Are your production goals being held back by a slow, manual packing process? I see it all the time. Your team works hard, but they just can't keep up with the slitting machine. This bottleneck causes delays, increases labor costs, and creates serious safety risks with workers handling heavy coils. There has to be a better way to get your finished products out the door safely and on time.
A slit coil packing line automates the entire process from taking coils off the turnstile to wrapping, strapping, and stacking them for shipment. Its main advantages are a massive increase in packing speed, a significant reduction in workplace injuries, improved product protection, and lower operational costs.
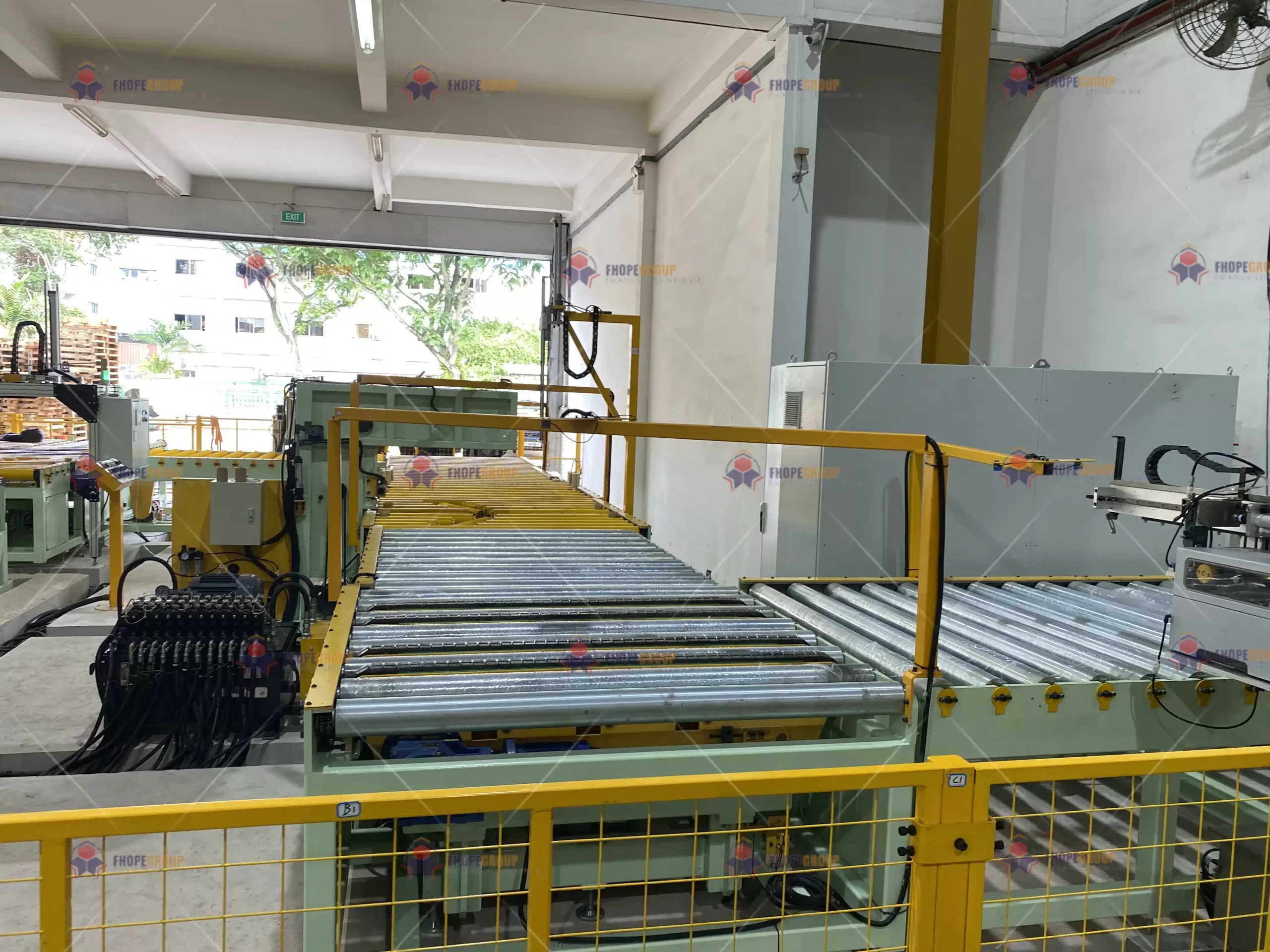
This sounds great in theory, but as a factory manager, you need to know the details. How does it actually work? And how do these advantages translate into real numbers for your business? Let's break it down together.
