Struggling with the final step in your production line? In the U.S. steel industry, many mills perfect the process of creating high-quality steel coils, only to face bottlenecks, safety risks, and rising costs at the packing stage. Manual packing is not just slow; it's a drain on resources and a constant source of inefficiency. You watch as labor costs climb, skilled workers become harder to find, and the risk of a workplace injury looms over every shift. This final, crucial step is holding your entire operation back, impacting your bottom line and your ability to compete. The solution is no longer a question of 'if,' but 'when.' Shifting to an automated coil packing system is the strategic move that transforms this weak link into a powerhouse of efficiency, safety, and quality.
U.S. steel mills are replacing manual coil packing with automation primarily to reduce high labor costs, improve worker safety, increase operational efficiency, and ensure consistent, high-quality packaging that protects valuable steel coils during transport and storage. This strategic shift allows mills to reallocate their workforce to higher-value tasks, eliminate a major source of workplace accidents, and deliver a perfectly protected product to their customers every time, strengthening their competitive position in a demanding market.
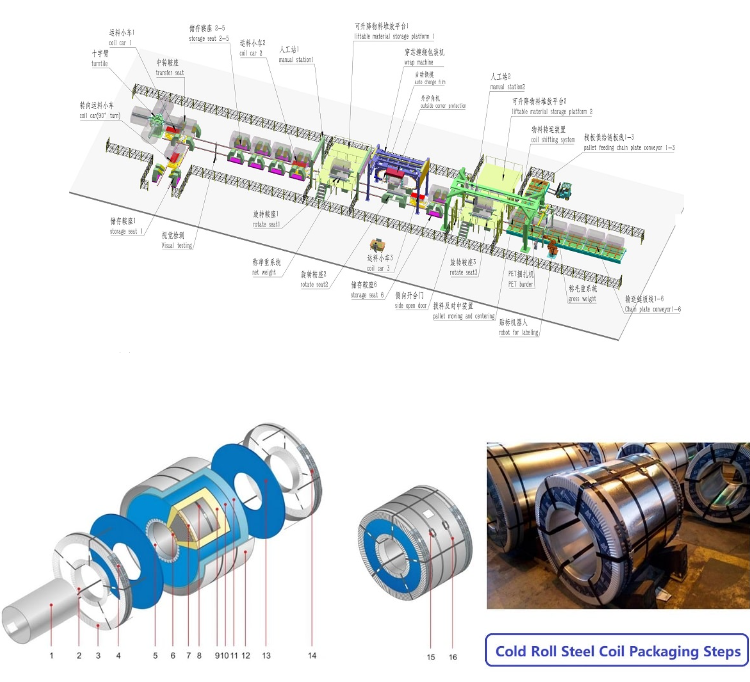
I’ve spent my entire career in this industry, from working on the factory floor to building my own packing machine company, SHJLPACK. I’ve seen firsthand how a well-designed automated system can completely change a company's future. It’s not just about a new machine; it's about a new way of thinking about your process. For leaders like Javier Morales in Mexico, who I know are always looking for a strategic edge, understanding this shift is critical. It’s about more than just keeping up; it’s about leading the way. Let's dig deeper into the specific reasons why this change is happening now and what it means for your operation.
How Does Automated Coil Packing Address Rising Labor Costs and Safety Concerns in U.S. Mills?
Finding good people for the tough, physically demanding job of packing steel coils is a major challenge. Mills across the U.S. tell me the same story: it's hard to hire, even harder to retain, and the costs just keep going up. This isn't just about wages; it includes training, benefits, and the high cost of turnover. This constant staffing problem creates instability right at the end of your production line. Worse, the work itself is hazardous. You have heavy coils, sharp strapping, and powerful equipment all in one place. A single moment of inattention can lead to a serious injury, a production shutdown, and a huge liability. You're constantly balancing the need for output with the safety of your team. This is a difficult, stressful, and expensive way to operate. The answer is to take the person out of the hazardous equation with a system that works reliably and safely, 24/7.
Automated coil packing directly addresses labor issues by replacing dangerous, manual tasks with reliable machinery. This cuts labor costs, reduces staff turnover, and dramatically improves workplace safety by minimizing human interaction with heavy coils and moving equipment. By automating, you solve two of your biggest headaches at once: you create a more stable, predictable cost structure and you build a much safer work environment for your employees.
