Are you running a steel plant in Canada and struggling with inconsistent packing, high labor costs, and safety concerns on your packing line? I see it all the time. Manual or semi-automatic processes become a bottleneck. They slow down your entire production output. Every minute of downtime or slow packing means lost revenue. Inconsistent wrapping can lead to damaged coils during transport. This results in customer complaints and costly returns. And I know finding and retaining skilled labor for such physically demanding jobs is a constant battle. You watch your operational costs rise while your competitors who've embraced automation pull ahead. Many forward-thinking Canadian steel plants are discovering the answer lies in full automation. A fully automated coil packing line isn't just an upgrade. It's a complete transformation of your end-of-line process, designed to solve these exact problems.
Canadian steel plants are adopting fully automated coil packing lines primarily to combat rising labor costs and overcome skilled worker shortages. These systems also enhance workplace safety and significantly improve operational efficiency. Automated lines ensure consistent, high-quality packaging 24/7. This reduces product damage and increases throughput to meet demanding market needs.
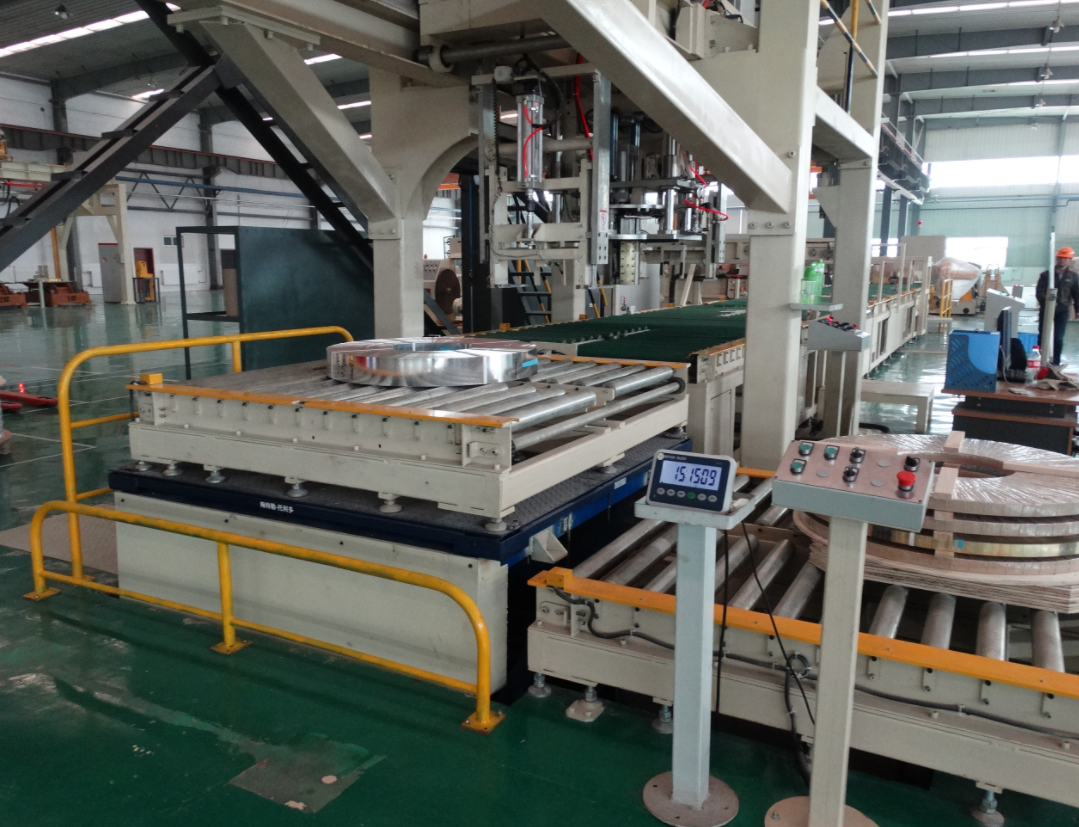
This shift isn't just a trend. It's a strategic move to build more resilient and profitable operations. But I know what you might be thinking. As someone who started as an engineer and later built my own factory, I understand that any major investment requires a hard look at the details. I’ve been in your shoes. So, let's break down exactly how these systems deliver real value. We will look at how they address the core challenges you face every single day.
