Your factory's energy bill keeps climbing. You know the packaging line is a major consumer, but pinpointing the waste feels impossible. Every kilowatt wasted is profit down the drain. Old, inefficient machines are not just slow; they are silent thieves in your facility, driving up operational costs and hurting your bottom line. This makes it harder to compete and invest in growth. But what if you could cut energy use without sacrificing performance? With the right knowledge and a strategic approach, you can turn your packaging line from an energy drain into an efficient, cost-saving asset.
Reducing energy consumption on steel coil packaging systems involves a multi-faceted approach. Key strategies include upgrading to high-efficiency motors and variable frequency drives (VFDs), optimizing the wrapping process to minimize material and cycle time, integrating automated systems to eliminate idle energy waste, and implementing a strict, proactive maintenance schedule to keep all components running at peak efficiency.
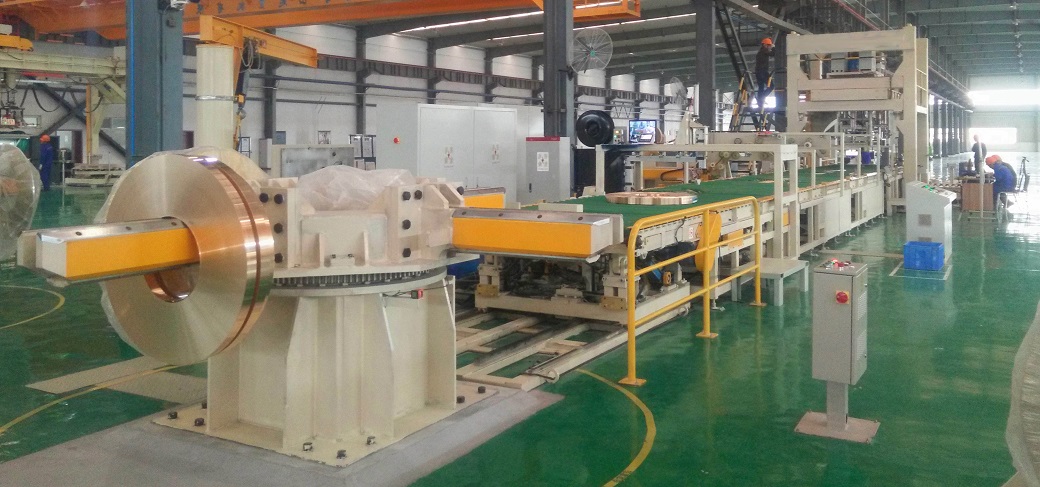
That’s the big-picture view. But as a factory manager, you know the devil is in the details. It’s not just about buying a new machine and hoping for the best. It’s about understanding the specific areas where energy is being lost every single shift. We need to break this down into actionable steps you can take on your factory floor. Let's start with the heart of your machine: the motors and drives that power the entire operation.
How Does Choosing the Right Motor and Drive System Impact Energy Use?
You see the motors on your packaging line running all day. But do you know how much energy they are really wasting? I've been in countless factories where older machines use standard-efficiency motors. They run at full speed from the moment they are switched on until they are switched off. This constant, unnecessary power draw is like leaving a tap running all day long. It's a steady stream of wasted money that directly impacts your operational costs. The solution isn't just a new motor; it's smarter motor control.
Choosing the right motor and drive system is fundamental to reducing energy use. Upgrading from standard motors to premium-efficiency models (IE3 or IE4) and implementing Variable Frequency Drives (VFDs) can cut motor energy consumption by 20-50%. VFDs allow motors to adjust their speed to the exact demand of the task, eliminating the massive energy waste from running at full power constantly.
