Running a steel mill, especially in a competitive market like Italy, is a constant balancing act. I know this because I've spent my entire career in the packaging machine industry, first as an engineer and now as a factory owner myself. You're likely dealing with equipment that has served you well for over a decade, but is now starting to show its age. You face unpredictable energy costs, increasing pressure for environmental compliance, and the constant challenge of unplanned downtime. These issues aren't just minor annoyances; they directly eat into your profitability and create bottlenecks that ripple through your entire operation. It can feel like you're always one step behind, fighting fires instead of focusing on strategic growth. But what if you could turn your packaging line, often an overlooked part of the process, into a center of efficiency and a driver of profit? The solution is not just about buying a new machine; it's about implementing a total solution that delivers a clear, measurable return on investment.
Boosting efficiency and ROI in Italian mills is achieved by implementing modern, integrated coil packaging solutions. These systems automate demanding manual tasks, use materials and energy more effectively, and connect with plant-wide management systems. By replacing aging, standalone equipment with a cohesive line—from coil handling and upending to automated wrapping and strapping—mills can significantly cut operational costs, reduce product damage, and increase throughput, leading to a strong and predictable financial return.

I've seen firsthand how a strategic upgrade can transform a mill's performance. It’s about more than just speed; it’s about reliability, data, and building a foundation for future growth. The question isn't whether you can afford to upgrade, but rather, how much longer you can afford not to. Let's dig deeper into the specific challenges you face and explore how the right packaging solutions can provide concrete answers and tangible results for your mill.
How can modern coil packaging lines reduce downtime caused by aging equipment?
If your mill is like many I've worked with, you have a critical piece of packaging equipment that everyone knows is a problem. It might be an old strapper or a wrapper that requires constant adjustments and frequent repairs. These machines cause unexpected stops that bring your entire production to a halt. The delays are frustrating for your team, create serious bottlenecks, and make it impossible to plan your output reliably. You end up losing valuable production time and money, all because of one weak link in your process. The good news is that modern coil packaging lines are designed specifically to solve this problem, offering a level of reliability and predictability that older machines simply can't match.
Modern coil packaging lines reduce downtime by replacing failure-prone legacy equipment with robust, integrated systems designed for continuous operation. They feature high-quality components, fewer wear parts, and streamlined mechanics that minimize breakdowns. Furthermore, built-in diagnostics and sensors enable predictive maintenance, allowing you to fix issues before they cause a stoppage, drastically increasing your overall equipment effectiveness (OEE).

When I started as a young engineer, the philosophy was often "if it ain't broke, don't fix it." We would run machines until they failed, then scramble to get them back online. This reactive approach is incredibly costly. A modern approach is about proactive control. It's about turning unplanned downtime into scheduled, efficient maintenance. Let’s look at how this shift in thinking, supported by new technology, directly impacts your mill's productivity and bottom line.
From Reactive Repairs to Proactive Maintenance
The biggest difference between old and new equipment is the shift from a reactive to a proactive mindset. Aging equipment forces you into a reactive cycle. A belt snaps, a motor burns out, or a pneumatic valve fails, and your line stops. You then have to diagnose the problem, find the right spare part, and get a technician to make the repair. All of this takes time—time your mill isn't producing.
Modern packaging lines are fundamentally different. They are built with sensors that monitor key components in real-time. These sensors track motor temperature, vibration, cycle counts, and tension levels. This data is fed into the machine's control system (PLC), which can alert your maintenance team to a potential issue long before it leads to a catastrophic failure. For example, the system might detect that a motor is drawing more current than usual, indicating that a bearing is beginning to wear out. Instead of the motor failing during a critical production run, you receive an alert. You can then schedule the bearing replacement for the next planned maintenance window. This simple change transforms unpredictable, costly downtime into a controlled, low-impact task. It's a core principle of Industry 4.0, and it's readily available in today's packaging machinery.
