Your manufacturing facility in Canada faces a unique set of challenges. The extreme cold can seize up standard equipment, leading to unexpected downtime right when you need to meet production targets. On top of that, finding and retaining skilled labor for manual packing is a constant struggle, driving up costs and creating inconsistencies in your final product. This isn't just an inconvenience. These issues directly impact your operational efficiency, damage your products, and eat into your profits, making it harder to compete in a tough market.
Coil packing solutions for Canadian manufacturing must be specifically engineered to withstand extreme cold, address labor shortages through automation, and ensure product protection during long-distance shipping. These systems integrate winterization features like low-temperature components and heated enclosures, along with robust automation to create a reliable, efficient, and cost-effective packing process suited for the Canadian industrial landscape.
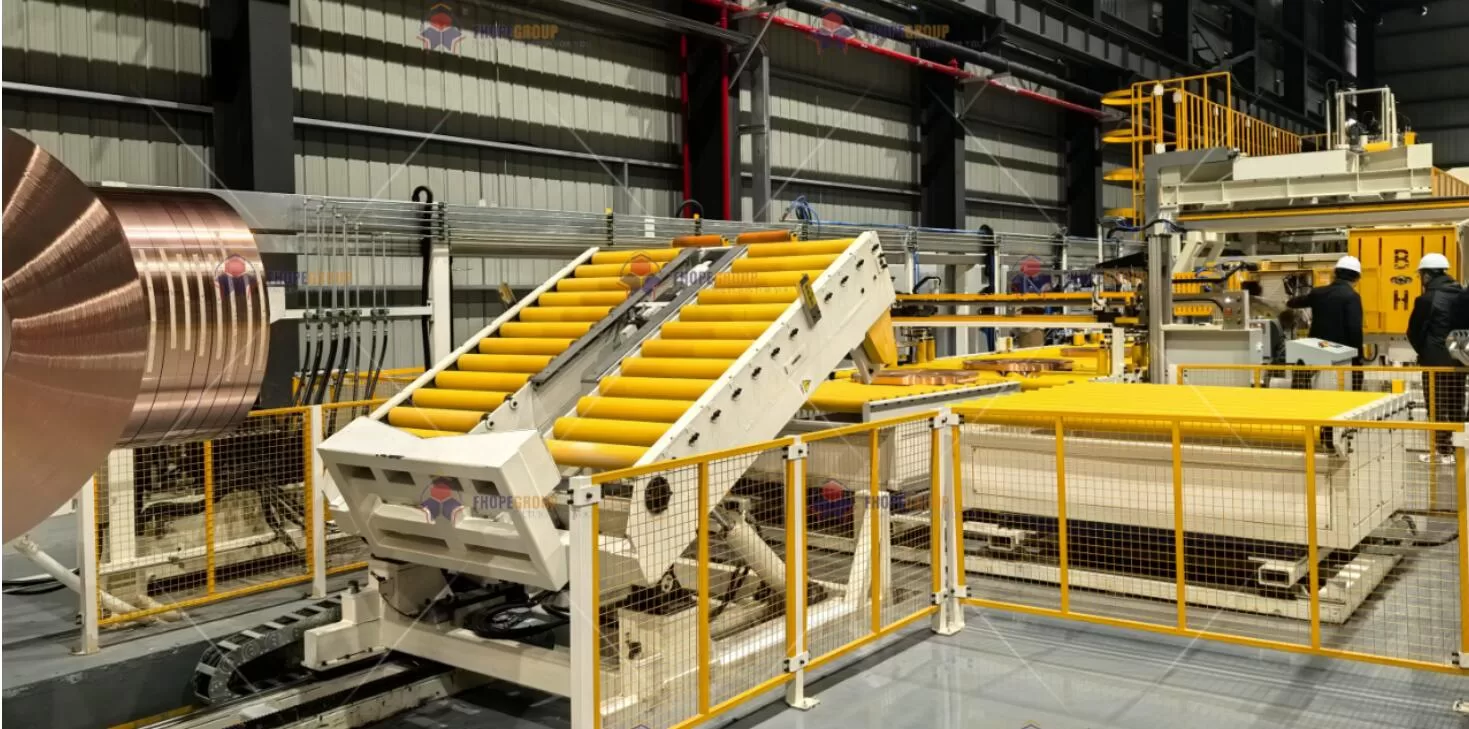
My journey in this industry, from an engineer on the factory floor to founding SHJLPACK, has taught me one crucial lesson: a machine is not just a machine. It's a core part of your entire operation. A packing line that fails in the cold or requires constant supervision isn't a solution; it's another problem. For my Canadian clients, the conversation always starts with the environment, both outside the plant and inside it. We have to think beyond the standard specifications. We need to build for resilience and for the future. Let's explore what that really means for your coil packing line.
