Your U.S. steel factory is under pressure. Global competition is tough. Labor costs are rising. And your customers expect perfect quality, every time. You have likely invested heavily in your production lines, but the packaging area at the end often gets overlooked. This creates a hidden bottleneck. It causes delays, damages products, and hurts your reputation. This is not just a small problem. Every minute your line is down and every coil that gets damaged costs you money. You are working hard, but these inefficiencies are slowly eating away at your profits. What if you could change this? What if your packaging line became a source of strength, not a weakness? Next-generation technology can make your packaging faster, safer, and more cost-effective.
Yes, your U.S. factory is ready for next-gen steel coil packaging technology if you face challenges like high operational costs, production bottlenecks, or inconsistent package quality. Adopting automated and integrated systems is no longer a choice but a necessary step. It helps you stay competitive, improve safety, and meet the demands of the modern market.

I have spent my entire career in this industry. I started on the factory floor and eventually built my own company, SHJLPACK. I have seen firsthand how the right equipment can transform a business. Being ready for this technology is the first step. The next step is understanding how it can solve your specific problems. Let's look at the key questions you should be asking. We will explore how these new solutions can make a real difference in your daily operations.
How Can Automation Reduce Your Reliance on Manual Labor and Cut Operational Costs?
Finding good people for the packaging line is a constant challenge. The work is physically demanding and repetitive. This leads to high turnover and the constant need for training. Manual packaging is also slow and can be inconsistent. This increases the risk of workplace injuries, which drives up your insurance costs. Every shift, you are dealing with the possibility of human error. A coil that is not strapped correctly can get damaged in transit. This leads to expensive customer claims and hurts your reputation. You feel stuck in a cycle of hiring, training, and dealing with preventable mistakes. Automated packaging systems offer a direct solution. They work around the clock with precision. They reduce the need for difficult manual tasks and create a much safer environment for your team.
