Steel producers in the United States are navigating a difficult landscape. You're facing pressure from all sides: aging equipment is becoming less reliable, volatile energy costs are eating into your margins, and demanding safety and environmental regulations require constant attention and investment. Your current coil packaging line, once a reliable part of your process, might now be a significant bottleneck. It could be causing production delays, driving up operational costs, and holding you back from achieving your true potential. Every time an old machine breaks down, it costs you more than just the repair bill; it costs you precious production time and affects your delivery schedules. Every wasted kilowatt-hour is a direct hit to your profitability. Failing to keep up with safety and environmental standards is not just a compliance issue; it's a direct risk to your reputation, your people, and the long-term health of your business. What if you could solve this? Imagine replacing that inefficient bottleneck with a modern, automated coil packaging line, engineered specifically for the rigorous demands of the American market. A system that doesn't just meet standards but exceeds them, drastically cuts energy consumption, and integrates perfectly with your vision for a digital, data-driven factory.
Coil packaging lines built for U.S. manufacturing standards are complete, engineered systems that prioritize safety, efficiency, and long-term durability. They achieve this by integrating robust, North American-spec components, advanced automation for consistency and speed, and fully customizable features designed to meet or exceed specific OSHA, ANSI, and environmental regulations. This ensures reliable, predictable performance and delivers a lower total cost of ownership for American steel producers.

This is about more than just buying a new piece of equipment. It's a strategic investment in the future resilience and profitability of your plant. I've been in this industry for a long time, first as an engineer, then as a factory owner myself. I have seen, time and again, how the right packaging solution can transform an entire operation from a cost center into a competitive advantage. It’s not just about wrapping steel; it’s about unlocking efficiency. Let's break down what truly matters when you are looking for a packaging line that is genuinely built for the challenges and opportunities in the American market.
How Can a Modern Coil Packaging Line Tackle Rising Energy Costs and Aging Equipment?
Your packaging line has been a workhorse for over 15 years, but now it's starting to show its age. It consumes far too much power, and unexpected breakdowns are happening more often, creating a ripple effect of delays across your entire production flow. You feel the constant pressure of this unreliability. Every time that line goes down, you're not just paying for a technician and parts; you're losing valuable output and potentially delaying customer orders. At the same time, your energy bills continue to climb, driven by inefficient motors and outdated hydraulic systems that run at full power whether they need to or not. You know a change is necessary, but the thought of a large capital investment feels like a major hurdle. A modern coil packaging line, however, is designed specifically to solve these problems. It is built with energy efficiency as a core principle, using high-efficiency motors, intelligent sensors, and power-saving standby modes to cut electricity consumption significantly. It also replaces high-maintenance mechanical and hydraulic parts with durable, reliable, and predictable components, directly addressing the root cause of your expensive downtime.
A modern coil packaging line directly confronts these challenges by integrating energy-efficient technologies and robust, low-maintenance designs. It utilizes Variable Frequency Drives (VFDs) on all major motors to drastically reduce power consumption during non-peak movements and incorporates predictive maintenance sensors to alert your team to potential issues before they cause a failure. This approach simultaneously boosts your equipment uptime to new levels and cuts your daily operational costs.