How Does Automation Directly Address the Soaring Labor Costs and Skills Shortages in Canada?
Does your wage bill for the packing line keep climbing? Is finding reliable workers for physically demanding, repetitive tasks getting harder each year? I talk to plant owners constantly, and this is a major headache. Every time an operator calls in sick or quits, your entire production schedule takes a hit. This constant cycle of hiring and training is a huge drain on your resources. You're not just paying salaries. You're paying for recruitment, training, and the inevitable slowdowns that come with staff turnover. This instability makes it almost impossible to plan for consistent output. A fully automated coil packing line directly replaces the most labor-intensive parts of the process. It operates continuously with minimal human supervision. This effectively decouples your packing capacity from a volatile labor market.
Automation directly addresses labor costs by reducing the number of operators needed per shift. This minimizes expenses related to wages, benefits, and recruitment. It also solves the skills shortage by taking over the repetitive, physically demanding tasks. This allows you to reassign your valuable human team members to more complex, value-added roles that are easier to fill and retain.
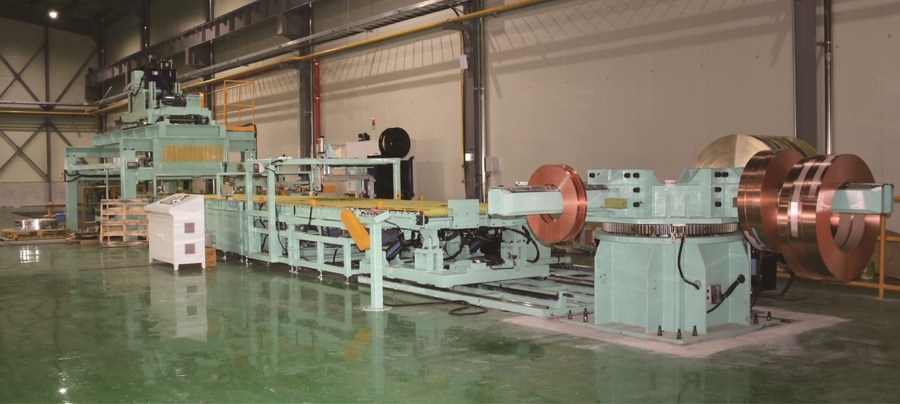
Breaking Down the True Labor Cost Savings
When we talk about labor costs, it’s easy to just think about hourly wages. But the real costs run much deeper. I encourage my clients to look at the complete picture. You have direct costs, like salaries and mandatory benefits. But then you have the indirect costs. These include recruitment agency fees, the time your HR team spends on hiring, and the weeks of a supervisor's time spent on training new people who might leave in six months. Then there is overtime pay when you're short-staffed but need to meet a deadline. These costs add up quickly.
An automated system runs three shifts a day, seven days a week, without needing a break. The financial impact is significant. Let’s look at a simple comparison.
Cost Factor | Typical Manual Line (3 Operators/Shift) | Fully Automated Line (1 Supervisor/Shift) |
---|---|---|
Operators Needed (24/7) | 9 - 12 | 3 - 4 |
Direct Wages | High | Significantly Lower |
Overtime Costs | Frequent | Minimal / Eliminated |
Recruitment & Training | Constant & Ongoing | Minimal (Initial Training) |
Injury & Compensation | Higher Risk | Drastically Reduced Risk |
By reducing the headcount on the packing line from a team of 9-12 to a team of 3-4 supervisors, you are not just cutting the wage bill by two-thirds. You are eliminating a huge administrative and operational burden. This frees up capital and management focus for other growth areas in your plant.