Automation directly cuts operational costs by minimizing the need for manual labor in repetitive tasks like coil wrapping, strapping, and labeling. This reduces expenses for wages and training. It also significantly lowers the risk of human error, product damage, and workplace accidents. The result is a more predictable and efficient operation.
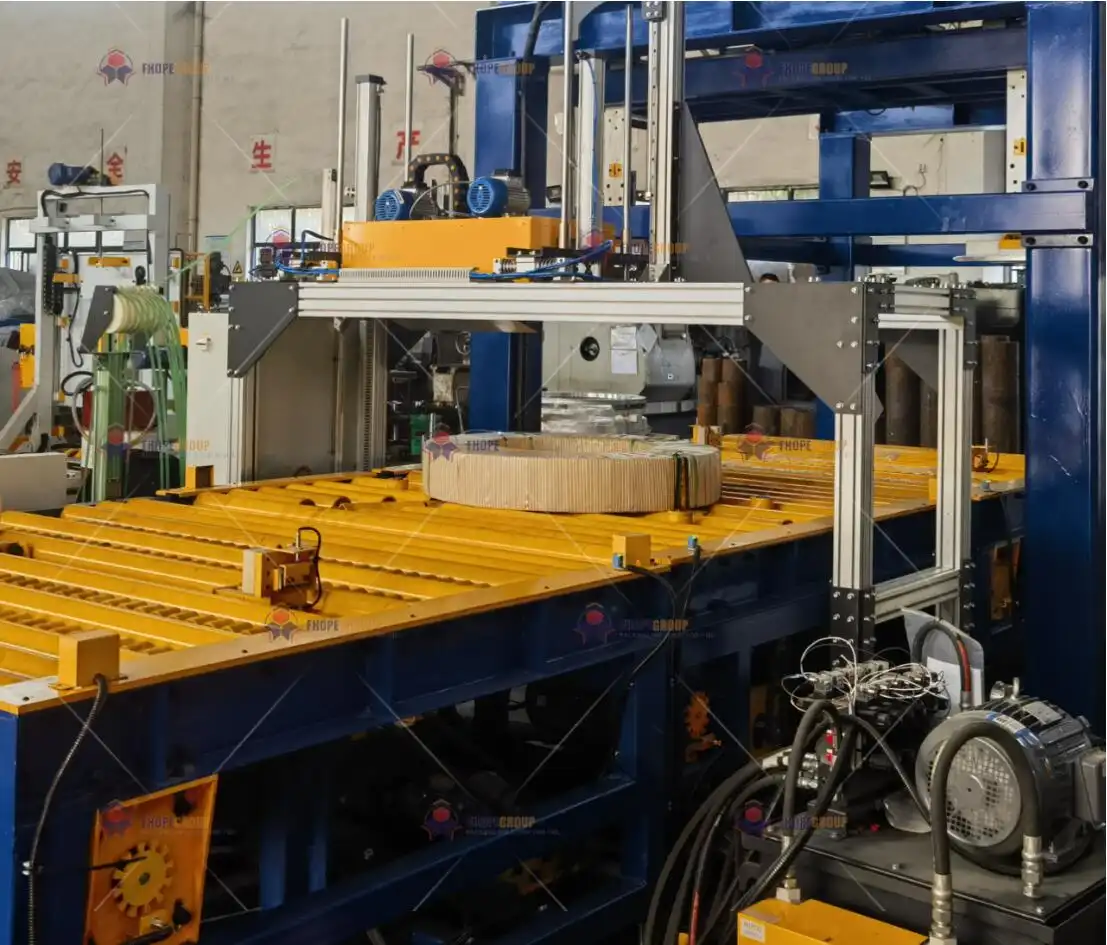
The True Cost of Manual Packaging
When we think about labor costs, we often just think about salaries. But the real costs go much deeper. I remember visiting a steel service center in Indiana. The manager was proud of his experienced team, but his numbers told a different story. His costs for rework and shipping damage were alarmingly high. The problem was not his people; it was the manual process itself. It is impossible for a person to wrap every coil with the exact same tension and overlap, day after day. This is where the hidden costs appear.
Cost Category | Manual Process Challenges | Automated System Benefits |
---|---|---|
Direct Labor | High wages for physically demanding work. | Reduces the number of operators needed. |
Training & Turnover | Constant need to train new employees. | Consistent operation regardless of operator. |
Workplace Injuries | Risk of strains and other injuries. | Eliminates dangerous manual handling. |
Inconsistency | Varies by operator, shift, and fatigue. | Every coil is packed to the same standard. |
Product Damage | Improper wrapping or strapping leads to loss. | Precise application protects the product. |
Material Waste | Operators may use too much film or paper. | Uses the exact amount of material needed. |
Where to Start with Automation
Implementing automation does not have to be an all-or-nothing decision. You can start with the areas that cause the most problems. For many U.S. factories, the biggest gains come from automating a few key tasks. An automated coil upender can safely tilt a coil from eye-to-sky to eye-to-horzontal, a task that is slow and dangerous to do with a crane. An automatic strapping machine applies straps with perfect tension every time, which is critical for coil integrity. Robotic wrapping arms can apply stretch film flawlessly, protecting the coil from moisture and dirt. These are not just machines; they are solutions to specific operational headaches. They solve the problems of safety, consistency, and efficiency all at once. I helped a client in Ohio integrate an automatic strapping machine into his line. He was worried about the investment. But within 18 months, his savings from reduced labor and zero shipping damage paid for the machine completely.
Can Integrated Systems Truly Boost Your Production Uptime to 95%?
