Steel mills across Canada, from the industrial heartland of Ontario to the resource-rich plains of Alberta, face a common and relentless pressure. You're likely dealing with aging packing lines, equipment that feels more like a liability than an asset. These older systems are often slow, prone to breakdowns, and a constant drain on resources. Every unexpected stop means lost production time and mounting frustration. You're constantly fighting fires on the factory floor, which keeps you from focusing on strategic growth. This challenge is made worse by fluctuating energy costs and stricter environmental targets that never seem to let up. But what if your packing line could be transformed? What if it stopped being a source of problems and instead became a strategic tool that actively lowers your costs, boosts your uptime, and helps you meet your most ambitious goals? This isn't just a possibility; it's what a modern packing solution delivers.
A reliable coil packing system for Canadian mills integrates robust, automated machinery with intelligent controls to ensure consistent and secure wrapping. This approach significantly reduces the need for manual labor, minimizes material waste through precision, and operates dependably in demanding industrial environments. The direct result is an improvement in your mill's bottom line and output consistency, whether you are located in Ontario, Alberta, or anywhere in between.

I've spent my entire career in the packing machine industry. I started on the factory floor and eventually built my own company, SHJLPACK. I understand the challenges you face because I've seen them firsthand. I know that a packing line is much more than just the last step in the process. It can be the bottleneck that holds you back or the engine that drives your efficiency forward. Let's break down how a modern system can address the specific questions I hear from mill owners like you. We'll look at costs, sustainability, uptime, and what it really means to find a partner, not just a supplier.
How Can Modern Coil Packing Systems Reduce Operational Costs in an Aging Mill?
You see the maintenance reports and you know the story. An aging packing line means constant repairs, sourcing hard-to-find parts, and paying for unplanned downtime. Your team spends valuable hours on manual wrapping or fixing old machinery instead of on more productive tasks. The costs just keep adding up, not just in labor and parts, but in wasted wrapping materials and lost production. It feels like a battle you can't win. The solution lies in shifting from a reactive, high-cost model to a proactive, low-cost one, which is exactly what modern automation is designed to do.
A modern coil packing system directly reduces operational costs in three key areas: it automates labor-intensive tasks, uses materials with extreme precision to eliminate waste, and is built with reliable components that drastically cut down on maintenance and downtime. This translates to immediate and measurable savings on labor, materials, and repair expenses.

Dive Deeper: A Breakdown of Cost Savings
When I first started as an engineer, I was shocked by how much hidden cost was tied to the packing station. It was often seen as a simple, final step, but the inefficiencies were huge. Let's look at how a modern system attacks these costs head-on.
1. Reducing Labor Costs and Reallocating Talent
Older packing lines often require a team of workers for manual wrapping, strapping, and moving coils. This is not only expensive but also a source of safety risks and inconsistencies in wrap quality. An automated system changes this completely. A single operator can often oversee an entire packing line that previously needed three or four people. This doesn't necessarily mean reducing headcount. It means you can reallocate your skilled team members to higher-value roles, like quality control, machine supervision, or preventative maintenance. I remember working with a client in Hamilton, Ontario, who was able to move two of their best operators from the packing line to lead a new predictive maintenance team. Their expertise was far more valuable there than in manually wrapping coils. The investment in automation paid for itself not just in direct labor savings, but in improved overall plant reliability.
2. Slashing Material Waste with Precision
Material cost is another major drain. Manual wrapping is inconsistent by nature. One operator might use more stretch film than another. Paper wrapping can be applied unevenly, leading to waste or, worse, unprotected coils. A modern packing machine eliminates this guesswork.
- Stretch Film: It uses a powered pre-stretch unit that can stretch film by up to 300%. This means 1 meter of film becomes 4 meters, providing strong containment with significantly less material.
- Paper/VCI: The machine applies wrapping paper or VCI paper with precise overlap, ensuring full protection without the massive waste you see in manual application.
Here’s a simple comparison:
Metric | Old Manual Method | Modern Automated System |
---|---|---|
Labor Requirement | 2-3 Operators | 1 Supervisor |
Stretch Film Usage/Coil | ~1.5 kg (variable) | ~0.5 kg (consistent) |
Wrapping Time/Coil | 5-10 minutes | 1-2 minutes |
Consistency | Low | High |
Result | High labor & material costs | Drastically lower costs |
3. Minimizing Maintenance and Downtime
Finally, the cost of downtime on an old machine is enormous. It doesn't just stop the packing line; it can back up your entire production process. Modern systems are built for reliability using high-quality, standardized components. This means fewer breakdowns and easier, faster repairs when maintenance is needed. The design philosophy is completely different. Instead of reacting to failures, you move to a schedule of simple, preventative maintenance, keeping the line running smoothly.