Re-skilling and Re-deploying Your Workforce
One of the best things I've seen is how automation transforms jobs for the better. This isn’t about replacing people. It's about elevating them. Nobody enjoys the physically draining, repetitive work of manually strapping and wrapping heavy steel coils. It's tough on the body and mind. A machine can do that part. This frees your people to use their brains. We had a client in Ontario who was facing a massive turnover issue on their packing line. After installing an automated line, they re-trained their former packing crew. These employees became system operators, quality control inspectors, and preventive maintenance technicians. Their job satisfaction skyrocketed. They were no longer laborers; they were skilled technicians managing advanced equipment. The company kept its experienced, loyal employees, and the employees gained new, valuable skills. This is the real win-win of automation.
Can a Fully Automated Packing Line Really Boost Throughput and Maintain Quality Consistency?
Is your packing station the main bottleneck in your plant? It's a common problem. Your slitting and rolling lines are modern and efficient, but then the coils start piling up, waiting to be strapped, wrapped, and labeled. This traffic jam at the end of the line slows down your entire operation. This bottleneck means your expensive production machinery isn't running at full capacity. And that's lost money. Even worse, rushed manual packing leads to inconsistent quality. Some coils get wrapped too loosely, risking damage from moisture. Others are wrapped too tightly, which can be a safety hazard. This leads to customer dissatisfaction and potential claims. A fully automated packing line is engineered for speed and precision. It works in perfect sync with your production output. It eliminates the bottleneck and ensures every single coil is packed to the exact same high standard, every single time.
Yes, a fully automated packing line significantly boosts throughput by operating at a consistent, high speed that matches or exceeds production line output, eliminating bottlenecks. Quality consistency is maintained because the machine applies wrapping materials, straps, and labels with robotic precision, following pre-programmed parameters for every coil size and type, which removes the element of human error.

The Mechanics of Increased Throughput
Think about a manual packing process. A coil arrives. An operator needs to guide it, position it, apply the strapping, move it to a wrapper, wrap it, and then move it again. Each step involves human intervention, judgment, and physical movement. There are natural pauses and variations in speed. Now, contrast that with an automated line. A conveyor brings the coil from your slitter directly to the packing line. Sensors detect its arrival and dimensions. The coil is automatically centered. A robotic arm applies the straps at precise intervals. It then moves seamlessly into the wrapping station, where the through-eye wrapper applies the packaging material with a specific, pre-set overlap. Finally, it moves to an automatic weighing and labeling station before being transported to the stacking area.
The entire process is a continuous, fluid motion. There are no unnecessary stops. The cycle time for each coil is predictable and consistent.
Process Step | Manual Operation | Automated Operation |
---|---|---|
Coil Transfer & Centering | 1-2 minutes, variable | 20-30 seconds, consistent |
Strapping | 2-3 minutes, variable placement | 30-45 seconds, precise placement |
Wrapping | 2-3 minutes, inconsistent overlap | 45-60 seconds, perfect overlap |
Labeling & Weighing | 1 minute, risk of error | 15 seconds, automated & accurate |
Total Estimated Time | 6-9 minutes | 2-3 minutes |
As you can see, an automated line can easily be two to three times faster. It directly clears the bottleneck, allowing your primary production equipment to run at its true capacity.
Achieving Perfect, Repeatable Quality
Quality is about consistency. Your customers expect their coils to arrive in perfect condition. An automated system guarantees this. In the system's control panel (HMI), you can program specific "recipes" for each customer or product type. For a sensitive aluminum coil, you might specify a gentle wrap with VCI paper. For a heavy-duty steel coil, you might program three steel straps and a layer of waterproof stretch film. Once programmed, the machine executes that recipe perfectly every time. Sensors control the wrapping tension, ensuring it's never too tight or too loose. The strapping head applies straps at the exact same position on every coil. This level of precision is simply not possible with manual labor, no matter how skilled your team is. I worked with a steel service center that was dealing with a 5% product damage rate due to moisture during shipping. After installing our automated line with specific wrapping parameters, their damage claims dropped to virtually zero within three months. This didn't just save them money; it strengthened their reputation as a high-quality supplier.
What Role Does Data and Integration Play in Modern Automated Coil Packing Systems?
