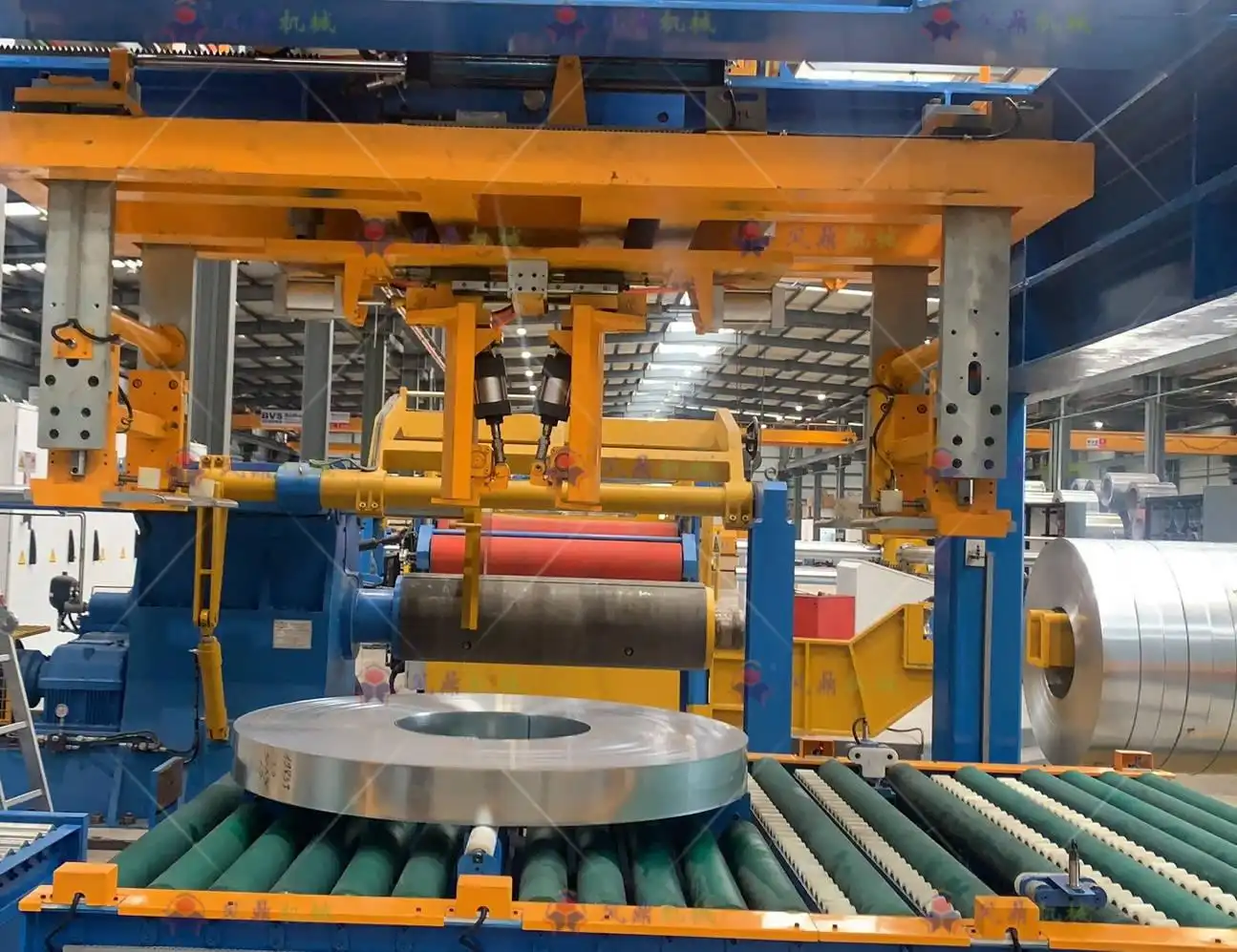
Breaking Down the Cost Savings
From my years as an engineer and now as a factory owner myself, I know that a machine's price tag is only the beginning of the story. The true cost of ownership includes capital, energy, maintenance, and parts. A modular system is designed to minimize all of these.