How Does an Upgraded Packing Line Align with Sustainability and Energy Efficiency Goals?
You're facing pressure from all sides. The government is implementing stricter environmental regulations across Canada. Your customers are asking about your company's green initiatives. And on top of it all, volatile energy prices are directly hitting your bottom line. It can feel like sustainability and profitability are competing goals. You might wonder how investing in a packing line—a piece of heavy machinery—could possibly help. The truth is, modern packing equipment is specifically engineered to address these challenges, turning a potential compliance headache into a competitive advantage.
An upgraded packing line directly supports sustainability and energy goals by incorporating high-efficiency motors and smart controls that minimize electricity consumption. It also drastically reduces material waste, which lowers the carbon footprint associated with producing and transporting those packaging materials. This allows a mill to improve its environmental performance while simultaneously cutting operational costs.
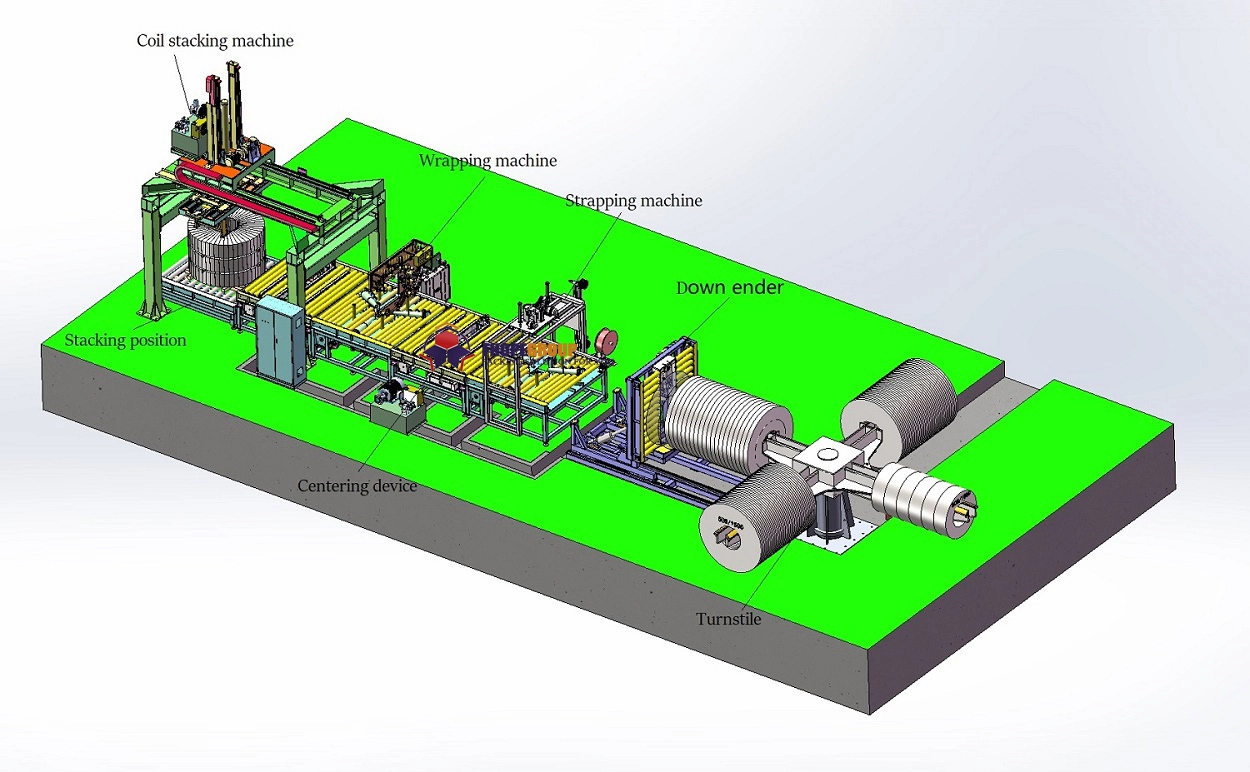
Dive Deeper: The Green Machine
When I established my own factory, I made a commitment to not just build machines, but to build responsible solutions. For a modern steel mill, being "green" isn't about PR; it's about smart, efficient business. An investment in an upgraded packing line is a tangible step towards that goal. Here’s how.