Do you feel like your packing and shipping area is a "black box"? You have good data from your production line. But once a coil is finished, you lose visibility. This makes it hard to track inventory, verify production counts, and plan logistics efficiently. This lack of data often leads to manual data entry errors. These errors cause inventory discrepancies and delays in generating shipping documents. It means you can't make fast, informed, data-driven decisions about your end-of-line processes. You simply don't have the information in real-time. Modern automated packing lines are not just machines. They are intelligent data hubs. We design them to integrate seamlessly with your plant's MES (Manufacturing Execution System) and ERP (Enterprise Resource Planning) systems. This provides total visibility from the moment a coil is produced to the moment it is dispatched.
Data and integration are central to modern automated coil packing systems. They connect to the plant's MES or ERP to receive coil data like ID, dimensions, and customer specs. In return, they send back real-time status updates, final weight, and packaging details. This enables full product traceability, automated labeling, and data analysis for process optimization and predictive maintenance.
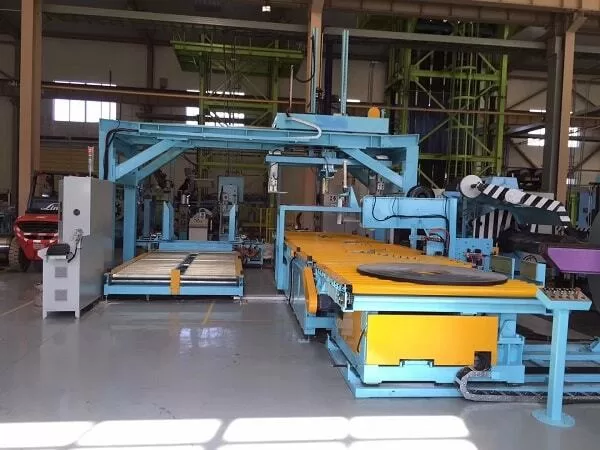
The Seamless Flow of Information
This integration works like a conversation between your systems. It’s a process I find fascinating because it eliminates so much human error. First, your MES sends a "birth certificate" for the coil to the packing line's PLC. This digital file contains the coil ID, weight, width, customer name, and the required packaging specification. The packing line receives this data. It automatically calls up the correct packing "recipe" you have programmed. The line then executes the process: strapping, wrapping, and so on. As it finishes, the integrated weigh scale captures the final packaged weight. A scanner verifies the coil ID one last time. The system then automatically prints a label with all the correct information—customer, dimensions, weight, barcode—and applies it to the coil. Finally, the packing line sends a "completion" signal back to your MES or ERP. This signal confirms the coil has been packed and provides the final, verified data. Your inventory is updated in real-time. Your shipping department has the information it needs instantly. The entire process is touchless and error-free.
From Raw Data to Actionable Insights
This data is not just for tracking. It's for improving your entire operation. Every action the machine takes can be recorded and analyzed. This is how you achieve the goals of higher efficiency and lower costs that every plant owner, including myself, strives for.
Data Point Collected | Actionable Insight Gained | Business Goal Addressed |
---|---|---|
Cycle Time per Coil | Identify efficiency trends, spot micro-delays. | Increase Capacity Utilization |
Packaging Material Used | Track consumption per coil, optimize recipes to reduce waste. | Reduce Operating Costs |
Motor Amperage / Faults | Detect signs of wear before a breakdown occurs. | Predictive Maintenance / Boost Uptime to 95% |
Coil Weight (In vs. Out) | Ensure billing accuracy and track material yield. | Improve Profitability & Quality Control |
By analyzing this data, you can move from a reactive maintenance model to a predictive one. You can fine-tune your operations for that extra 10% reduction in energy use or an 8% reduction in overall cost. This is the power of Industry 4.0, and it starts with having intelligent, connected equipment on your plant floor.
Beyond the Initial Install, What Does Long-Term Reliability and Support for an Automated Line Look Like?
You've probably been through this before. You invest a lot of money in new equipment, only to be let down by poor after-sales service. A machine is only as good as the support behind it. You absolutely cannot afford extended downtime while you wait for a technician to fly in or for a spare part to ship from overseas. When a critical piece of machinery like a packing line goes down, your entire plant can grind to a halt. The frustration of dealing with unresponsive suppliers and long lead times for parts is immense. It costs you more than just the repair bill; it costs you your production schedule and your reputation with customers. A true strategic partner, like us at SHJLPACK, understands that our relationship only begins at installation. We build our systems for durability. And we provide a comprehensive support structure that includes remote diagnostics, preventive maintenance programs, and readily available spare parts to ensure you get maximum uptime.
