As a steel plant owner, you face relentless pressure. You're balancing the high costs of production against the volatile demands of the market. Your existing packing lines, likely built for a different era, are probably rigid and inefficient. They create bottlenecks, increase maintenance costs, and struggle to adapt to new customer requirements. This inflexibility is more than just an operational headache; it's a direct threat to your profitability. Every hour of downtime spent on changeovers or repairs is an hour of lost production, and every customer request you can't fulfill is a missed opportunity. But what if your packing line could become a source of strength? Imagine a system that could adapt as quickly as the market, offering the flexibility to handle any order and the reliability to maximize your output. This is the promise of a modular coil packing line, a strategic solution designed for the modern steel industry.
A modular coil packing line provides flexibility for steel plants by breaking down the entire packing process into independent, interchangeable modules. This design allows for rapid reconfiguration to handle different coil sizes, packaging materials, and production volumes. It also enables phased upgrades and simplified maintenance, ensuring the line can evolve with market demands and technological advancements without causing major disruptions.
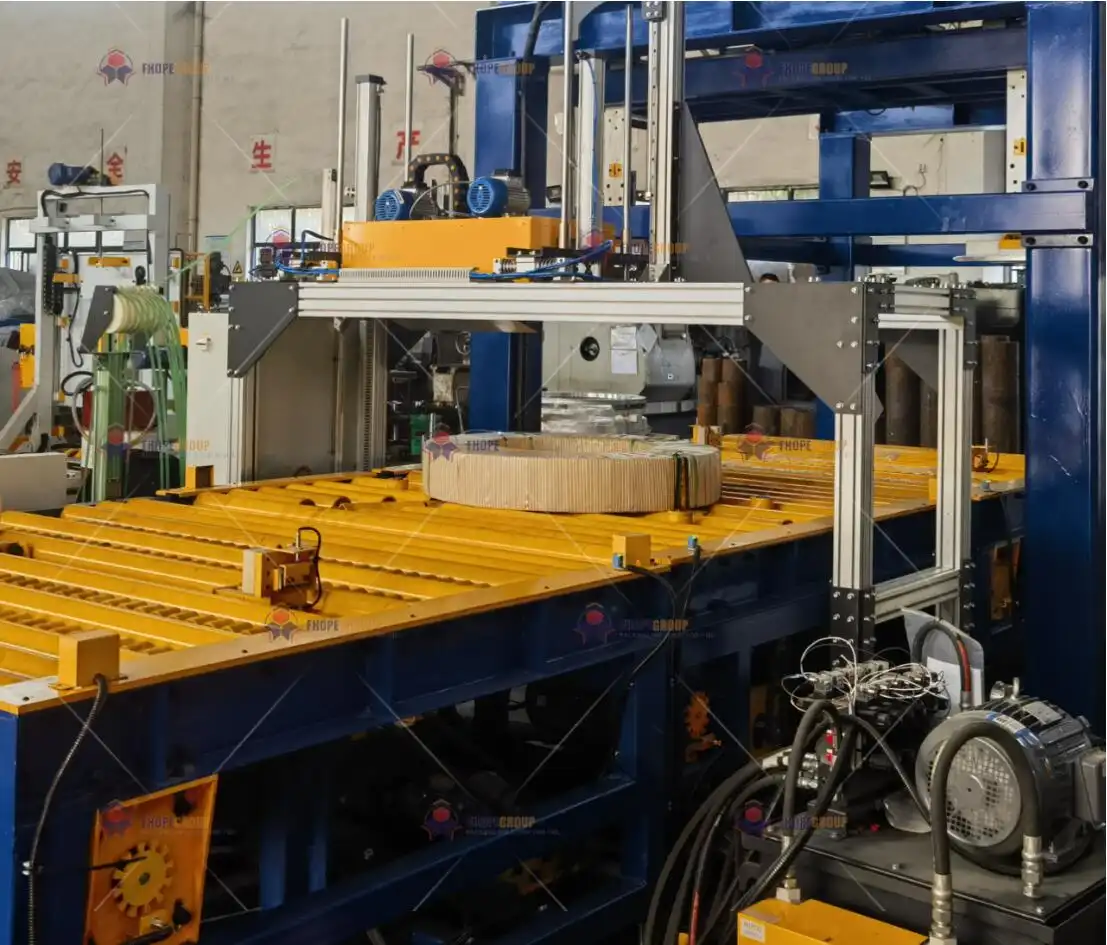
This concept sounds great in theory, but as a practical engineer and business owner myself, I know you're focused on real-world application. I built my company, SHJLPACK, on the principle of providing solutions that deliver tangible results. You want to understand how this modularity translates into concrete benefits for your plant, whether it's in Spain or Mexico. Let's break it down further. We will explore how each part of a modular system can solve the specific challenges you face every day.