Your main production line is a high-speed, well-oiled machine. But what happens when the coils reach the packaging area? Often, it becomes a traffic jam. The process is broken into separate steps. A finished coil sits and waits for a wrapping machine. Then it waits for a strapping machine. Then it waits for a crane or forklift to move it. Each of these waiting periods is lost time. It creates a major bottleneck that slows down your entire plant. This stop-and-go process makes it impossible to achieve a smooth, continuous flow. Your overall plant efficiency suffers because it is being held back by the slowest part of the process. You can never reach a high uptime target, like 95%, when your packaging operations are disconnected and inefficient. An integrated packaging line solves this problem. It connects all the steps into a single, seamless system. Coils move automatically from one station to the next, controlled by a central system. This eliminates the waiting time and maximizes your output.
Yes, integrated systems can significantly boost production uptime toward the 95% goal. By connecting individual machines like coil cars, wrappers, and strapping stations into one seamless line, you eliminate bottlenecks and waiting periods. This continuous flow ensures the packaging process keeps pace with production, preventing upstream delays and maximizing overall equipment effectiveness (OEE).
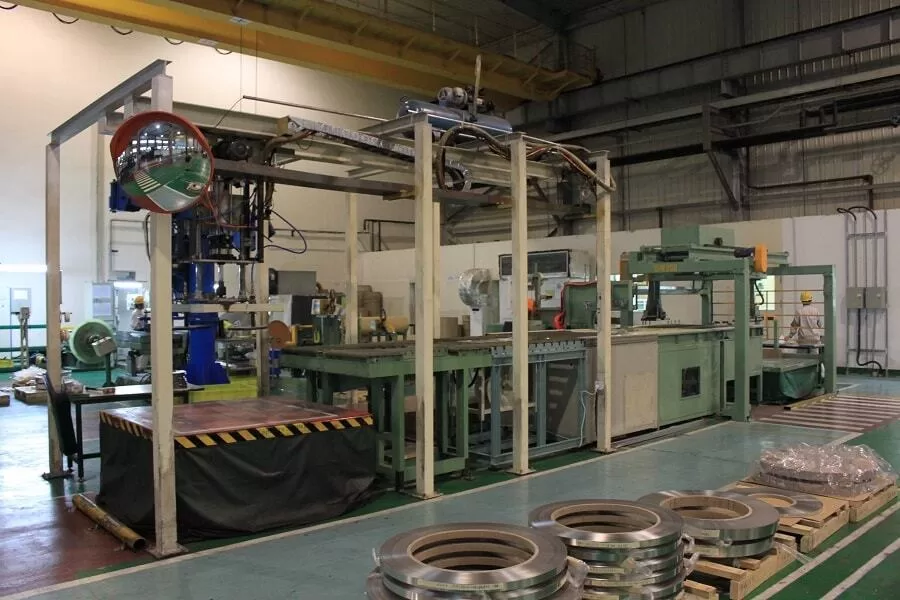
From Separate Steps to a Single Flow
The difference between a collection of standalone machines and a fully integrated line is huge. Think about your current process. It likely involves a lot of starting and stopping. An integrated line transforms this into a smooth, continuous operation. The goal is to make the packaging process as efficient as your production line.
Let's compare the two approaches:
Step | Standalone Process | Integrated Line |
---|---|---|
Coil Entry | Crane or forklift places coil. (Wait time) | Coil car automatically receives and positions coil. |
Wrapping | Operator starts manual or semi-auto wrapper. | Conveyor moves coil into automated wrapper. |
Strapping | Coil is moved to a separate strapping area. (Wait time) | Conveyor moves coil to automated strapping station. |
Weighing/Labeling | Coil is moved to a scale. (Wait time) | In-line scale and label applicator. No stopping. |
Exit | Forklift removes finished coil. (Wait time) | Conveyor moves coil to holding area for pickup. |
As you can see, the "wait time" is eliminated in an integrated line. This is how you reclaim lost minutes and push your uptime higher.