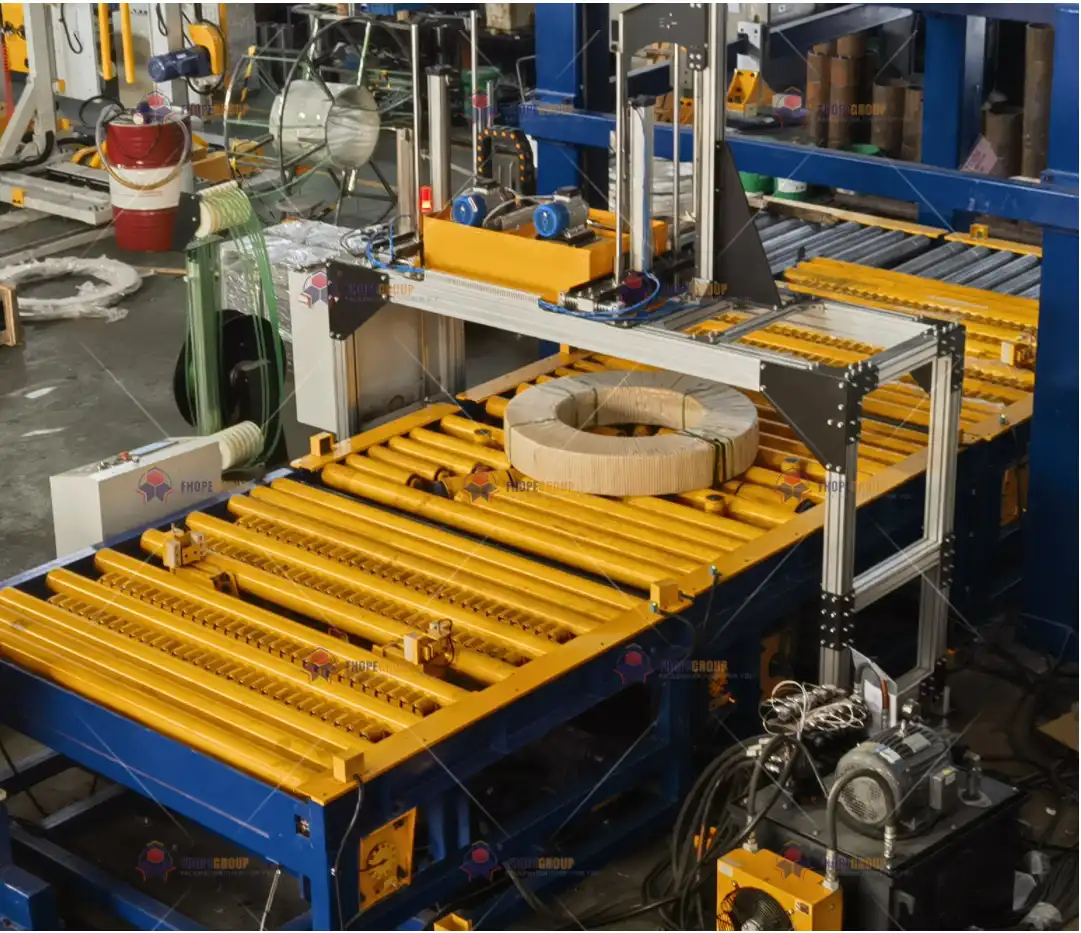
Dive Deeper: The Tangible Benefits of Upgrading
Let's look closely at the specific technical differences that deliver these results. It’s not just a vague promise of "better"; it's a fundamental change in engineering philosophy.
The High Cost of Inefficiency
An older packaging line likely uses oversized, fixed-speed AC motors. These motors run at 100% capacity from the moment you turn them on until you shut them off, even when the machine is idle between coils. This is like leaving your car's engine revving at full throttle while you're stopped at a red light. The wasted energy is immense. A modern line from SHJLPACK uses Variable Frequency Drives (VFDs) on all key motors—for the conveyor, the wrapper, and the tilter. A VFD acts like a smart gas pedal, supplying the exact amount of power needed for the task at hand. When a coil is being conveyed, the motor gets full power. When it's waiting for the next coil, the VFD ramps the motor down to a near-zero energy state. This single technology can reduce the line's energy consumption by 15-30%.
From Reactive Repairs to Predictive Maintenance
The maintenance model for aging equipment is almost always reactive: something breaks, production stops, and your team scrambles to fix it. This is the most expensive and disruptive way to manage machinery. A modern line is designed for a proactive, predictive approach. We embed IoT-ready sensors to monitor critical components. For example, we place vibration sensors on motor bearings and temperature sensors on gearboxes. This data can be fed directly into your plant's MES or control system. Instead of discovering a problem when a bearing seizes and destroys a motor, your system will flag a small increase in vibration weeks in advance. This allows you to schedule a quick, low-cost bearing replacement during planned downtime. You move from unpredictable, catastrophic failures to predictable, manageable maintenance. This is essential to achieving a goal like 95% uptime.
Here's a simple comparison:
Feature | Aging Equipment (15+ years) | Modern SHJLPACK Line |
---|---|---|
Motors | Fixed-speed, constantly running | Variable Frequency Drive (VFD), power on demand |
Energy Use | High, constant consumption | Optimized, load-dependent, significantly lower |
Maintenance | Reactive, breakdown-based ("firefighting") | Predictive, data-driven, planned interventions |
Downtime | High, unpredictable, and costly | Minimal, scheduled, and controlled |
Data & Insights | None or from isolated, manual checks | Integrated with MES/IoT for real-time visibility |
This transition is fundamental. It changes your packaging line from a simple machine into an intelligent asset that actively contributes to your cost reduction and efficiency goals.