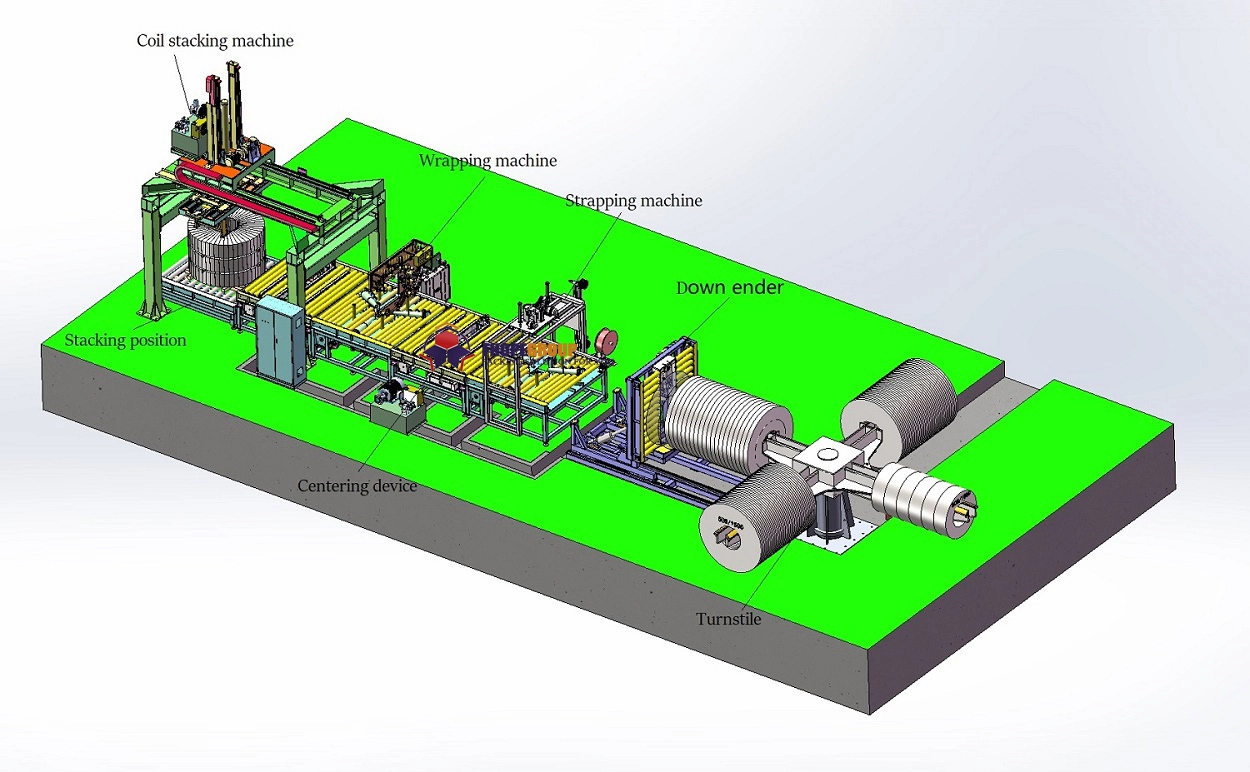
A Deeper Look at the Numbers and Risks
As an engineer and a factory owner, I always look at the hard data. The decision to automate isn't just about feeling better; it's about making a sound financial and operational choice. When we analyze the real impact of manual packing, the numbers are often worse than leaders realize.
The Financial Drain of Manual Labor
Let's break down the true cost of a manual packing team. It's not just the hourly wage. Consider a typical manual packing station in a U.S. mill that requires three workers per shift, running three shifts a day. The costs add up quickly.
Cost Component | Annual Cost (Estimated) | Notes |
---|---|---|
Direct Wages | $438,000 | Based on 9 workers at ~$25/hr |
Benefits & Payroll Taxes | $131,400 | Typically 30% of wages |
Training & Onboarding | $27,000 | Assuming 30% annual turnover, costing $10k per new hire |
Overtime | $43,800 | To cover absenteeism and demand spikes (est. 10%) |
Total Annual Labor Cost | $640,200 | This is a recurring, variable expense. |
This is a conservative estimate. It doesn't even include the indirect costs of lower morale or the management time spent dealing with staffing issues. An automated system, on the other hand, has a predictable, fixed operating cost. You replace a large, variable expense with a capital asset that builds equity.