How Can a Coil Packing Line Handle Canada's Extreme Weather?
Your production doesn't stop when the temperature drops to -30°C, but your equipment might. Standard packing lines often use components that aren't rated for such deep cold. Hydraulic fluids can thicken, plastic parts can become brittle and snap, and sensors can fail, causing a complete shutdown. This forces your team into emergency maintenance in harsh conditions, costing you valuable time and money. The winter becomes a season of risk, not just of cold.
A coil packing line built for Canadian winters is designed with low-temperature resilience from the ground up. This involves using specialized lubricants and hydraulic fluids that maintain viscosity, selecting electronic components rated for extreme cold, and using materials that do not become brittle. Key moving parts and control cabinets are often protected by insulated and heated enclosures to maintain a stable operating temperature, ensuring consistent performance no matter the weather outside.

When I first worked with a steel service center in Alberta, their biggest complaint was film breakage. The standard stretch film they used would become stiff and snap as it was applied to the cold steel coils. The machine itself was fine, but the process was failing. It’s a detail many machine builders overlook. They test their equipment in a comfortable factory in a moderate climate. They don't simulate a Canadian winter. We learned that the machine design had to account for the properties of the packing materials in the cold. It’s not just about making the machine survive; it’s about making the entire packing process work flawlessly.
Deconstructing Winter-Proof Design
A truly "winter-proof" machine is more than just a few heavy-duty parts. It is a system where every component is chosen and integrated with the cold in mind. The design philosophy shifts from "will it run?" to "will it run reliably at -30°C?".
First, let's look at the mechanical and fluid systems. Standard hydraulic oil becomes thick like molasses in extreme cold. This sluggishness can burn out motors and cause slow, jerky movements, leading to poor wrapping or strapping. We must use synthetic, wide-temperature-range hydraulic fluids. Similarly, pneumatic systems are a major point of failure. Moisture in the compressed air lines can freeze, blocking valves and actuators. An effective solution involves installing high-efficiency air dryers with heating elements directly on the supply lines feeding the packing machine.
Electronics and Control Systems in the Cold
The brain of the machine, the PLC and its sensors, are also vulnerable. Condensation is a huge enemy. When a cold machine is in a warmer, humid plant, moisture can form inside control cabinets and short-circuit sensitive electronics. A proper design includes NEMA-rated enclosures that are sealed, insulated, and often equipped with a small, thermostat-controlled heater and a fan. This keeps the internal temperature above the dew point and circulates air to prevent "hot spots," ensuring the PLC, VFDs, and power supplies operate within their specified temperature range. Proximity sensors, photo-eyes, and encoders must also be rated for low temperatures to avoid false readings or complete failure.
Component | Standard Solution | Canadian Winter Solution | Why It Matters |
---|---|---|---|
Hydraulic Oil | Standard ISO 32/46 | Synthetic, low-temp grade | Prevents pump strain and slow operation. |
Control Cabinet | Standard ventilated | NEMA 4 sealed, insulated, heated | Protects electronics from condensation and cold. |
Pneumatics | Basic air filter | Heated air dryer system | Stops ice from blocking valves and lines. |
Wrapping Film | Standard stretch film | Cold-rated film + localized pre-heater | Prevents film from becoming brittle and snapping. |
Cables & Hoses | PVC insulation | PUR or low-temp rated insulation | Avoids cracking and electrical failures when flexed. |
This systematic approach ensures that the machine isn't just patched with solutions but is fundamentally built to perform in the challenging Canadian climate. It's an investment in uptime.