The Hidden Costs of "Good Enough" Equipment
Even when an old machine isn't completely broken, it's still costing you money. These are the "hidden costs" that often don't show up on a maintenance report but drain your efficiency. Think about slow cycle times or lengthy changeovers between different coil sizes. An old strapping head might take 30 seconds per strap, while a modern one does it in 15. That difference adds up to hours of lost production over a year.
Changeovers are another major source of hidden downtime. On older lines, adjusting guides, strap tension, and wrapper settings for a new coil dimension can be a manual, time-consuming process that relies on operator experience. Modern systems automate this. The operator simply selects the new coil size on a touchscreen HMI (Human-Machine Interface), and the machine's guides, strapping head, and wrapper automatically adjust to the correct positions. What once took 15 minutes of manual tweaking can now be done in under a minute. This dramatically increases your flexibility to handle varied orders without sacrificing uptime.
Metric | Aging Packaging Line | Modern Integrated Line |
---|---|---|
Failure Mode | Reactive (Fix when broken) | Proactive (Predict & prevent) |
Unplanned Downtime | High (5-10%) | Very Low (<1%) |
Mean Time To Repair (MTTR) | Hours | Minutes (with diagnostics) |
Changeover Time | 15-30 Minutes (Manual) | < 2 Minutes (Automated) |
Data Availability | None / Manual Logs | Real-time performance data |
Can automated coil wrapping systems truly lower a mill's energy consumption?
Energy is one of the largest and most volatile operating expenses for any steel mill. As a mill owner, you are acutely aware of how fluctuations in electricity and fuel prices can impact your production costs. You've likely already invested in major energy-saving initiatives, like waste heat recovery from your furnaces. However, the energy consumed by your downstream processes, like packaging, is often overlooked. It's easy to assume that these machines are a minor part of your overall energy bill. But when you have equipment running 24/7, even small inefficiencies add up to a significant cost over the course of a year. You may be wondering if upgrading your packaging line can really make a dent in such a large expense.
Yes, modern automated coil wrapping and handling systems are specifically engineered to lower a mill's energy consumption. They achieve this by using high-efficiency servo motors instead of power-hungry hydraulic or pneumatic systems, incorporating intelligent "sleep modes" that power down components during idle times, and optimizing mechanical designs to perform tasks with the minimum energy required. The cumulative savings can be substantial, directly contributing to your goal of reducing unit production costs.

In my journey from an engineer to founding SHJLPACK, I've focused heavily on designing machines that are not just effective, but also efficient. The days of oversized motors and constantly running hydraulic pumps are over. A smart design philosophy focuses on providing power only when and where it's needed. Let's break down where the energy is wasted in older systems and how new technology addresses it.
Pinpointing Energy Waste in Packaging Lines
In many older packaging lines, the primary culprits of energy waste are outdated power systems. Hydraulic power units are a perfect example. To provide the force needed for tasks like lifting a coil or pressing a strap, these systems rely on a large electric motor to constantly run a pump, keeping hydraulic fluid pressurized. The pump runs continuously, consuming a significant amount of electricity, even when the machine is idle between coils. It's like leaving your car engine running while you're parked. This is a massive source of "vampire" energy drain.
Similarly, older pneumatic systems, which use compressed air for movement, are notoriously inefficient. Leaks in the air lines are common and difficult to detect, meaning your air compressors have to work harder—and use more electricity—just to maintain pressure. Furthermore, many older machines use simple, oversized AC induction motors that run at a constant full speed, regardless of the load. They lack the intelligence to scale their power usage to the task at hand. All of these small inefficiencies combine to create a much larger energy footprint than you might realize.
The Technology Behind Energy Savings
The solution lies in smarter, all-electric designs. At SHJLPACK, this is a core part of our philosophy. We replace inefficient hydraulic and pneumatic systems with high-efficiency electric servo motors and variable frequency drives (VFDs). A servo motor only draws significant power when it is performing a task, like moving a wrapping shuttle or tensioning a strap. During idle times, its energy consumption is near zero.
