As a U.S. steel manufacturer, you face constant pressure. Global competition is fierce. Energy costs are unpredictable. And the demand for higher quality and faster delivery never stops. You know that every part of your operation must be efficient, reliable, and cost-effective. Your packing line is no exception. Often seen as the last step, it can become a major bottleneck, a drain on resources, and a source of frustrating downtime. This directly impacts your bottom line and your ability to serve your customers. But what if your packing line could be transformed from a liability into a strategic asset? A modern solution can do more than just wrap coils; it can actively lower your energy bills, reduce labor costs, and provide the data you need to run a smarter, more profitable mill.
The best coil packing line solutions for U.S. steel manufacturers are fully automated systems designed to tackle modern challenges head-on. These lines integrate high-efficiency motors, IoT sensors for predictive maintenance, and seamless data communication with your plant's MES or ERP systems. The goal is to minimize manual intervention, drastically cut energy consumption per ton, and provide the operational visibility needed to boost overall equipment effectiveness (OEE) and protect your profit margins.

I've spent my entire career in the packing machinery industry. I started on the factory floor as an engineer, learning every nut and bolt. Later, I founded my own factory, SHJLPACK. I understand the view from the control room and the boardroom. I know the numbers have to work. An investment in new equipment isn't just about getting a new machine; it's about solving real-world problems and achieving tangible goals. For leaders like you in the U.S. steel market, the right packing line is a critical piece of the puzzle for improving productivity and securing your competitive edge. Let's explore what that solution looks like.
How Can a Modern Coil Packing Line Address Rising Energy Costs?
You see it on every utility bill. The fluctuating cost of electricity and fuel eats directly into your profits. In a steel mill, where energy consumption is massive, every kilowatt-hour saved matters. Your old packing line, with its oversized motors running constantly, is likely a silent energy thief. You might think it's just a small part of your overall energy use, but these costs add up, coil after coil, day after day. It's a persistent, hidden drain on your resources. This makes it harder to compete on price and invest in other critical areas of your business.
A modern coil packing line addresses rising energy costs through a combination of energy-efficient components and intelligent design. It uses high-efficiency IE3 or IE4 motors, variable frequency drives (VFDs) that match power use to the immediate task, and smart "sleep" modes that power down sections of the line when idle. This holistic approach can reduce the packing line's energy consumption by 30-50% compared to older systems.
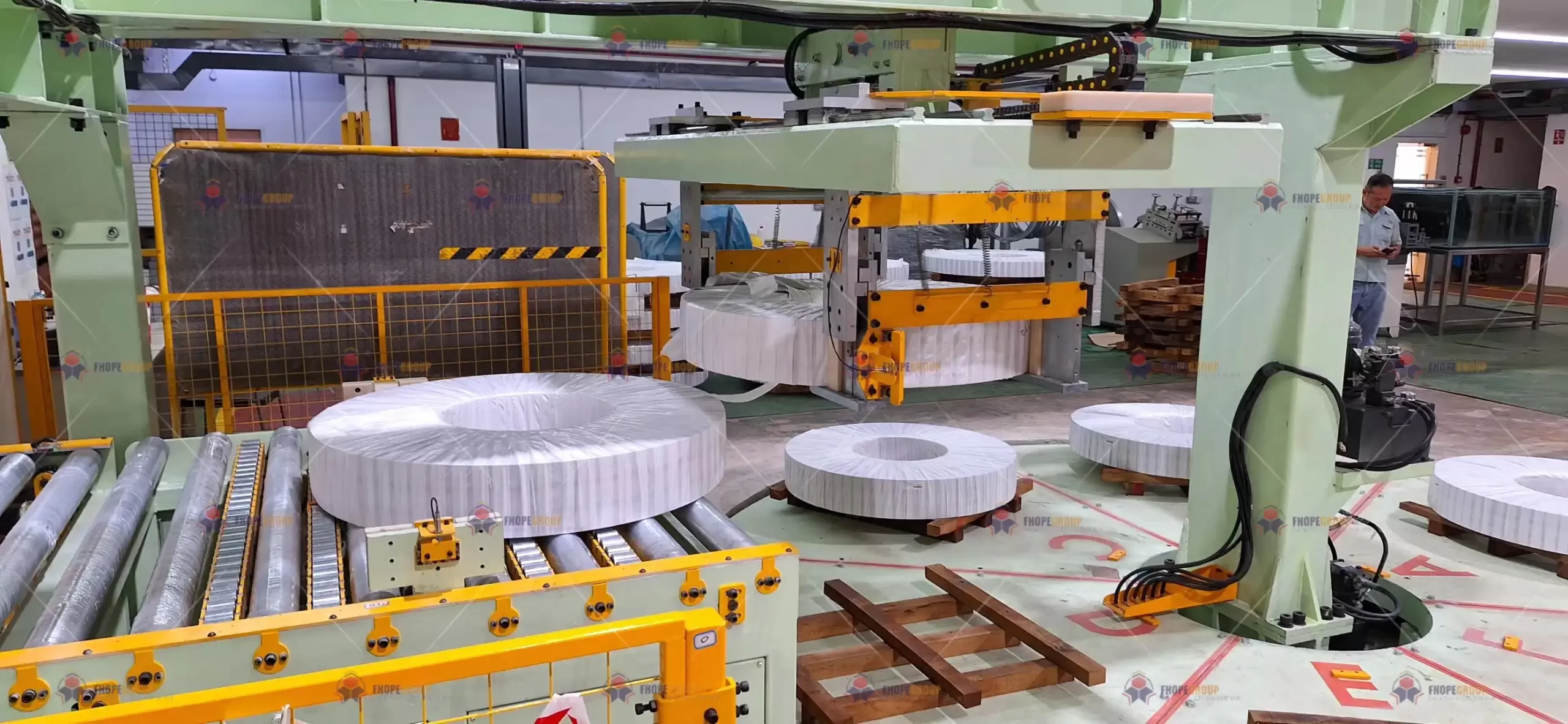
