Facing an aging workforce, rising labor costs, and the constant challenge of finding skilled talent, many Canadian steel plants are at a crossroads. The traditional ways of operating are becoming riskier and less sustainable. You might worry about a key production line stopping because a veteran operator retired, or the financial and human cost of a workplace accident. These aren't just abstract fears; they are real threats to your plant's bottom line and future stability. The good news is that there is a proven path forward. Automation, especially in areas like coil packing and handling, provides a powerful solution to reduce these labor risks, creating a safer, more efficient, and more resilient operation.
Automation helps Canadian steel plants reduce labor risks by taking over dangerous, repetitive, and physically demanding tasks. This directly minimizes workplace accidents and injuries. It also ensures consistent, high-quality output, regardless of individual worker skill levels, which makes plants less dependent on a shrinking pool of experienced labor. By doing this, automation boosts safety, lowers operational costs associated with errors and training, and increases overall productivity.
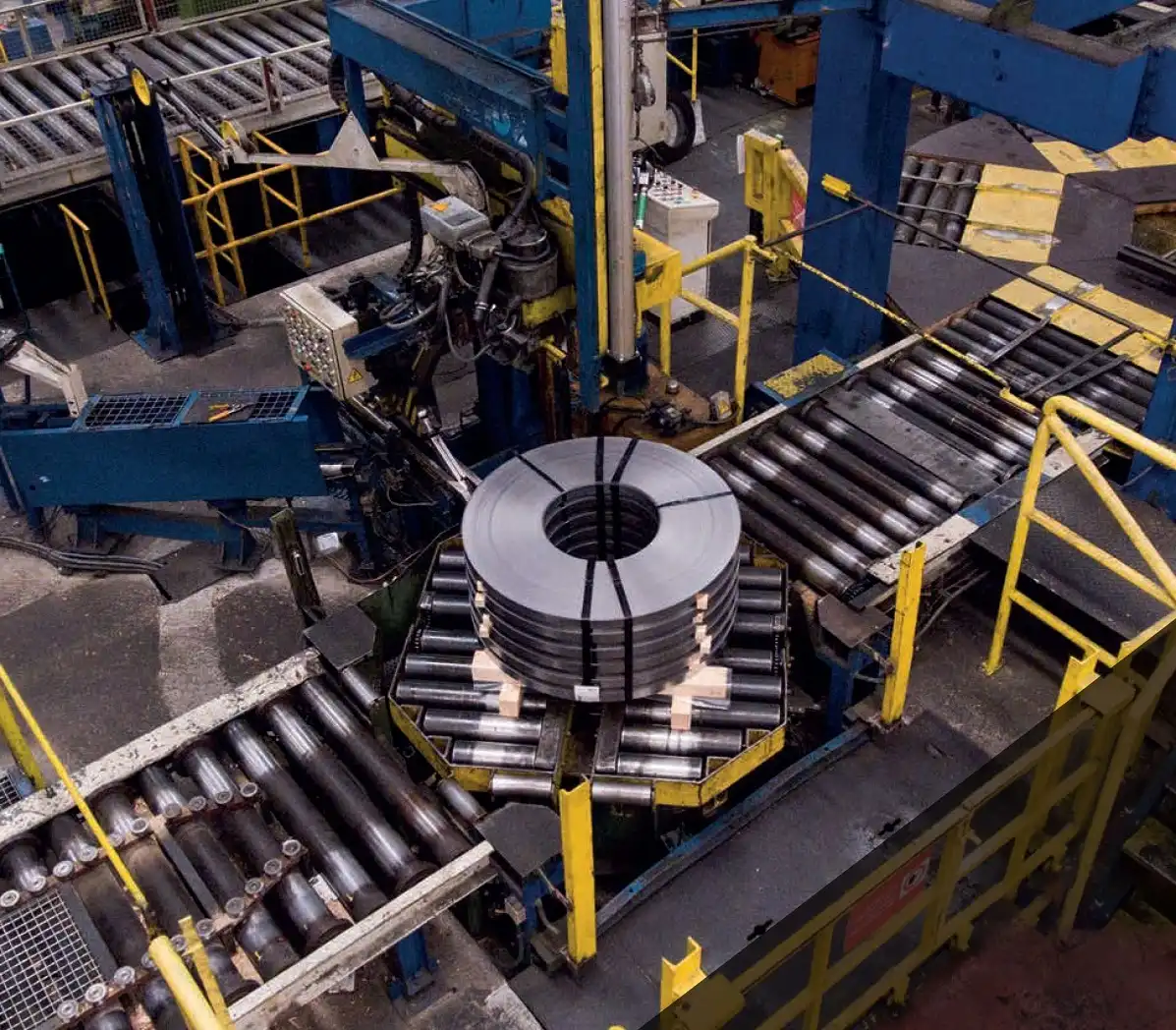
It’s one thing to talk about the benefits of automation in general terms. It's another to see how it works on the ground, solving real problems that plant managers and owners like you face every day. I’ve spent my entire career in this industry, first as an engineer on the floor and now as a designer of these systems. I've seen firsthand how targeted automation can transform a plant. Let's break down the specific challenges and explore how automated solutions can directly address them.
