Are you struggling to upgrade your coil packing line because of a cramped, unconventional factory layout? Many steel mills and service centers, especially established ones, have production floors that have evolved over decades. You have structural columns, pits, and existing machinery that you can't just move. You know you need to automate your packing to reduce costs and improve efficiency, but a standard, off-the-shelf packing line simply won't fit. This leaves you stuck with inefficient, labor-intensive manual packing, which creates a bottleneck that slows down your entire operation. The constant pressure to improve output clashes with the physical reality of your plant, making modernization feel impossible. The solution isn't a massive, expensive factory rebuild. It's a smart, flexible coil packing machine designed with modularity in mind. We've encountered this exact problem countless times, particularly in the dense industrial landscapes of Turkey, and have engineered specific solutions that work.
Flexible coil packing machines are specifically designed for challenging factory layouts, like those common in Turkey, by using a modular design. This approach breaks the packing line into independent components—such as the tilter, conveyor, wrapping station, and strapping unit. These modules can be arranged in non-linear configurations, for example, at 90-degree angles or around existing pillars, to create a custom-fit solution that integrates perfectly into limited or irregular floor space.
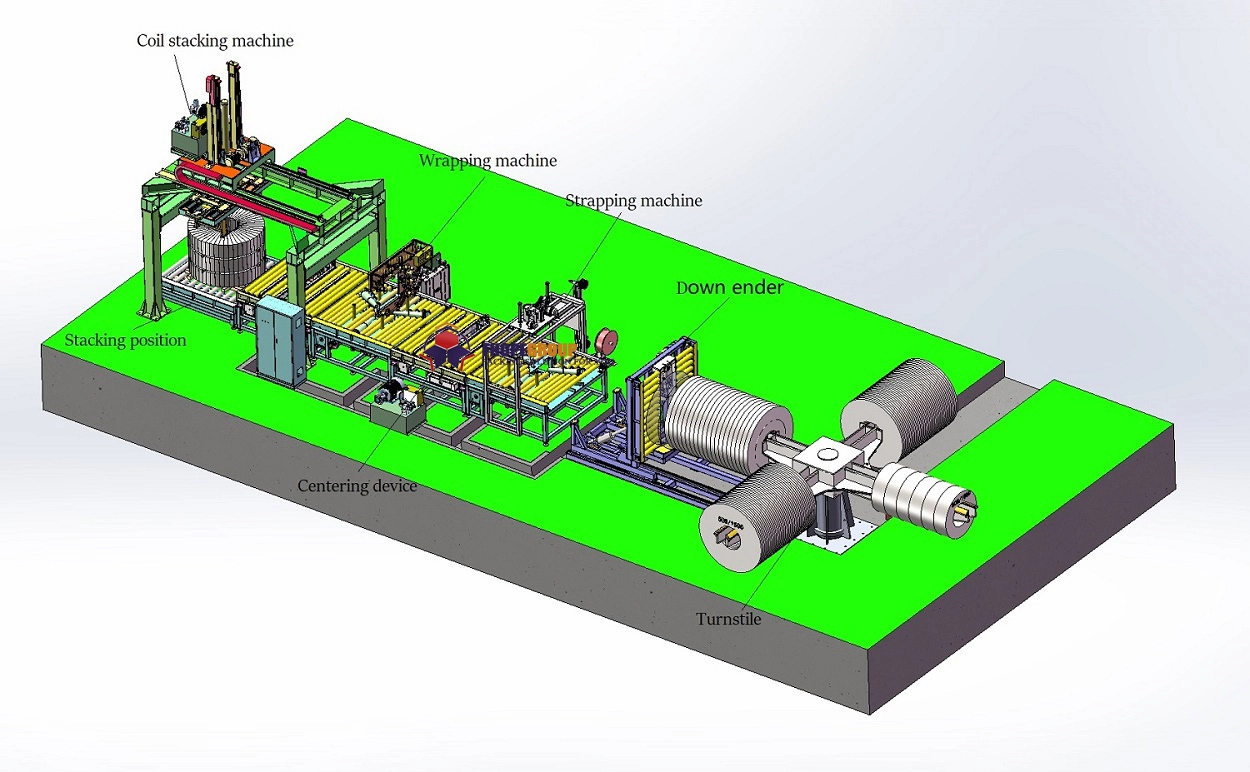
This modular approach is the key to unlocking automation in plants that were never designed for it. It’s about adapting the machine to the factory, not the other way around. But how does this translate into solving the real-world problems you face every day, from high labor costs to the urgent need for digitalization? Let's explore the specific questions that forward-thinking leaders like you are asking and see how these flexible systems provide the answers.