When I was a young engineer, the focus was all on speed and durability. Energy efficiency was an afterthought. Today, it's a core design principle at SHJLPACK. We don't just build machines; we engineer cost-saving solutions. To truly understand how a new line saves you money, we need to look deeper than just the motor specifications. It's about a smarter way of thinking about energy usage throughout the entire packing cycle.
Breaking Down the Energy Savings
The biggest mistake I see is focusing only on one component. A truly energy-efficient system is a sum of many smart parts working together. It’s not about one magic bullet; it’s about a comprehensive engineering philosophy. Let's break down where the savings come from.
High-Efficiency Components
This is the most obvious starting point. Older equipment often uses standard efficiency motors that run at full power regardless of the load. Modern lines are built differently.
- Motors: We use IE3 (Premium Efficiency) or IE4 (Super Premium Efficiency) motors as a standard. These motors convert more electricity into useful work and less into wasted heat.
- Variable Frequency Drives (VFDs): A VFD is crucial. It acts like a dimmer switch for the motor. Instead of running at 100% speed to convey a light coil, the VFD adjusts the motor's speed and torque to the exact level needed. This alone can lead to significant savings, especially in operations with varying coil sizes and weights.
Component | Older System (Typical) | Modern SHJLPACK System | Energy Impact |
---|---|---|---|
Main Motors | Standard Efficiency (IE1) | High-Efficiency (IE3/IE4) | 5-10% less energy loss per motor |
Power Control | Direct On-Line (Full Power) | Variable Frequency Drives (VFDs) | 20-40% savings by matching power to load |
Conveyors | Run continuously | Run-on-demand with sensors | Eliminates idle energy consumption |
Intelligent Operational Design
Beyond the hardware, the logic of the machine plays a huge role. An old line is "dumb"—it runs continuously whether a coil is present or not. A modern line is "smart."
- Run-on-Demand: We place sensors along the line. A conveyor section only activates when a coil is approaching it. The strapping head only powers up right before it needs to apply a strap.
- "Sleep" Modes: During longer periods of inactivity (e.g., a gap in production), the entire line can enter a low-power "sleep" mode. It then wakes up instantly when the next coil is detected. This eliminates the parasitic energy drain from dozens of motors and control panels sitting idle. It's a simple concept, but in a 24/7 operation, the accumulated savings are substantial.
What's the ROI of Upgrading an Aging Coil Packing Line?
Your existing packing line has been running for over 15 years. You know it's not perfect. Breakdowns are becoming more frequent, sourcing spare parts is a headache, and it requires a lot of manual oversight. You may be thinking, "It still works, so why replace it?" But the hidden costs of keeping that old equipment running are likely much higher than you realize. Every unexpected shutdown, every scrapped coil due to a bad wrap, and every hour of overtime for maintenance is a direct hit to your profit margin. These small, consistent losses prevent you from reaching your goal of an 8% reduction in operating costs.
