How Strategic Coil Packing Automation Can Solve a Steel Mill CEO's Biggest Challenges
You are running a massive steel mill. You face constant pressure from fluctuating energy costs, aging equipment, and strict environmental rules. On top of that, market demand is a moving target. It feels like you are fighting battles on multiple fronts just to protect your profit margins. Every day, an older machine could break down, halting your entire production line. A sudden spike in electricity prices could wipe out the profits from a major order. You know you need to modernize, but a wrong investment could be a costly mistake. The stakes are incredibly high. What if you could turn one of your final production stages—coil packing—into a strategic asset? A modern, automated packing line does not just wrap steel. It can directly combat your biggest challenges, cutting costs, boosting efficiency, and preparing your mill for the future.
Yes, strategic coil packing automation can fundamentally solve a steel mill CEO's most pressing challenges. By replacing aging, inefficient equipment with an integrated, automated system, you can reduce labor and energy costs, minimize downtime through predictive maintenance, and ensure consistent, high-quality packaging that meets customer demands. This investment directly boosts your production stability and bottom line.
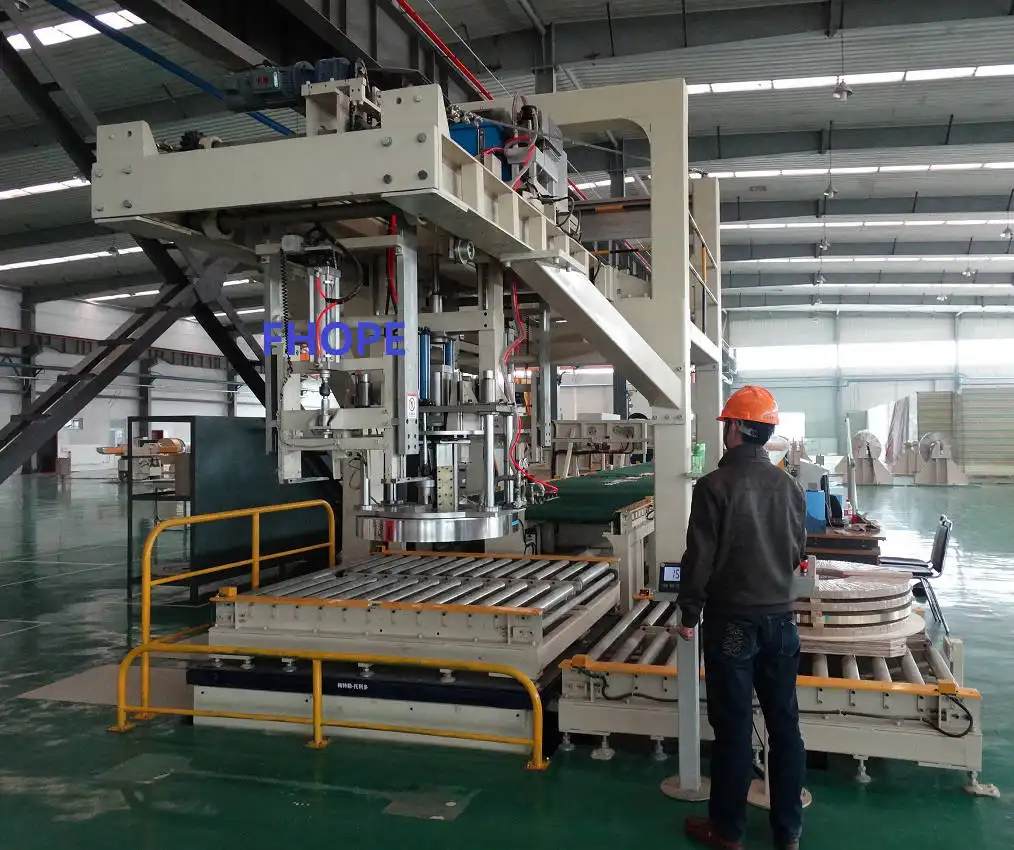
I understand the hesitation. You are not just buying a machine; you are making a strategic decision that impacts your entire operation. You need to know exactly how this investment will pay off. Let's break down how a modern packing line can address each of your key concerns, one by one. I have been in this industry for decades, first as an engineer on the factory floor and now as a factory owner myself. I have seen firsthand what works.
How can automated packing lines tackle rising operational costs and market volatility?