Long-term reliability for an automated line is built on a foundation of robust design, high-quality components, and proactive support. This includes remote diagnostic capabilities for quick troubleshooting, scheduled preventive maintenance programs to minimize unexpected failures, comprehensive training for your staff, and a strategic inventory of critical spare parts for rapid replacement.

Designing for Durability and Uptime
Reliability starts with the design and the components. It's something I learned early in my engineering career. Taking shortcuts is never worth it. That's why we build our machine frames from heavy-duty, welded steel, not bolted aluminum. We use oversized bearings and powerful, reliable motors from world-class suppliers like SEW or Siemens. We choose pneumatic and electrical components from brands like Festo and Schneider Electric. Why? Because these are not just high-quality parts; they are globally available. If a component fails in a remote part of Canada, your local industrial supplier is likely to have it in stock. This commitment to quality components drastically reduces the chance of unexpected breakdowns. It also makes repairs faster and easier when they are eventually needed after years of service. It's about building a machine that is prepared for the harsh reality of a 24/7 steel plant environment.
A Partnership Approach to Maintenance
Our job doesn't end when the machine is running. We see ourselves as your long-term partner in productivity. A key part of this is our support structure. First, every machine we build is equipped with a remote access module. If your team encounters an error or needs to adjust a setting, our engineers can securely log into your machine's PLC from our office. We can see exactly what your operator sees. We can diagnose the problem and guide your team through the solution in minutes, not days. This saves you the immense cost and delay of a service visit. Second, we work with you to develop a preventive maintenance schedule. We show your team what to check daily, weekly, and monthly. This proactive approach helps you catch small issues before they become big problems. Third, we provide a recommended list of critical spare parts to keep on-site. These are the key wear items that might need replacing over time. Having them on your shelf means a repair takes an hour, not a week. We believe that a well-trained team is the best defense against downtime. That's why we provide thorough training for both your operators and your maintenance staff. We don't just hand you a manual; we ensure your people are confident and capable of running and maintaining their new equipment.
What is the One Thing Most Steel Plant Owners Overlook When Considering Automation?
So, you've done the math. You have calculated the ROI, the labor savings, and the gains in throughput. The numbers on the spreadsheet look good. But there might be a nagging feeling that you're missing something. A hidden factor that could make or break the success of this entire project. I've seen this happen. Focusing only on the technical specifications and the financial returns can cause you to overlook the profound cultural impact that automation has on your company. If your team isn't prepared for the change, you can face resistance, fear, and a failure to fully leverage the new system's capabilities. This can undermine the very investment you worked so hard to justify. The most overlooked aspect is the human element. From my own journey, the most successful automation projects I have ever been a part of were the ones where the leadership viewed it not just as a machine installation, but as a catalyst for building a safer, more modern, and more engaging work environment for their team.
The single most overlooked factor when considering automation is its transformative impact on workplace culture and safety. Beyond the clear efficiency gains, a well-designed automated line drastically reduces physical strain and eliminates the most dangerous manual tasks. This leads to a safer work environment, higher employee morale, and a stronger company image that helps attract new, high-quality talent.