VFDs add another layer of intelligence. A VFD allows a standard motor to adjust its speed and torque precisely to match the load. For example, a conveyor moving a light coil doesn't need to run with the same power as when it's moving a heavy one. The VFD automatically scales the motor's energy output, ensuring no watt is wasted. This technology not only saves energy but also reduces mechanical stress on the components, extending their lifespan.
Power System | Key Characteristic | Energy Efficiency | Maintenance Level |
---|---|---|---|
Old Hydraulic | Constantly running pump | Low | High (Oil leaks, filter changes) |
Old Pneumatic | Prone to air leaks | Low to Medium | Medium (Line and valve checks) |
Modern All-Electric | Power-on-demand (Servos/VFDs) | High | Low (Fewer wear parts) |
By adopting these modern electric systems, a mill can realistically achieve the goal of a 10% reduction in unit energy consumption for its packaging operations, contributing directly to a stronger, more resilient bottom line.
What is the real ROI of upgrading your coil handling and strapping solutions?
As a business owner, every major capital expenditure comes down to one critical question: "What is my return on investment?" An investment in a new coil packaging line is significant, and you need to be confident that it will pay for itself and contribute to your profitability. With the cyclical nature of the steel industry, it's easy to be cautious and try to get one more year out of your existing equipment. You might see the new machine's price tag and hesitate, wondering if the benefits truly outweigh the cost. The reality is that a properly planned upgrade delivers a multi-faceted ROI that goes far beyond the simple math of the machine's cost versus labor savings.
The real ROI of upgrading coil handling and strapping solutions is a powerful combination of direct cost reductions and indirect efficiency gains. It is calculated from decreased labor costs through automation, significant savings in consumable materials like stretch film and strapping, a dramatic reduction in costly downtime, and the elimination of expenses related to product damage. Together, these factors often result in a full payback period of 18 to 36 months, while also increasing overall plant throughput.

I've helped many clients analyze the ROI for their projects. The key is to look at the complete picture, not just one or two factors. Your goal of reducing overall operating costs by 8% is ambitious, but it is achievable. Often, the packaging area is a goldmine of overlooked savings opportunities. Let's dissect how to calculate the true return.
Calculating Your Total Cost of Ownership (TCO)
The initial purchase price is just one part of the equation. To understand the true financial impact, you need to compare the Total Cost of Ownership (TCO) of your old line versus a new one. TCO includes all the costs associated with running the equipment over its lifetime.
First, consider labor costs. An older, manual, or semi-automatic line might require two or three operators. A modern, fully automated line can often be managed by a single operator who oversees the process, freeing up valuable personnel to work on other high-value tasks.
Second, look at material consumption. Modern stretch wrappers use powered pre-stretch systems that can stretch film by 200-300%. This means you use significantly less film to securely wrap a coil compared to an old machine with no pre-stretch. Modern strappers also apply precise tension, preventing over-use of strapping material. These savings on consumables are direct and recurring.
Third, factor in maintenance and downtime costs. As we discussed, old lines break down more often and cost more to maintain. Quantify the cost of lost production per hour of downtime and add the cost of spare parts and maintenance labor. A new line with a warranty and predictive maintenance features dramatically reduces these expenses.
Beyond the Numbers: Intangible Returns
Not all returns can be captured on a spreadsheet, but they are just as important. A major one is product quality and customer satisfaction. A modern line provides a consistent, high-quality, and secure package every single time. This means fewer coils damaged during transport and handling. Fewer customer complaints and damage claims not only save you money but also protect your mill's reputation as a quality supplier.
Another intangible benefit is employee safety and morale. Manual handling of heavy coils and strapping tools carries inherent safety risks. Automating these processes creates a safer work environment. This can lower insurance premiums and improve employee morale. When your team works with reliable, modern equipment instead of constantly fighting with an old machine, their job satisfaction and productivity increase.