How Can Modular Coil Packing Lines Adapt to Existing, Space-Constrained Layouts?
You have a productive facility, but the packing area feels like an afterthought, squeezed into a corner with immovable obstacles. You need to install a modern packing line, but every standard design you see is too long, too wide, or requires a straight-line flow that you simply don't have. This physical constraint creates a major bottleneck. Coils begin to queue up, waiting for slow manual packing, which not only kills your plant's overall throughput but also creates a significant safety hazard with material congestion. The answer is to stop thinking of a packing line as one single machine. A modular coil packing line breaks the process into smaller, independent stations that can be strategically placed to navigate your unique factory floor, using unconventional angles and even vertical space to create a seamless flow.
A modular coil packing line adapts to space-constrained layouts by separating key functions into independent units. The coil tilter, infeed conveyor, main wrapping station, and outfeed conveyor are not part of a single rigid frame. Instead, they are individual modules connected by customized transport sections. This allows the line to bend around a structural column, use a pit-type car to cross an aisle, or incorporate a vertical lift to work across different elevations, ensuring a perfect fit within your existing plant footprint without costly demolition or construction.

Deconstructing the "Standard" Line
A conventional packing line is typically designed for a new, purpose-built facility. It assumes a long, straight, and unobstructed path. The process flows linearly: a coil is loaded at one end, moves straight through a wrapping station, and exits at the other end. This is highly efficient if you have the space. However, in an established mill, this rigid design often fails. I've walked through dozens of factories where this kind of line would require moving a critical piece of machinery or even an office wall, which is simply not feasible. The limitation of the standard line is its inflexibility; it demands the factory adapt to it.
The Power of Independent Modules
A modular approach flips this logic. We adapt the machine to your factory. By breaking the line into functional blocks, we gain immense flexibility in layout design. We can arrange these blocks like building blocks to create the optimal flow for your specific space.
Module | Standard Position | Flexible Position Examples |
---|---|---|
Coil Tilter/Upender | At the start of the line | Offline with a turnstile feed; in a pit to save space |
Infeed Conveyor | Straight line to wrapper | L-shaped with a 90-degree transfer; short section fed by crane |
Wrapping Station | Inline with conveyors | Positioned at an angle; offset from the main production line |
Outfeed Conveyor | Straight line from wrapper | Exits to the side via a transfer car; includes a lifting station |
Stacking/Palletizing | At the end of the line | Separate automated cell fed by AGV; vertical stacking system |
A Real-World Example from My Experience
I remember a project with a steel service center in Gebze, Turkey. Their production line was highly efficient, but the packing area was a nightmare. A massive concrete support column stood exactly where the outfeed conveyor of any standard machine would need to be. For years, they used a forklift to move coils from the slitter to a separate, manual wrapping station—a slow and dangerous process. They thought automation was impossible.
We walked the floor with their team and proposed a modular solution. We installed a compact wrapping station right at the exit of their slitter. Then, instead of a long outfeed conveyor, we designed a powered 90-degree transfer car. Once a coil was wrapped, this car moved it sideways, completely bypassing the column, and presented it to a parallel conveyor for strapping and removal. It fit perfectly. The solution eliminated the forklift bottleneck, increased their packing speed by 300%, and made the entire area safer. This is the kind of problem-solving that a flexible, modular approach makes possible.
What Automation Features Reduce Labor Costs and Improve Safety in Tight Spaces?
You're facing the dual challenge of rising labor costs and a shrinking pool of skilled workers. The manual packing process is slow, physically demanding, and often results in inconsistent quality. This not only drives up your operational costs but also leads to high employee turnover and an increased risk of workplace injuries. In a cramped packing area, these dangers are magnified. Workers maneuvering around heavy coils, sharp strapping material, and moving equipment is a recipe for an accident. You know that the cost of a single serious injury—in terms of medical bills, lost time, and potential fines—can easily erase any savings from using manual labor. Strategic automation is the solution. It’s not about replacing all your staff, but about deploying technology to handle the most dangerous, repetitive, and strenuous tasks, making the process safer, faster, and more reliable, even in a confined space.