1. Engineering for Energy Efficiency
Old machines are often energy vampires. They use oversized motors that run at full power all the time, even when the machine is idle between coils. It's like leaving a car engine running at full throttle at a red light. Modern packing systems are much smarter.
- Variable Frequency Drives (VFDs): This is a critical technology. VFDs allow motors to adjust their speed and power consumption based on the real-time need. The motor for the wrapping ring speeds up for the wrap, slows down, and then stops, using a fraction of the energy of an old, constantly running motor.
- Energy-Efficient Motors: Today's motors are simply built to a higher standard (like IE3 or IE4 classifications), converting more electricity into useful work and less into wasted heat.
- Smart "Sleep" Modes: When the line is idle for a set period, non-essential components can automatically power down, waking up instantly when the next coil arrives.
I visited a client's facility in Alberta that had recently upgraded. Their energy bill for the packing area dropped by over 40%. The savings were so significant that the energy efficiency alone provided a return on their investment far faster than they had projected.
2. Reducing the Footprint Through Material Savings
Sustainability isn't just about energy; it's also about resources. Every kilogram of steel, plastic, or paper you save is a direct reduction in your environmental footprint. As we discussed, automation brings precision. This precision has a powerful green side effect.
Sustainability Factor | Old Packing Method | Modern Packing System |
---|---|---|
Material Consumption | High and inconsistent | Low and precise |
Waste Generation | Significant scrap from off-cuts and over-wrapping | Minimal to zero waste |
Associated Carbon Footprint | Higher due to more material production & transport | Lower due to resource optimization |
Use of Recyclables | Often uses older, less eco-friendly materials | Designed to work with modern, thinner, recyclable films |
By using less material to achieve a better, more secure wrap, you are reducing the energy needed to produce that plastic film or paper in the first place. You are also reducing the weight of trucks needed to bring those supplies to your plant and the amount of waste that ends up in a landfill. It's a chain reaction of positive environmental impact that starts right at your packing line.
Can a New Packing System Truly Boost Overall Plant Uptime to 95%?
You have a goal: 95% uptime. It's an ambitious but achievable target for a modern steel mill. But you might be looking at your big-ticket items—your furnace, your caster, your rolling mill—as the keys to achieving it. It's easy to overlook the end of the line. The problem is, your entire production chain is only as strong as its weakest link. If your multi-million dollar slitting line is producing coils faster than your old packing line can handle them, you don't have an efficient plant. You have a very expensive traffic jam.
Yes, a new packing system is a critical component in achieving 95% overall plant uptime. It does this by removing a common bottleneck, operating with high reliability to prevent unplanned stops, and integrating with plant-wide digital systems to enable predictive maintenance and smooth production flow. When your packing line can consistently keep pace with production, it unlocks the true capacity of your entire facility.

Dive Deeper: From Bottleneck to Pacesetter
In my journey from employee to factory owner, the concept of the "bottleneck" was one of the most important lessons I learned. Optimizing one part of a process is useless if another part is holding everything back. For many mills, especially in Ontario and Alberta with their mix of legacy and modern equipment, the packing station is that hidden bottleneck.
1. Matching the Speed of Production
The core function of a packing line in boosting uptime is simple: it needs to be fast and reliable enough to clear coils from the production line without delay. Imagine your slitting line finishes a set of coils. They are moved to the packing entry conveyor. If the packing machine is slow, or broken down, that conveyor fills up. Soon, there's no place to put the next set of coils. Your slitting line must stop. Your entire production schedule is thrown off, and your overall equipment effectiveness (OEE) plummets. A modern, automated line is designed with this in mind. It's sized and configured to match or exceed the cycle time of your production equipment, ensuring a smooth, continuous flow of material. It effectively becomes the pacesetter for outbound logistics.
2. The Power of Data: Enabling Predictive Maintenance
Achieving 95% uptime isn't about being lucky and avoiding breakdowns. It's about preventing them before they happen. This is where digitalization comes in. Modern packing systems are equipped with IoT (Internet of Things) sensors that monitor the health of critical components in real-time.