Let's first look at the initial investment, or Capital Expenditure (CapEx). A traditional, all-in-one machine forces you to pay for every possible feature upfront, even if you won't need some of them for years. It's a massive, one-time expense. The modular approach is different. It's like building with LEGOs instead of carving a statue from a single block of marble. You can start with the essential wrapping unit. This gets your basic packaging automated immediately. Later, as your budget allows or as you win contracts with new packaging requirements, you can add other modules. You might add an in-feed conveyor, an automatic strapping unit, or a labeling system. I remember a client in the steel wire industry who started with just our core packing machine. A year later, they added our automatic coiling and strapping system to create a fully integrated line. They spread their investment over time, matching their cash flow and business growth.
Next is Operational Expenditure (OpEx), which is where modular systems truly shine. Energy is a huge factor. A large, monolithic machine often uses one giant motor to power everything. It draws a massive amount of power, whether it's wrapping a small 1-ton coil or a large 10-ton one. A modular system uses smaller, independent motors for each section. The conveyor runs on its own power, as does the wrapper and the strapper. If you're only wrapping a coil, only the wrapper's motor is running at full tilt. This targeted energy use can lead to significant savings, helping you reach those tough energy reduction goals.
Finally, think about maintenance and spare parts. A large, custom-built machine requires custom-built parts. They are expensive and can have long lead times. With a modular system, the parts are standardized. The same motor or sensor might be used across several different modules. This means you can keep a smaller, cheaper inventory of spare parts. And if a single module fails, like a section of the conveyor, you can often isolate it, or even swap it out quickly, without shutting down the entire operation. This drastically reduces downtime and keeps your products moving.
Cost Factor | Traditional Monolithic Machine | Modular Wrapping System |
---|---|---|
Initial Investment | High, all-in-one cost | Low, phased investment possible |
Energy Consumption | High, constant power draw | Optimized, based on active modules |
Maintenance | Complex, specialist needed, long downtime | Simple, module swap-out, shorter downtime |
Spare Parts | Custom, expensive, large inventory | Standardized, cheaper, smaller inventory |
Scalability | Limited or impossible | High, easily add new functions |
Can Modular Wrapping Machines Integrate with Existing Aging Production Lines?
Your plant is filled with equipment that has served you well for years. Maybe you have a slitting line or a crane system that is over 15 years old. It’s a workhorse, but it’s from a different era. It doesn't communicate with modern systems, and it creates a bottleneck in your workflow. The thought of ripping out this entire line and replacing it is overwhelming. The cost would be enormous, and the production shutdown would be even more painful. But doing nothing is also a risk. Inefficiency grows, safety concerns mount, and you fall behind competitors who are embracing automation. This is a common problem, and modular machines are designed to be the perfect solution. They act as a bridge, connecting your proven, older equipment with modern efficiency and data capabilities, all without forcing you to start from scratch.
Yes, modular wrapping machines are specifically designed to integrate with existing and even aging production lines. Their flexibility is their greatest strength. The layout can be customized. We can design entry and exit conveyors to match the exact height and position of your current equipment. More importantly, their control systems are adaptable. They can be configured to "talk" to older PLCs using simple signals, or they can be fully integrated into a modern plant-wide MES platform. It’s about fitting into your world, not forcing you to rebuild your world around our machine.

The Art of Integration
I spent many years on factory floors, sketching out layouts and solving logistical puzzles. I know that no two plants are the same. Space is always tight, and existing equipment creates fixed points that you have to work around. This is where the "art of integration" comes in, and it's something modular design makes possible.
First, there is the physical integration. A traditional machine has a large, rigid footprint. If it doesn't fit, you have to change your plant. A modular system is different. It’s a collection of components—conveyors, turntables, tilters, and the wrapping unit itself. We can arrange these pieces to fit into challenging spaces. We can create L-shaped or U-shaped lines to navigate around building columns or other machinery. I once worked with a client in Italy whose packing area was long and narrow, with very little room. We designed a line where the coils came in on one side, were lifted and wrapped, and then exited on a conveyor running parallel to the entry point. A monolithic machine would never have fit.