ROI Calculation Category | Potential Annual Savings (Example) | Description |
---|---|---|
Labor Reduction | €70,000 | Re-assigning 1.5 operators to other tasks (€45k/year avg. cost per operator) |
Material Savings | €25,000 | 40% reduction in stretch film consumption due to powered pre-stretch |
Uptime Increase | €120,000 | Gaining 2 hours/week of production (Valued at €1,250/hour) |
Maintenance Reduction | €15,000 | Reduced spare parts, lubricants, and emergency labor costs |
Total Annual Savings | €230,000 | --- |
This example shows how a new line, even with a significant initial cost, can generate substantial annual savings that lead to a very attractive ROI.
How does a packaging partner support a mill’s long-term digital transformation goals?
You are a forward-thinking leader. You understand that the future of the steel industry lies in data and digitalization. Your goal to deploy MES, IoT sensors, and data analytics platforms is exactly the right strategy to stay competitive. However, a digital transformation is not just about software; it's about the hardware on your factory floor. You need machines that can speak the same language as your management systems. The challenge is that many equipment suppliers still think in terms of standalone machines. They sell you a piece of equipment, but leave the complex task of integration entirely up to you. This can create a major roadblock to achieving your vision of a fully connected, "smart" factory.
A true packaging partner supports a mill's digital transformation by providing equipment that is "Industry 4.0-ready." This means the machinery is built with integrated IoT sensors, modern PLCs, and open communication protocols (like OPC-UA or Profinet) that allow it to seamlessly connect and share data with your MES, SCADA, and ERP systems. The partner's role extends beyond the sale to provide the technical support needed to ensure this data flow is successful, turning your packaging line into an intelligent node in your digital ecosystem.
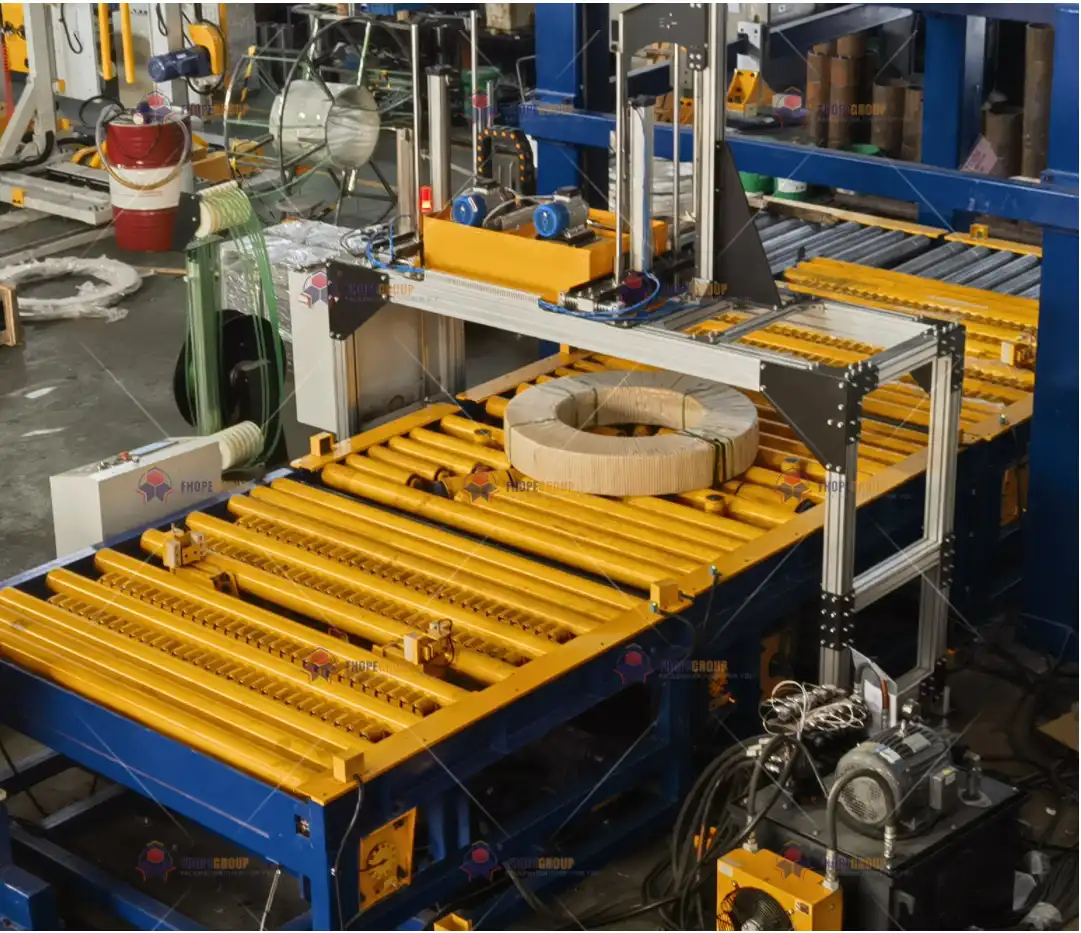
This is an area I am incredibly passionate about. When I started SHJLPACK, my goal was not just to build reliable machines, but to provide a "TOTAL SOLUTION." In today's world, a total solution must include digital integration. We don't just sell you a machine in a box; we provide a tool that helps you become a more data-driven manufacturer. Let's look at what this means in practice.
The "Smart" Packaging Line: What to Look For
When you are evaluating new packaging equipment, you need to look beyond the mechanical specifications. You need to ask about its digital capabilities. A "smart" packaging line should come standard with several key features. First, it should be equipped with a network of onboard sensors that go beyond basic operation. These sensors should monitor everything from motor current and wrapping film consumption to the number of strap cycles and any operational faults.
