As a steel plant owner in Turkey, you are navigating a challenging landscape. You face volatile energy prices, increasing pressure for environmental compliance, and the constant need to modernize aging equipment. Your packing line, often an overlooked part of the operation, might be a hidden bottleneck. It could be causing delays, increasing labor costs, and holding your plant back from its true potential. Every minute of downtime on that line, every manually strapped coil that gets damaged, and every kilowatt of wasted energy chips away at your hard-earned profits. The market is competitive, and this kind of inefficiency is a heavy burden to carry. But what if your packing line could be more than just a cost? What if it could become a strategic asset that actively drives your business forward? The new generation of coil packing machines for 2025 is designed with features that directly address these challenges. They can boost your efficiency, slash costs, and prepare your plant for a more profitable future. I know this because I've dedicated my life to this industry, first as an engineer, then as a factory owner, and now as a consultant helping people just like you.
The top coil packing features for Turkish plant owners in 2025 are full automation to reduce labor costs, modular designs for production flexibility, energy-efficient systems to combat high energy prices, and integrated IoT capabilities for data-driven decision-making. These features are essential for maximizing your return on investment, ensuring operational stability, and staying competitive in the demanding steel market.
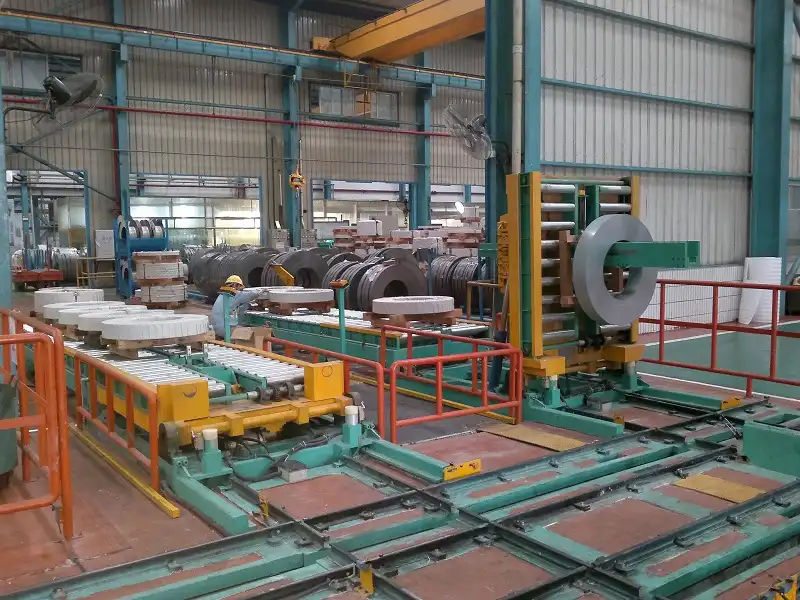
These features sound promising, but I know you're a practical business owner. You need to see how they translate into real-world results for your bottom line. You want to understand the mechanics behind the promises. In this article, I will break down each of these key features. I'll use my years of experience designing, building, and running these machines to show you exactly how they can solve your plant's most pressing challenges. Let's get into the details.
How Can Automated Packing Lines Reduce Operational Costs and Reliance on Manual Labor?
Finding skilled and reliable workers for your packing line is a constant struggle. The work is repetitive and physically demanding, leading to high turnover. And manual packing is often slow, inconsistent, and brings significant safety risks. You worry about these things. Every coil that is improperly strapped, every damaged edge from rough handling, and every minute of lost time costs you money and can damage your reputation with customers. On top of that, labor costs continue to rise, and a single workplace accident can bring your entire operation to a halt. The solution is to remove these unpredictable variables from the equation. A fully automated packing line provides consistent, high-speed, and high-quality packing 24/7, with very little human intervention.
Fully automated coil packing lines reduce operational costs by minimizing manual labor, eliminating human error, increasing throughput, and improving workplace safety. This directly lowers your expenses on salaries, reduces material waste from improper packing, and guarantees a consistent, professional-looking final product, which boosts your bottom line.

Dive Deeper: The Tangible Value of Automation
Let's break down how automation delivers these benefits in a concrete way. It's not just about replacing people with machines; it's about re-engineering a process for maximum efficiency and minimum cost.