The Unacceptable Cost of Poor Safety
Beyond the financial numbers, there's the human cost. Manual coil packing is consistently one of the highest-risk areas in a steel mill. Common injuries include severe back strains from lifting, deep cuts from steel strapping, and crushing injuries from moving coils. An OSHA recordable incident isn't just a number; it means one of your team members got hurt. It also means investigations, potential fines, and a significant increase in your workers' compensation insurance premiums. Automation removes your employees from this "danger zone." The machine handles the heavy lifting, the sharp materials, and the repetitive motions. Your workers can then be retrained for safer, higher-value roles like quality control, system monitoring, or maintenance planning. This shift doesn't just reduce your liability; it shows your team that you value their well-being, which is essential for building a strong company culture.
What Is the True ROI of an Automated Coil Packing Line?
I speak with steel mill owners like Javier all the time. They are sharp business leaders. The first question they ask is always about the return on investment. "Vincent, this is a big check to write. How fast will I get my money back?" They know that every piece of equipment must justify its place on the factory floor with a clear, measurable financial return. They are tired of hearing vague promises. They want to see the numbers. The risk of investing a large amount of capital into a system that doesn't deliver a fast and significant return is a major concern. It can feel safer to stick with the "known" cost of manual labor, even if it's inefficient. But this is a trap. Continuing with an outdated manual process is not avoiding a cost; it's choosing to accept a continuous financial leak.
The true ROI of an automated coil packing line goes beyond labor savings. It includes increased throughput, reduced material waste, eliminated product damage claims, lower energy consumption, and improved uptime, often resulting in a payback period of 18 to 36 months. When you calculate the full scope of savings and new value created, the investment in automation becomes one of the most financially sound decisions a mill can make.
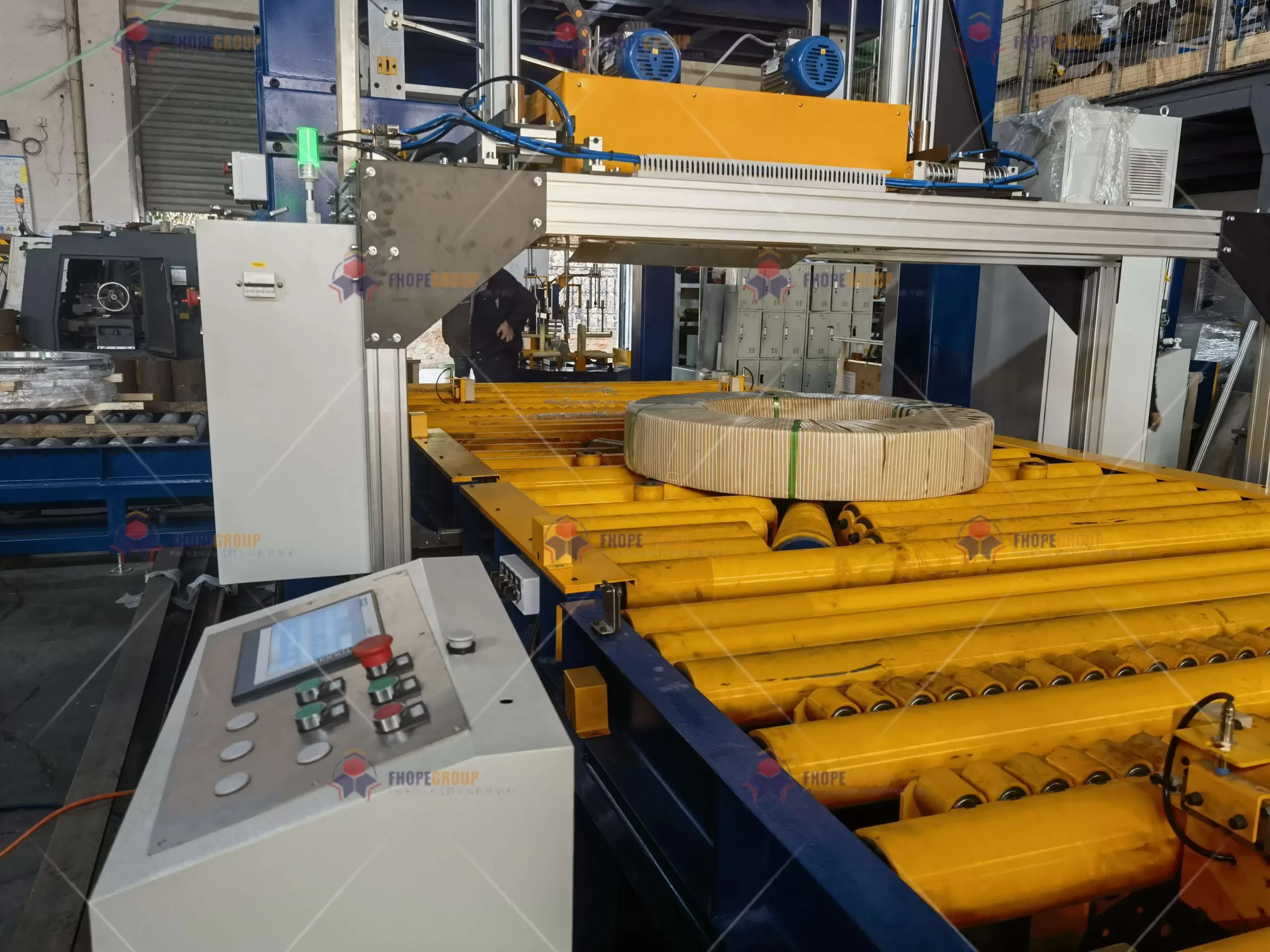
A Deeper Look at Calculating Your Return
A proper ROI calculation must be comprehensive. When I started my own factory, I learned that the obvious costs are only part of the story. You have to look at everything the new system touches. Let's build a sample calculation to see how this works in a real-world scenario for a U.S. mill.
A Framework for ROI Analysis