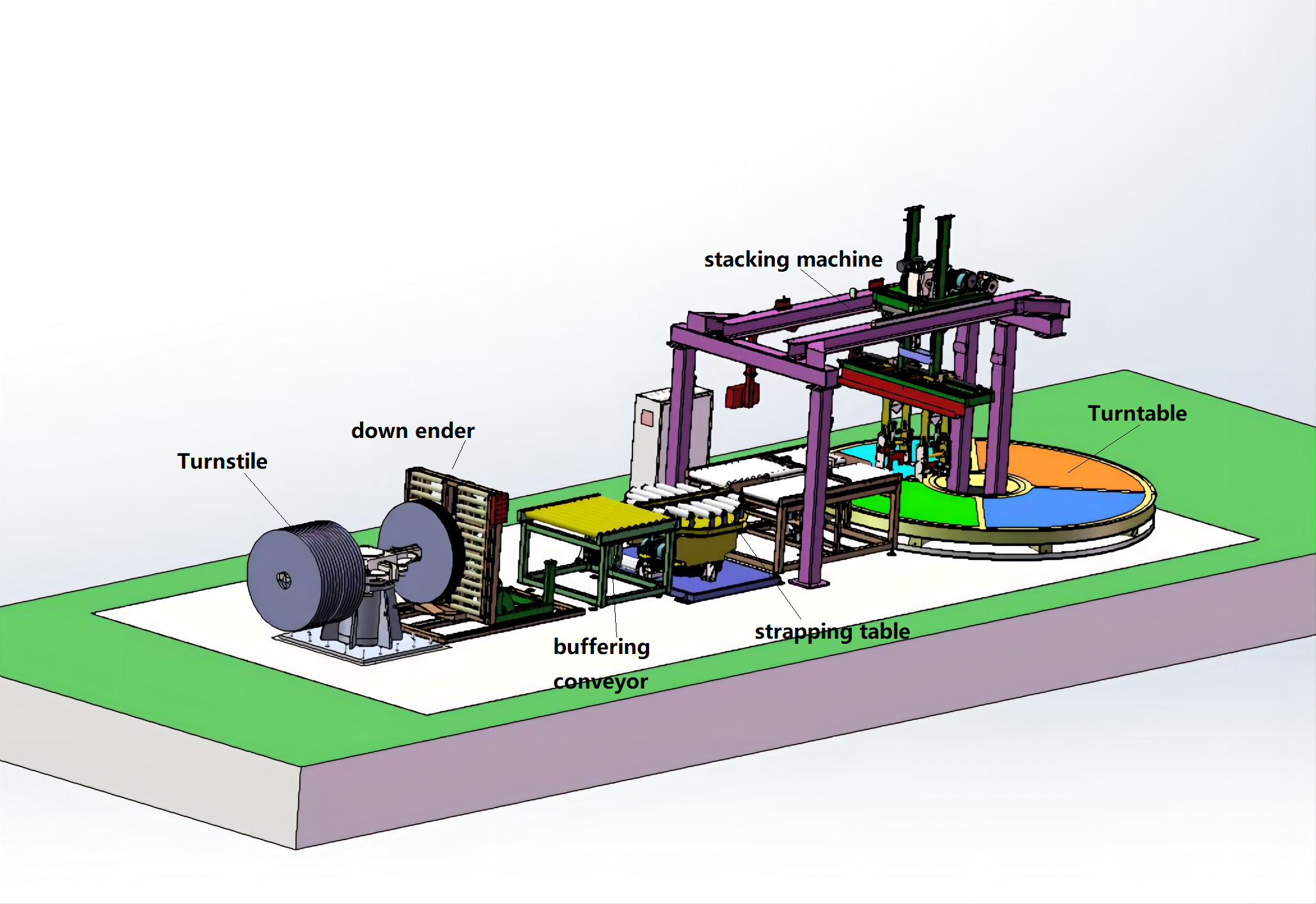
The Hidden Costs of Standard Motors
When I first started my own factory, I learned a tough lesson about upfront costs versus long-term costs. A standard motor is cheaper to buy. That's a fact. But its operating cost is much higher. These motors are designed for one speed: full speed. They are either on or off. Think about your packaging cycle. The machine needs high torque to start the rotation, but much less to maintain the speed. A standard motor, however, draws near-maximum power throughout the entire cycle. It's incredibly inefficient. This inefficiency doesn't just show up on your electricity bill. It also generates more heat, which can contribute to a warmer facility and even shorten the motor's lifespan. It also means more stress on the mechanical parts due to abrupt starts and stops, which increases maintenance needs.
Why Variable Frequency Drives (VFDs) are a Game-Changer
This is where VFDs come in. A VFD is a motor controller that changes the frequency and voltage supplied to the motor. In simple terms, it gives the motor a gas pedal. Instead of just "on" or "off," a VFD can ramp the motor's speed up smoothly and then run it at the precise speed needed for the task. For a coil wrapper, this means a gentle start, an efficient wrapping speed, and a smooth stop. I remember working with a client in Mexico, a manager much like yourself named Michael. He was skeptical about the extra cost of VFDs. I showed him the numbers. His old machine was drawing almost the same amperage during the entire 90-second cycle. With a VFD, the power draw spikes for a second at the start and then drops by nearly 40% for the rest of the cycle. The proof was right there on the amp meter.
