Are you running a steel or wire factory with a layout that feels... restrictive? Many established plants, especially in historic industrial regions like those in Italy, face a common problem: limited floor space. This can make upgrading your equipment feel like an impossible puzzle. You know you need modern, powerful machinery to stay competitive, but the thought of fitting a massive new packing line into your already crowded facility is a major headache. This forces you to stick with older, less efficient equipment that breaks down more often and eats into your profits. But what if there was a way to get all the power and efficiency of a state-of-the-art packing line, specifically designed to fit into the compact footprint of your factory?
A compact and powerful coil packing line is achieved by using smart engineering to integrate multiple functions into single stations, leveraging vertical space, and employing modular designs. This approach allows for high-speed throughput and advanced packaging features without demanding a large, linear footprint. This makes these lines the perfect solution for space-constrained or older factory layouts, like those commonly found in Italy and other established industrial areas.

As an engineer who has spent his entire career on the factory floor, I’ve seen this challenge countless times. I started as an employee, learning every nut and bolt of these machines. Later, when I founded my own factory, SHJLPACK, I had to solve these same problems for my clients. The belief that "compact" means "compromise" is one of the biggest myths in our industry. In reality, a well-designed compact line isn't a downsized version of a standard one; it's a smarter, more efficient solution. Let's explore how we turn the limitation of space into a strategic advantage for your operation.
How Can a Compact Design Deliver Uncompromised Packing Power?
You see a machine described as "compact," and your first thought is likely "less powerful" or "slower." You might assume it has fewer features and can't handle your production volume. This assumption is dangerous because it can stop you from considering a solution that perfectly addresses your space and efficiency issues. It keeps you tied to outdated technology that costs you money every day. But modern engineering has completely changed the game. "Compact" no longer means you have to compromise on performance.
A compact design delivers uncompromised power through intelligent engineering. We use multi-function modules that perform several tasks, like strapping and wrapping, at a single station. We use high-speed servo motors instead of bulky hydraulic systems. We also make clever use of vertical layouts to stack processes. This ensures your packing line has the speed, reliability, and strength you need.

Deeper Dive: Re-engineering Power for Modern Needs
For a long time, "power" in our industry meant bigger, heavier machines. But true power isn't just about brute force or raw speed. It's about precision, reliability, and delivering a perfectly protected product to your customer every time. A packing line that is fast but damages coils or applies wrapping inconsistently isn't powerful; it's a liability. Modern compact designs focus on delivering effective power where it counts.
The Shift from Bulky Hydraulics to Smart Electrics
One of the biggest enablers of compact power is the move away from traditional hydraulic systems. I remember in my early days, the hydraulic power unit for a large packing line was a massive, noisy beast that took up a huge amount of floor space and was prone to messy leaks. Today, we use high-performance electric servo motors. These motors are incredibly small by comparison, but they offer superior control, precision, and speed. They are also much more energy-efficient, which directly addresses the challenge of volatile energy costs that factory owners like Javier Morales face. This switch alone can shrink a machine's footprint significantly while actually increasing its performance and lowering operational costs.
Integrated Functions: Doing More with Less
The core principle behind a compact, powerful line is functional integration. Instead of a long, linear process with separate stations for weighing, strapping, wrapping, and labeling, we combine these tasks.
Traditional Linear Line (Separate Stations) | Integrated Compact Line (Multi-Function Station) |
---|---|
1. Entry Conveyor & Weighing Station | 1. Entry, Weighing, and Centering Station |
2. Strapping Machine 1 (Radial) | 2. Combined Strapping & Wrapping Unit |
3. Turntable | |
4. Strapping Machine 2 (Eye) | |
5. Wrapping Machine | 3. Integrated Labeling and Exit Station |
6. Labeling Station | |
Approximate Length: 15-20 meters | Approximate Length: 8-12 meters |
As you can see, a multi-function approach can cut the required floor length nearly in half without sacrificing any capability. This isn't about removing features; it's about engineering them to work together in a single, efficient space. This kind of thinking turns a space problem into an efficiency gain.