From Manual Tasks to Robotic Precision
An automated line takes over the entire sequence of tasks that are currently done by hand. This includes moving the coil from the slitter, centering it, weighing it, applying circumferential and radial straps, wrapping it in protective film, and printing and applying a label. Each step is performed by a specialized module controlled by a central computer. There are no breaks, no fatigue, and no variations in quality. A robot arm applies a strap with the exact same tension every single time. A wrapping shuttle applies the film with the perfect overlap, ensuring complete protection without wasting material. This level of precision is simply impossible to achieve with a manual team over a long shift.
Quantifying the Return on Investment (ROI)
As a plant owner, you live and die by the numbers. Let’s look at a realistic comparison. I've seen this transformation in dozens of factories I've worked with. The numbers don't lie.
Metric | Manual Packing Line | Automated Packing Line | Annual Impact |
---|---|---|---|
Labor Requirement | 4-6 operators per shift | 1 supervisor per shift | ~80% reduction in labor cost |
Throughput | 8-10 coils per hour | 20-30 coils per hour | 2-3x increase in capacity |
Material Waste | 5-10% (uneven wrapping) | <1% (precise control) | Significant savings on VCI/stretch film |
Uptime | ~85% (breaks, shift changes) | >98% (continuous operation) | More production hours per year |
Package Quality | Inconsistent | 100% Uniform | Fewer customer complaints/returns |
Safety as a Direct Financial Benefit
Never underestimate the financial impact of safety. The packing area, with its heavy coils and moving machinery, is a high-risk zone. Manual handling leads to strains, sprains, and more serious injuries. Automation removes your workers from harm's way. This drastically reduces the risk of accidents. The result? Lower insurance premiums, fewer lost workdays, and avoidance of the massive costs associated with production shutdowns and regulatory fines. A safer plant is a more profitable plant.
Can Modern Packing Systems Adapt to Different Coil Sizes and Types Without Long Changeover Times?
Your customers have diverse needs. One day they need narrow slit coils for a small stamping operation, and the next they need wide, heavy coils for the automotive industry. Your current packing line might struggle with this. Every time you need to switch from one coil size to another, it requires a long and complicated manual changeover. Your team has to stop the line, get out the tools, manually adjust guides and rollers, and reconfigure the strapping head. This downtime is killing your productivity. It forces you to run large batches of one size to minimize changeovers, which creates excess inventory and ties up capital. Or worse, you have to turn down smaller, high-margin orders because the setup time just doesn't make it worthwhile. Modern systems are built to solve this exact problem. They use advanced controls and motors to make these adjustments automatically, allowing you to switch between different coil specifications in minutes, not hours.
Yes, modern coil packing systems are designed with modularity and advanced automation to handle various coil sizes and types with minimal changeover time. Features like automatic eye-to-center positioning, programmable strapping patterns, and adjustable roller stations allow for near-instantaneous adaptation to new product specifications entered via a simple touch-screen interface (HMI).

Dive Deeper: The Power of Production Flexibility
Flexibility is no longer a luxury; it's a core requirement for survival and growth in the modern steel industry. A packing line that can adapt quickly is a powerful competitive advantage.
The Technology That Makes It Possible
The magic behind this speed and flexibility lies in three key components working together:
- PLC (Programmable Logic Controller): This is the brain of the machine. It stores "recipes" for every coil size and packing requirement you have. A recipe includes data like coil diameter, width, weight, number of straps, and wrapping layers.
- HMI (Human-Machine Interface): This is the simple touch-screen where your operator interacts with the machine. Instead of using wrenches and levers, they just select the recipe for the next coil coming down the line.
- Servo Motors and Sensors: These are the muscles of the system. When the operator selects a recipe, the PLC sends precise commands to servo motors connected to the guide rollers, strappers, and conveyors. Sensors confirm that everything has moved to the correct position with sub-millimeter accuracy. The entire changeover is done automatically.
A Practical Comparison: The Old Way vs. The New Way
Let's visualize the difference this technology makes on your factory floor.