Calculating the ROI on a VFD Upgrade
For a practical manager like you, Michael, the decision always comes down to the return on investment (ROI). The math is surprisingly simple, and it makes the decision clear. Let's look at a basic example for one motor on your line.
Parameter | Value | Description |
---|---|---|
Motor Power (P) | 5.5 kW | A typical motor for a wrapping ring. |
Operating Hours (H) | 16 hours/day x 250 days/year | 4000 hours/year |
Average Load Reduction | 30% | The VFD allows the motor to run at a lower average speed. |
Energy Saving Factor | ~1.5 | A rough rule: a 30% speed reduction can lead to a ~45% energy saving. |
Electricity Cost (C) | $0.15 / kWh | A sample industrial rate. |
Annual Savings ≈ (P x H x Avg. Load Reduction x Factor) x C
Annual Savings ≈ (5.5 kW x 4000 h x 0.30 x 1.5) x $0.15/kWh ≈ $1,485 per year
This calculation is for a single motor. A full packaging line has several. The VFD investment often pays for itself in less than 18 months, and after that, it's pure profit. It also reduces mechanical wear, which lowers maintenance costs and extends the life of your machine—a crucial factor for reliability.
Can Optimizing the Wrapping Process Itself Save Energy?
Is your wrapping machine using more film and taking longer than necessary for each coil? This "over-wrapping" is a common problem I see on factory floors. Operators, wanting to ensure a secure package, will often add extra layers of film or use a very high overlap. This not only wastes expensive packaging material but also forces the machine to run longer for every single coil. A longer cycle time means more electricity consumed by motors, heaters, and control systems. It's a double loss that quietly eats into your profits every day. But you can fix this with smart process optimization.
Yes, optimizing the wrapping process directly saves energy. By fine-tuning parameters like film pre-stretch ratio, turntable/ring speed, and overlap settings, you can reduce cycle times. A shorter cycle means the machine's motors and heaters run for less time per coil, leading to significant cumulative energy savings without compromising packaging quality.
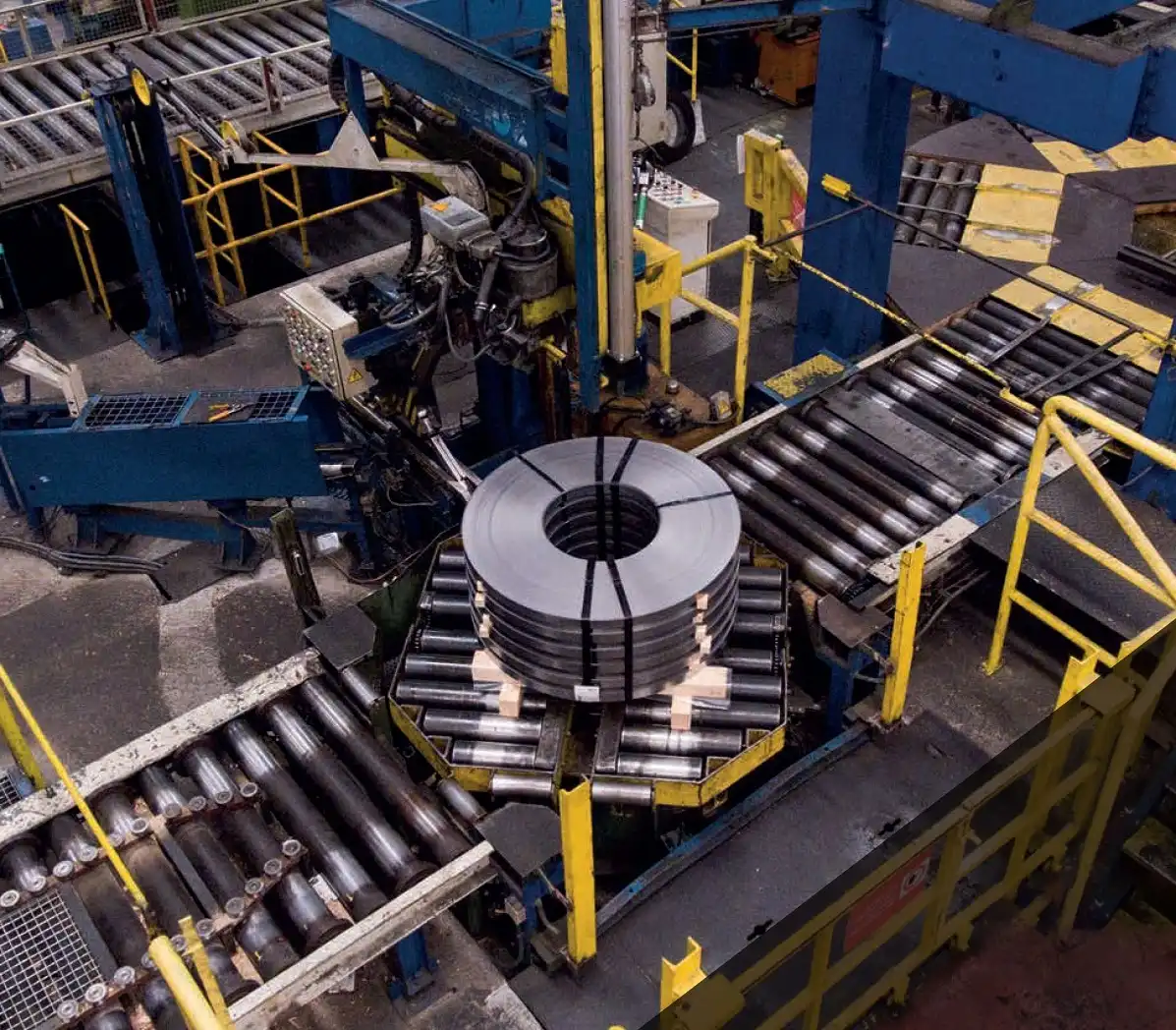
The Power of Film Pre-Stretch