How can a modular design tackle the high costs of aging equipment and frequent downtime?
You have likely seen it countless times. A single component on a 15-year-old packing line fails, and the entire production process grinds to a halt. Your maintenance teams scramble to diagnose the issue, you struggle to find the right spare parts, and every minute of downtime bleeds money from your bottom line. These old, monolithic systems become a significant financial drain. The repair costs accumulate, and the lost production hours make it impossible to reach your plant's utilization targets. You get stuck in a frustrating cycle of reactive maintenance, constantly applying temporary fixes to keep outdated machinery running. A modular design fundamentally changes this dynamic. Instead of one large, interconnected machine, you have a series of independent units. This approach radically simplifies maintenance, slashes downtime, and allows you to strategically upgrade your line piece by piece.
A modular design tackles aging equipment costs by allowing for targeted replacement of individual modules instead of a full line overhaul. When a specific function, like strapping or wrapping, becomes obsolete or fails frequently, only that module needs to be upgraded or replaced. This phased approach minimizes capital expenditure and dramatically reduces downtime, as maintenance or replacement can be performed on one module while others are quickly brought back online.
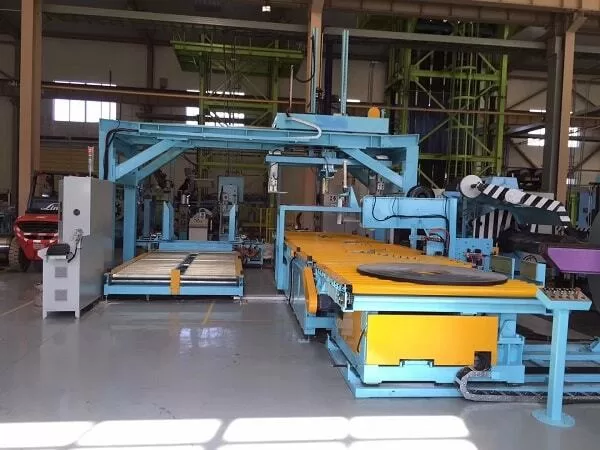
Dive Deeper: From Cost Center to Strategic Asset
I remember my early days as an engineer on the factory floor. We had a massive, custom-built packing line. It was considered state-of-the-art when it was installed. But when the main strapping head began to fail regularly, it became a recurring nightmare. The original manufacturer had discontinued the parts. We had to wait weeks for a machine shop to fabricate a replacement. During that time, finished coils piled up, and our entire downstream production was choked. That experience taught me a powerful lesson about the hidden, long-term costs of inflexible, monolithic design. It’s a lesson I carried with me when I founded SHJLPACK.
Let’s get practical and break down how modularity changes this entire picture for a steel plant owner like you.
Phased Modernization vs. Complete Overhaul
An aging production line presents a difficult choice. You can either endure the constantly rising maintenance costs or commit to a massive capital investment for a complete replacement. A modular line gives you a third, much more strategic option: phased modernization. You can perform a health check on your entire line and identify the weakest links. Is the wrapping unit slow and consuming too much film? Is the old strapping machine responsible for 50% of your downtime? You can choose to replace just that single module. This "pay-as-you-go" approach to modernization spreads out the financial commitment and operational disruption over time. It transforms what would be a giant financial risk into a series of manageable, strategic upgrades.
Reducing Mean Time To Repair (MTTR)
Downtime is the enemy of profitability. In a traditional line, troubleshooting can be incredibly complex because all systems are intertwined. A failure in one area could be caused by a faulty sensor in a completely different section. With a modular system, each unit has its own dedicated controls and diagnostics. This isolation makes it much faster to pinpoint the exact source of the problem. Furthermore, for critical functions, you can even keep a spare module on-site. If a strapping module goes down, your team can swap it out in a matter of hours, not days or weeks. This has a massive positive impact on your Overall Equipment Effectiveness (OEE) and gets you much closer to your goal of 95% effective run time.
Let's look at a simple table to make this clear.