The Return on Investment (ROI) for upgrading an aging coil packing line is typically realized within 18 to 36 months. This rapid payback comes from direct cost reductions in three key areas: significantly lower maintenance and downtime expenses, reduced labor costs through automation, and lower consumption of energy and wrapping materials. The investment directly boosts operational efficiency and profitability.

I once had a client, a steel processor in the Midwest, who was in this exact situation. He was proud of how long he'd kept his old Italian packing line running. But when we sat down and actually calculated the "cost of doing nothing," the numbers were shocking. He was spending a fortune on reactive maintenance and lost production. The decision to upgrade became simple once he saw the true cost. Calculating the ROI isn't just about the price of the new machine; it's about a clear-eyed comparison of your current reality versus a more efficient future.
Calculating the True Cost and Return
To make a smart investment decision, you need to look at the full picture. A CEO like Javier needs to see a clear, data-driven case. Let's break down the calculation into the tangible costs of the old line and the quantifiable gains of a new one.
The Hidden Costs of Your Old Line
These are the expenses that drain your budget every year. They are the "cost of doing nothing."
- Unplanned Downtime: This is the biggest killer. When the packing line stops, the entire production flow can back up. You're paying for operators to stand around, and you risk missing delivery deadlines.
- Maintenance & Spare Parts: Older machines require more frequent maintenance. Sourcing obsolete parts can be expensive and time-consuming, sometimes requiring custom fabrication.
- Labor Inefficiency: Old lines often require more manual labor for feeding materials, clearing jams, and positioning coils. This labor could be reallocated to more value-added tasks.
- Material Waste: Inconsistent wrapping or strapping can lead to damaged coils or wasted packaging materials, which is a direct material cost.
Quantifying the Gains of a New Line
Now, let's contrast that with the benefits of a new, automated line from SHJLPACK. We can put real numbers to these improvements.
Metric | Aging Line (Annual Cost Example) | New SHJLPACK Line (Annual Savings) | How the Savings Are Achieved |
---|---|---|---|
Downtime Costs | $150,000 (at 40 hrs/year) | $120,000 | 80% reduction in downtime due to reliable new components and predictive maintenance alerts. |
Labor Costs | $120,000 (2 operators/shift) | $60,000 | Automation reduces need from 2 operators to 1, reassigning the other person. |
Energy Costs | $30,000 | $12,000 | 40% reduction from high-efficiency motors, VFDs, and smart sleep modes. |
Material Costs | $15,000 (waste/inefficiency) | $10,000 | Precise, automated application of wrapping material reduces waste and ensures consistency. |
Total Annual Savings | $202,000 |
With a new line costing, for example, $450,000, the payback period would be just over two years. For a steel mill owner, this is a compelling business case. It's not an expense; it's a high-return investment in efficiency and profitability.
How Does a New Packing Line Integrate with Digital Transformation Goals?
You're a forward-thinking leader. You've already invested in a smart scheduling platform and are looking at MES and IoT to get a complete view of your plant. You want to move from reacting to problems to predicting them. But a digital transformation is only as strong as its weakest link. If your packing line is an "analog island" in a "digital sea," it can't share data. You have no visibility into its performance, efficiency, or health. This creates a blind spot in your operations, making it impossible to achieve your goal of 95% capacity utilization and true production visualization.
A modern packing line is designed as a native digital asset, built to integrate seamlessly with your plant's digital ecosystem. It integrates with your MES/ERP systems using standard protocols like OPC-UA to receive production orders and send back real-time data on cycle times, material consumption, and operational status. Onboard IoT sensors provide the raw data for predictive maintenance platforms, transforming the line from a black box into a transparent, data-rich node in your smart factory.