Let’s assume a mid-sized U.S. mill is considering a fully automated packing line with an initial investment of $1,200,000.
Financial Impact Area | Manual Process Cost/Loss (Annual) | Automated System Benefit (Annual) | Notes |
---|---|---|---|
Direct Labor Savings | $640,200 | $576,180 | Replaces 9 manual packers with 1 system supervisor (90% reduction). |
Material Cost Reduction | $50,000 | $25,000 | Automated stretch wrappers use 50% less film due to precise pre-stretch. |
Product Damage Reduction | $120,000 | $108,000 | Reduces damage claims from 1% to 0.1% on $12M of shipped product. |
Increased Throughput Value | $0 | $150,000 | Packing 10% more coils per day without overtime adds significant revenue. |
Total Annual Savings/Value | $859,180 |
Payback Calculation:
- Initial Investment: $1,200,000
- Total Annual Savings: $859,180
- Payback Period = $1,200,000 / $859,180 = 1.4 years (or approximately 17 months)
This is a powerful result. A payback period under two years makes this a top-priority project for any CFO or CEO.
The Hidden Costs of Inaction
What the table above doesn't show is the opportunity cost of not automating. While you delay, you are actively losing nearly $860,000 per year. Your competitors who have already automated are operating with a lower cost base, allowing them to be more aggressive on pricing or to reinvest that money into other innovations. Furthermore, every time a customer receives a poorly wrapped or damaged coil, your brand reputation takes a hit. In a competitive market, a reputation for unreliable packaging can be enough to lose a major contract. These are the soft costs that become very hard, very quickly. Automating is not just about saving money; it's about protecting and growing your business for the future. It aligns directly with strategic goals like reducing overall operating costs and improving profitability.
How Does Automation Improve Packing Quality and Reduce Product Damage?
You've spent millions of dollars and immense effort to produce a perfect coil of steel. It meets every metallurgical and dimensional specification. Then, it gets to the final stage: packing. A poorly wrapped coil is a huge problem. If the wrap is too loose or has gaps, moisture gets in during transport or storage, leading to rust and surface defects. Your customer rejects the coil, and you have to deal with a costly claim and the logistics of a return. Or, if the strapping isn't tight enough, the coil can shift, causing edge damage or even safety issues during handling. The quality of manual packing is inconsistent. It depends on the skill of the worker, how tired they are, and whether they are rushing at the end of a long shift. This variability introduces risk you cannot control.