Your operational costs are a constant worry. Energy bills are unpredictable. Labor costs keep rising. And when the market for steel dips, you are forced to find savings everywhere. This can sometimes compromise quality or safety. This balancing act is exhausting. You might delay essential maintenance to save cash, only to face a bigger, more expensive breakdown later. Or you might be fully staffed for a big order that gets downsized, leaving your team underutilized and your costs high. You feel trapped in a reactive cycle. An automated coil packing line offers a powerful way to break this cycle. It gives you predictable, controllable costs in one key area of your plant. It operates with minimal manpower and optimized energy use, giving you a stable cost base, no matter how the market fluctuates.
Automated packing lines directly combat operational costs and market volatility by replacing variable labor expenses with a fixed, predictable asset. They use energy more efficiently than older equipment and reduce consumable waste. This creates a stable, lower-cost process that protects your margins, even when market demand or energy prices are unstable.
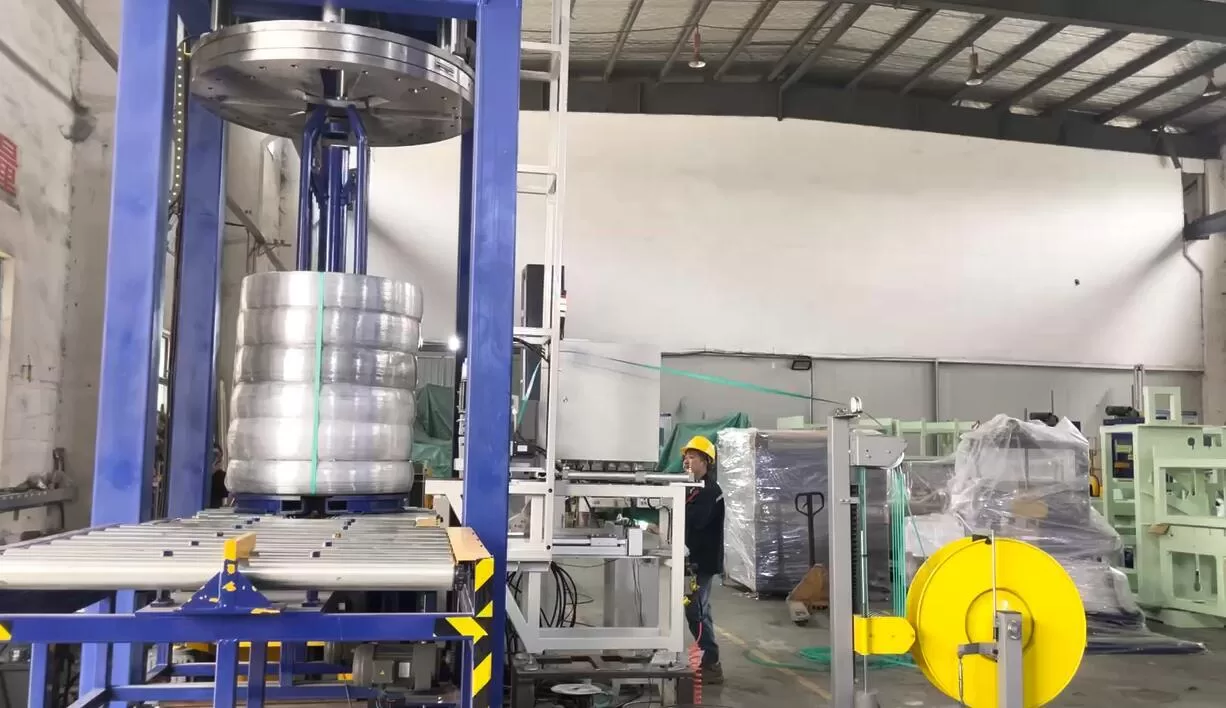
Let's get into the specifics of how this works. I have worked with many steel mill owners like you, Javier, who are brilliant at making steel but are frustrated by the final 100 meters of their production line. The packing area is often seen as a cost center, not a place for strategic advantage. I am here to change that perspective.
Breaking Down the Cost Savings
An automated packing line attacks costs from multiple angles. It is not just about one big saving; it is about dozens of small, consistent improvements that add up.
- Labor Reduction: Manual or semi-automatic packing requires a team of workers. They need salaries, benefits, training, and supervision. An automated line can often be managed by a single operator overseeing the entire process from a control panel. This does not just cut payroll; it frees up your skilled workers to focus on more complex tasks elsewhere in the mill.