What Does a Strategic Partnership for Coil Packaging Look Like in Practice?
You have likely worked with suppliers who are great at making the sale but seem to vanish once the invoice is paid. They deliver a machine, but they provide no real support or guidance, leaving your team to struggle with complex installation, integration, and long-term maintenance issues on their own. This approach leaves you feeling isolated and unsupported. When a problem inevitably arises, you find yourself digging through complicated manuals or waiting days for a simple email response from an overseas time zone. You didn't just buy a piece of equipment; you inherited all the problems and responsibilities that come with it. This is a simple transaction, not a partnership. Now, imagine a different experience. Imagine a partner who is with you every step of the way, from the very first design consultation to long-term operational support and optimization. Imagine a dedicated team of engineers who take the time to understand your specific challenges, help you select the perfect configuration, manage the entire installation process, and provide ongoing advice to ensure you get the most out of your investment for years to come. That is what a true strategic partnership looks like.
A strategic partnership for coil packaging moves far beyond a simple transactional sale. It is a deeply collaborative process where the supplier effectively acts as an expert extension of your own team. This partnership provides comprehensive, end-to-end support, beginning with initial consultation and custom design, and continuing through professional installation, operator training, and proactive long-term maintenance. The entire goal is to ensure your equipment delivers maximum possible value and reliability throughout its entire lifecycle.
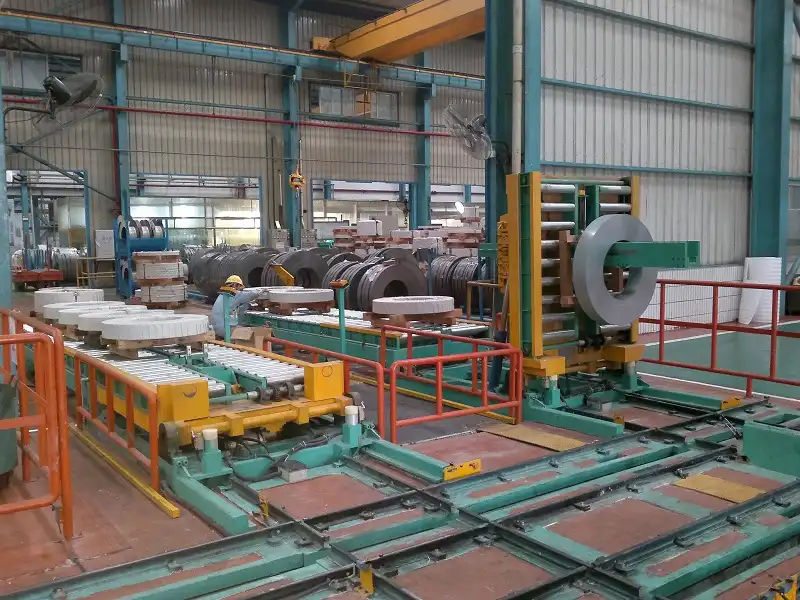
Dive Deeper: The Partnership Journey
A strategic partnership isn't just a sales pitch; it's a structured process designed to guarantee your success. It unfolds in distinct phases, each building on the last.
Phase 1: Consultation and Custom Design
This is the most critical stage. A true partner doesn't start by showing you a catalog. We start by listening. We send our engineers to your facility, or we have detailed remote sessions to understand your reality. We analyze your plant layout, your current process flow, coil dimensions and weights, required throughput, and your specific business goals, like your target of reducing operational costs by 8%. I remember a lesson I learned the hard way when I was running my own factory. I once bought a standard machine because the price was low. It was "good enough," but it wasn't designed for my specific workflow. The small, daily inefficiencies—a few extra seconds per cycle, an awkward loading position—added up to thousands of dollars in lost productivity over the year. That experience taught me everything. It's why at SHJLPACK, we start by understanding your unique needs so we can design a solution that fits your operation perfectly.
Phase 2: Installation and Seamless Integration
Once the design is finalized, the partnership moves to execution. A supplier just delivers a machine to your door. A partner manages the project. We coordinate logistics, provide detailed schematics for electrical and air supplies, and work hand-in-hand with your maintenance and engineering teams during installation. Critically, we focus on integration. We ensure the packaging line's control system can communicate with your plant-level systems, like your MES. This is crucial for your goal of digital transformation. The packaging line shouldn't be an island; it should be a node in your smart factory network.