Feature | Monolithic (Traditional) Line | Modular Line |
---|---|---|
Upgrading | Requires complete line replacement. High CAPEX. | Phased replacement of individual modules. Lower, staggered CAPEX. |
Troubleshooting | Complex, interconnected systems. High MTTR. | Isolated diagnostics per module. Low MTTR. |
Spare Parts | Often custom or discontinued for older lines. | Standardized parts for common modules. Easier to stock. |
Downtime Impact | Failure in one part stops the entire line. | Failure can be isolated. May allow partial operation or quick swap. |
This modular approach is not just about saving money on repairs. It is about building resilience and control into your production process. It gives you, the owner, command over your assets, your budget, and your plant's future.
Can modular packing lines truly adapt to fluctuating market demands and diverse product specifications?
The steel market is anything but stable. One month, the automotive sector demands thousands of small, narrow coils with specific packaging. The next month, the construction industry needs large, heavy coils with robust, weatherproof wrapping. Your rigid, existing packing line probably struggles to keep up with these shifts. Every changeover to accommodate a different coil size or packaging type takes hours, wasting valuable production time that you can never get back. Worse, you might have to turn down profitable orders simply because your line physically cannot handle the product's dimensions or meet the customer's unique packaging requirements. This lack of agility directly limits your market reach and your revenue potential.
Yes, modular packing lines are designed specifically to adapt to fluctuating demands. By using interchangeable modules for different tasks like weighing, strapping, wrapping, and labeling, a plant can quickly reconfigure the line. For example, a module for through-the-eye strapping can be swapped for a radial strapping unit, or an additional wrapping station can be added to meet a customer's specific packaging standard. This agility allows a steel plant to serve a wider range of clients and respond swiftly to market shifts.

Dive Deeper: Turning Flexibility into Profit
I once worked with a client in Mexico who ran a very successful steel service center. Their biggest challenge was a major bottleneck in their packing area. Their entire business model was based on handling a huge variety of slit coils for many different industries, from automotive to appliance manufacturing. Their old packing line was a "one-size-fits-all" solution, which in reality meant it was not optimized for anything. Changeovers were a daily nightmare for their operators. They were losing business to more agile competitors who could promise faster turnaround times. We worked together to design and implement a new, modular packing line. The result was transformative. They could finally say "yes" to almost any customer request, which opened up new markets and significantly grew their business.
Flexibility is not just a buzzword; it is a core operational capability that drives revenue. Let's examine how modularity delivers this in a practical way.
Handling a Wide Product Mix
A traditional packing line is typically optimized for a very narrow range of coil dimensions, including width, inner diameter, and outer diameter. If a new order comes in that falls outside this limited range, you are often out of luck. A modular line, however, is built with adjustability as a core principle. Conveyors, centering devices, and wrapping stations are all designed with wider operational ranges. More importantly, you can incorporate specialized modules for non-standard products. For example, your line can handle standard coils 95% of the time, but you can quickly integrate a special module for stacking and strapping very narrow "pancake" coils. Or you can add a heavy-duty unit for handling ultra-heavy coils destined for a specific industrial application.
Multi-Material Packaging
Your customers have diverse needs. Some may require simple plastic stretch wrap. Others will specify VCI paper for long-term corrosion protection. Still others might need a full outer steel shell for maximum protection during international shipping. With a monolithic line, adding a new packaging material can require a major, custom-engineered retrofit. In a modular system, you can simply add or swap a material dispenser module. You could have one module for VCI paper, another for stretch film, and a third for bubble wrap. The line's central control system recognizes the active module and automatically adjusts the packing sequence to apply the correct material.
Flexibility Aspect | Monolithic Line Challenge | Modular Line Solution |
---|---|---|
Product Variety | Limited by fixed mechanical dimensions. | Adjustable modules, swap-in specialized units. |
Packaging Material | Hard to add new material types. Requires major retrofit. | Add or swap material dispenser modules easily. |
Production Volume | Fixed throughput. Becomes a bottleneck during growth. | Add parallel modules (e.g., a second wrapper) to scale capacity. |
This level of adaptability ensures that your end-of-line packaging operation can keep pace with your sales team's success and your company's growth.
How does a modular approach integrate with digital transformation goals like MES and IoT?