Automation improves packing quality by applying wrapping materials and straps with consistent tension, precise overlap, and perfect placement. This uniformity creates a superior moisture barrier and a stable package, drastically reducing the risk of corrosion and physical damage during shipping and handling. The machine executes the perfect packing recipe every single time, 24/7, without getting tired or distracted. This consistency is the key to protecting your product, your reputation, and your bottom line.

A Deeper Look at the Science of Protection
From my years designing these machines, I can tell you that a perfect wrap is a science. It's about controlling specific variables that are nearly impossible for a human to manage consistently. An automated system gives you precise control over the entire process, turning packaging from an art into an engineering discipline.
The Key Parameters of a Perfect Wrap
When we design a packing line, we focus on several critical factors that determine the integrity of the final package. A machine can control these with incredible precision, while a human can only approximate them.
Parameter | Manual Packing | Automated Packing | Impact on Quality |
---|---|---|---|
Film Stretch Ratio | Inconsistent (0-50%) | Precisely controlled (250-300%) | Higher stretch makes the film stronger and uses less material. |
Film Overlap | Variable | Consistent (e.g., 50% +/- 1%) | Ensures a complete, waterproof seal with no gaps. |
Wrapping Tension | Inconsistent | Consistent | Prevents film from loosening during handling. |
Edge Protection | Placed by hand, can shift | Applied automatically before wrapping | Protects the most vulnerable part of the coil from damage. |
Strap Tension & Placement | Variable by operator | Precisely controlled and placed | Ensures the coil is secure and stable for transport. |
This level of precision makes a huge difference. For example, our automated stretch wrappers have a powered pre-stretch carriage. This device stretches the film by up to 300% before it's applied to the coil. This not only makes the wrap much stronger and more puncture-resistant but also reduces film consumption by 50-70% compared to manual wrapping. That's a direct saving on consumables that adds up with every coil you ship.
Protecting Your Brand and Customer Relationships
Think about it from your customer's perspective. When they receive a delivery, the packaging is the first thing they see. A professionally wrapped, secure, and uniform coil sends a powerful message. It says you are a high-quality, reliable supplier who cares about every detail. It builds confidence. On the other hand, a shipment that arrives with loose wrapping, signs of rust, or damaged edges immediately raises concerns about the product inside and your company's standards. In my experience helping clients, improving packaging quality has a direct impact on customer retention and can even become a selling point to win new business against competitors with sloppy standards. It turns your packaging from a simple necessity into a part of your brand promise.
Can New Automated Packing Lines Integrate with Existing MES and IoT Systems?
You are a forward-thinking leader. You're not just running a steel mill; you're building a smart factory. You're investing in a Manufacturing Execution System (MES) to schedule and track production. You're deploying Internet of Things (IoT) sensors to monitor equipment health. The goal is total visibility and data-driven decision-making. The last thing you want is to buy a new, expensive piece of equipment that operates like a "black box." A machine that can't communicate with your other systems is a dead end. It creates an island of isolation on your factory floor, preventing you from achieving your digitalization goals and making it impossible to get a true picture of your overall equipment effectiveness (OEE).
Yes, modern automated packing lines are designed to fully integrate with existing MES and IoT platforms through standard industrial protocols like OPC-UA, Profinet, or EtherNet/IP. This enables seamless two-way communication. Your MES can automatically send the coil ID and required packing recipe to the line, and the line can send back vital data like cycle times, material consumption, and machine status, providing the real-time visibility needed for a truly smart factory.

A Deeper Look at Creating a Connected Factory
When I built my factory, I saw the power of connected systems. Information flowing freely between machines and software is what separates a modern, efficient plant from an old, inefficient one. For a leader like Javier, who has a goal of 95% equipment uptime and a fully visualized production process, this integration is not a luxury; it is a necessity.
The Data Handshake: MES and the Packing Line
Let's look at how the connection works in practice. It’s a simple but powerful flow of information that eliminates manual data entry and potential errors.
- Coil Arrival: A coil arrives at the packing line. An overhead scanner reads its unique barcode or QR code.
- MES Request: The packing line's PLC (Programmable Logic Controller) sends the coil ID to the plant's MES.
- Recipe Download: The MES looks up the coil ID in its database, finds the specific customer order, and sends the correct "packing recipe" back to the PLC. This recipe tells the machine exactly how to wrap and strap that specific coil (e.g., film type, number of wraps, strap positions).