- Material Efficiency: Every coil needs to be wrapped. How much packing material are you using? Are you sure it is the optimal amount? Automated systems are precise. They apply the exact amount of VCI paper, stretch film, or strapping needed for secure transport, every single time. This eliminates the "little bit extra" that workers often add. This waste can add up to thousands of dollars over a year.
- Energy Optimization: Older machines are often energy hogs. They run continuously, even when there is no coil to pack. Modern systems are smarter. They use high-efficiency motors, variable frequency drives (VFDs), and sensors. These components put the machine into a low-power standby mode when idle. This can cut the packing line's energy consumption significantly, directly addressing your challenge with volatile electricity prices.
A Buffer Against Market Swings
Market volatility is a reality in the steel industry. How does an automated packing line help? It provides operational flexibility.
- Scalable Throughput: When demand is high, the line can run 24/7 at maximum speed without worker fatigue. You can meet tight deadlines and capture market opportunities.
- Cost Control in Downturns: When demand is low, you do not have to worry about paying a full packing crew. The line's operational cost is minimal when it is not running. This allows you to manage downturns more effectively, protecting your profitability until the market recovers.
Here is a simple comparison:
Cost Factor | Manual/Semi-Auto Packing | Fully Automated Packing Line |
---|---|---|
Labor | 3-5 operators per shift | 1 operator/supervisor per shift |
Material Use | Inconsistent, often excessive | Precise, optimized, minimal waste |
Energy | Constant high draw | Variable draw, standby modes |
Throughput | Limited by worker speed/fatigue | Consistent, high-speed, 24/7 capable |
Cost Structure | High variable costs | High fixed cost, low variable costs |
I remember a client whose packing team was a constant source of overtime costs during busy periods. After installing an automated line, not only did his overtime budget disappear, but his material savings in the first year alone were enough to cover nearly 15% of the machine's cost. This is the kind of tangible, predictable result that a strategic investment should deliver.
Can new packing equipment integrate with aging production lines and digital systems?
You have invested heavily in your core production equipment over the years. Some of it is old but reliable. Now you are looking at new technology. But you worry it will not "talk" to your existing machinery or your new digital platforms. The nightmare scenario is buying a state-of-the-art packing line that creates a bottleneck. It cannot get data from your upstream process. Or it cannot feed information into your MES (Manufacturing Execution System). You are left with a disconnected "island of automation" that causes more problems than it solves. Modern packing equipment is designed specifically for integration. A good supplier does not just sell you a machine; they provide an engineering solution. This solution ensures seamless communication between your old and new systems, creating a truly connected production flow from the furnace to the shipping dock.
Yes, new packing equipment can and should integrate with both aging production lines and modern digital systems. Through customized conveyors, sensors, and communication protocols like OPC-UA or Profinet, a new packing line can receive coils from older equipment and feed real-time data directly into your MES and ERP systems, bridging the gap between your physical and digital operations.