This is one of the most important, yet often misunderstood, features of a modern wrapping machine. Pre-stretch is the process of stretching the wrapping film before it's applied to the coil. A good machine can stretch the film by 250% or even 300%. This means that for every 1 meter of film on the roll, you get 3.5 meters of film applied to your product. The first benefit is obvious: you save a huge amount on film costs. But the energy benefit is just as important. When the film is properly pre-stretched, it becomes thinner and easier to apply. The motors that drive the ring or turntable don't have to work as hard to pull the film and wrap the coil. This lower torque requirement translates directly into lower energy consumption. A machine with a poorly designed or disabled pre-stretch system is fighting against the film, wasting energy on every rotation.
Dialing in Your Wrapping "Recipe"
Your factory doesn't produce just one size of steel coil. You have different widths, different diameters, and different weights. So why would you use a single, one-size-fits-all wrapping setting? This is a major source of inefficiency. A setting that is perfect for a large, heavy coil will be excessive for a small, light one. It will use too much film and run for too long. Modern packaging systems allow you to create and save multiple "recipes" or programs. Your operator can simply select the program that matches the product being packaged. This ensures every single coil is wrapped with the optimal amount of film and in the shortest possible time. Taking an hour to program these recipes can save you hundreds of hours of wasted machine runtime over a year.
A Tale of Two Coils: Optimized vs. Unoptimized
Let's make this practical. Here is a direct comparison of a typical unoptimized process versus an optimized one for the same steel coil. The difference is stark.
Parameter | Unoptimized Process | Optimized Process | Impact on Efficiency and Cost |
---|---|---|---|
Film Pre-Stretch | 150% (or less) | 250% | Uses 40% less film, reduces motor strain. |
Film Overlap | 70% | 50% | Fewer wraps needed, shortening the cycle. |
Cycle Time | 90 seconds | 65 seconds | 28% less machine runtime per coil. |
Operator Action | Manual setting adjustment | Selects pre-saved program | Faster changeover, eliminates errors. |
Energy Impact | High | Low | Less runtime means direct kWh savings per coil. |
Product Protection | Inconsistent | Consistent and secure | Proper tensioning protects coil edges. |
As you can see, optimizing the process isn't just about energy. It reduces material costs, increases throughput (more coils per hour), and even improves the quality of your packaging, which helps reduce the product damage you’ve been facing. It turns your packaging line into a precision tool, not a blunt instrument.