Automation features that directly reduce labor costs and improve safety in tight spaces include automatic coil loading and centering, which eliminates manual pushing; robotic application of corner protectors, removing a difficult ergonomic task; and fully automated label printing and application. Furthermore, integrated safety systems using PLC-controlled light curtains, area scanners, and physical guarding are essential. These technologies minimize the need for operators to physically handle coils or enter the machine's operational footprint, drastically cutting labor requirements and creating a much safer work environment.
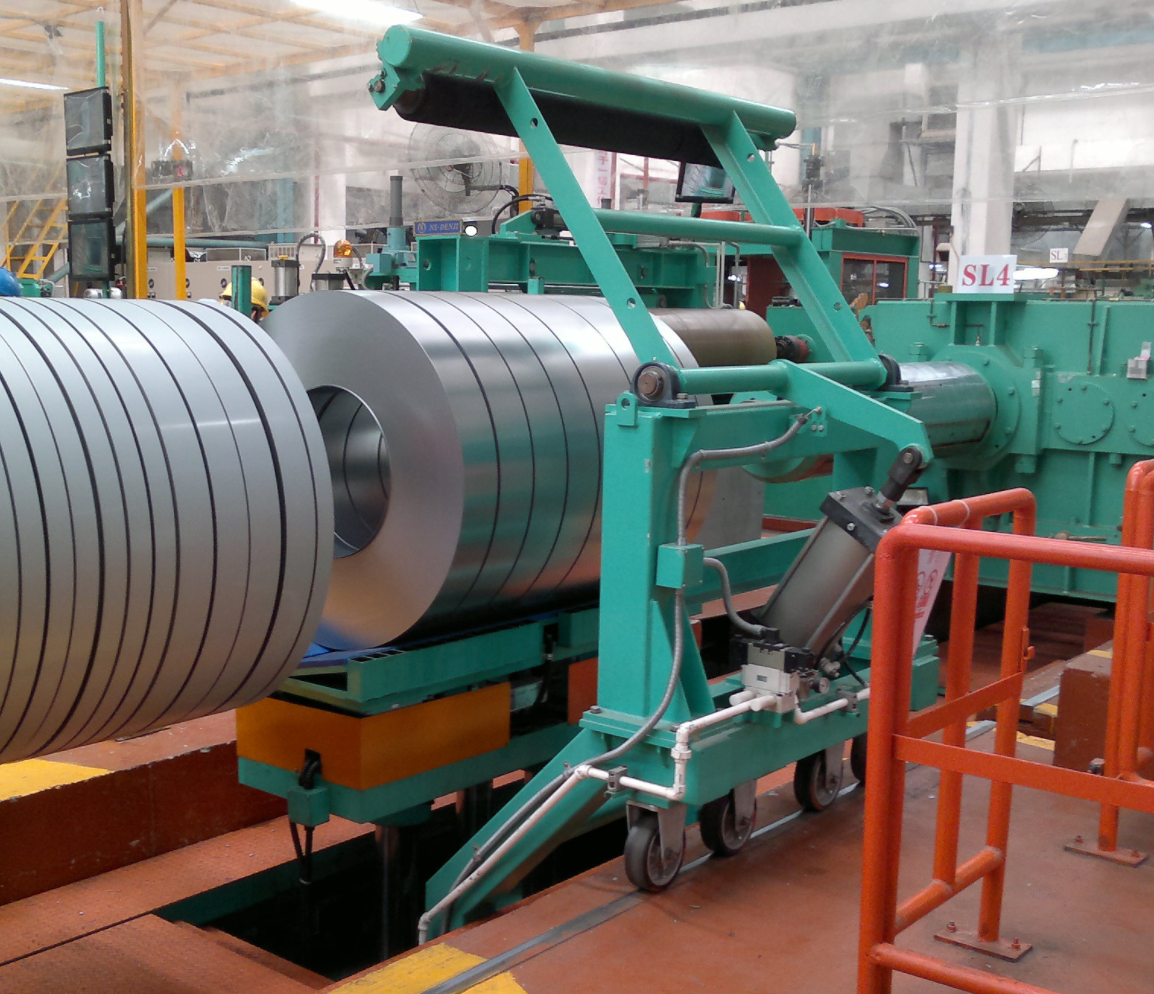
From Manual to Automated: A Phased Approach
Implementing automation doesn't have to be an all-or-nothing investment. For many factories, especially those with budget constraints or a workforce to retrain, a phased approach is best. You can target the biggest pain points first.