Can Automation Solve the Skilled Labor Shortage in the Steel Industry?
Finding and keeping good people is one of the biggest challenges in the Canadian steel industry today. You know the story well. Experienced operators are nearing retirement, and it’s incredibly difficult to attract younger generations to these demanding roles. This creates a dangerous knowledge gap and a constant bottleneck. Your plant's output can be limited not by your machines, but by the lack of qualified hands to run them. This reliance on a few key individuals is a huge risk. Automation offers a direct and effective way to solve this problem. It's not about replacing your entire workforce; it's about making your team stronger and your operations more reliable.
Yes, automation directly addresses the skilled labor shortage by systematically taking over the most repetitive and physically demanding tasks. This allows a smaller, more flexible team to oversee a much larger part of the production process. Instead of needing several operators to manually handle, strap, and wrap coils, you can have one skilled technician monitoring an entire automated line. This makes your plant far less vulnerable to retirements, sick days, or challenges in the local hiring market.

The "Knowledge Drain" from a Retiring Workforce
For decades, the value of a steel plant was not just in its machinery, but in the people who ran it. A veteran operator who has worked on a slitting or packing line for 20 years has a level of knowledge that is almost impossible to write down in a manual. They can hear a slight change in the machine's sound and know a bearing is about to fail. They know exactly how much tension to apply to a strap based on the coil's specific grade and width. When these experts retire, that knowledge walks out the door with them. This "knowledge drain" is a critical risk for many Canadian plants. Automation is the most effective way to capture and standardize this expertise. An automated coil packing system is programmed with the optimal parameters for every single product. It applies the exact same wrapping sequence and strapping tension every time. The expertise of your best operator is essentially coded into the machine's logic, ensuring that best practice is followed 24/7, long after that operator has retired.
Shifting the Skillset to Attract New Talent
The nature of work in a steel plant is changing. The old perception of it being just hard, dirty, manual labor is what makes it difficult to attract new talent. Automation helps change that perception. It transforms the job from one of manual labor to one of technical oversight. Instead of manually lifting heavy materials, workers are now managing advanced robotic systems. They are monitoring control panels, analyzing production data, and performing preventative maintenance on sophisticated equipment. This new type of role is far more appealing to a younger, tech-savvy generation. It creates a career path that involves skills in robotics, data analysis, and system management, which are seen as valuable and future-proof. By investing in automation, you are also investing in your ability to build a workforce for the next 30 years.
Feature | Manual Operation | Automated Operation |
---|---|---|
Required Skills | Physical strength, manual dexterity, years of experience | Technical aptitude, problem-solving, system monitoring |
Training Time | Months or years to become an expert | Weeks for system oversight and basic maintenance |
Knowledge Transfer | Difficult, relies on apprenticeship | Standardized in system software and procedures |
Attraction for Youth | Low, perceived as old-fashioned labor | High, seen as a modern, technology-focused career |
How Does Automation Drastically Improve Worker Safety in Steel Mills?
Let's be honest, a steel plant can be a dangerous place to work. The sheer weight of the coils, the sharp edges of slit steel, the high-powered strapping tools—all of these present daily risks to your employees. As a plant owner, I know that your top priority is sending everyone home safe at the end of their shift. But accidents happen, and when they do, the cost is immense. It affects the injured worker, their family, team morale, and your company's finances through downtime and insurance claims. You've likely spent a fortune on personal protective equipment and training, but some risks are just inherent to the manual process. Automation is the single most impactful step you can take to remove your people from harm's way.
Automation improves worker safety by creating a physical barrier between employees and the most hazardous tasks. Robots and dedicated machinery can handle the entire process of moving, strapping, and wrapping heavy steel coils without any direct human intervention. This eliminates the risks of crushing injuries, deep cuts from steel strapping, and long-term strain from repetitive lifting. It effectively engineers the danger out of the process, which is far more effective than relying on protective gear alone.