What Makes a Packing Solution Truly "Automated" for Canadian Labour Shortages?
Many factories in Canada struggle to find enough workers for physically demanding jobs like coil packing. Manual or semi-automatic processes require people to lift, push, and wrap heavy coils all day. This leads to high employee turnover, training costs, and the constant risk of workplace injuries. The problem gets worse when you can't find a replacement, and a production bottleneck forms in your packing area, slowing down your entire plant.
A truly automated coil packing solution removes these manual steps. It is a fully integrated system that takes a coil from the slitter or crane, conveys it, identifies it, applies the correct packing materials, straps it, weighs it, and labels it for shipping without requiring an operator for each step. This level of automation means one technician can supervise the entire line, reallocating your valuable workforce to more skilled tasks. It directly addresses labor shortages by reducing the number of people needed on the floor.
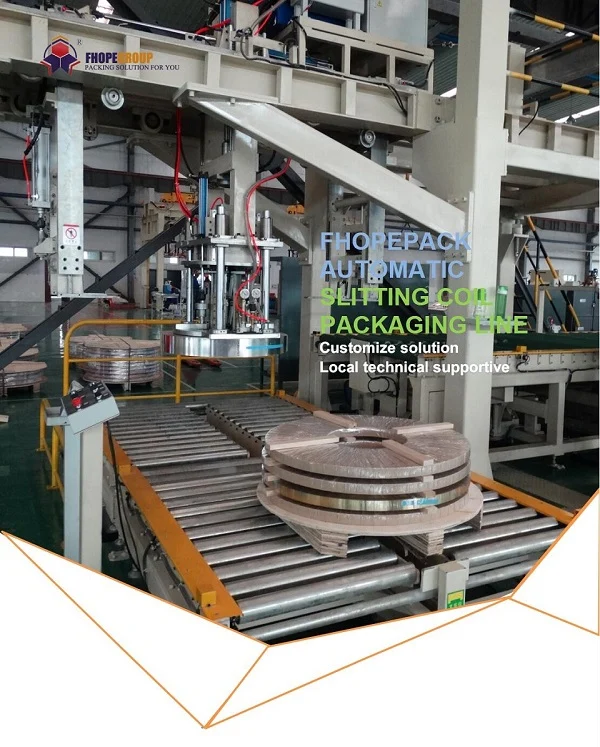
I remember visiting a client whose "automated" line still required two people. One person had to manually place corner protectors before the coil was strapped. Another had to attach the final shipping label. The machine did the wrapping, but the process was still broken. They had bought a machine, not a solution. True automation thinks about the entire workflow, from start to finish. It's about eliminating the small, repetitive tasks that drain your labor pool. For that client, we designed a retrofitted module with a robotic arm to place the corner protectors. It was an extra investment, but it freed up an entire person per shift. That's the real meaning of automation.
Beyond the Wrapping Robot
When manufacturers think of automation, they often picture just the main machine, like the orbital wrapper. But a fully automated line is a symphony of connected systems working together. It is an end-to-end process that requires minimal human intervention.
First, let's consider the entry point. A truly automated system integrates with your production exit. This could be a turnstile that receives coils from a C-hook or a powered conveyor that moves coils from the slitter recoiler. There should be no need for a forklift driver to carefully place each coil onto the packing line. The system should receive them automatically. Sensors then identify the coil's width and diameter to select the right packing program.
The Core of the Automated Process
Once the coil is on the line, the sequence is seamless.
- Strapping: An automatic strapping head applies radial straps through the eye of the coil. The machine feeds the strap, tensions it, seals it, and cuts it. Advanced systems can rotate the coil to apply multiple straps at precise intervals.
- Wrapping: The coil moves to the orbital wrapper. The machine automatically starts the wrap, applies the correct number of layers of film or paper, and seals and cuts the material. The human job is simply to change the material roll when it runs out.
- Stacking and Palletizing: This is where many systems fail. A manual process requires an operator and a crane to stack coils. A fully automated line uses a down-ender to tilt the coil, then a robotic or gantry system to pick it up and place it precisely on a pallet. This is not only faster but also much safer.