- Level 1: Semi-Automation. Start by automating the core wrapping process. An operator still loads the coil and applies corner protection, but the machine handles the wrapping and cutting of the film. This immediately improves consistency and reduces physical strain.
- Level 2: Targeted Automation. Add modules that handle specific, high-labor tasks. An automatic corner protection applicator or a label printer-applicator can often free up one full-time employee to be deployed to a more value-added role.
- Level 3: Full Automation. This is a "lights-out" solution where the coil is received, identified, wrapped, strapped, labeled, and moved to the dispatch area with minimal human intervention. This is the ultimate goal for maximizing efficiency and safety.
Key Automation Upgrades and Their Return on Investment
Each automation feature has a clear and measurable impact. As an engineer, I always focus on the practical benefits. Here’s how some key upgrades translate into savings and safety:
Automation Feature | Manual Task Replaced | Impact on Labor | Impact on Safety |
---|---|---|---|
Auto Coil Centering | Manually pushing/aligning the coil | Saves minutes per cycle | Eliminates crushing/pinching hazards |
Auto Corner Protector | Worker manually places cardboard/plastic | Reduces labor by 1 FTE in high-volume lines | Removes ergonomic strain, cuts risk |
Auto Label Applicator | Worker prints & sticks label by hand | Speeds up process, ensures accuracy | Keeps operator away from moving parts |
Auto Strapping Unit | Manually tensioning and sealing straps | Improves cycle time, consistent tension | Eliminates risk of strap recoil injury |
Safety is Non-Negotiable in Confined Areas
In a standard, open layout, you can use simple fencing to create a safe zone. In a tight, modular layout, safety systems must be more intelligent. We use 3D safety scanners that create invisible, dynamic safety zones. If a person or forklift crosses a defined boundary, the machine immediately enters a safe state. Light curtains guard openings, and interlocking gates prevent access during operation. These modern safety controls are not just add-ons; they are integrated into the machine's core PLC. This not only protects your people but also ensures compliance with increasingly strict international safety standards, a major concern for any responsible factory owner.
How Do Flexible Systems Integrate with MES and IoT for Better Production Visibility?
You have data. Your production lines, your furnaces, and your slitters are likely connected to a central system. But what about the final step? For many, the packing area is a "black box." You know a coil went in and came out, but you don't know the exact packing cycle time, the amount of material consumed, or where small delays are adding up to major bottlenecks. This lack of data-driven insight means you're making critical scheduling and logistics decisions based on assumptions, not facts. You can't give your customers precise delivery estimates or truly optimize your end-to-end workflow. Modern flexible packing systems are designed to solve this problem. They are not just mechanical machines; they are intelligent data nodes that integrate seamlessly with your plant's Manufacturing Execution System (MES) and Industrial Internet of Things (IIoT) platforms.
Flexible packing systems integrate with MES and IoT platforms using standard industrial communication protocols like OPC-UA, Profinet, or Ethernet/IP. The machine's central PLC controller acts as a data hub, collecting and transmitting real-time information for each coil—including its unique ID, weight, wrapping start and end times, film and paper consumption, and any error codes. This data stream is fed directly into the MES, allowing you to track each product through the final, critical stage of production and achieve complete, end-to-end manufacturing visibility.