What Role Do System Integration and Automation Play in Energy Efficiency?
Think about the gaps in your current packaging process. A coil gets wrapped, and then it sits there, waiting. It waits for an operator to notice it's done. It waits for a forklift driver to become available. While it's waiting, the wrapping machine might be idling, consuming standby power. The conveyor ahead of it is stopped. The strapper after it is waiting. These small delays and idle times add up to a huge amount of waste across a full shift. Your process is a series of "islands of automation," and this disjointed flow kills both your throughput and your energy efficiency. The solution is to connect these islands into a single, intelligent system.
System integration and automation play a critical role by creating a seamless, continuous flow that minimizes idle time and standby energy consumption. An automated line that links the wrapper with conveyors, strapping machines, and weighing stations ensures machines only run when a product is present, eliminating wasted energy between manual steps and significantly boosting overall efficiency.

The Problem with "Islands of Automation"
I see this constantly in otherwise well-run factories. You have a great slitting line, and you have a high-quality wrapping machine. But the process of moving a coil from one to the other is entirely manual. An operator has to load the coil, start the machine, wait for it to finish, and then call a forklift to move it. This stop-and-go workflow is incredibly inefficient from an energy perspective. Every time a machine starts, it draws a spike of energy. When it sits idle, it's still consuming power for its control panels, safety circuits, and standby functions. You are essentially paying for energy that is not being used to produce anything. This workflow also introduces variability. Sometimes the transfer is fast; other times, the forklift is busy elsewhere, and the line stops. You can't plan your output effectively, and you are wasting power.
Building a "Smart" and Efficient Packaging Line
Now, imagine a fully integrated line. This is the "total solution" we talk about at SHJLPACK. A steel coil comes off the slitter and moves onto an in-feed conveyor. A photo-eye sensor detects the coil and tells the conveyor to move it into the wrapping machine. The wrapping machine automatically centers the coil, performs its wrapping cycle using the correct pre-programmed recipe, and then signals the out-feed conveyor. The wrapped coil moves out, perhaps onto a weighing station or a strapping machine, while the next coil is already being moved into place. In this system, machines only run when they need to. When a machine's task is done, it can enter a low-power "sleep" mode until the next product arrives. This eliminates idle time and standby power consumption.
The Ripple Effect of Integration on Your Goals
For a manager like you, Michael, the benefits of this go far beyond just energy savings. This is how we address your key challenges head-on:
- Efficiency Bottleneck: An integrated line is designed for continuous flow. It removes the manual bottlenecks and dramatically increases your throughput (coils per hour).
- Safety Incidents: Automation removes the need for operators to manually handle heavy coils or interact closely with moving machinery. Conveyors and automated transfers are fundamentally safer than relying on forklifts in a congested area. This directly reduces the risk of injuries.
- Product Damage: A smooth, automated transfer on a conveyor system is much gentler on your products than the bumps and potential impacts from forklift handling. This helps protect the sensitive edges of your coils, reducing customer complaints and losses.
- Supplier Trust: A supplier who only talks about their one machine isn't a partner. A true partner, like us at SHJLPACK, looks at your entire process. We help you design a system that works, solving your core problems of efficiency, safety, and quality.
Why is a Proactive Maintenance Schedule Crucial for Sustained Energy Savings?
You would never drive your car for 50,000 miles without an oil change, right? You know that would damage the engine and make it run poorly. Yet, I often see factories run their packaging machines until something breaks. A worn-out bearing, a loose chain, or a dirty air filter doesn't seem like a big deal at first. But these small issues force the machine's motors to work harder, quietly consuming extra energy every single day. This neglect not only leads to higher energy bills but also guarantees an eventual breakdown, which means expensive downtime, missed shipments, and a frantic call for emergency repairs.
A proactive maintenance schedule is crucial because it ensures all machine components operate with minimal friction and resistance. Regularly lubricating bearings, tensioning belts and chains, and cleaning filters prevents the motors from working harder—and drawing more power—to overcome mechanical inefficiency. This maintains the system's original energy efficiency rating over its entire lifespan.