Second, and perhaps more important for the future, is the control system integration. This is how you bridge the gap between old and new technology. Your 20-year-old slitter might not have a modern communication protocol, but it can send a simple electrical signal when a coil is ready. The PLC of our modular wrapping machine can receive that simple "coil ready" signal. Once it gets that signal, it takes over, managing the entire automated sequence: conveying the coil, wrapping it to precise specifications, strapping it, and moving it to the exit station. We can also add modern IoT sensors to the modular line. These sensors can track cycle times, material consumption, and machine health. This data can then be fed into a new MES or analytics platform, giving you clear visibility into a part of your process that was previously a "black box." You are essentially making your old equipment smarter without having to replace it.
This enables a strategy of phased modernization, which is very powerful for managing budgets and minimizing disruption.
- Step 1: Replace a dangerous or slow manual packing process with a standalone modular wrapper. This gives you an immediate win in safety and consistency.
- Step 2: A few months later, add automated conveyors to feed the machine, reducing your reliance on overhead cranes and freeing up operators.
- Step 3: Next, integrate an automatic strapping and labeling module to create a fully finished package ready for shipping.
- Step 4: Finally, connect the entire line's control system to your plant-wide network to achieve full production visibility.
This step-by-step approach breaks a massive project into manageable, affordable pieces.
What Makes a Modular System a Future-Proof Investment for Italian Steel Mills?
The steel market is in constant motion. Your customers' demands change. One year, your biggest contracts might be for standard rebar for the construction sector. The next year, you could win a major order from an automotive manufacturer who requires high-spec steel coils with very specific, protective packaging. If you invest a huge amount of capital in a machine that is only good at one thing, you are taking a massive gamble. What happens if the market shifts away from that one thing? What if a new, more sustainable packaging material becomes the industry standard? Your expensive, specialized machine could quickly become a relic. A true future-proof investment is not one that claims to predict the future, but one that is built to adapt to it. A modular system is, by its very nature, designed for adaptation. It's ready for what's next.
A modular system is a future-proof investment because it is built on three pillars: scalability, upgradeability, and adaptability. As your business grows or your product mix changes, you can add, remove, or upgrade individual modules. For instance, you could add a specialized VCI paper dispenser to bid on contracts for corrosion-sensitive steel, or you could upgrade your strapping head to a newer model that uses less material. You do this without throwing away your initial investment in the core system. This protects your capital and ensures your packaging line can evolve right alongside your business strategy.

Building for Tomorrow's Steel Industry
When I founded my company, SHJLPACK, my goal was to provide total solutions, not just machines. A key part of that philosophy is helping my clients prepare for the future. The Italian steel industry is known for its quality and diversity, serving everything from construction to high-fashion appliances. Your packaging line needs to be able to handle that diversity.
Let's talk about adaptability to market demands. You might start by producing coils for local construction, which only require a basic stretch film wrap for protection. Our basic modular wrapper handles this perfectly. Then, an opportunity arises to supply a major automotive parts manufacturer. Their standards are much higher. They require VCI paper to prevent any chance of corrosion and a layer of thick plastic sheeting for physical protection. With a monolithic machine, you might have to say no to this contract. With a modular system, you simply add a VCI paper dispenser module and a top sheet dispenser module to your existing line. You can now serve this new, higher-margin market. The system adapts to your business opportunities.
Technology also evolves. The strapping head that was state-of-the-art five years ago has likely been surpassed by a newer model that is faster, more reliable, and uses less plastic. With an integrated, old-style machine, you are stuck with the old technology. In a modular system, the strapping unit is its own self-contained module. You can unbolt the old one and install a new, upgraded one in its place. This is also true for the brains of the operation—the control system. As Industry 4.0 becomes a reality, you will need your machines to communicate using new protocols like OPC-UA to connect with plant-wide AI scheduling platforms and robotic systems. A modular control system can be updated or replaced to ensure it stays current with the latest digital manufacturing standards. It’s a machine that learns and grows with technology.