You are likely investing heavily in smart manufacturing. You are deploying Manufacturing Execution Systems (MES) and data analytics platforms to get a clear, real-time view of your entire operation. But too often, the final packing line is a "black box." It is an isolated island of old technology that does not communicate with your new, intelligent systems. This lack of data integration creates a significant blind spot at the very end of your production process. You cannot track coils in real-time through the packing stage. You do not know the true OEE of your packing equipment. And you cannot automatically link packaging data back to a specific production order in your MES. This gap undermines your entire digitalization effort.
A modular approach seamlessly integrates with digital transformation by treating each module as an intelligent, connected device. Each unit (strapping, wrapping, conveying) can be equipped with its own sensors and PLC, which communicates with a central line controller. This controller then acts as a single, organized gateway to your plant's Manufacturing Execution System (MES). This architecture simplifies data collection for OEE tracking, predictive maintenance, and real-time product traceability, turning your packing line into a valuable data source.
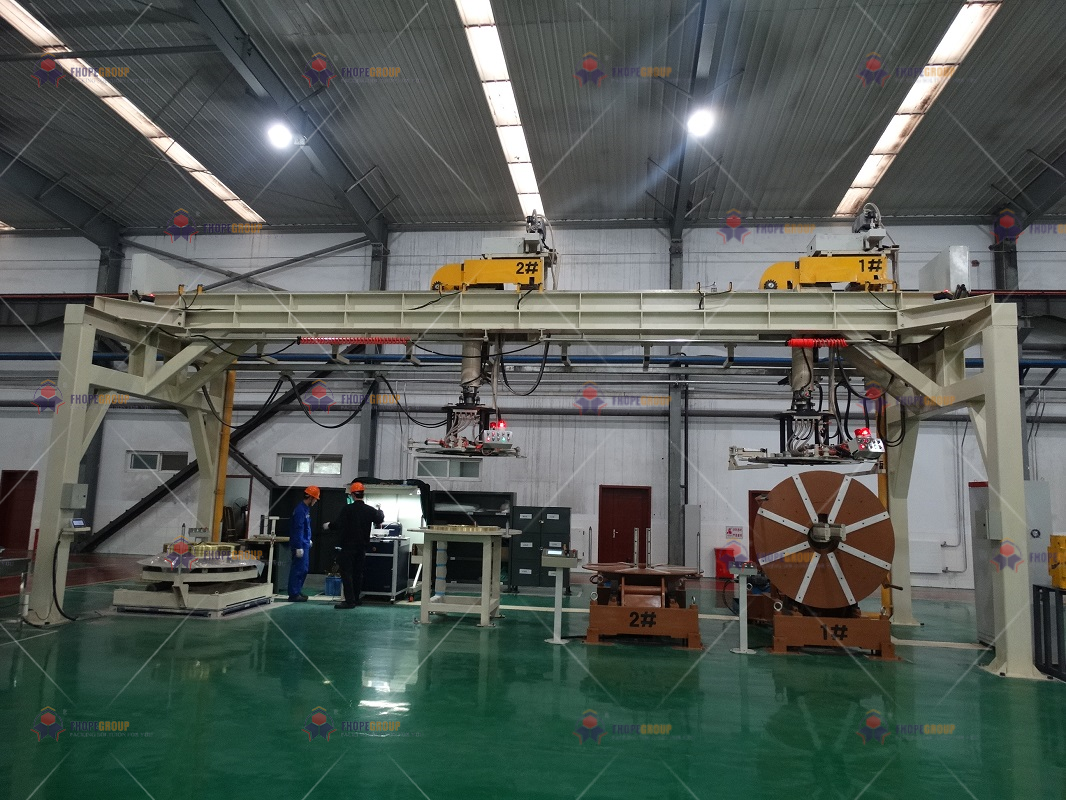
Dive Deeper: Connecting Packaging to the Smart Factory
When I started my own factory, SHJLPACK, one of the first principles I established was to "build for the future." For me, this meant building machines that could communicate. In the past, a packing machine just had to run. Now, a modern machine has to run, and it has to report. It needs to provide clean, reliable data. As a forward-thinking CEO like yourself, Javier, you know that data is the new steel. It is the raw material that gives you a competitive edge. That is why our modular designs prioritize open communication protocols and seamless sensor integration from the very beginning.
Let's explore the practical digital benefits this approach brings to your plant.