Here is a breakdown of manual versus automated tasks.
Task | Manual / Semi-Auto Method | Fully Automated Method | Benefit |
---|---|---|---|
Coil Loading | Forklift or crane operator places coil. | Integrated conveyor or turnstile. | Faster, safer, less waiting time. |
Corner Protection | Operator manually places protectors. | Robotic arm or custom applicator. | Eliminates a tedious, repetitive job. |
Strapping | Hand-held tools, operator feeds strap. | Automatic strapping head. | Consistent tension, faster cycle. |
Labeling | Operator prints and sticks label. | Automatic print-and-apply system. | Accurate data, no human error. |
Stacking | Crane and operator stack coils. | Down-ender and robotic stacker. | High speed, improved safety. |
This level of integration is what separates a collection of machines from a true automated solution. It tackles the labor shortage head-on by designing the human out of the repetitive, low-skill tasks.
How Does a Modern Packing Line Improve ROI for Canadian Steel Producers?
As a steel producer, every investment must have a clear return. You look at the cost of a new packing line and see a major capital expense. You worry about whether it will actually deliver the promised savings or just become another maintenance headache. The risk is that you spend a lot of money and only see a minor improvement, while your operational costs for energy, materials, and labor remain high.
A modern packing line delivers a strong ROI by attacking costs on multiple fronts. It reduces labor expenses through automation, cuts down on packing material waste with precise application, and lowers energy consumption with efficient motors and smart controls. It also increases throughput, allowing you to ship more product with the same facility, and improves product quality by providing consistent, protective packaging that reduces damage during transit. The return is not just in one area; it's a cumulative effect across your entire operation.

I have a client, a steel mill owner like Javier Morales, who was very skeptical. He saw our proposal and said, "Vincent, these are big numbers. My old line works." I asked him to track three things for one month: how much stretch film they wasted from over-wrapping, how much time they lost to packing-related bottlenecks, and how many customer complaints they got about rusted or damaged coils. A month later, he called me back. The numbers surprised him. The "cost" of the old line wasn't its purchase price; it was the hidden daily expenses. We calculated that a new line would pay for itself in under 24 months just from material savings and increased throughput. A modern machine isn't a cost center; it's a profit driver.
Breaking Down the Return on Investment
A solid ROI calculation for a packing line goes far beyond the initial purchase price. It requires a detailed look at both direct and indirect savings. As a business owner, you need to see the numbers clearly.
First, there are the tangible, easy-to-measure savings.
- Labor Reduction: This is the most obvious one. If a new automated line allows you to reassign two operators per shift, you can calculate the annual savings based on their wages, benefits, and overhead. In a three-shift operation, this saving is multiplied by three.
- Material Savings: Modern orbital wrappers have precise controls. You can program the exact film overlap and tension needed for each coil size. Older machines or manual wrapping often lead to over-wrapping "just to be safe." A 10-15% reduction in film or paper consumption is a very realistic goal. Over a year, this adds up to a significant amount of money.
- Reduced Product Damage: How much does a damaged coil cost you? You have the cost of the product itself, the shipping costs, and the administrative cost of handling the customer claim. And you have the damage to your reputation. A modern line provides consistent, full-coverage wrapping that protects against moisture and impact, drastically reducing these incidents.
The Hidden Financial Gains
Next are the less obvious but equally important financial benefits.
- Increased Throughput: An old, semi-automatic line might pack 10 coils per hour. A new, fully automated line could pack 20 or even 30. This means the packing station is no longer the bottleneck. You can run your slitter or mill at its full capacity, leading to higher overall production and sales.
- Lower Energy Costs: Modern machines use high-efficiency motors (IE3 or IE4 standards) and variable frequency drives (VFDs). A VFD ensures the motor only draws the power it needs for the task, instead of running at full speed all the time. This can cut the machine's energy consumption by 20-40%.
- Predictive Maintenance: An integrated line with IoT sensors can monitor its own health. It can alert you that a motor's temperature is rising or a bearing's vibration is increasing. This allows you to schedule maintenance before a catastrophic failure occurs, preventing costly unplanned downtime.