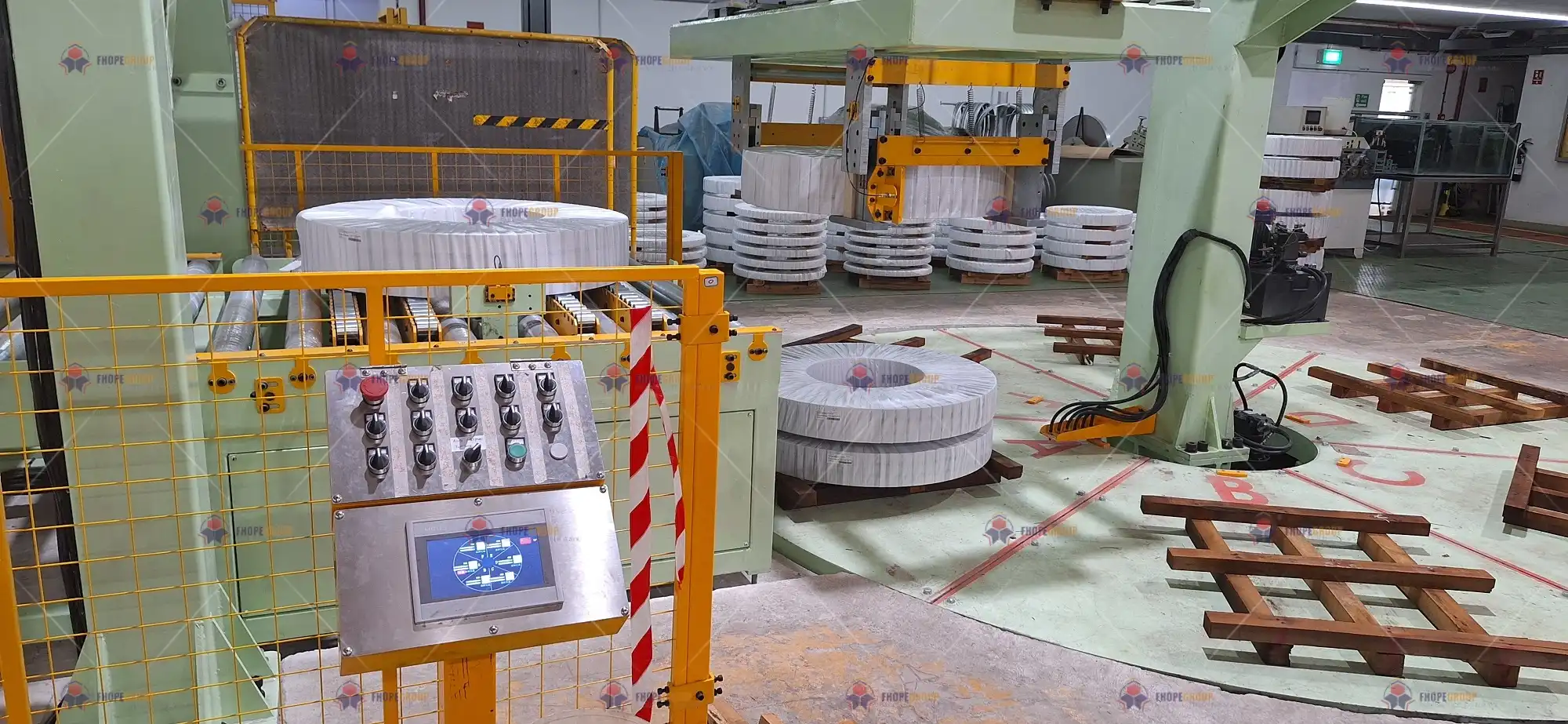
When I started SHJLPACK, our focus was on building robust mechanical systems. But the world has changed. Today, we are just as focused on the data and controls as we are on the steel and motors. A machine that cannot communicate is a machine that belongs in the past. We design our equipment with the understanding that it must be a contributing member of your digital factory, providing the information you need to make smarter, faster decisions. It’s not an add-on; it’s part of the core design.
Building a Bridge to Your Digital Factory
Integrating a piece of equipment into a plant-wide digital system can seem complex, but we've simplified it by focusing on three key areas. This approach ensures our machines are ready for Industry 4.0 from day one.
The Foundation: Data Collection via IoT
You can't manage what you don't measure. That's why we embed sensors throughout our packing lines. This isn't just about counting coils.
- Operational Sensors: We track cycle times, wrapping material tension, number of straps applied, and conveyor speed. This data feeds directly into your OEE calculations.
- Condition Monitoring Sensors: We monitor motor temperature, bearing vibration, and hydraulic pressure. These are the vital signs of the machine's health. This data is the foundation for moving from a reactive "fix it when it breaks" model to a proactive, predictive maintenance strategy.
Speaking the Same Language: MES/ERP Integration
A machine that generates data is good. A machine that can share it with your central planning systems is powerful. We ensure seamless communication.
- Standard Protocols: Our control systems are built on universal platforms (like Siemens or Allen-Bradley) and communicate using standard protocols like OPC-UA or Profinet. This means we don't need complex, custom gateways to talk to your MES. It's a plug-and-play philosophy.