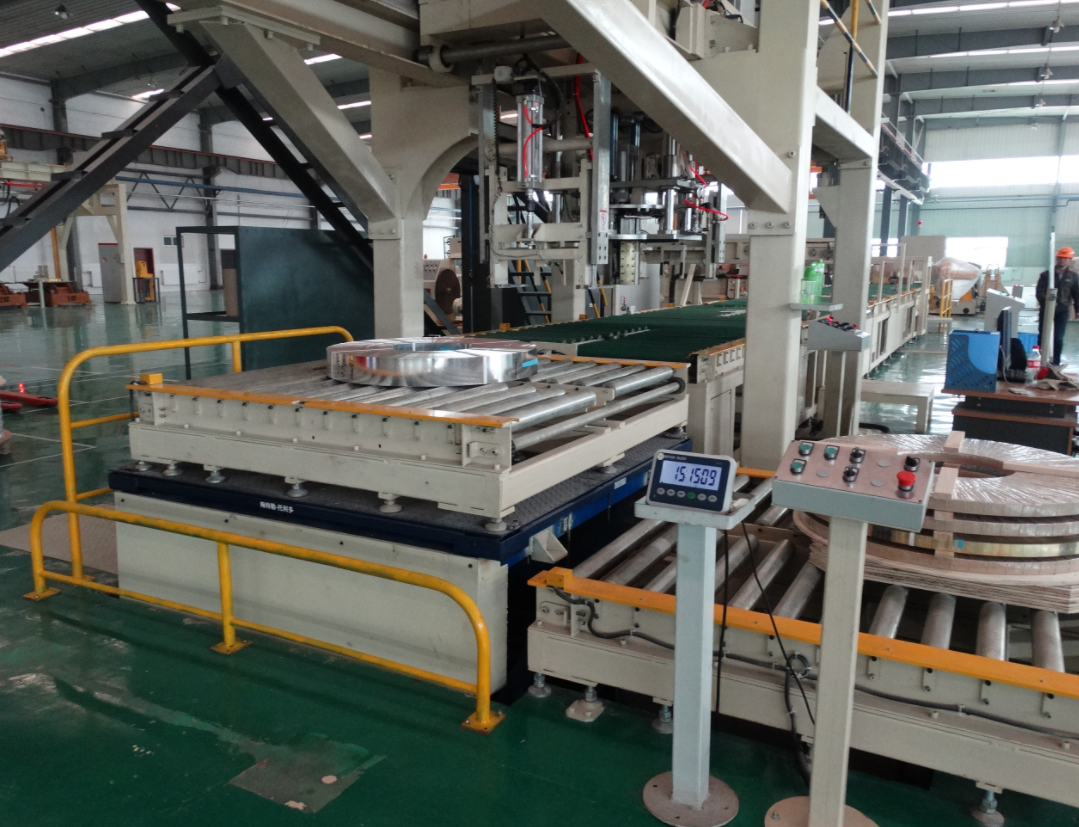
Safety: The Unquantifiable ROI
We can easily calculate the ROI on labor savings. But how do you calculate the ROI of preventing a career-ending injury? The manual packing area is one of the most hazardous places in a steel plant. I've seen it myself. Workers are constantly lifting, pushing, and pulling heavy materials. There are risks of back injuries, muscle strains, and repetitive stress injuries. There are sharp edges on coils and steel straps that can cause deep cuts. There are dangerous pinch points on manual equipment. I remember visiting a plant years ago, before I started SHJLPACK. Seeing the physical toll that this work took on people was one of the key reasons I became so passionate about finding a better way through automation.
A fully automated packing line removes your people from this "danger zone." The machine does all the heavy lifting and handling of sharp materials. Your team supervises from a safe distance. This drastically reduces your workplace accidents and workers' compensation claims. It creates a work environment where your employees feel safe and valued. This positive change in safety culture is one of the most powerful, though less-talked-about, benefits of automation.
Building a Company for the Next Generation
Finally, think about the future of your company. Automation is not just about competing today; it's about building a company that can attract the workforce of tomorrow. The next generation of workers has different expectations. They are not looking for physically punishing, manual labor. They grew up with technology, and they want to work with technology. A plant with modern, clean, automated equipment is a much more attractive place to work than an old-fashioned, manual-heavy factory. When you invest in automation, you are sending a clear message. You are telling current and future employees that you are a forward-thinking employer who invests in technology and in your people's well-being. When I started my own factory, my goal wasn't just to make a profit. It was to build something sustainable, something my team could be proud to be a part of. This is the ultimate goal that automation helps you achieve. It positions you as an industry leader and an employer of choice for years to come.
Conclusion
Adopting automation is a powerful, strategic decision. It enhances safety, boosts efficiency, and secures a Canadian steel plant's competitive edge for the future.