Task | Manual Changeover | Automated Changeover |
---|---|---|
Initiation | Stop production line. | Operator selects next coil recipe on HMI. |
Adjustment | Crew uses tools to manually loosen, move, and tighten guides and supports. | Servo motors automatically adjust all contact points. |
Strapping Head | Manually adjust for new coil diameter and strapping position. | Strapping head automatically moves to pre-programmed positions. |
Testing | Run a test coil slowly to check for alignment and clearance. | No test coil needed. System is pre-calibrated. |
Total Time | 1-2 hours | < 5 minutes |
The Strategic Advantage of Agility
This drastic reduction in changeover time unlocks new business strategies. You can now operate on a "Just-in-Time" (JIT) basis. You can confidently accept smaller, more specialized orders that often carry higher profit margins because the cost of switching production is negligible. This agility allows you to be more responsive to the market's fluctuations, a key challenge you face. Instead of your production schedule dictating what you can sell, your customer orders can dictate what you produce, day by day. This reduces inventory, improves cash flow, and makes your business far more resilient.
What Energy-Saving Features Are Essential in a 2025 Coil Packing Machine?
As a plant owner in Turkey, I know that volatile electricity and fuel prices are one of your biggest headaches. They directly impact your production costs and make financial planning difficult. Your older equipment, including the packing line, likely consumes a high and constant amount of energy. The motors run at full speed whether a coil is present or not, and every stop and start wastes energy as heat. This is like leaving a tap running all day. You are paying for energy that is not being used to produce anything, and that waste is directly eating into your profit margin on every coil you ship. New machines are engineered differently. Energy efficiency is a core design principle, not an afterthought. They use smart technologies to cut power consumption dramatically.
Essential energy-saving features for a 2025 coil packing machine include variable frequency drives (VFDs) on all motors, regenerative braking systems, automatic sleep modes during idle periods, and high-efficiency IE3 or IE4 rated motors. Together, these features can reduce the packing line's energy consumption by 15-30%, providing a direct and measurable reduction in your monthly electricity bill.
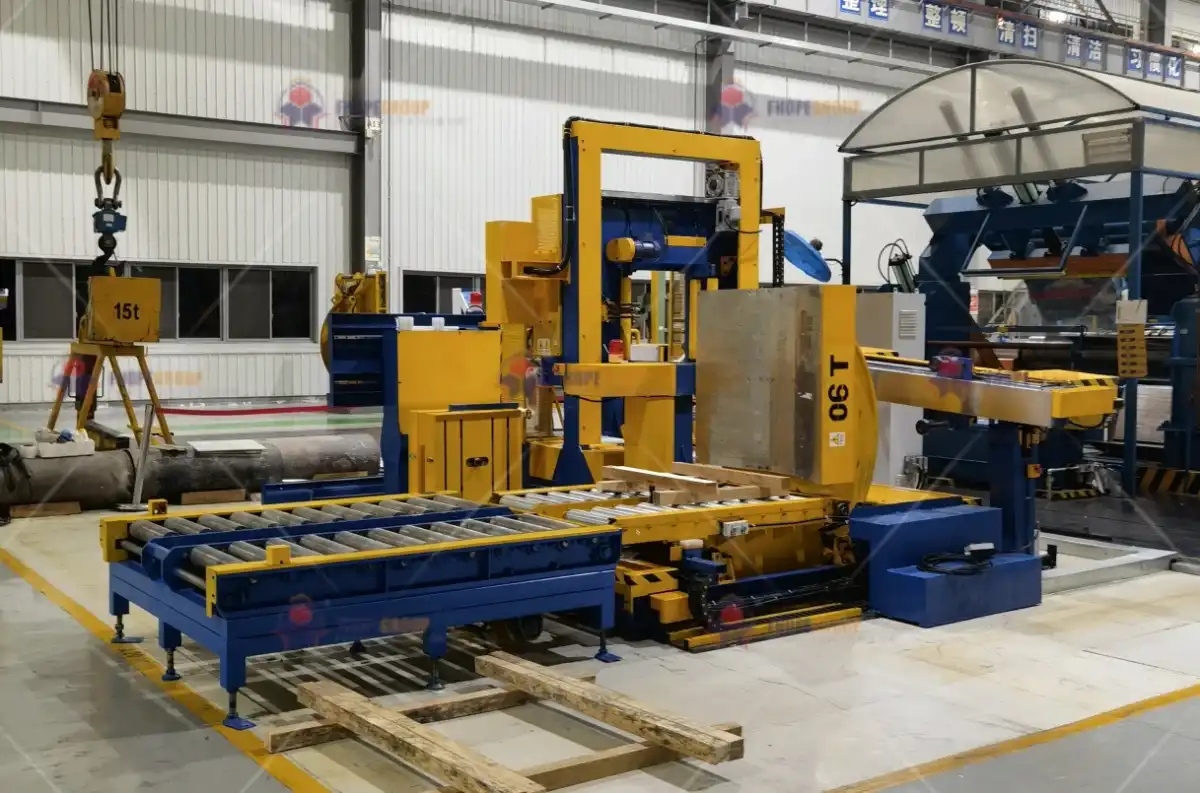
Dive Deeper: Engineering for Lower Energy Costs
Let's look at how these technologies work in simple terms and how they contribute to your goal of reducing unit energy consumption. This is the kind of innovation that I saw make a real difference when I was running my own factory.