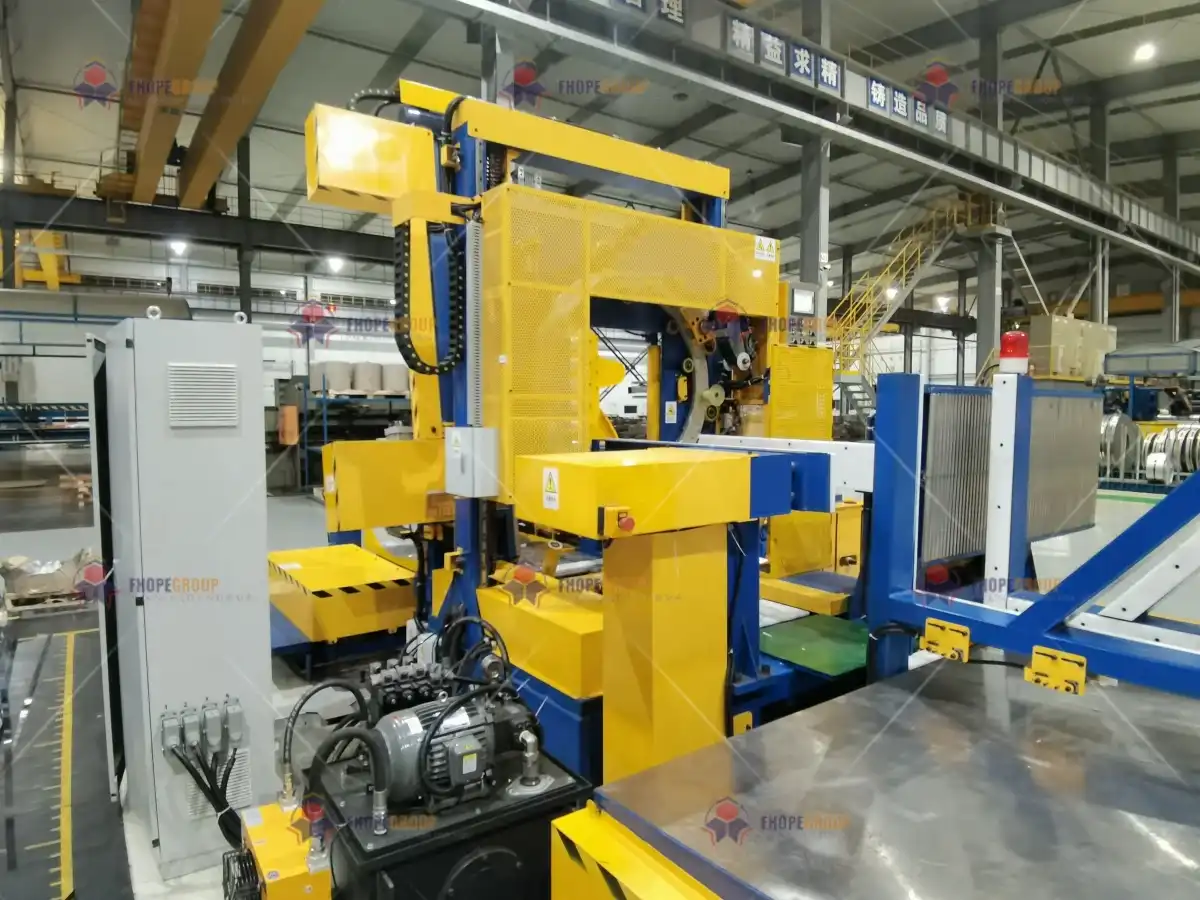
Where Energy Hides in a Poorly Maintained Machine
Energy waste from poor maintenance is insidious. It's not a sudden failure; it's a slow creep. Your operators might not even notice it, but your electricity meter does. Here are the common culprits I look for when I walk through a plant:
- Friction: Bearings and rollers that are not properly lubricated create drag. The drive motors have to overcome this extra friction, drawing more amps to do the same amount of work.
- Slippage: Belts and chains that have stretched and are no longer at the correct tension will slip. This means the motor is turning, but not all of that rotational energy is being transferred to the machine. It's pure wasted energy.
- Air Leaks: In systems that use pneumatics for clamps or cutters, compressed air is a form of energy. It's very expensive to produce. A single small leak in an airline or fitting is like leaving a window open with the air conditioning on. It's a constant, invisible drain of energy.
- Dull Blades: A dull film cutter requires more force from the pneumatic or electric actuator to make a clean cut. This extra force means more energy used on every single cycle.