ROI Factor | Old Line (Annual Cost) | Modern Line (Annual Savings) | Impact |
---|---|---|---|
Labor | 2 operators/shift = $300,000+ | 1 supervisor/shift = $200,000+ | Direct cost reduction |
Materials | $100,000 (with 20% waste) | $80,000 (with <5% waste) | Reduces consumable spending |
Downtime | 80 hours (unplanned) | 10 hours (planned) | Increases production capacity |
Damaged Goods | 1% of shipments = $50,000 | 0.1% of shipments = $5,000 | Protects revenue and reputation |
When you add up all these factors, the investment in a modern line is not just a defensive move to replace old equipment. It is an offensive strategy to lower your cost per ton and increase your profitability.
Why Should Canadian Manufacturers Partner with a Specialized Packing Machine Supplier?
You can buy a packing machine from a general catalog, or you can find a large company that sells all types of industrial equipment. The machine might look good on paper and the price might seem attractive. But when you have a specific problem—like your strapping head freezing up or your software not communicating with your MES system—who do you call? You might get a generic support line and wait days for a technician who has never even seen a steel coil before. This is a common story.
Partnering with a specialized supplier means you are working with experts who live and breathe your industry. A specialist understands that a steel coil is not the same as a pallet of boxes. They know about the challenges of oil, sharp edges, and heavy weights. They have already solved the problems you are facing for other clients. They can advise you not just on the machine, but on the best packing materials, the most efficient line layout, and how to integrate the system with your existing operations. They are not a vendor; they are a resource.

My entire career is built on this principle. When I started SHJLPACK, I didn't want to build every machine imaginable. I wanted to be the best at one thing: coil packing and handling. Because I started as an engineer on the floor, I saw the frustration when a supplier couldn't answer a technical question. They sold the machine, and then they were gone. I decided my company would be different. We are not just selling equipment. We are sharing knowledge. When a client in Canada calls us, we are already thinking about snow load on the conveyors and the grade of steel they are strapping. That's a conversation you can only have with a specialist.
The Value of Deep Expertise
A general supplier sells a product. A specialized partner provides a total solution. This difference is crucial, especially for a significant investment like a packing line. The value of this partnership shows up in three key stages: design, implementation, and long-term support.
During the design phase, a specialist asks better questions. They won't just ask for the coil's max weight. They will ask:
- What is the gauge of the steel? Are the edges sharp? This affects the choice of conveyor belts and protective materials.
- Is the coil oily? This determines the type of wrapping film needed and if a VCI paper layer is required for rust prevention.
- How will the coil be transported? By truck, rail, or sea? This defines the level of packaging needed for protection.
- What is your factory layout? They will analyze your floor space and product flow to design a line that is efficient and safe, not just one that fits.
Implementation and Beyond
During implementation, a specialist's team knows what to expect. They aren't learning on your factory floor. They can anticipate challenges with integrating the line with your crane or slitter. Their technicians can train your operators not just on which buttons to push, but on why they are pushing them. They can explain the purpose of each sensor and the importance of proper material loading.
Long-term support is where the partnership truly proves its worth. When you have a problem two years later, you can call someone who knows your machine's specific configuration. They have the drawings, the software parameters, and a history of your operation.
Aspect | General Supplier | Specialized Partner (like SHJLPACK) | The Canadian Advantage |
---|---|---|---|
Consulting | Sells a standard model. | Analyzes your unique process. | Designs for your specific climate and logistics. |
Customization | Limited options. | Can engineer custom solutions. | Can build a winter-proof, automated line. |
Training | Basic operator functions. | In-depth training on mechanics & software. | Empowers your team to handle minor issues. |
After-Sales | Generic helpdesk. | Direct access to expert engineers. | Faster problem-solving, less downtime. |
Knowledge | Product-focused. | Industry-focused. | Understands the steel and metals market. |
Choosing a partner is like hiring a key employee. You want someone with the right experience, who understands your goals, and who will be there to help you succeed in the long run. For Canadian manufacturers, this means finding a partner who understands the North.
Conclusion
Investing in the right coil packing line is investing in your plant's resilience, efficiency, and future profitability. It's more than steel and motors; it's a strategic operational advantage.