What Layout Strategies Maximize Efficiency in Tight Factory Spaces?
Your factory floor is a real-world puzzle. You have support columns, existing production lines, and walkways that you can't just move. Trying to force a standard, straight-line packing system into this environment is a recipe for disaster. It often leads to inefficient workflows, creating bottlenecks where there were none before. Worse, it can create safety hazards for your team and make routine maintenance a nightmare. The solution isn't to knock down walls; it's to think creatively about the layout from the very beginning.
To maximize efficiency in tight factory spaces, you must move beyond linear thinking. The best strategies involve using U-shaped or L-shaped layouts that fit around obstacles, utilizing vertical space with lifts and overhead conveyors, and selecting modular equipment that can be configured to your specific plant geography.
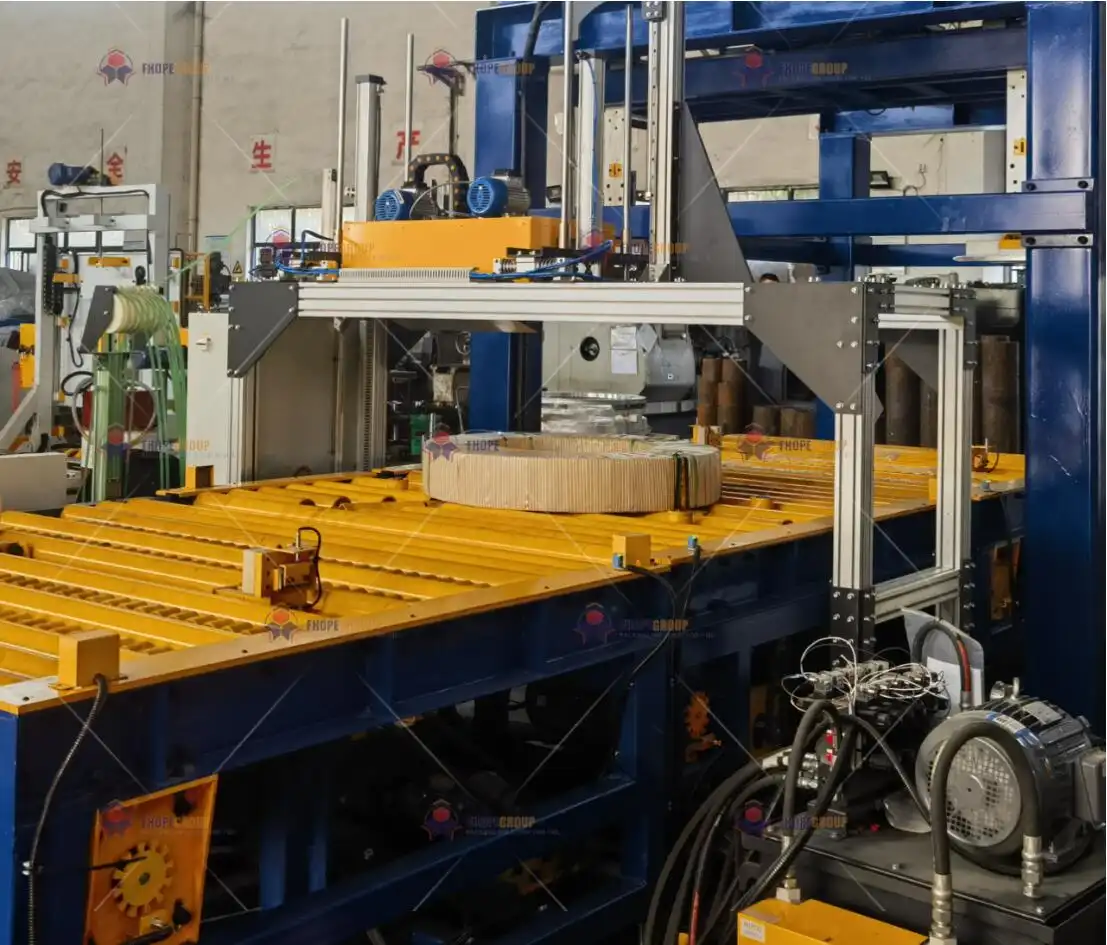
Deeper Dive: Thinking in 3D to Solve a 2D Problem
When I visit a client's factory for the first time, I don't just look at the empty space on the floor plan. I look up. I look around corners. The solution to a floor space problem is often not on the floor itself. By adopting a three-dimensional approach, we can design a highly efficient packing line that respects the reality of your existing infrastructure.