Future Challenge | Monolithic Machine Response | Modular System Response |
---|---|---|
New Customer Packaging Spec | Difficult or impossible to change | Add or change a specific module |
New Packaging Material (e.g., paper) | Requires extensive, costly modification | Add a new dispenser module to the line |
Desire for More Automation | Limited by original fixed design | Easily add robotic pick-and-place or AGV integration |
Upgrading Control System/Sensors | Costly, complex system-wide refit | Simple and fast module-level upgrade |
How Does Modularity Support Italy’s Push for Greener Steel Production?
The pressure for sustainable manufacturing in Europe, and particularly in Italy, is not just a trend; it's a core business requirement. Governments are implementing stricter environmental regulations. More importantly, your customers—from large automakers to appliance manufacturers—are demanding greener supply chains. They are looking at your entire operation, including how you package your products. Your packaging process can be a hidden source of waste, from consuming too much energy to using materials that can't be recycled. Ignoring this can lead to penalties, but it can also mean losing business to a competitor with a better environmental story. A modern, modular approach to packaging is an inherently greener choice that helps you meet your sustainability targets.
Modularity supports greener steel production in several direct ways. It optimizes energy use by ensuring that only the necessary machine sections are powered for a given task, which lowers your overall carbon footprint. It reduces material waste through precise, programmable control over the application of stretch film and other wrapping materials. Crucially, it also allows you to easily integrate new modules that handle emerging, sustainable packaging materials, like recyclable paper wraps, as they become available and demanded by the market.
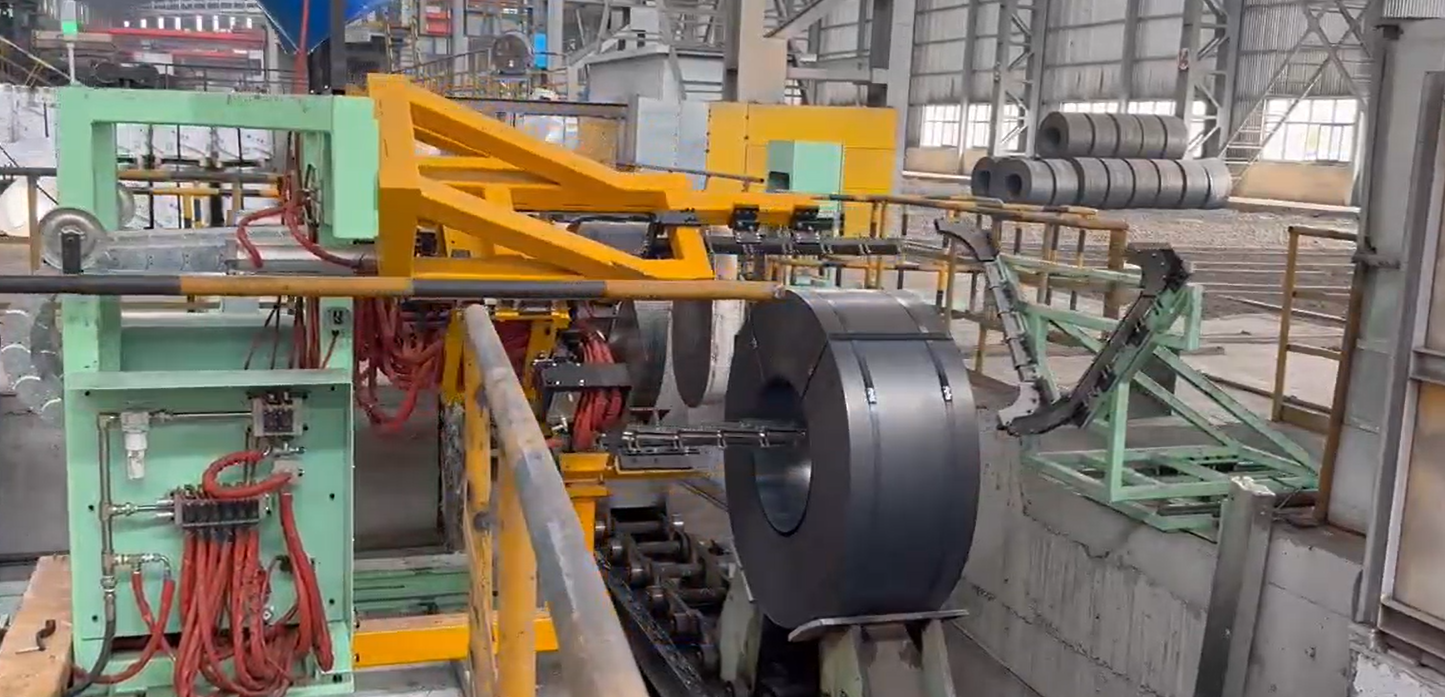
Packaging's Role in a Circular Economy
Sustainability is about more than just looking good on a report; it's about real efficiency that impacts the bottom line and the planet. I believe that smart packaging is a critical, and often overlooked, part of a steel mill's environmental strategy.
First, let's revisit energy efficiency from a green perspective. As we discussed, a modular line uses less electricity because it only powers the components needed for the job. This isn't just a cost saving; it's a direct reduction in your factory's carbon footprint. For every kilowatt-hour you save, you are contributing to Italy's national energy goals and demonstrating to your stakeholders that you are serious about reducing your environmental impact. This directly supports the goal of lowering unit energy consumption across your entire operation.