Achieving Total Production Visibility
Your goal of deploying an MES for a full view of production is absolutely the right strategy. A modular packing line fits perfectly into this vision. Imagine the workflow: a steel coil arrives at the start of the packing line. An RFID or barcode scanner automatically identifies it. This unique ID is sent to your MES. The MES, which already knows the customer's specific requirements for this coil, sends the correct "packing recipe" back to the line controller. The line then automatically configures its modules to execute that recipe perfectly. Every step is tracked. How long did the wrapping cycle take? How much strapping material was used? Was there any downtime during the process? All this valuable data is fed back to the MES in real-time and linked to that specific coil's digital record. You now have a complete, unbroken digital history from the furnace to the final packed product.
Enabling Predictive Maintenance
You want to move from a reactive maintenance schedule to a predictive one to achieve that 95% uptime goal. This is impossible without good data from your equipment. Each module on our lines can be fitted with a suite of IoT sensors to monitor key health indicators.
- Strapping Head: We can track cycle counts, motor current, and operating temperature to predict when maintenance is needed before a failure occurs.
- Wrapping Ring: We can monitor bearing vibration and drive motor load to detect wear and tear long before it causes a breakdown.
- Conveyors: We can track motor amperage to identify potential jams or bearing issues that could lead to a stoppage.
This data stream can be fed directly into your plant's big data platform, allowing your team to create a highly accurate predictive model for your maintenance schedule.
Digital Goal | How Modularity Helps | Practical Example |
---|---|---|
MES Integration | Centralized line controller acts as a single, clean data gateway. | The line receives a "packing recipe" from MES and reports back status. |
IoT & Data Analytics | Each module is a data node with its own dedicated sensors. | Vibration sensors on a wrapping motor predict a bearing failure. |
Traceability | Data from each packing step is linked to the specific coil ID. | Scan a packed coil to see its entire production and packing history. |
This digital integration turns your packing line from a simple machine into an intelligent asset that actively contributes to your plant's overall efficiency and profitability.
What is the real ROI of a modular packing line, considering both initial investment and long-term operational savings?
As a pragmatic CEO, I know that every investment decision you make comes down to the numbers. You can see the operational benefits of a modular system, but you are rightly concerned about the initial cost. You need to know if this advanced technology comes with a premium price tag that is difficult to justify on a balance sheet. It is easy to get excited about new technology, but if the return on investment (ROI) is not clear, compelling, and quick, it is just a distraction. You must be certain that investing in a modular line will directly contribute to your core financial goals, like reducing overall operating costs by 8% and improving your profit margin.
The real ROI of a modular packing line comes from a significant reduction in its Total Cost of Ownership (TCO). While the initial investment might be comparable to a traditional line, the long-term savings are substantial. These savings stem from four key areas: 1) lower maintenance costs and reduced downtime due to easier repairs and module swaps; 2) phased, lower-cost upgrades instead of full line replacement; 3) increased production flexibility, allowing the plant to capture more market opportunities; and 4) lower operational costs through energy-efficient modules and optimized material usage.