Non-Linear Flow: The Power of the U-Shape
The standard packing line is often a long "I" shape. This is simple, but highly inflexible. For factories with limited length but more width, an "L" or "U" shape is far more effective.
- I-Shape (Linear): Simple material flow, but requires a long, uninterrupted space. Inflexible around obstacles.
- L-Shape: Good for fitting into corners. The entry and exit points are on different axes, which can be useful depending on logistics.
- U-Shape: This is often the most space-efficient design. The entry and exit points are close to each other, which streamlines logistics for forklift or crane operators. It allows one operator to oversee both the start and end of the line, improving labor efficiency.
I once worked with a client in Northern Italy whose factory was over 100 years old. The production floor was filled with massive, unmovable structural columns. A linear line was impossible. We designed a U-shaped packing line that literally wrapped around one of these columns. The column, once seen as a major problem, became the central point of a compact, efficient work cell.
Going Vertical: Your Untapped Resource
The most underutilized space in any factory is the vertical dimension. When floor space is tight, we build up.
Vertical Solution | Function | Benefit in Compact Layouts |
---|---|---|
Coil Lifts/Tilters | Move coils between different levels or change their orientation (eye to sky). | Replaces long, sloping conveyors. Allows stacking processes. |
Overhead Conveyors | Transport coils above other machinery or walkways. | Frees up valuable floor space for other operations or access. |
Vertical Accumulators | Hold a buffer of coils vertically instead of on a long horizontal conveyor. | Prevents line stoppages without consuming a large footprint. |
By using lifts to feed coils into a wrapping station from above, for example, you can place the wrapping machine much closer to the previous station, saving critical meters of floor space. This is essential for achieving the kind of operational efficiency goals that someone like Javier sets, where every square meter must be productive.
How Does a Tailored Packing Solution Boost ROI and Operational Stability?
A new packing line is a significant capital investment. You are under pressure to show a clear return on that investment, and fast. The temptation can be to choose a standard, off-the-shelf machine because the initial price seems lower. However, this can be a costly mistake. A standard machine that isn't a perfect fit for your operation can lead to hidden costs from poor integration, unexpected downtime, and daily inefficiencies that slowly erode your profitability. A tailored solution, on the other hand, is engineered from the start to meet your specific goals and deliver a strong, predictable ROI.
A tailored packing solution boosts ROI by precisely matching the equipment's capacity and features to your production needs, which eliminates waste and bottlenecks. This lowers the initial investment by avoiding over-engineering, reduces ongoing energy and consumable costs, and dramatically increases operational stability by integrating seamlessly with your existing workflow, minimizing downtime.