Variable Frequency Drives (VFDs): The Smart Throttle
Think of a traditional motor like a light switch: it's either 100% on or 100% off. It uses maximum power all the time. A motor with a VFD is like a dimmer switch. The VFD adjusts the frequency and voltage of the electricity supplied to the motor, precisely matching the power output to the immediate need. For example, a conveyor motor only needs full power when accelerating a heavy coil. When it's moving at a steady speed or is empty, the VFD ramps down the power consumption significantly. By applying VFDs to all the main motors—conveyors, turntables, wrappers—you eliminate a huge amount of electrical waste.
Regenerative Braking: Capturing Wasted Energy
When a heavy, spinning object like a turntable needs to stop, its momentum has to go somewhere. In older machines, this energy is dissipated as heat through mechanical brakes—it's completely wasted. A regenerative braking system works like the one in a hybrid or electric car. As the motor slows the turntable down, it acts as a generator. It captures that kinetic energy, converts it back into electricity, and feeds it back into the machine's local power circuit to be used by another part of the system. This is a direct answer to your interest in waste energy recovery, applied right at the machine level.
The Compounding Effect on Your Electricity Bill
These features don't just save a little energy here and there. Their effects compound over time to create substantial savings. Let's compare a traditional line with a modern, energy-efficient one.
Feature | Old Packing Line (15+ years) | Modern Packing Line (2025) |
---|---|---|
Motors | Standard Efficiency (IE1), constant speed | High-Efficiency (IE3/IE4) with VFDs |
Braking | Mechanical (energy lost as heat) | Regenerative (energy recovered) |
Idle State | Motors run continuously | Automatic sleep/standby mode |
Avg. Power Draw | ~40 kWh | ~28 kWh |
Annual Savings | - | ~30% reduction in electricity costs |
This 30% reduction isn't just a theoretical number. It's a realistic target that translates directly into thousands of dollars saved per year, improving your profit margin on every single coil that leaves your plant.
How Do IoT and Data Integration in Packing Machines Improve Overall Plant Efficiency?
Right now, you probably have a feeling that your packing line could be more efficient, but you lack the hard data to know for sure. You rely on manual reports from supervisors and your own observations to guess where the bottlenecks are. You are flying blind. This uncertainty is a barrier to reaching your goal of 95% capacity utilization. Without real-time data, you can't see the impact of micro-stoppages, you don't know the true cause of downtime, and you can't accurately predict when a machine component might fail. The solution is to make your machine intelligent. IoT-enabled packing lines are equipped with sensors that provide a constant stream of data, making your entire packing operation transparent, measurable, and predictable.
IoT and data integration improve plant efficiency by providing real-time production data, enabling predictive maintenance, and connecting the packing line to your plant-wide Manufacturing Execution System (MES). This allows you to track Overall Equipment Effectiveness (OEE), detect potential failures before they happen, and automate the flow of information between production planning and the factory floor. The result is higher uptime, increased throughput, and smarter decision-making.