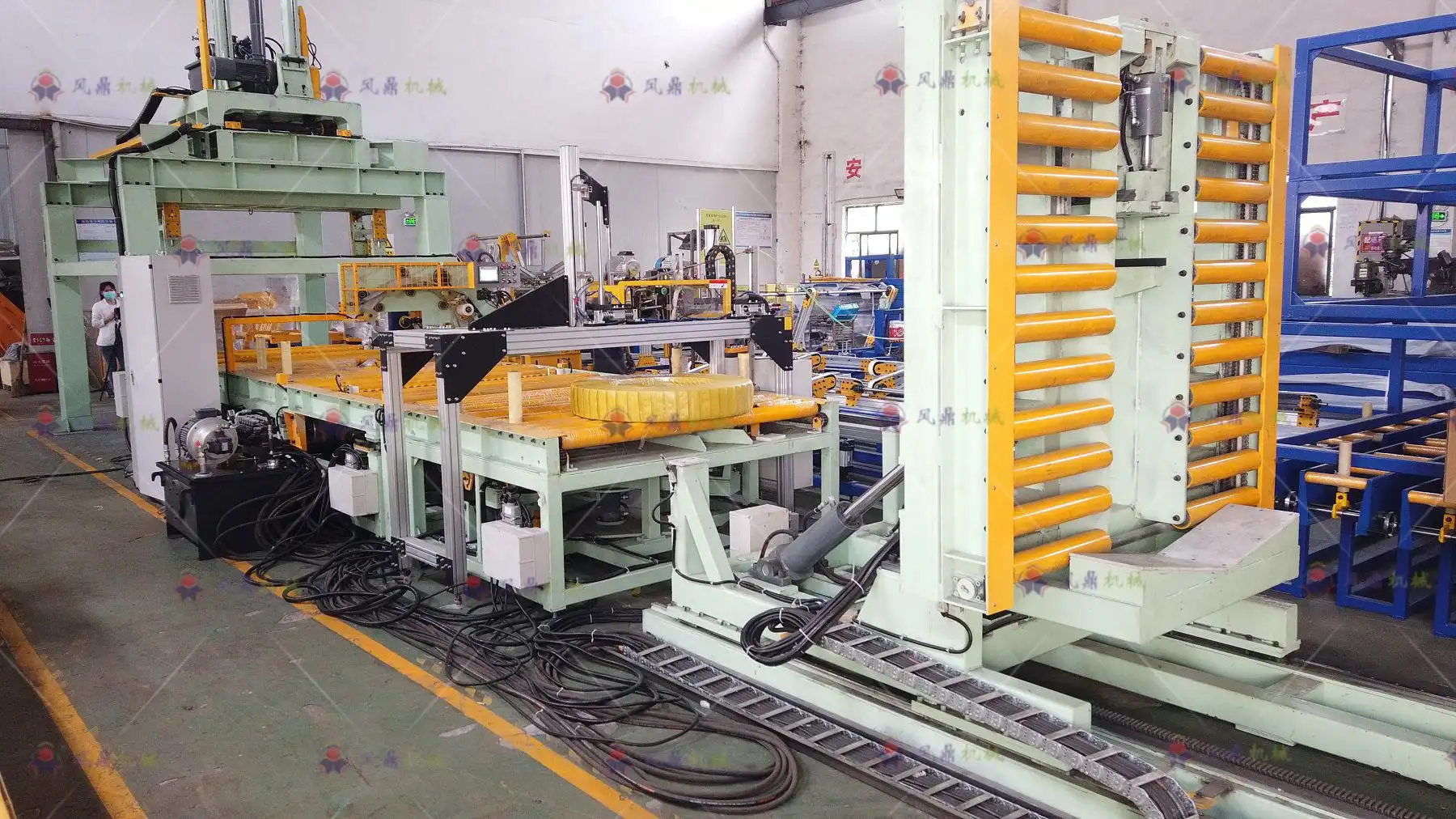
Eliminating High-Risk Manual Handling
In a traditional packing area, workers are constantly exposed to danger. I remember watching teams manually guide a C-hook to lift a 15-ton coil. One moment of inattention could be catastrophic. Then comes the strapping process. Manually feeding steel straps around a coil, tensioning it with a pneumatic tool, and cutting it creates multiple opportunities for injury. The strap can snap back, the tool can slip, or the sharp edges of the strap can cause serious cuts. After that, workers might have to manually wrap the coil with paper or film, which involves repetitive bending and reaching. An automated coil packing line takes the human element out of every one of these steps. The coil is received from the turnstile by an automated car. It is then lifted, centered, and strapped by a robotic system. The wrapping is done by a machine that orbits the coil. The worker's role changes to one of supervision from a safe distance, often from inside a control room.