How Does a Slit Coil Packing Line Work, Step-by-Step?
Does the idea of integrating a new, complex system into your existing workflow seem overwhelming? You worry about disrupting production and whether your team can manage the new technology. The fear is that a new line might create more problems than it solves if it's not understood properly from the start.
A slit coil packing line works in a sequential, automated process. It typically starts with a turnstile that separates individual slit coils. A coil car then picks up a coil and transports it to the wrapping station. Here, the coil is wrapped in protective material. After wrapping, it may be moved to a stacking station where coils are palletized and strapped together for final shipment.

Understanding each stage is key to seeing how it can solve your specific bottlenecks. From my experience building and running a factory, I know that every second saved in the process adds up. Let's look at the individual steps in more detail.
From Slitter to Shipment: The Automated Journey
The entire system is designed to be a continuous flow. It minimizes waiting time and manual handling. Think of it as an extension of your slitting machine, ensuring the end of your production line moves as fast as the beginning.
-
Coil Downender/Turnstile: After the main coil is slit, the smaller "slit coils" are often on a shared mandrel. The first step is to safely separate them. A turnstile receives the coils from the slitter's exit car. It rotates to present one coil at a time to the packing line. This single step eliminates a dangerous and slow manual separation process.
-
Coil Pick-up and Transport: A mechanical coil car or an overhead C-hook automatically picks up the separated coil. It then moves it along a track to the next station. This removes the need for forklifts or manual crane operations in this tight space, which is a common area for accidents.
-
Wrapping Station: This is the heart of the line. The coil is placed on rollers and enters an orbital wrapping machine. The machine wraps the coil tightly with stretch film or VCI paper. The wrapping is consistent, providing better protection against moisture and physical damage than a person could ever achieve by hand.
-
Stacking and Palletizing: Once wrapped, the coil moves to a stacking unit. This machine safely lifts the coil and places it on a pallet. It can stack multiple coils on top of each other, creating a stable, secure pallet ready for strapping. This process is precise, preventing the edge damage that often happens when coils are stacked manually.
Manual vs. Automated: A Clear Comparison
Let's look at a side-by-side comparison. For a manager like you, Michael, seeing the direct operational change is what matters.
Process Step | Manual Method | Automated Packing Line Method |
---|---|---|
Coil Separation | Workers use pry bars and cranes. Slow and high risk of injury. | Turnstile automatically separates and presents coils. Fast and safe. |
Transport to Packing | Forklift or manual cart. Risk of dropping coils or collisions. | Coil car on a dedicated track. No human interaction needed. |
Wrapping | Two workers walk around the coil with rolls of film. Inconsistent and slow. | Orbital wrapper provides a tight, uniform wrap in seconds. |
Stacking on Pallet | Workers manually lift or use a crane to stack. High risk of back injury and coil edge damage. | Stacking unit precisely places coils. No manual lifting. |
Final Strapping | Workers use manual tensioners to strap the pallet. Variable tension. | Automatic strapping machine applies consistent, optimal tension. |
This isn't just about speed. It's about creating a predictable, reliable, and safe system that you can count on, shift after shift.
What are the Key Advantages of Automating Your Coil Packing?
You're constantly under pressure to improve your factory's numbers. You need to increase output, but your labor costs are high and you're worried about workplace accidents driving up insurance premiums. Justifying a new capital investment can be tough unless you can clearly show a strong return on investment (ROI).
The key advantages of an automated packing line are a dramatic increase in throughput, a fundamental improvement in worker safety, superior product protection that reduces damage claims, and a significant long-term reduction in labor and operational costs.

When I decided to build my own factory, every investment had to be justified with numbers. I couldn't afford equipment that didn't pay for itself. Let's look at the real-world impact of these advantages on your bottom line.
Boosting Efficiency and Throughput
Your slitting machine can produce coils much faster than a manual team can pack them. This creates a bottleneck that slows down your entire operation. An automated line is designed to match the speed of your production machinery.