Second, the machine must be controlled by a modern PLC (Programmable Logic Controller) from a reputable brand (like Siemens or Allen-Bradley). This PLC should be equipped with an Ethernet port and support standard industrial communication protocols. This is non-negotiable. It's the gateway that allows the machine to talk to the rest of your factory.
Third, look for a user-friendly HMI (Human-Machine Interface). This touchscreen panel is not just for operating the machine; it's your window into its performance. It should clearly display key performance indicators (KPIs), production data, and alarm histories. Crucially, a good partner will also provide options for remote access, allowing your engineers or our technicians to securely log in to diagnose issues, reducing the need for on-site service calls.
From Data to Decisions
Having a connected machine is only the first step. The real power comes from what you do with the data. When your coil packaging line is integrated with your MES (Manufacturing Execution System), you unlock a new level of operational visibility. You can track the OEE (Overall Equipment Effectiveness) of your packaging line in real-time. If there is a stop, the system can automatically log the reason, whether it was a lack of coils, a film roll change, or a mechanical fault.
Analyzing this data over time allows you to move from guessing to knowing. You can identify the most common causes of micro-stops and address their root causes. You can track material consumption per coil and compare it against a standard to identify waste. You can use cycle count data to precisely schedule preventative maintenance on high-wear components like strapping heads. This data-driven approach is the key to achieving your goals of 95% uptime and an 8% reduction in operating costs. It transforms the packaging line from a black box at the end of your process into a transparent, manageable asset.
Digital Feature | What It Is | Benefit to the Mill Owner |
---|---|---|
Integrated IoT Sensors | Devices measuring vibration, temp, usage | Enables predictive maintenance, prevents failures |
Open Communication Protocol | Standard language (e.g., OPC-UA) for data sharing | Seamless integration with your existing MES/ERP |
Real-time OEE Tracking | Automatic calculation of Availability, Performance, Quality | Provides a clear, instant view of line efficiency |
Remote Diagnostics | Secure access to the machine's PLC from off-site | Faster troubleshooting, reduced service costs |
This is the future of manufacturing, and your packaging partner should be helping you get there, not holding you back.
Conclusion
Upgrading your coil packaging solution is a strategic investment in efficiency, profitability, and future-readiness for your Italian mill. It is a direct path to achieving measurable operational and financial goals.