Phase 3: Long-Term Support and Optimization
Our relationship doesn't end after the machine is running. It's just beginning. We provide comprehensive on-site training for your operators and maintenance staff to empower them. We establish a clear channel for support and ensure the availability of critical spare parts from U.S.-based suppliers. Furthermore, as your business evolves, we are there to help you adapt. If you need to handle a new type of coil or meet a new environmental standard, we can provide the engineering advice and upgrades to help you do it. This long-term view is the core of a partnership.
Partnership Stage | A Supplier's Transactional Role | Our Role as a Strategic Partner |
---|---|---|
Consultation | Sells a standard machine from a catalog | Conducts a deep-dive analysis of your specific operational needs |
Design & Eng. | Offers limited or no customization | Customizes the line for your layout, coils, and goals |
Installation | Delivers the equipment and a manual | Manages the project and ensures seamless integration with your systems |
Training | Minimal or optional | Provides comprehensive on-site training for operators & maintenance |
Ongoing Support | Reactive; you call them with problems | Proactive; provides maintenance advice, optimization, and future-proofing |
How Does Advanced Automation in Packaging Lines Drive Profitability and Digital Transformation?
Your current packaging process may still depend heavily on manual labor. This approach inevitably leads to inconsistencies in the quality of the wrap, creates significant safety risks for your employees, and makes it nearly impossible to get the accurate, real-time operational data you need to make smart decisions. You find yourself constantly battling high labor costs and struggling with workforce availability in a tight labor market. Every single manual step in your process is a potential point of failure, a source of inconsistency, or a cause for delay, actively preventing you from reaching your ambitious goal of 95% equipment uptime. You feel stuck in an analog past while the rest of your industry is rapidly moving towards a digital future. Advanced automation completely changes this dynamic. It transforms your packaging station from a simple, manual workstation into a smart, data-generating hub. Robotic systems, automatic strapping and wrapping heads, and a network of integrated sensors all work in perfect harmony to create a consistent, high-speed, and safe packaging process, all while feeding a constant stream of crucial data directly into your MES platform.
Advanced automation in modern coil packaging lines directly drives profitability by slashing labor costs, dramatically increasing throughput, and nearly eliminating the costly inconsistencies of human error. It serves as a powerful catalyst for your digital transformation goals by using integrated sensors and intelligent PLCs to capture and transmit real-time production data. This data—on cycle times, material consumption, and uptime—enables full production visualization and provides the foundation for smarter, data-driven operational decisions within your Manufacturing Execution System (MES).
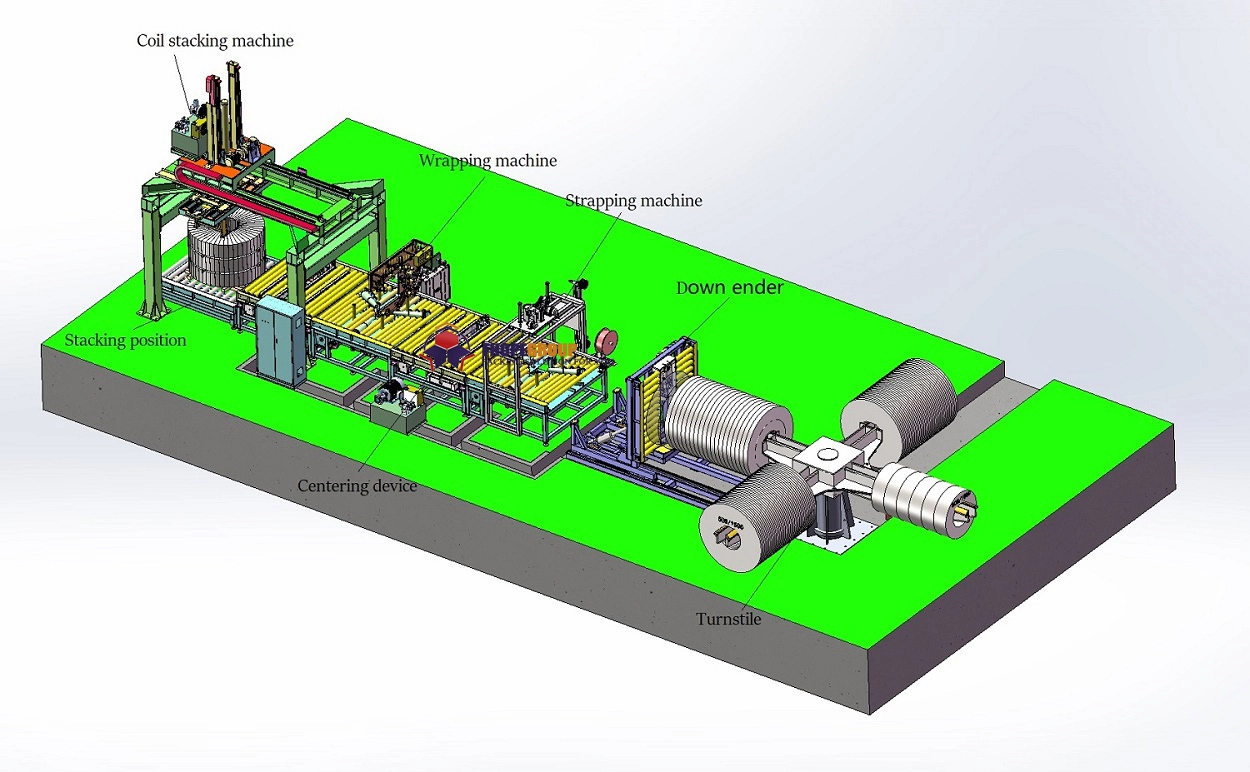
Dive Deeper: Automation as a Two-Part Solution