- Vibration sensors on motors and bearings can detect tiny changes that signal a future failure.
- Temperature sensors can alert you to overheating components.
- Cycle counters track the exact usage of parts like grippers or cutters.
This data is fed to your control system. Instead of a maintenance team reacting to a sudden, catastrophic failure, they get an alert: "The main ring bearing has shown increased vibration for 24 hours. Recommend replacement during the next scheduled maintenance window." This transforms your maintenance from a reactive fire-fight to a proactive, planned activity, which is the secret to sustained high uptime.
Data Point | Old System | Modern System with IoT |
---|---|---|
Failure Detection | A loud noise, then a breakdown | A dashboard alert, days in advance |
Maintenance Type | Reactive (Emergency Repair) | Predictive (Planned Replacement) |
Impact on Uptime | Hours or days of lost production | Zero unplanned downtime |
Integration | Standalone "dumb" machine | Communicates with plant MES/ERP |
This data integration is the final piece. The packing line tells the main plant system (MES) exactly what it's doing—which coil it's wrapping, when it finished, its current status. This gives you true, real-time visibility of your entire process, from molten steel to finished, packed coil.
What Defines a True Strategic Partner for Coil Handling and Packing Solutions?
You've been through it before. You buy a piece of equipment, the sales team is great, and the machine is installed. Then, when a real problem comes up six months later, the supplier is slow to respond or can't provide the expert help you need. You're left on your own to figure it out. This experience makes you cautious. You understand that a complex piece of equipment like a packing line is not just a one-time purchase. You're looking for more than a vendor who sells you a machine. You need a strategic partner who is invested in your success for the long haul.
A true strategic partner provides value far beyond the initial sale. They act as an expert consultant during the planning phase, offer hands-on support through installation and training, and remain committed to your success with proactive service, optimization advice, and long-term support. Their goal isn't to close a deal; it's to build a relationship that helps your business grow.

Dive Deeper: The Partnership Test
When I started SHJLPACK, I built it on a single principle that I learned from my own journey: my success is tied directly to my clients' success. I achieved my own goals by helping other businesses grow. This philosophy defines how we operate and it's the core of what a true partnership looks like. It’s about being there for the entire lifecycle of the equipment.
1. The Consultation Phase: Before the Sale
A vendor tries to sell you a standard machine from their catalog. A partner starts by listening. They invest time to understand your specific needs.
- What are the exact dimensions and weights of your coils?
- What is the layout of your plant? Where are the space constraints?
- What are your production goals and bottleneck points?
- What are your long-term plans for digitalization and sustainability?
I insist on this deep dive because a "one-size-fits-all" solution rarely fits anyone perfectly. A true partner will analyze your unique situation and then design a solution tailored to you. This might mean a custom conveyor layout, a specific type of wrapping material a machine is optimized for, or a software interface that connects perfectly with your existing ERP system. The goal is to propose the right solution, not just a solution.
2. The Implementation Phase: During Installation and Commissioning
A vendor might ship the machine and a manual. A partner is on-site. They work alongside your team during installation, ensuring everything is mechanically and electrically correct. But the most critical part is training. A partner ensures your operators and maintenance staff are not just shown which buttons to press; they understand how the machine works, how to perform routine maintenance, and how to troubleshoot common issues. This transfer of knowledge is essential. It empowers your team to own the equipment, which is critical for long-term reliability.
3. The Long-Term Phase: After the Sale
This is where the difference becomes clearest. A vendor's job is done. A partner's job is just beginning.
Aspect of Service | Vendor Mentality | Partner Mentality |
---|---|---|
After-Sales Support | A reactive helpdesk, may be slow to respond. | Proactive check-ins and a dedicated support line. |
Spare Parts | Standard list, may have long lead times. | Manages critical spare parts list, offers stocking programs. |
Optimization | "The machine works as sold." | "How can we help you get more out of it?" |
Future Growth | "You'll need to buy a new machine." | "Let's discuss how we can upgrade your current line to meet new needs." |
A strategic partner stays in touch. They might call to discuss a new film that could save you money, or a software update that could improve efficiency. They see your growth as their growth. This is the ultimate test: a partner is someone you can call five years from now to discuss the future, and they'll be just as engaged as they were on day one.
Conclusion
Investing in the right coil packing system with a true partner is not an expense. It's a strategic move toward greater efficiency, reliability, and profitability for your Canadian mill.