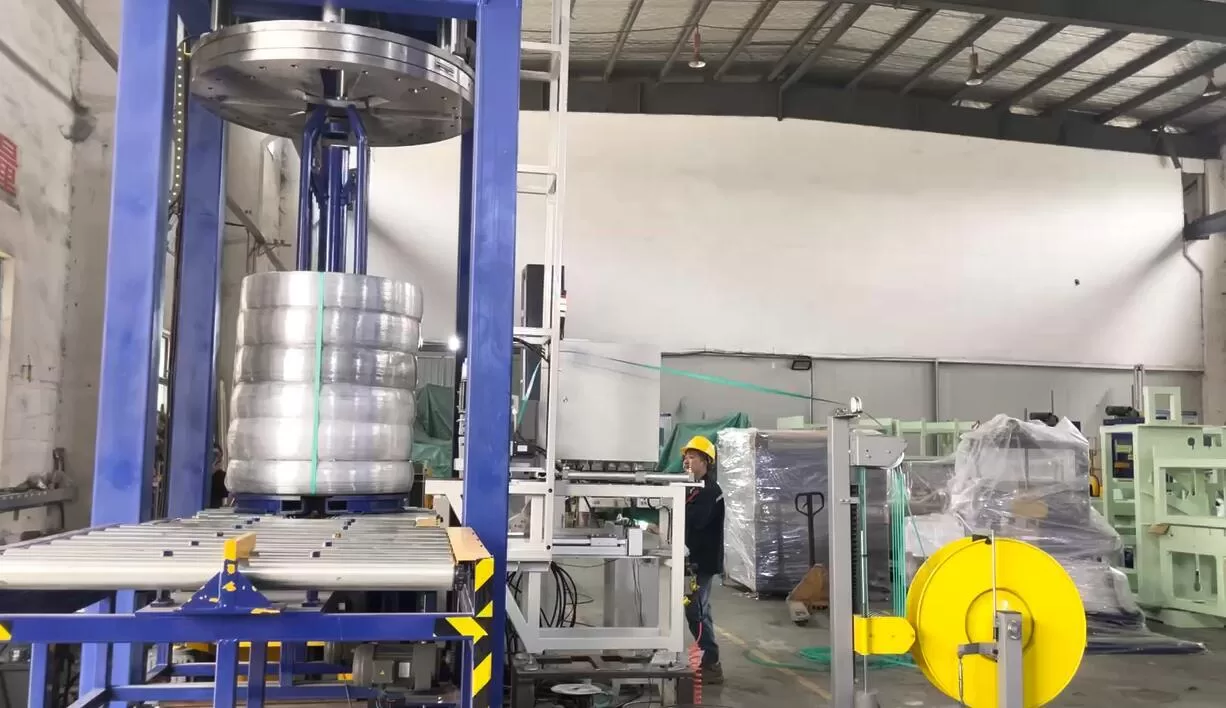
Dive Deeper: A Financial Case for Modularity
I have been fortunate enough to achieve financial independence through my career in the packing machine industry, and now my mission is to help my clients grow their own businesses. I achieve this by being completely transparent about costs and returns. I never just sell a machine; I work with my clients to provide a solution that makes strong financial sense. The conversation about ROI is the most important one we can have. A machine that does not improve your bottom line is a liability, not an asset.
Let's break down the ROI calculation beyond the initial sticker price. We need to look at the complete financial picture.
Calculating the Total Cost of Ownership (TCO)
The initial purchase price (CAPEX) is just one part of the equation. The real costs of any industrial equipment are found in its long-term operation (OPEX).
- Reduced Maintenance & Downtime: This is a massive factor in the TCO calculation. As we have discussed, faster troubleshooting and the ability to swap modules can cut maintenance-related downtime by 50% or more. If your line's downtime costs your plant $10,000 per hour, saving just 100 hours of downtime per year translates directly to a $1 million saving.
- Phased Investment: A modular approach helps you avoid the massive, multi-million dollar capital expenditure of a full line replacement every 15 years. Instead, you have smaller, predictable technology refreshment costs that can be planned and spread over time. This improves your company's cash flow and makes long-term financial planning far easier.
- Energy Savings: Your goal of a 10% reduction in unit energy consumption is ambitious but achievable. Modern modular components are designed for high efficiency. They use premium, high-efficiency motors, intelligent sleep modes that power down components when idle, and optimized wrapping techniques that use less power and less film per coil. A modern wrapping module can easily use 20% less energy than a 15-year-old design.
Quantifying Flexibility
This benefit is sometimes harder to measure, but it is critically important to your ROI. How much is it worth to be able to say "yes" to a new customer with unique requirements? What is the value of being able to enter a new, high-margin market segment because your line can finally handle their specific packaging needs? This "opportunity revenue," which was previously lost due to inflexibility, is a direct and significant return generated by a modular system.
Cost/Benefit Area | Monolithic Line Impact | Modular Line Impact | Estimated Savings/Gain |
---|---|---|---|
Downtime | High MTTR, major production loss. | Low MTTR, quick swaps. | 50-70% reduction in downtime costs. |
Capital Expenditure | Huge, infrequent lump sums. | Smaller, predictable, phased costs. | Better cash flow, lower long-term CAPEX. |
Energy Consumption | Older, inefficient motors and systems. | High-efficiency drives, smart controls. | 15-20% energy reduction per module. |
Market Agility | Limited product range, lost orders. | Wide product range, new opportunities. | 5-10% increase in potential revenue. |
When you add all these factors together—reduced OPEX, smarter CAPEX, and increased revenue potential—the business case for a modular packing line becomes undeniably clear. It is a direct investment in your plant's efficiency, resilience, and future growth.
Conclusion
A modular packing line is not just a piece of equipment. It is a strategic asset for flexibility, efficiency, and future-proof growth in the demanding steel industry.