The Power of Predictive Maintenance
Achieving 95% uptime is not just about speed. It is also about reliability. You cannot afford unexpected breakdowns. This is another area where modern integrated systems have a huge advantage. They are built with sensors that monitor the health of the equipment. These sensors track things like motor temperature, vibration, and cycle counts. This data can be used for predictive maintenance. Instead of waiting for a machine to break, the system can alert you that a component is wearing out and needs to be replaced soon. You can schedule the repair during planned downtime, instead of having a surprise failure in the middle of a production run. I worked with a large steel mill that was struggling with downtime on their old packaging equipment. After we installed an integrated line with predictive maintenance features, their unplanned downtime in the packaging area dropped by over 80%. This was a game-changer for their overall plant efficiency. It is about moving from being reactive to being proactive.
What Role Does Data Play in Modernizing Your Coil Packaging Line?
As a factory owner or manager, you make decisions every day. But what are those decisions based on? Often, it is based on experience, intuition, and what you can see on the factory floor. You might feel like you have a good handle on things, but you lack hard data. You probably cannot say exactly how many seconds it takes to package each coil, or how much wrapping film you used last week, or why coils from one slitter seem to get damaged more often. Without this data, you are operating with blind spots. You cannot accurately identify where your process is inefficient. You cannot justify new equipment investments with a clear, data-backed ROI. You might be wasting money on excess packaging materials or using the wrong strapping tension, but you have no way to systematically prove it or fix it. Modern packaging lines are different. They are smart. They have sensors that connect to your plant's Manufacturing Execution System (MES). They produce a constant stream of useful data, turning your packaging line from a cost center into a source of business intelligence.
Data plays a critical role in modernizing your coil packaging line by providing complete visibility into the process. By collecting information on cycle times, material consumption, and equipment status, you can identify inefficiencies, optimize performance, track every coil, and implement data-driven strategies for predictive maintenance and quality control. This transforms your packaging operation from a black box into a transparent, manageable system.
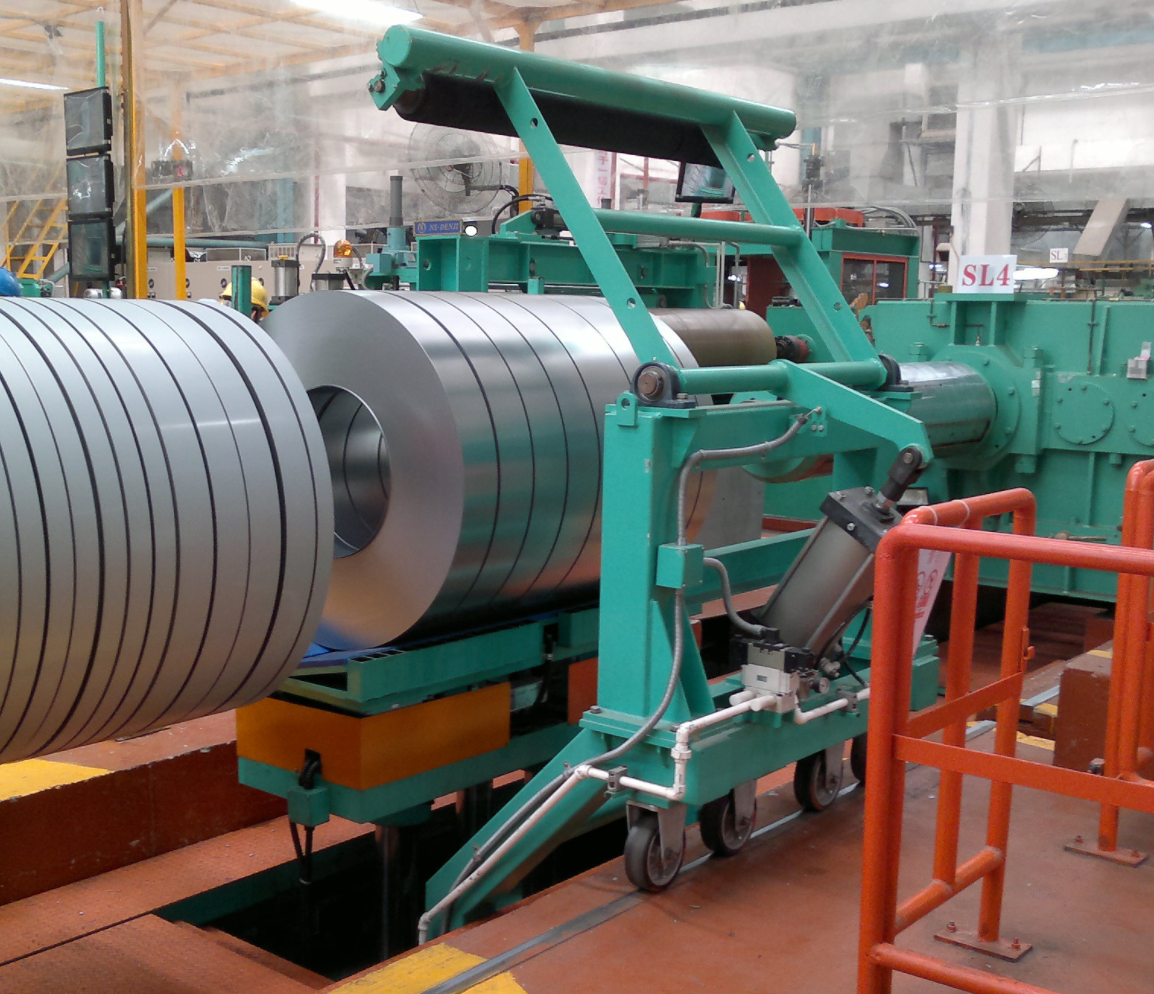
Turning Information into Action
Having data is one thing; knowing what to do with it is another. A modern packaging line can give you a dashboard with key performance indicators (KPIs). This is not just a bunch of numbers. This is actionable information that helps you improve your business.