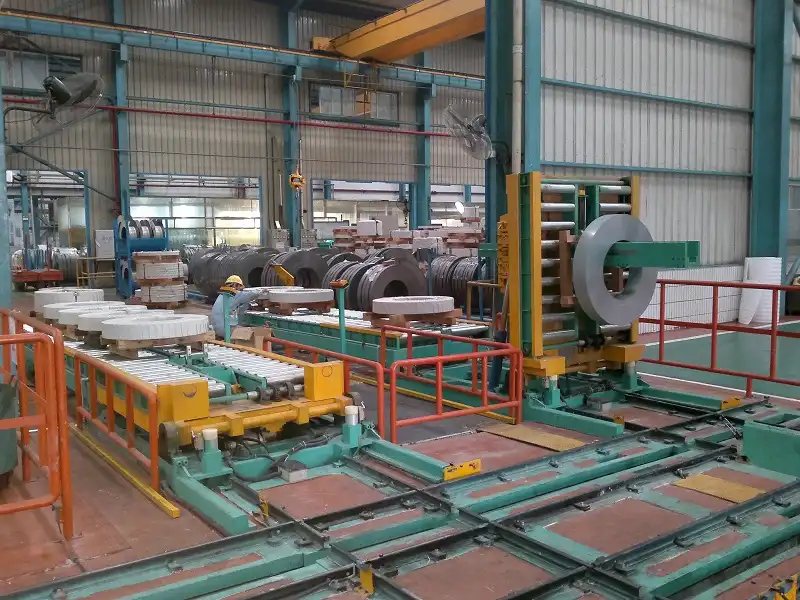
The Data You Didn't Know You Were Missing
When we connect a packing line to a factory's MES, managers are often amazed at the level of detail they can suddenly access. This isn't just about knowing if the machine is on or off. It's about granular data that drives real improvement. Key data points include:
- Coil ID: Automatically read from a barcode or upstream system.
- Entry/Exit Timestamp: Precise tracking of how long each coil spends in the packing station.
- Cycle Time: The exact time taken to wrap, strap, and label.
- Material Consumption: The precise length of stretch film and/or VCI paper used.
- Final Packaged Weight: Confirmed weight for shipping documents.
- Recipe Used: Which packing specification was applied.
- Error & Alarm Logs: A detailed record of any machine stoppages or warnings.
Bridging the Gap: PLC to MES Communication
At the heart of every modern machine is a PLC (Programmable Logic Controller). This is the machine's brain. In the past, this brain was isolated. Today, we build our systems with open connectivity. Think of it like making sure your machine speaks the same language as the rest of your factory. By using universal protocols like OPC-UA, we don't need complex, custom software to make them talk. It's a plug-and-play data connection that gives your MES direct access to the machine's brain, allowing for two-way communication. The MES can not only receive data but also send instructions to the packing line, such as which packing recipe to use for an incoming coil.
Data Point | How It's Used in MES | Benefit for Management |
---|---|---|
Cycle Time per Coil | Track Overall Equipment Effectiveness (OEE) | Identify performance drift, enable accurate scheduling |
Material Consumption | Reconcile inventory, calculate cost-per-coil | Optimize material ordering, prevent stockouts |
Error/Alarm Logs | Pinpoint recurring issues before they fail | Shift from reactive to proactive maintenance |
Coil ID Tracking | Provide end-to-end product traceability | Improve quality control, provide proof to customers |
The Power of Predictive Maintenance
This integration is the foundation for achieving goals like 95% uptime. By adding simple IoT sensors—to monitor motor vibration, temperature, and pneumatic pressure—we can feed this data into your analytics platform. The system can then learn the machine's normal operating signature. When it detects a subtle change, like a slight increase in a motor's temperature over several days, it can automatically generate a maintenance alert before the component fails. This is the shift from fixing broken machines to preventing them from breaking in the first place. For a CEO like Javier, this means more predictable output, fewer unplanned shutdowns, and a much higher return on his equipment investment.
Can Modern Packing Machines Lower Energy Consumption and Material Waste?
Energy prices are volatile, and raw material costs are always on the rise. You've likely already optimized your main production processes for efficiency, but what about your packing line? An older wrapping machine can be a significant energy hog, with motors running constantly, and an inefficient design can waste a shocking amount of stretch film or VCI paper. Every meter of wasted film and every kilowatt-hour of unnecessary electricity usage is a direct hit to your profit margin. With growing pressure to meet environmental standards and the constant need to control costs, turning your packing operation into a model of efficiency is no longer optional; it's a competitive necessity. The good news is that modern machines are specifically engineered to address this, using advanced technology to deliver dramatic cuts in both energy and material consumption.