From Reactive to Proactive: A Simple Checklist
Shifting from a "fix it when it breaks" mindset to a proactive one is key to reliability and efficiency. This doesn't have to be complicated. A simple, regular checklist for your maintenance team or even your lead operators can make a huge difference.
Maintenance Task | Recommended Frequency | Why it Saves Energy |
---|---|---|
Inspect and Lubricate Bearings | Monthly | Reduces rotational friction, which directly lowers the load on the motor. |
Check Belt and Chain Tension | Weekly | Prevents slippage and ensures that 100% of the motor's power is transferred efficiently. |
Clean or Replace Air Filters | Monthly | Ensures pneumatic systems operate at the correct pressure without making the compressor overwork. |
Inspect for Compressed Air Leaks | Weekly (Listen for hissing) | Stops the waste of expensive compressed air, a major energy consumer in many plants. |
Inspect and Clean Photo-Eyes | Weekly | Prevents false reads that can cause the machine to stop or cycle unnecessarily. |
Maintenance as an Investment, Not a Cost
When I built my own factory, I treated my maintenance budget as an investment in uptime and efficiency, not an expense to be cut. Every dollar spent on proactive maintenance saves three to five dollars in avoided energy waste and emergency repair costs. For a manager like you, Michael, this is crucial. A well-maintained machine is a reliable machine. It's a safe machine. And as we've seen, it's an energy-efficient machine. It delivers the consistent performance you need to control costs and meet your production targets.
What’s The One Overlooked Factor Most Managers Miss for Energy Savings?
You can have the most efficient motors with the best VFDs. You can optimize your wrapping recipes perfectly. You can have a world-class maintenance schedule. But many managers I have worked with over the years still miss the biggest potential for savings. They focus only on the hardware and the process. They see the packaging line in isolation, as a piece of equipment to be managed. This tunnel vision prevents them from seeing the single most impactful factor for sustainable savings: your people and the data they can provide.
The most overlooked factor for energy savings is often the lack of operator training combined with a failure to monitor and analyze performance data. An untrained operator can easily override efficient settings, while a lack of data makes it impossible to track consumption, identify trends, or prove the ROI of any improvements made. True efficiency comes from combining smart technology with skilled operators and data-driven decisions.
Your Operators Are Your First Line of Defense
I learned this lesson not in an office, but on the factory floor. Your operators are the ones who interact with the machine all day, every day. If they don't understand why a certain setting is important, they will often change it. I once visited a client's plant and saw that their film costs were sky-high despite having a new, high-efficiency wrapper. I watched the operator. He had turned off the pre-stretch function. When I asked him why, he said, "It makes the machine run a little faster." He was trying to improve his throughput, but he didn't realize he was doubling their film cost and making the motors work harder. He wasn't a bad employee; he was simply an untrained one. Training your team on how the machine saves energy and why the optimized settings are important is the most critical step.
"If You Can't Measure It, You Can't Improve It"
This is a core principle for any engineer or successful manager. How do you know if your changes are working? How can you justify an investment in new technology to your superiors? You need data. Many modern packaging systems can be equipped with energy monitoring. They can track key performance indicators (KPIs) that tell the real story.
- kWh per Coil: This is your ultimate energy efficiency metric.
- Coils per Hour: This tracks your throughput and the impact of cycle time reductions.
- Film/Material Used per Coil: This directly measures your material savings from optimization.
- Downtime Minutes: This helps you track reliability and the effectiveness of your maintenance program.
Without this data, you are flying blind. With this data, you can spot problems early, show your team the positive results of their efforts, and prove the ROI of your investments.
Building a Culture of Efficiency, Not Just Buying It
This is the core of our mission at SHJLPACK. We are more than a machine manufacturer; we are a knowledge-sharing platform. True, lasting efficiency doesn't come from a purchase order. It comes from building a culture of continuous improvement in your factory. This means empowering your operators with training and trust. It means giving your maintenance team the tools and time they need. And it means using data to make smart, informed decisions. When you combine great technology with a well-trained and motivated team, you create a system that is not only energy-efficient but also safer, more productive, and more profitable. That is the total solution.
Conclusion
Reducing energy consumption is not a single fix but a continuous process. By combining efficient technology, optimized processes, and diligent maintenance, you can significantly lower costs and boost your factory's profitability.