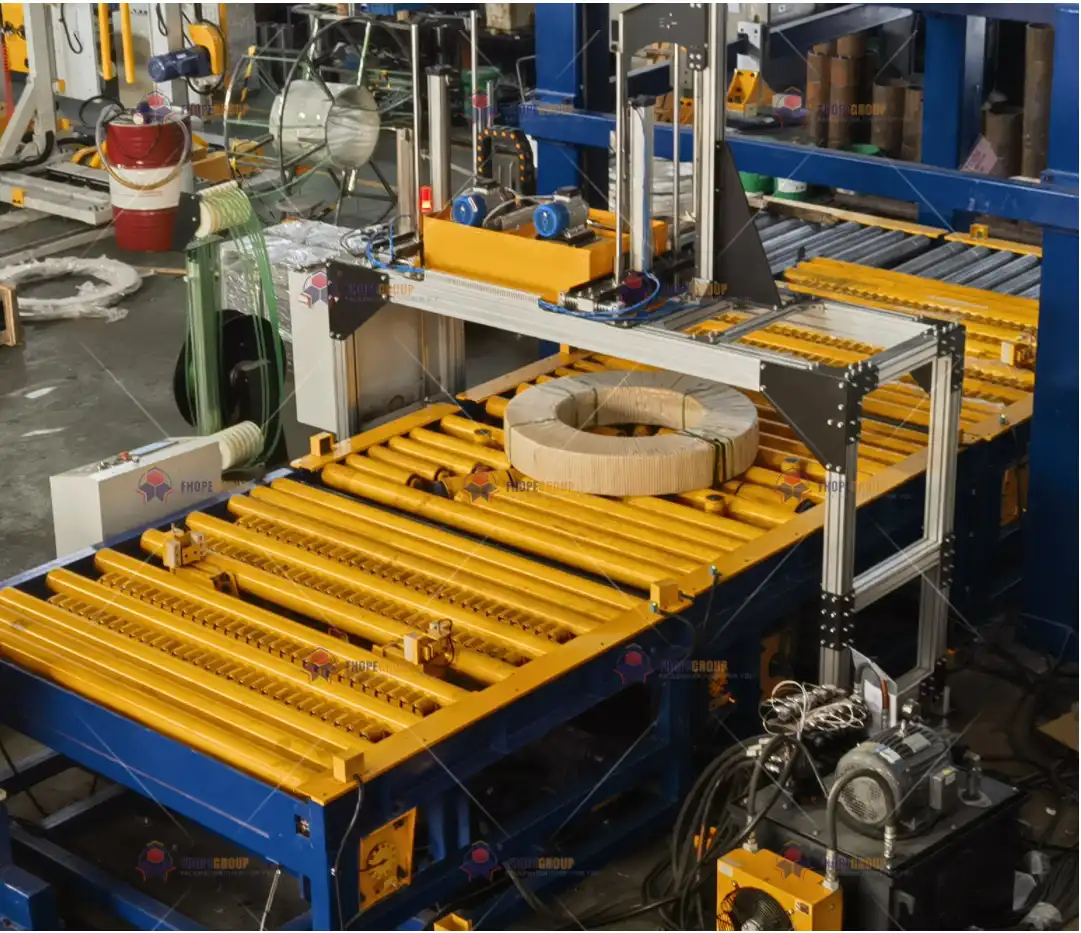
Dive Deeper: Turning Data into Action
Data is useless unless it helps you make better decisions. An IoT-enabled packing machine is designed to turn raw data into actionable insights that directly address your goals for digitalization and efficiency.
From Reactive to Predictive Maintenance
This is a game-changer for plant reliability. A traditional maintenance schedule is reactive (fix it after it breaks) or based on a fixed time interval (replace it every 6 months). Both are inefficient. An IoT-enabled machine uses sensors to monitor the health of its components in real time.
- Vibration sensors on motors and bearings can detect tiny changes that indicate wear and tear long before a failure.
- Temperature sensors can flag an overheating component.
- Power consumption monitoring can show if a motor is working harder than it should be, suggesting a mechanical problem.
Instead of a sudden, catastrophic breakdown that stops your entire line, you get an alert on your computer or phone: "Warning: Turntable Motor 3 is showing elevated vibration levels. Failure probability is 75% in the next 72 hours. Please schedule maintenance." This allows you to plan repairs during scheduled downtime, order parts in advance, and turn unplanned stops into planned maintenance. This is the path to achieving 95% uptime.