Yes, modern coil packing machines are designed to significantly lower energy consumption and material waste. This is achieved through core engineering features like using Variable Frequency Drives (VFDs) on all major motors, so they only draw the power needed for the task at hand. Critically, they incorporate powered pre-stretch carriages that can elongate wrapping film by up to 300% or more. This means one meter of film on the roll becomes four meters on the coil, drastically reducing the amount and cost of film required to securely package each product.
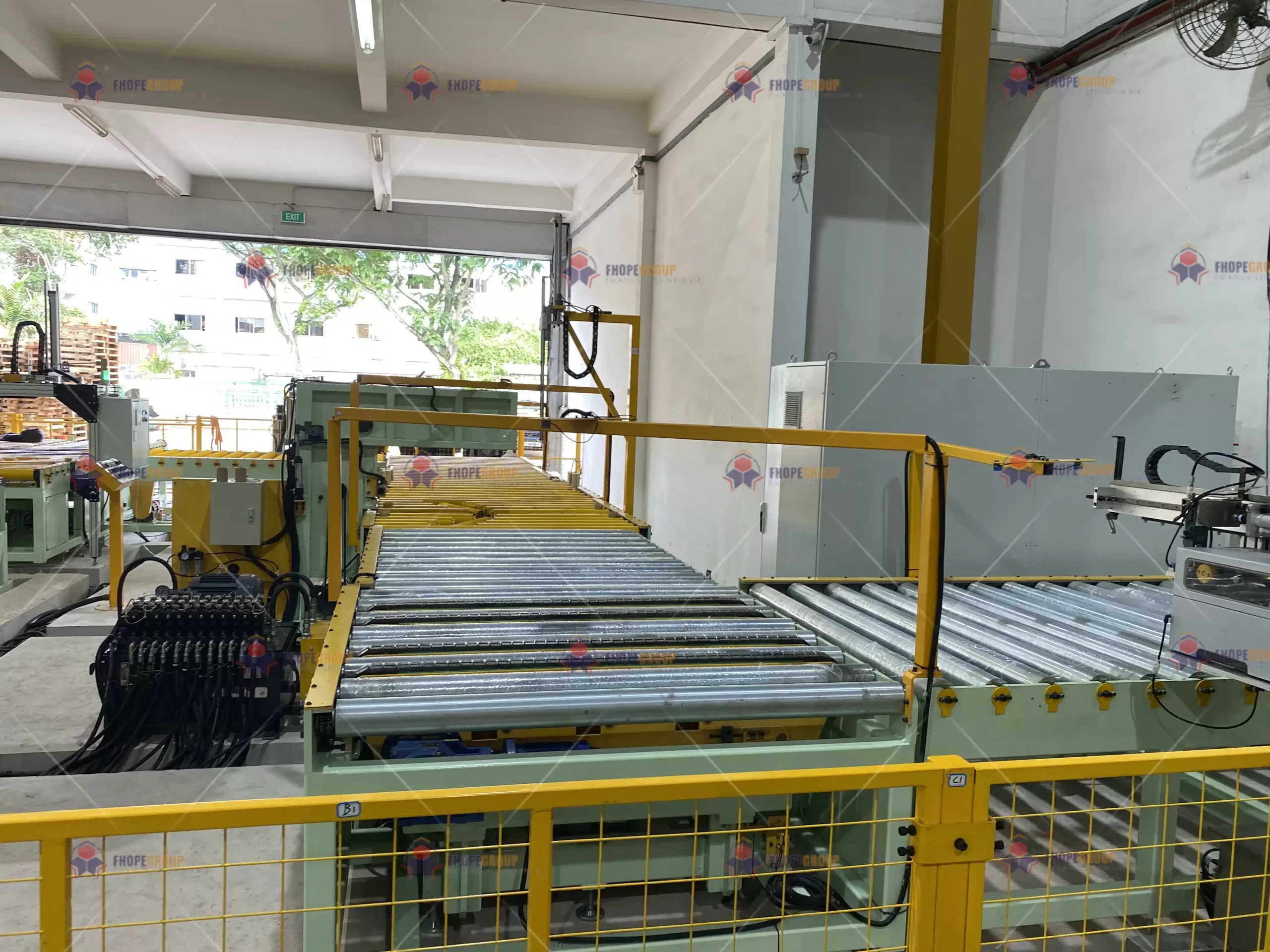
Targeting Energy Hogs: The VFD Revolution
In older machine designs, a large electric motor often runs at 100% speed all the time, even when the machine is idle between coils. It's like leaving your car engine revving at full throttle at a red light. It's an incredible waste of energy. Modern machines use Variable Frequency Drives (VFDs) on all major motors—the main ring, the conveyors, the film carriage. A VFD is a smart controller that adjusts the motor's speed and power consumption to match the exact need of the moment. The motor ramps up smoothly for the wrapping cycle and then slows to a crawl or stops completely during idle times. This simple change can reduce the machine's total electricity consumption by 30-50% compared to an older, fixed-speed design.