- Process Execution: The automated line executes the recipe perfectly.
- Data Feedback: Once complete, the line sends data back to the MES: cycle time, film and strap consumption, final weight, and a "complete" status.
This closed-loop communication is the foundation of Industry 4.0. It ensures the right packing is used for every coil, provides accurate material consumption data for inventory management, and gives production managers real-time status updates.
Predictive Maintenance through IoT
This is where things get really smart. We embed IoT sensors throughout our packing lines to monitor the health of critical components.
- Vibration sensors on main drive motors can detect bearing wear weeks before a failure.
- Temperature sensors on hydraulic pumps can alert you to overheating issues.
- Pressure sensors in pneumatic lines can identify leaks that waste compressed air and energy.
This data is streamed to your plant's data analytics platform. Instead of waiting for a machine to break down and stop production (reactive maintenance), your maintenance team gets an alert: "The main wrapper motor is showing increased vibration. Schedule a bearing replacement during the next planned downtime." This is predictive maintenance. It is the single most effective strategy to move from 85% uptime to the 95% target that leaders like Javier are aiming for. It turns unplanned, costly downtime into planned, efficient maintenance.
My Insights: Beyond the Machine – Why Your Team Is Key to Automation Success
I've sold and installed hundreds of packing lines. I've seen incredible successes, and I've seen projects that struggled. The difference was never the quality of the steel or the size of the mill. It wasn't even the technology itself. The single biggest factor for a successful automation project is the people.
When I first started my own factory, I thought that having the best machines would solve all my problems. I was an engineer, and I believed in technology. But I quickly learned a hard lesson. A machine is just a tool. It has no passion, no ingenuity, and no commitment. The real power comes from the team that operates, maintains, and continuously improves the process around that machine. Buying an automated system is not about replacing your people. It's about empowering them. It's about taking away the dangerous, dull, and dirty work so they can use their minds to solve bigger problems.
This is the part of the process I am most passionate about now. I've been fortunate in this industry, and I want to share what I've learned. The machine is the easy part. Building the right culture around it is what creates lasting success.
Your Team Is Your Greatest Asset, Not an Obstacle
I often hear managers worry that their team will resist a new automated system. They fear change. But in my experience, that resistance usually comes from a place of fear—fear of being replaced or fear of not being able to learn the new technology. The solution is simple: involve them from day one.
Before we even finalize a design, I insist on talking to the operators and maintenance technicians who work on the current packing line. They know things no engineer or manager can. They know why one type of wrapping film always tears. They know the forklift driver on the night shift has a habit of bumping into the conveyor. This "on-the-ground" knowledge is priceless. When you listen to their input and incorporate their ideas into the new system, they are no longer being forced to accept a change. They become co-creators of the solution. They take ownership.
Training Is an Investment, Not an Expense
Once the system is installed, the work is not over; it has just begun. The most successful U.S. mills I've worked with invest heavily in training. And I don't mean a two-hour session on which buttons to push. I mean deep, comprehensive training that covers:
- Operation: How to run the machine safely and efficiently.
- Mechanics: How the different parts of the machine work together.
- Troubleshooting: How to identify and fix common problems.
- The "Why": Why the machine is programmed a certain way, and how it connects to the plant's overall goals.
When you empower your team with this level of knowledge, they stop being simple operators and become system technicians. They can solve small problems before they become big ones, and they can suggest improvements to make the line run even better. This is how you unlock the full potential of your investment.
Choose a Partner, Not a Supplier
Finally, this journey is too important to take with someone who just wants to sell you a machine. A supplier will deliver the equipment and disappear. A true strategic partner, which is what we strive to be at SHJLPACK, works with you for the long term. We help you design the right system, we work with your team during installation, we provide the deep training they need, and we are there to support you for the life of the machine.
For a leader like Javier, who thinks in terms of long-term strategy and partnerships, this is the only approach that makes sense. The goal is not just to install a machine. The goal is to make your business more competitive, more profitable, and more resilient for the future. And that is something you build together.
Conclusion
Automating coil packing is a strategic imperative for U.S. steel mills. It delivers clear returns in cost, safety, quality, and efficiency, securing a competitive advantage for years to come.