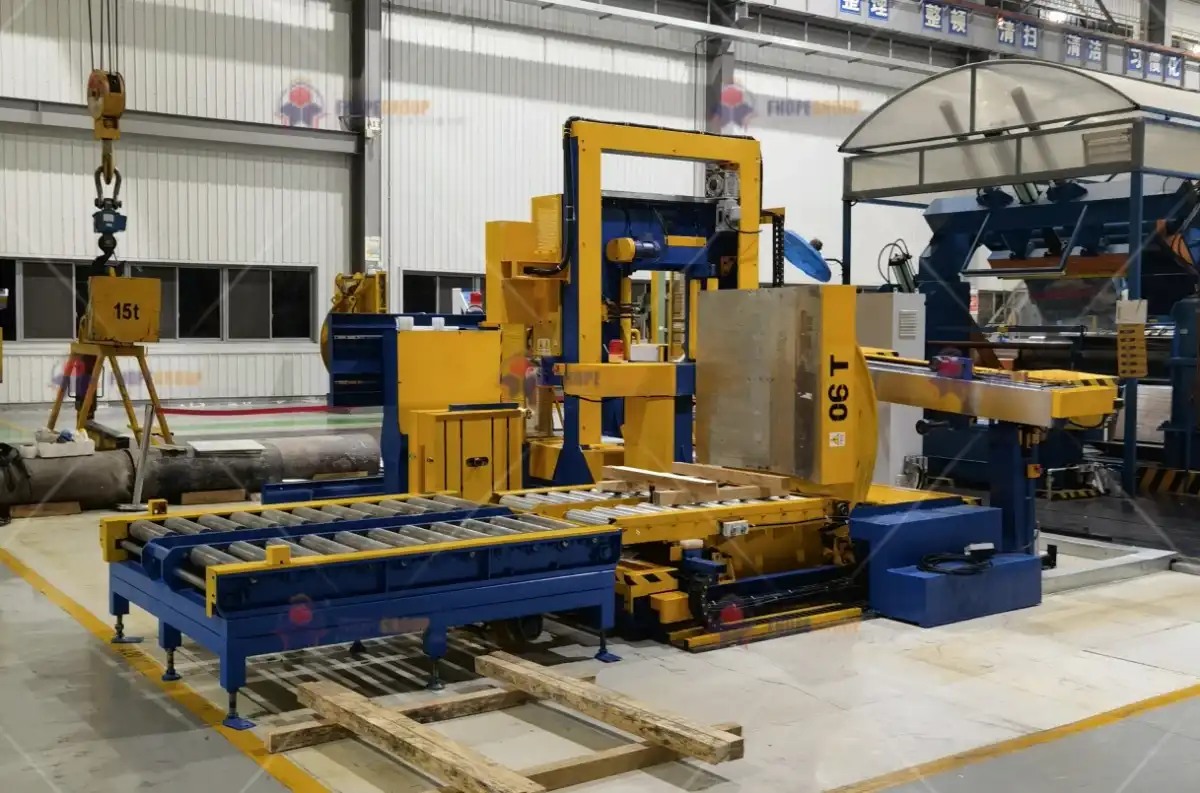
This is a critical point, and it is where a true engineering partner shines. As an engineer myself, I know that integration is not just about plugging in a cable. It is about understanding the entire production flow. Your goal of deploying MES, IoT sensors, and big data analytics is exactly the right path. Your packing line must be an active participant in this digital ecosystem, not a passive endpoint.
Bridging the Physical Gap: Connecting to Aging Lines
Many steel mills have a mix of equipment from different eras. Your rolling mill might be 20 years old, while your crane system is 10 years old. A new packing line needs to physically connect to whatever is upstream. How do we do that?
- Customized Conveying: We do not use a one-size-fits-all approach. We analyze your plant layout, floor space, and the output of your existing lines. We then design the entry and exit conveyors of the packing line to match perfectly. This could involve turnstiles, walking beams, or shuttle cars to smoothly transport coils from your existing infrastructure to the new packing station.
- Sensors and Triggers: We can place sensors on your older equipment. For example, a simple photo-eye sensor can detect when a coil is ready to be moved from the annealing line. This signal can trigger the automated conveyor system. This creates a seamless handover without manual intervention. It is a simple, reliable way to make old and new equipment communicate.
Bridging the Digital Gap: Connecting to Your MES/IoT Platform
Achieving your goal of 95% equipment uptime and comprehensive production visualization depends on data. Your new packing line should be a rich source of it.
- The Data Hub: A modern packing line's PLC (Programmable Logic Controller) is the brain. It knows everything: which coil is being packed, what packing materials are being used, the cycle time, any errors that occurred, and the total energy consumed.
- Seamless Communication: This data needs to get to your MES. We ensure the PLC can speak the same language as your central system. Common protocols we use include:
- OPC-UA: A secure, platform-independent standard perfect for modern factories.
- Profinet/EtherNet/IP: Industrial Ethernet protocols for high-speed communication.
- APIs and Databases: We can even have the packing line write data directly to a SQL database or communicate via a custom API if your system requires it.
Here is what that data flow looks like in practice:
Data Source (Packing Line) | Information | Destination (Your System) | Strategic Benefit |
---|---|---|---|
Coil ID Scanner | Unique identifier for each coil | MES / ERP | Tracks product from start to finish. Ensures correct packing recipe is used. |
Cycle Timers | Start/end time for each packing step | MES / Big Data Platform | Identifies bottlenecks. Helps with smart scheduling and capacity planning. |
Sensor Readings | Motor temperature, vibration, pressure | Predictive Maintenance System | Predicts failures before they happen, moving you from reactive to proactive maintenance. |
Material Sensors | Film/paper/strapping levels | ERP / Inventory System | Automatically re-orders consumables, preventing stock-outs and production stops. |
When I started my journey, I was an engineer on the floor. I was often frustrated by machines that could not talk to each other. That is why at SHJLPACK, we made integration a core part of our design philosophy. A machine that gives you data is a machine that helps you make better decisions. It is essential for achieving the kind of digital transformation you envision for your mill.