The Power of OEE (Overall Equipment Effectiveness)
OEE is the gold standard for measuring manufacturing productivity. It’s a simple formula: OEE = Availability x Performance x Quality.
- Availability: Is the machine running when it's supposed to be? IoT sensors track every stop, even for a few seconds.
- Performance: Is it running as fast as it's designed to? The system tracks the actual cycle time vs. the ideal cycle time.
- Quality: Is it producing good products? The system can be linked to scanners that track successfully packed coils versus any that need rework.
Without IoT, calculating OEE is a manual, inaccurate nightmare. With an integrated system, you get a live OEE score on your dashboard, allowing you to see problems instantly and drill down to find the root cause.
Seamless Integration with Your Plant's MES
Your goal is total production visibility. An IoT-enabled packing machine is no longer an isolated island. It becomes a fully integrated part of your digital factory. It communicates directly with your MES platform. When the slitter finishes a coil set, it signals the packing line. When the packing line finishes a coil, it logs the data (weight, dimensions, time) automatically into the MES and your inventory system. This seamless flow of information eliminates manual data entry, reduces errors, and gives you a true, real-time picture of your entire production process, from raw materials to finished goods.
What is the One Thing Most Plant Owners Overlook When Choosing a Packing Solution?
You have done your due diligence. You've analyzed the technical specifications, compared the features, and negotiated hard on the price. You have spreadsheets filled with data on throughput, motor sizes, and energy consumption. You feel confident you have covered all your bases to make a sound investment decision. But in my experience, many smart plant owners focus so intensely on the machine itself that they overlook the single most critical factor for long-term success: the relationship with the company that sells it. A cheap machine from a supplier who disappears after installation can quickly become the most expensive and frustrating piece of equipment you'll ever own. The real solution, the one that delivers value for years, is a supplier who acts as a true strategic partner.
The single most overlooked factor when choosing a packing solution is the quality and depth of the long-term partnership with the supplier. Beyond the initial purchase price and machine specs, it is the supplier's commitment to providing comprehensive support—covering installation, training, maintenance, and future-proofing advice—that truly determines the lifetime value and ROI of your investment.
Dive Deeper: Why Your Supplier is More Important Than the Machine
I built my company, SHJLPACK, on a lesson I learned the hard way. Early in my career, after I started my own factory, I needed a critical piece of equipment. I chose the cheapest option. It looked good on paper, but when we had problems, the support was non-existent. The downtime and stress nearly put me out of business. That painful experience taught me everything. It's why our slogan is "TOTAL SOLUTION FOR WRAPPING MACHINE." We don't just sell steel and wires; we sell a promise. We are partners in your success because I know what it feels like to be on your side of the table.
What a True Strategic Partnership Looks Like
A vendor sells you a machine. A partner helps you succeed with it. The difference is clear in their actions.
Aspect | Vendor (Just Sells a Machine) | Partner (Provides a Solution) |
---|---|---|
Design Phase | Offers a standard, off-the-shelf model. | Works with your team to customize the layout and features for your specific plant flow and product mix. |
Installation | Ships the machine with a manual. | Sends experienced engineers to your site for installation, commissioning, and full integration. |
Training | Provides a basic operator's guide. | Conducts in-depth, hands-on training for your operators and your maintenance team. |
After-Sales Support | A call center, slow response times. | A dedicated support line with engineers who can perform remote diagnostics and troubleshoot in real time. |
Spare Parts | Long lead times, often from overseas. | Maintains a stock of critical spare parts for immediate dispatch. |
Future Growth | The relationship ends after the warranty. | Proactively contacts you with information on software updates, new upgrade modules, and advice on meeting new regulations. |
The Hidden, Long-Term Costs of a Poor Partnership
Choosing the wrong supplier can cost you far more than you saved on the initial price. The costs are hidden in downtime, inefficiency, and frustration. When a sensor fails, how long does your line sit idle waiting for support? When you hire a new operator, how effectively can they be trained? When you need to adapt the machine in five years, will anyone answer the phone? A strong partner mitigates these risks, ensuring that your machine remains a high-performing asset for its entire lifespan. This is the final, and most important, feature to look for.
Conclusion
Choosing the right coil packing machine is a major strategic investment. Focus on automation, flexibility, energy efficiency, and data integration to secure your plant's future success.