Here are some of the most important data points to track:
- Cycle Time Per Coil: How long does the entire packaging process take for each coil? If this number starts to increase, it is an early warning of a problem.
- Material Consumption: Are you using the programmed amount of stretch film and strapping? This helps you control costs and spot waste.
- Equipment Downtime: When a machine stops, the system should log the reason why. This helps you identify and fix recurring problems.
- Packaging Recipe: The system can store different packaging instructions for different customers or product types. This ensures everyone gets exactly what they ordered.
Integration with Your Factory's Brain
The real power of data comes when you connect your packaging line to your larger factory systems, like your MES or ERP (Enterprise Resource Planning). This is a key part of digital transformation. When a coil is finished and packaged, the packaging line can automatically send a signal to your ERP system to update the inventory. It is now ready to ship. This eliminates manual data entry and reduces errors. Imagine another scenario: The data shows that coils with a certain width have a slightly higher rate of strapping issues. This information can be sent to the MES. You can then investigate the slitter that produced those coils. Maybe the edge quality is not perfect. Without data, you would just blame the strapping machine. With data, you find the root cause of the problem. This is how you move from just fixing problems to preventing them from ever happening. It is a more intelligent way to run your factory.
How Does Advanced Packaging Technology Improve Product Safety and Meet Compliance Standards?
There are few things worse than getting a call from a customer about a damaged shipment. A coil that arrives rusted, dented, or telescoped is a major problem. It leads to expensive returns, customer claims, and, worst of all, damage to your hard-earned reputation. At the same time, you are facing increasing pressure to meet safety and environmental rules. These regulations are always changing, and keeping up with them can feel like a full-time job. The consequences of failing are serious. A single rejected shipment can erase the profit from dozens of good ones. Failing a safety or environmental audit could lead to large fines or even force you to stop production. You simply cannot afford to take these risks in today's market. Next-generation packaging technology gives you control and peace of mind. It provides precise, repeatable, and documented quality. It ensures that every single coil is wrapped and strapped according to exact engineering specifications, protecting it during its journey. It also creates a verifiable digital record for compliance purposes.