What makes a packing machine supplier a true strategic partner, not just a vendor?
You have dealt with countless suppliers. Many promise the world before the sale, but disappear once the check is cashed. They sell you a product, not a solution. When a problem arises—a complex installation, a need for a custom part, or a software glitch—a vendor might be slow to respond. Or they might charge you for every minute of their time. You are left feeling unsupported. And your expensive new equipment is not delivering the value you expected. A strategic partner works with you for the long term. They invest time to understand your business, your challenges, and your goals. They co-create a solution with your team. And they provide comprehensive support throughout the entire lifecycle of the equipment, from initial design to ongoing optimization.
A strategic partner, unlike a vendor, provides end-to-end support that goes far beyond the initial sale. They offer in-depth consultation during the selection phase, customized engineering for seamless integration, on-site installation and training, and proactive after-sales service, including maintenance and future-proofing advice for your digital transformation and environmental compliance.

Javier, your perspective is spot-on. You are not looking for a transaction; you are looking for a partnership. This is a philosophy I have built my company on. I started as an employee in a packing machine factory. I saw firsthand how a lack of support from suppliers created huge problems for customers. When I founded my own factory, I vowed to do things differently. I achieved my own success by helping my clients succeed. That is what partnership means to me.
The Vendor vs. Partner Checklist
How can you tell the difference? A vendor focuses on the what (the machine). A partner focuses on the why (your business goals). Here is a breakdown of what to look for.
Aspect | A Typical Vendor Does This | A Strategic Partner Does This |
---|---|---|
Pre-Sale | Sends a standard catalog and price list. | Conducts a detailed site visit. Analyzes your production flow, space, and goals. Asks about your challenges. |
Proposal | Offers a standard machine model. | Presents a customized solution, explaining how each feature addresses your specific needs (e.g., cost reduction, MES integration). |
Installation | Ships the machine with a manual. May offer installation for an extra fee. | Manages the project. Sends a dedicated engineering team for installation, commissioning, and integration with your existing lines. |
Training | Provides a basic operational manual. | Conducts comprehensive on-site training for your operators and your maintenance team. Ensures your people are confident and capable. |
After-Sales | Has a reactive customer service hotline. Sells you spare parts when you call. | Provides a dedicated point of contact. Offers proactive maintenance plans, remote diagnostics, and regular check-ins to optimize performance. |
Future Focus | Sells you a new machine when yours is outdated. | Advises you on upgrades, software updates, and how to adapt the equipment for future needs, like new environmental regulations. |
The Partnership in Action
Let me give you a real-world example. We worked with a steel company that was facing new, stricter government regulations on packaging waste. A vendor would have simply sold them a machine that used a different wrapping material. As a partner, we did more.
- We researched the regulations: We worked with them to understand the exact requirements for material reduction and recyclability.
- We tested new materials: We used our R&D facility to test thinner, stronger, and more eco-friendly stretch films on our machines. We found one that met the regulations without compromising coil protection.
- We modified the machine program: We adjusted the tension controls and pre-stretch ratio on their new packing line's software to optimize the use of this new film.
- We provided documentation: We gave them the data to prove their compliance to the authorities, showing a quantifiable reduction in plastic consumption per ton of steel.
This is the difference. A vendor sells you a tool. A partner helps you solve your business problem. Your search for a partner who can provide professional advice on digitalization and environmental compliance is exactly the right mindset. You need someone who is invested in your success because their success depends on it.
How does modern coil packing equipment address environmental pressures and improve safety?
The pressure to be "green" is immense. Governments are enforcing stricter environmental standards. Your customers are starting to ask about your carbon footprint. At the same time, ensuring the safety of your workers is non-negotiable. You worry about the high cost of compliance. Fines for violating emissions standards can be steep. The investment in greener technology feels like a purely defensive move. Worse, a single safety incident in the hazardous packing area could be devastating for your team and your company's reputation. Modern coil packing equipment is designed with sustainability and safety at its core. It is not about just meeting the minimum standard. It is about transforming your packing operation into a showcase of efficiency, responsibility, and workplace safety.
Modern coil packing equipment addresses environmental pressures by using energy-efficient motors, minimizing the consumption of packing materials, and being compatible with recyclable films. For safety, it incorporates comprehensive guarding, light curtains, emergency stops, and automated handling to eliminate the need for workers to be in close proximity to heavy, moving machinery, drastically reducing accident risks.