- Two-Way Communication: The integration isn't just one-way. Your MES can send a "recipe" to the packing line for an incoming coil (e.g., specific wrapping layers, strapping pattern). After the coil is packed, our line sends back a confirmation, along with the actual materials used and the time taken. This closes the loop on production tracking and inventory management.
From Data to Action: Enabling Smart Operations
Data is only useful if it leads to better decisions.
Digital Goal | How the Packing Line Contributes | Tangible Outcome for You |
---|---|---|
Full Production Visualization | The line reports its status (running, idle, fault) and performance in real-time to your central dashboard. | You can see bottlenecks at the end of your process instantly, without walking the floor. |
Predictive Maintenance | Vibration data from a motor shows a trend of increasing alerts over several weeks. | Your system flags the motor for replacement during the next planned shutdown, avoiding a catastrophic failure and 12 hours of unplanned downtime. |
Increased Capacity Utilization | By providing accurate cycle time data, the line helps your smart scheduling platform create more realistic and efficient production plans. | Your plant can process more tons per shift, moving closer to the 95% utilization target. |
This level of integration turns your packing line from a simple machine into an intelligent part of your entire manufacturing process.
Why Is a Strategic Partnership More Valuable Than a Simple Supplier Relationship?
When you're making a significant capital investment, you have a choice. You can find a supplier who will sell you a machine based on a spec sheet and a price. The transaction is clean, but it's also shallow. When a problem arises during installation or a unique operational challenge appears a year later, where is that supplier? You're often left with a manual and a phone number for the spare parts department. This transactional approach leaves you to solve complex problems on your own, putting your production and long-term goals at risk.
A strategic partnership is more valuable because it extends far beyond the initial sale. A true partner, like SHJLPACK, invests time to understand your specific challenges and goals—from cost pressures to digital ambitions. We act as an extension of your engineering team, providing customized design, hands-on project management during installation, ongoing optimization advice, and proactive support to ensure the equipment delivers maximum value throughout its entire lifecycle.

This is personal for me. I didn't achieve financial independence and build my company just by selling equipment. I did it by helping my clients succeed. I learned that my success was directly tied to theirs. When a client's business grew because our solution solved a critical problem, we both won. That's why I founded SHJLPACK on the principle of knowledge sharing and partnership. We're not just here to sell you a machine. We're here to give you the total solution and share the expertise we've gained over decades to help you thrive.
The Difference Between a Transaction and a Partnership
A pragmatic leader like Javier understands that the true value of an investment is measured over years, not just on the day of purchase. The difference between a supplier and a partner becomes clear when you look at how they engage with you at every stage of the equipment lifecycle.
The Supplier Mindset: A Limited View
A supplier's job is to fulfill an order. Their process is often linear and transactional.
- Sales: Provide a standard catalog and a quote based on your requested specs.
- Delivery: Ship the machine to your dock.
- Support: Act as a reactive source for spare parts and service calls when something breaks.
The relationship is defined by the transaction. Once the machine is paid for, their primary responsibility is over. They sold you a tool; it's up to you to figure out how to get the most out of it.
The SHJLPACK Partner Mindset: A Shared Journey
As your partner, our involvement is deeper and continuous. We see ourselves as part of your team, sharing your goals for efficiency, cost reduction, and growth.
Stage | The Supplier Approach | The SHJLPACK Partnership Approach |
---|---|---|
1. Discovery & Design | "What machine do you want to buy?" | "What is the core problem you need to solve? What are your five-year goals for this production line?" We then co-design a solution tailored to these answers. |
2. Installation & Commissioning | Sends technicians to assemble the machine. | Manages the project, integrates with your other systems, and provides comprehensive, hands-on training for both your operators and your maintenance crew. |
3. Operation & Optimization | Waits for your call when there's a problem. | Proactively schedules check-ins. We analyze the machine's performance data with you and suggest adjustments to improve efficiency or reduce material use. |
4. Future Planning | "Are you ready to buy a new machine?" | "How are your market demands changing? Let's discuss a potential upgrade to your control system to meet new environmental regulations or a modification to handle a new coil size." |
This partnership model is the core of our slogan: "TOTAL SOLUTION FOR WRAPPING MACHINE." The solution isn't just the physical equipment. It's the expertise, the support, and the shared commitment to your success. It's about building a relationship of trust where you know you have an expert on call who understands your business, not just his own products.
Conclusion
Choosing the right coil packing line is a strategic decision that directly impacts your costs, efficiency, and future growth. It's more than steel and motors; it's your path to greater profitability.