Advanced automation delivers value on two fronts simultaneously: it optimizes the physical process on the factory floor and provides the data needed for strategic management.
From Manual Labor to Robotic Precision
Think about the number of manual touches in a typical semi-automatic packaging process. An operator might position the coil, manually feed strapping, visually inspect the wrap, and then apply a label. Each step takes time and is subject to human variability. A fully automated line eliminates these variables.
- Automatic Handling: The line automatically receives the coil from an upender or turnstile, conveys it to the wrapping station, and centers it perfectly.
- Automatic Wrapping & Strapping: The wrapping shuttle applies the stretch film with consistent tension and overlap every single time. The strapping head automatically feeds, tensions, seals, and cuts the strap in seconds.
- Automatic Labeling: A print-and-apply system generates a unique label with a barcode and human-readable text, then applies it to the coil in the correct position.
This level of automation directly impacts your goal of reducing operating costs. It can re-assign 1-2 operators per shift to more value-added tasks, reduce packaging material waste through consistent application, and increase the speed of the entire line, boosting throughput. It also dramatically improves safety by removing workers from the immediate vicinity of heavy, moving equipment.
The Packaging Line as a Data Hub
This is where automation connects directly to your digital transformation goals. A modern packaging line is controlled by a powerful Programmable Logic Controller (PLC)—the "brain" of the operation. This PLC is connected to dozens of sensors—photoelectric sensors that detect coil presence, proximity sensors that confirm position, and encoders that measure film usage. Every action generates data:
- Coil ID is scanned upon entry.
- Cycle time is logged for every coil.
- Amount of wrapping film and strapping used is measured.
- Any stoppage or fault is instantly logged with a specific error code.
This data doesn't stay locked in the machine. We ensure the PLC can communicate using standard industry protocols (like OPC-UA or EtherNet/IP) to your plant's MES or SCADA system. Suddenly, your packaging line is no longer a "black box." You have a dashboard showing you real-time Overall Equipment Effectiveness (OEE), material consumption rates, and a detailed history of every coil packaged. This is the very definition of the "comprehensive production visualization" you're aiming for.
Metric | Manual/Semi-Auto Line | Fully Automated SHJLPACK Line |
---|---|---|
Throughput | Limited by operator speed and consistency | Consistent, high-speed, and predictable |
Labor Cost | High (often requires 2-3 operators per shift) | Low (1 supervisor can oversee multiple lines) |
Data Collection | Manual, often inaccurate, and delayed | Real-time, automatic, and fully integrated with MES |
Package Quality | Variable, depends heavily on the operator | Highly consistent and standardized to your spec |
Safety | Higher risk of repetitive strain or acute injury | Significantly lower risk; operators are supervisors |
Why is Customization Key for Meeting U.S. Safety and Environmental Standards?