The Financial Magic of Pre-Stretch
This is one of the most important technological advancements in wrapping, and it's something I always emphasize with my clients. The pre-stretch carriage is a system of rollers that stretches the film before it's applied to the coil. By stretching the film, we increase its yield and its strength. A standard carriage might achieve a 250% pre-stretch. This means that for every 1 meter of film pulled from the roll, 2.5 meters are created to wrap the coil. High-performance systems can reach 300-400%.
Let's look at the numbers. Assume you are using 1kg of film to wrap a coil with an old machine. A modern machine with 300% pre-stretch can provide the same or better holding force using just 0.25kg of film. That's a 75% reduction in material consumption. If you wrap 100 coils per day, the savings are enormous. This single feature often provides a return on investment in less than a year, purely from the reduction in film purchasing costs.
Efficiency Feature | How It Works | Impact on Costs | Environmental Benefit |
---|---|---|---|
Variable Frequency Drives | Matches motor power to real-time need | Lowers electricity bill by 30-50% | Reduced carbon footprint |
Powered Pre-Stretch | Stretches film before application | Reduces film consumption by 50-75% | Drastically less plastic waste |
Precise Film Cut & Clamp | Automated, clean film cut at cycle end | Eliminates long, wasteful film tails | No scrap material on the floor |
Programmable Recipes | Uses exact material amount for each coil size | Prevents operator overuse on smaller coils | Optimized material usage for every product |
Precision Eliminates "Just in Case" Waste
Manual packing is inherently inconsistent. One operator might use three wraps of paper, while another, being extra cautious, might use five "just in case." This leads to massive, un-tracked waste. An automated system is precise. When you program a recipe for a specific product, the machine will use the exact, optimal amount of wrapping material every single time. This consistency not only saves material but also improves the quality and appearance of your final product, enhancing your brand's reputation with your customers.
My Insight
Over my years in this industry, from my early days as an engineer on the factory floor to founding SHJLPACK, I've seen that the biggest challenges often hide in plain sight. I once visited a potential client in Mexico, a man much like Javier—incredibly sharp, pragmatic, and the owner of a very successful, but aging, steel plant. He walked me through his facility, and his frustration was obvious. He pointed to his packing bay and said, "Vincent, everyone tells me to automate, but look at this mess. It's impossible. We'd have to tear down that wall."
He saw an obstacle. I saw a puzzle. I didn't start by talking about our machines. I asked him to walk me through his process, from the slitter to the loading dock. We spent two hours just watching his people work, measuring distances, and sketching on a notepad. The problem wasn't the wall; it was the linear thinking that every machine had to be a straight line.
I drew a simple diagram showing a modular concept: a wrapping station here, a 90-degree transfer car there, and a strapping unit tucked into an unused corner. His engineers were skeptical at first. But when we laid it out, they saw it. It wasn't about the machine's specifications; it was about the operational flow. He wasn't just buying a piece of equipment; he was buying a solution to a problem that had plagued him for a decade. He was investing in a strategic partner who took the time to understand his unique factory. A few months ago, he sent me a video of the line running, with a simple message: "It works."
That's what this is all about for me. It's about sharing that knowledge and experience to solve real-world problems. The best solution is rarely the most obvious one. It’s the one that’s designed for you.
Conclusion
Flexible, modular coil packing machines are not just equipment. They are strategic solutions that adapt to your space, cut your costs, and prepare your factory for a digital future.