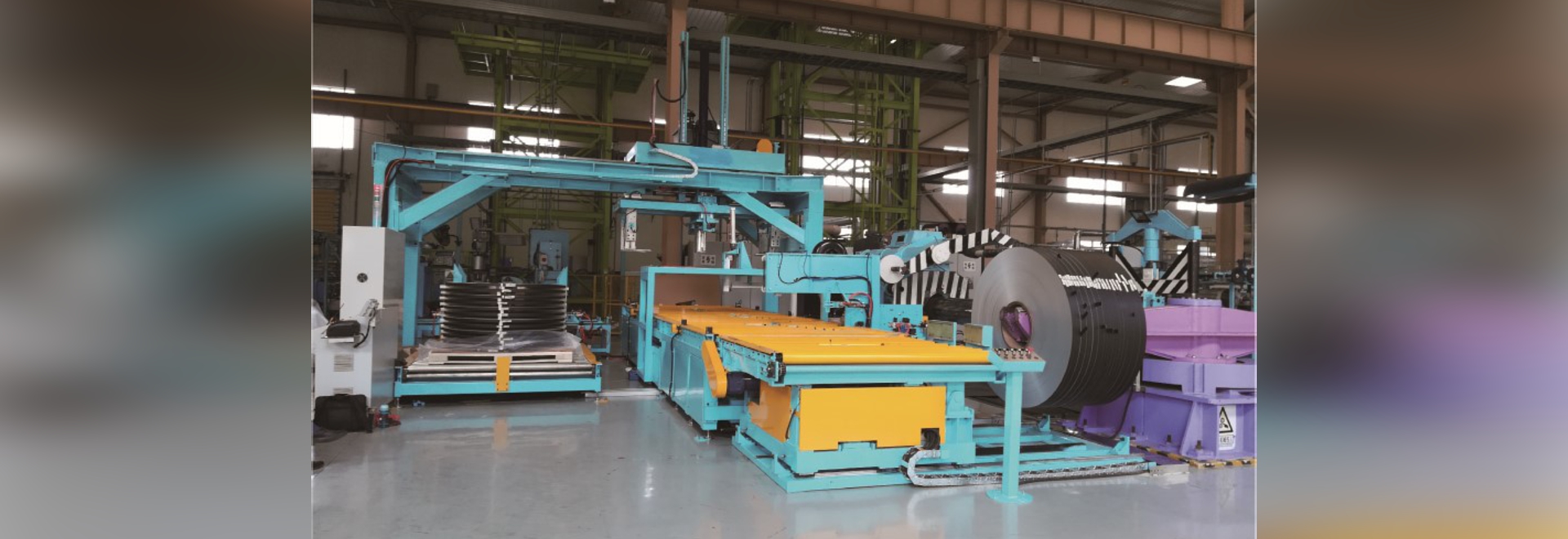
Deeper Dive: Looking Beyond the Price Tag to True Value
As an entrepreneur myself, I understand Javier's focus on rigorous financial analysis. A packing line isn't just a machine; it's a critical asset that must contribute to the bottom line. That's why we must analyze the Total Cost of Ownership (TCO), not just the purchase price.
Calculating the Total Cost of Ownership (TCO)
A tailored solution is designed to optimize TCO. Here’s how it breaks down:
- Capital Expenditure (CAPEX): A tailored line might seem like it has a higher initial cost, but not always. By specifying exactly the capacity and features you need, you avoid paying for an oversized or over-engineered standard machine. If your line produces 20 coils per hour, buying a machine designed for 40 is a waste of capital. We build for your target, with room for growth.
- Operational Expenditure (OPEX): This is where a tailored solution really shines and helps achieve goals like an 8% reduction in operating costs.
- Energy: We select motors and heaters sized perfectly for your coils, not for the maximum theoretical coil. This directly cuts energy consumption.
- Consumables: A tailored system is calibrated to use the precise amount of stretch film and strapping for your products, reducing material waste.
- Labor: By designing a line that fits your workflow, like the U-shape I mentioned, you can often run the entire system with one operator, reducing labor costs.
- Downtime Costs: This is the hidden killer of ROI. A standard machine forced into a space it wasn't designed for will have integration issues. A tailored line is designed to connect perfectly with your up-stream and down-stream equipment. This seamless integration is key to achieving the 95% uptime that ambitious leaders target.
Stability Through Customization
Operational stability comes from a system where every component works in harmony. When you buy a "standard" line, you're often getting a collection of modules from a catalog. When we design a "tailored" line, we are building a single, cohesive system. The conveyors speak the same language as the wrapper, which speaks the same language as the strapper. This synergy means fewer communication errors between components, fewer mechanical conflicts, and ultimately, far less unplanned downtime. It allows for more reliable implementation of predictive maintenance systems, because we know exactly how each part is designed to perform.