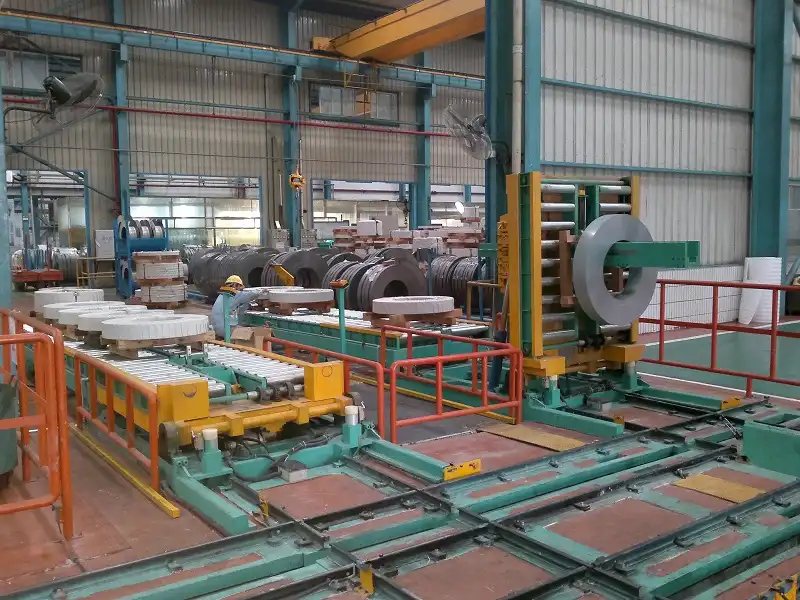
As a factory owner, I share your concerns about environmental responsibility and worker safety. These are not just line items on a budget. They are fundamental to running a sustainable, reputable business. Investing in the right equipment allows you to tackle both challenges simultaneously. Let's explore how.
Achieving Your Environmental Goals
Your goal to reduce unit energy consumption by 10% is ambitious and commendable. The packing line can be a significant contributor to this.
- Energy Efficiency: As I mentioned earlier, new machines with VFDs and smart standby modes are a world apart from old, continuously-running equipment. A simple motor upgrade on a large machine can save thousands of kilowatt-hours per year. Think of it as installing energy-saving lightbulbs, but on an industrial scale.
- Material Reduction (Source Reduction): The most effective way to deal with waste is to not create it in the first place.
- Optimized Wrapping: A key feature of our orbital wrappers is the powered pre-stretch carriage. It can stretch wrapping film by up to 300%. This means 1 meter of film from the roll becomes 4 meters of film on the coil. You use significantly less plastic while achieving a stronger, more secure wrap.
- Precision Strapping: Automated strappers apply the exact tension needed and place straps precisely. This avoids wasted strapping material and ensures the coil is secure with the minimum material necessary.
- Supporting a Circular Economy: We design our equipment to be compatible with a wide range of packing materials. This includes materials made from recycled content and those that are fully recyclable. This allows you to adapt to changing market demands for sustainable packaging.
Creating a Safer Workplace
The area around a coil packing line can be dangerous. You have heavy coils, moving conveyors, and powerful machinery. Automation is the single most effective way to improve safety.
Hazard in Manual Packing | How Automation Eliminates It | |
---|---|---|
Manual Strapping | Workers are close to the coil, handling sharp steel or plastic strapping under tension. Risk of cuts and eye injuries. | The entire strapping process is done inside a guarded machine. The operator is safely behind a control panel. |
Lifting and Moving Materials | Workers manually lift heavy rolls of VCI paper or stretch film. Risk of back injuries. | Automated systems have cranes or lifts to load large consumable rolls. The process is mechanized. |
Proximity to Moving Coils | Workers are on the floor near moving conveyors and turntables. Risk of crushing or impact injuries. | The entire line is fenced off. Light curtains create an invisible safety barrier that instantly stops the machine if a person crosses it. |
Repetitive Strain Injuries | Manual wrapping and handling tasks are highly repetitive. | The machine performs all repetitive tasks. The operator's role becomes one of supervision and quality control. |
I have walked through hundreds of factories. The difference between the safety culture in a plant with manual packing and one with a fully automated line is night and day. Automation removes your people from harm's way. It turns a hazardous job into a skilled technical role. This also helps with employee retention and morale. It is an investment in your people as much as it is an investment in steel.
Conclusion
Strategic packing automation is not just an upgrade. It’s a powerful tool to cut costs, boost efficiency, integrate systems, and build a safer, more sustainable steel mill.