Second is the critical issue of material reduction. I have seen older machines or manual wrapping processes that use far too much stretch film. The philosophy is often to add extra layers "just to be safe." A modern, programmable wrapping module is precise. You can set the exact number of layers, the overlap percentage, and the tension. This ensures the coil is secure while using the absolute minimum amount of material necessary. This reduces your plastic consumption significantly. Furthermore, a modular design makes it easy to adapt to new, greener materials. If a customer requires a biodegradable or paper-based wrap, you don't need a whole new machine. You can simply add a module designed to handle that specific material.
Finally, we must consider the biggest waste of all: a damaged product. The entire purpose of packaging is to protect the steel coil on its journey. If a coil gets rusted or damaged due to poor packaging, all the energy, resources, and labor that went into producing that steel are wasted. It becomes scrap. By using a modular system to create the right protective package—perhaps by adding a VCI paper module for rust prevention and a sturdy strapping module for stability—you are preventing that ultimate waste. You are ensuring that the valuable product you manufactured reaches the customer in perfect condition. That is a core principle of a sustainable, circular economy.
My Insight
When I started my career as a young engineer on the factory floor, we saw machines as simple tools. They were designed to be big, powerful, and to do one job for 30 years. But the world, and the steel industry, is not that simple anymore. It's faster, more demanding, and less predictable.
A steel mill owner today isn't just buying a machine to wrap coils. They are investing in something much more important: flexibility. They are buying the ability to say "yes" to a new customer with unique requirements. They are buying the resilience to adapt to a new environmental regulation without a massive crisis. They are buying the agility to survive a market downturn and the readiness to capture all the opportunities of an upswing.
This is why I believe so strongly in modular design. To me, it is more than just an engineering concept; it's a business philosophy. It is about building a resilient, adaptable operation. The goal is not to try and perfectly predict the future five or ten years from now. The goal is to build a system that is ready for any future. This changes the relationship between a machine builder and a steel mill. It's how we at SHJLPACK move from being just a supplier to being a true partner in our clients' long-term success. My mission is not simply to sell you a wrapping machine. It is to provide a total solution that helps secure your business for years to come.
Conclusion
Modular coil wrapping machines are not just equipment. They are strategic, flexible assets that empower Italian steel mills to cut costs, integrate technology, and build a sustainable, future-proof business.