Factor | Standard "Off-the-Shelf" Line | Tailored "Custom-Fit" Line | Impact on ROI & Stability |
---|---|---|---|
Integration | Potential conflicts with existing gear | Designed for seamless connection | Lower installation costs, faster startup, less downtime. |
Capacity Match | Often over- or under-sized | Precisely matched to production output | Optimal CAPEX, lower energy costs, no bottlenecks. |
Flexibility | Rigid design, hard to modify | Modular design for future upgrades | Protects investment against future market or product changes. |
Maintenance | Awkward access in tight spaces | Designed with maintenance access in mind | Faster repairs, higher uptime, improved worker safety. |
A tailored solution is more than a machine; it's a strategic partnership. It’s about understanding your goals for cost reduction, efficiency, and stability, and then engineering a solution that is guaranteed to help you achieve them.
What Automation Features are Crucial for Modern Compact Packing Lines?
You want to modernize your factory, increase throughput, and reduce your reliance on manual labor. But you might worry that "automation" means adding complex, bulky robotic cells that you simply don't have space for. This fear can hold you back from the huge gains in efficiency, safety, and data-driven management that modern automation offers. The great news is that today's automation is smarter, more integrated, and less physically intrusive than ever before, making it the perfect partner for a compact line design.
The most crucial automation features for modern compact packing lines include a centralized PLC/HMI control system for single-point operation, a network of IoT sensors for data collection and predictive maintenance, and streamlined robotics for tasks like labeling or corner protection. These features add intelligence and efficiency without adding significant physical bulk.

Deeper Dive: Automation That Adds Brains, Not Bulk
The goal of automation in a compact line isn't just to replace a person with a machine. It's to make the entire process smarter, more reliable, and completely visible to your management systems. This directly supports a strategic push towards digitalization and Industry 4.0.
The Central Nervous System: PLC and HMI
In the past, each machine on a line had its own control panel. The operator had to walk back and forth, and if there was a problem, you had to figure out which machine was the source. In a modern compact line, everything is controlled from one place.
- PLC (Programmable Logic Controller): This is the "brain" of the entire line. A single, powerful PLC coordinates every motor, sensor, and actuator from the entry conveyor to the exit palletizer. This ensures every action is perfectly timed and synchronized.
- HMI (Human-Machine Interface): This is the "face" of the operation—a single touchscreen panel that gives the operator full control and visibility. From this one screen, they can select packing recipes, monitor the status of every component, view production data, and diagnose alarms. This reduces the number of operators needed and dramatically simplifies training and troubleshooting.
IoT and Data: Making the Machine Talk
For a forward-thinking leader like Javier, who wants to implement predictive maintenance and a full MES, data is everything. A compact automated line is built for this. We embed IoT sensors throughout the machine to act as its voice.
Sensor Type | Data Collected | Benefit for Operations |
---|---|---|
Vibration Sensors | Motor and bearing vibrations | Predicts bearing failure before it happens, allowing for scheduled maintenance. |
Temperature Sensors | Motor, gearbox, and panel temperatures | Prevents overheating and electrical faults. |
Power Monitors | Real-time energy consumption (kWh) | Helps track and achieve energy reduction goals (e.g., 10% unit reduction). |
Optical Sensors | Film/strap levels, coil presence | Alerts operators to refill consumables before the line stops, maximizing uptime. |
This data is fed directly into your plant's MES or data analytics platform. It gives you a fully transparent view of your packing operation, turning it from a "black box" at the end of your production line into an intelligent, data-generating asset. This is the foundation of digital transformation.
Conclusion
Compact packing lines are not a compromise. They are a powerful, tailored solution to boost your factory's efficiency, stability, and ROI, no matter the layout constraints you face.