Designing Safety into the System
Modern automated systems are built with safety as their core principle, not as an afterthought. These systems are surrounded by safety fencing and light curtains. If a person breaks the light beam, the entire line comes to an immediate and safe stop. Emergency stop buttons are placed at multiple strategic locations. The machines themselves have sensors that detect jams or misalignments, preventing dangerous situations before they can develop. In my work designing these systems, we run countless failure mode analyses. What happens if power is lost? What happens if a strap coil runs out mid-cycle? The system is programmed to fail safely in every conceivable scenario. This proactive approach to safety is something that you can never fully achieve with manual processes, which always have the unpredictable element of human behavior.
Hazard Type | Manual Process Risk | Automated System Mitigation |
---|---|---|
Crushing/Impact | High risk from moving coils, C-hooks, forklifts. | Eliminated. Workers are outside the fenced operational area. |
Lacerations | High risk from handling sharp steel strapping and coil edges. | Eliminated. Robots handle all material contact. |
Ergonomic Strain | High risk of back/shoulder injury from repetitive lifting and tool use. | Eliminated. Machines perform all physical labor. |
Trips and Falls | Moderate risk from strapping debris and tools on the floor. | Reduced. The operational area is kept clear and automated. |
What is the Real Impact of Automation on Operational Costs and Consistency?
Every steel plant manager in Canada is under pressure to control costs while maintaining quality. Your customers expect perfectly packaged coils, delivered on time, every time. But with manual operations, consistency is a constant battle. The quality of the wrapping can vary from shift to shift, or even from the beginning of a shift to the end. One operator might apply straps a little tighter than another. These small inconsistencies can lead to big problems, like damaged products and customer complaints. On top of that, direct labor costs continue to rise. You're paying not just for the work, but also for the inherent inefficiency and risk of human error. This is where automation delivers a massive financial and operational advantage.
Automation directly impacts operational costs by reducing the need for direct labor and by nearly eliminating the hidden costs of human error, such as wasted packing material or damaged goods. More importantly, it provides perfect consistency. An automated line wraps and straps every coil to the exact same specification, 24 hours a day, 7 days a week. This locks in quality, improves customer satisfaction, and makes your entire production output far more predictable and profitable.

The High Price of Inconsistent Packaging
I once visited a client who was facing a serious problem. They were getting complaints from a major automotive customer about coils arriving with damage. The edges were dented, and some coils had "telescoped" during transit. We traced the problem back to their manual packing line. On the day shift, an experienced operator was doing a great job. But on the night shift, a less experienced team was not applying enough tension to the strapping and wasn't wrapping the protective paper tightly enough. During shipping, the loose coils shifted, causing the damage. The cost was enormous. They had to credit the customer, pay for return shipping, and their reputation took a hit. This is a classic example of how inconsistency costs money. An automated system would have prevented this entirely. It uses sensors to measure the coil and applies the precise, pre-programmed wrapping and strapping parameters every single time, removing the variable of human skill and fatigue.
Calculating the True Return on Investment (ROI)
When plant owners look at the price tag of an automated packing line, they sometimes only see the upfront cost. But to understand the real value, you have to look at the total cost of your current manual process. I encourage my clients to do a simple calculation. Add up the annual wages and benefits for all the workers on your packing line. Then, add the cost of wasted materials—like excess stretch film or damaged paper. Next, add the cost of product damage and customer claims from the last year. Finally, factor in the cost of any safety incidents or workers' compensation claims. When you see that total number, the investment in an automated system suddenly looks very different. I've seen automated lines deliver a full return on investment in as little as 18 to 24 months, simply by eliminating these direct and indirect costs. From that point on, the savings go directly to your bottom line.
![]() |
Cost Factor | Manual Packing Process | Automated Packing Line |
---|---|---|---|
Direct Labor | High (Wages for 3-5 operators per shift) | Low (1 supervisor for the entire line) | |
Material Waste | High (Inconsistent wrapping, errors) | Minimal (Precise, programmed material usage) | |
Product Damage | Moderate to High (Inconsistent strapping/wrapping) | Near Zero (Consistent, secure packaging) | |
Throughput | Variable, dependent on operator speed | Consistent and predictable, runs 24/7 | |
Safety Costs | Potential for high costs from injuries | Very Low, risks are engineered out |
Conclusion
Automation reduces labor risks by making your plant safer and more consistent. It empowers your team and secures your plant's competitive edge for the future.