You are rightfully concerned about compliance. You know that buying off-the-shelf machinery, especially from suppliers without deep experience in the North American market, carries significant risk. This equipment often fails to meet the stringent safety, electrical, and control standards required in the U.S. and can create major liabilities, including the risk of heavy fines, forced production shutdowns, and, most importantly, serious worker injury. The thought of investing hundreds of thousands of dollars in a new line only to have it red-tagged by an OSHA inspector during commissioning is a complete nightmare. Trying to retrofit a non-compliant machine after the fact is an incredibly expensive, time-consuming, and frustrating process. You need equipment that is designed from the ground up to be safe, reliable, and compliant within your specific operational environment. This is why customization is not a luxury; it is an absolute necessity. A purpose-built line incorporates U.S.-standard electrical components, robust safety features like light curtains and physical guarding, and considerations for environmental regulations right from the very first engineering drawing.
Customization is absolutely essential because U.S. manufacturing standards, such as OSHA for machine safety and UL for electrical systems, are non-negotiable and highly specific. A customized packaging line is engineered from its very foundation with compliant, locally-sourced components, appropriate safety guarding, and ergonomic design principles. This meticulous, tailored approach is the only way to ensure the equipment will pass any inspection, protect your workers, and operate reliably and safely within the demanding U.S. regulatory framework.

Dive Deeper: Engineering for Compliance and Peace of Mind
Compliance isn't a feature you can add on later. It must be designed in from the beginning. Here’s what that looks like in practice for the U.S. market.
Navigating the Maze of U.S. Safety Standards
The U.S. has a multi-layered system of codes and standards that go far beyond what is required in many other parts of the world. A responsible machine builder must design for these.
- Electrical Systems: We build control panels to be UL 508A certified. This is a rigorous standard for industrial control panels that ensures safety and quality. We design the entire electrical system according to NFPA 79, the Electrical Standard for Industrial Machinery. This dictates everything from wire colors and sizes to grounding techniques. We frequently use components from trusted, U.S.-supported brands like Allen-Bradley or Siemens, not just for their quality, but because your maintenance team is familiar with them and can get support and parts quickly.
- Machine Guarding: We design our guarding to meet OSHA 1910.212 standards. This means installing robust physical fencing to prevent access to moving parts, as well as integrating modern safety devices like light curtains. A light curtain creates an invisible barrier; if an operator breaks the beam, the machine enters a safe state immediately. We also place emergency stop buttons in all logical operator zones.
I have visited many steel plants in the United States, and I have always been impressed by the deep commitment to safety. It's on a different level. This is why we don't just sell a machine; we engineer a complete, safe system.
Designing for Environmental Compliance
Your challenge with increasing environmental pressure is also a key design consideration for us. A customized line can help you meet your goals.
- Waste Reduction: We can fine-tune the wrapping parameters in the PLC to use the absolute minimum amount of stretch film required to secure your coil, reducing your plastic waste and cost.
- Energy Efficiency: As mentioned before, using VFDs and efficient motors isn't just a cost-saving measure; it directly reduces your plant's energy consumption and, therefore, its carbon footprint.
- Spill Containment: We design systems with proper containment for any lubricants or hydraulic fluids to prevent spills that could lead to environmental contamination and costly cleanup.
This level of detailed customization is how we build a machine that works for you, not against you.
Compliance Area | Standard "Off-the-Shelf" Machine | SHJLPACK Custom-Built Line |
---|---|---|
Control Panel | Generic, may not be certified | UL 508A certified, clearly labeled |
Electrical System | May use non-standard components/wiring | Fully NFPA 79 compliant, uses trusted brands |
Operator Safety | Basic physical guards only | Integrated light curtains, safety PLCs, multiple E-stops |
Environmental | Not considered in the design | Optimized for minimal material waste and energy use |
My Insight: It’s Not About the Machine, It’s About Your Growth
When I started my journey in this industry, first as a young engineer on the factory floor and later as the founder of my own packaging machine factory, I learned a very hard lesson: chasing the lowest price on equipment is a short-term game with long-term costs. The real value is never in the steel frame of the machine itself; it's in how that machine helps your business grow. It’s about the day-in, day-out reliability that lets you sleep at night because you know you can meet your production targets. It's about the efficiency that adds directly to your bottom line, and it's about having a real partnership that helps you solve problems you haven't even thought of yet. I was fortunate enough to achieve financial independence because I eventually learned to stop buying machines and start investing in total solutions. My mission with SHJLPACK is to give you that same powerful advantage—a total solution for wrapping that becomes a cornerstone of your success, just as this industry became the cornerstone of mine. We're not just building packaging lines; we're building partnerships for growth.
Conclusion
Investing in a modern, customized coil packaging line is a direct investment in your plant's efficiency, safety, and future profitability. Let's build it together.