Advanced packaging technology improves product safety by applying wrapping and strapping with consistent, engineered precision, which minimizes damage during handling and transport. It helps meet compliance standards by providing documented proof of proper packaging procedures, using recyclable materials, and reducing waste, which is essential for both customer requirements and environmental regulations.
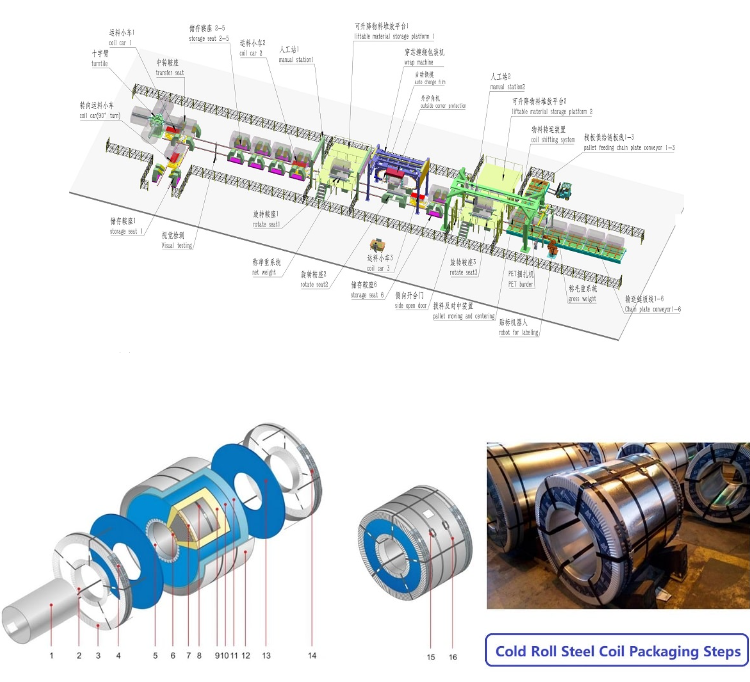
The Engineering Behind a Perfect Package
Properly packaging a steel coil is a science. It is not just about covering it up. It is about protecting a valuable and sensitive product from multiple threats. As an engineer, this is the part I find most interesting. Advanced packaging machines are designed based on the physics of coil protection.
- Corrosion Prevention: A perfect wrap with VCI paper or stretch film creates a barrier against moisture. An automated wrapper applies the film with a consistent overlap and tension that is difficult for a person to achieve, ensuring there are no gaps where moisture can get in.
- Shape Integrity: Steel coils, especially slit coils, can telescope or unwind if not handled correctly. Proper through-the-eye and radial strapping holds the coil together. An automated system applies the straps at precise locations with the exact right tension to secure the coil without damaging its edges. Edge protectors can also be applied automatically to prevent damage from the straps themselves.
I have seen clients who were able to offer better shipping guarantees to their customers after upgrading their packaging lines. This became a major selling point for them.
Meeting Modern Compliance Demands
Today's market demands more than just a quality product. Customers and governments want to see a commitment to safety and sustainability. This is where your packaging choices matter. Many U.S. and international customers now have specific packaging requirements. An automated system allows you to create and save a unique "packaging recipe" for each customer and apply it perfectly every time. This demonstrates a high level of professionalism and care. On the environmental side, modern machines are designed to be more efficient. They can use thinner, stronger stretch films, which reduces plastic waste. Many factories are also switching from steel strapping to PET (polyester) strapping, which is recyclable and safer to handle. An automated system also creates a digital paper trail. For every coil, you have a record of how it was packaged, what materials were used, and when it was completed. This data is extremely valuable if you ever need to prove compliance for an audit or resolve a customer dispute.
Conclusion
Adopting next-gen packaging technology is not just an upgrade. It is a strategic move to build a more resilient, efficient, and profitable U.S. factory for the future.