- Before: A manual team of 3-4 workers might pack one slit coil every 3-5 minutes.
- After: An automated line can pack a coil in 60-90 seconds with just one operator supervising.
This means you can ship more products with the same production capacity. You fulfill orders faster, which improves customer satisfaction and allows you to take on more business.
Revolutionizing Workplace Safety
In heavy industry, safety is not just a regulation; it's a financial and moral responsibility. The manual packing of steel coils is one of the most dangerous jobs in a metal processing plant.
- The Risks: Workers are constantly lifting heavy objects, leading to back and shoulder injuries. They work near moving forklifts. Handling sharp metal edges can cause severe cuts.
- The Solution: Automation removes the human from these hazardous tasks. The machine does the lifting, moving, and wrapping. This drastically reduces the risk of injuries, which in turn lowers your insurance costs and employee turnover. A safer workplace is a more productive and stable workplace.
Calculating the Return on Investment (ROI)
As a pragmatic manager, you need to see the financial case. Let's run a simplified ROI calculation. This is the kind of analysis I did for my own factory.
Cost Category | Manual Packing (Annual Cost) | Automated Line (Annual Cost) | Annual Savings |
---|---|---|---|
Labor | 4 workers x $30,000/year = $120,000 | 1 supervisor x $40,000/year = $40,000 | $80,000 |
Injury/Insurance | High premiums, potential claims = $15,000 | Drastically reduced risk = $3,000 | $12,000 |
Product Damage | 1% of $5M revenue = $50,000 | 0.1% of $5M revenue = $5,000 | $45,000 |
Total Annual Cost | $185,000 | $48,000 | $137,000 |
If the automated line costs, for example, $200,000, your payback period would be less than 1.5 years ($200,000 / $137,000). This doesn't even include the financial benefit of increased throughput. This is the kind of clear, compelling data that justifies the investment.
How Can a Packing Line Be Customized to Fit My Factory's Specific Needs?
You've seen standard equipment that just doesn't fit your unique factory layout or product mix. You're worried about buying a "one-size-fits-all" solution that forces you to change your processes, rather than enhancing them. A generic machine that doesn't account for your specific coil sizes, weights, or floor space is a wasted investment.
A slit coil packing line is highly modular and can be customized to your exact needs. You can select specific components like different types of conveyors, wrapping machines, strapping heads, and stacking systems. The layout is also designed to fit your available floor space and connect seamlessly with your existing production flow.
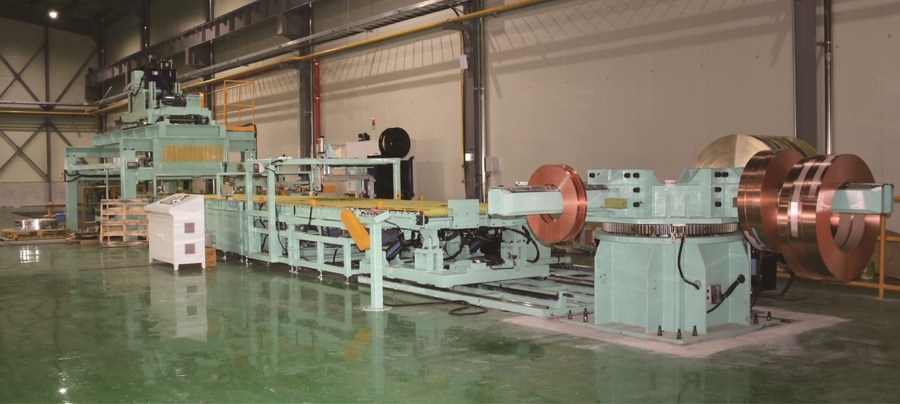
One of my first big projects as an engineer was for a client with a very old factory. The floor space was limited and full of support columns. We couldn't just drop in a standard line. We had to design a solution that worked around his limitations. This taught me that customization isn't a luxury; it's a necessity. A good partner doesn't sell you a machine, they design a solution.
Building Your Perfect Line with Modular Components
Think of it like building with LEGOs. You pick the blocks you need to create the exact system that solves your problems. A reliable supplier will work with you to analyze your requirements first.
- Your Coils: What are the dimensions? We need to know the inner diameter (ID), outer diameter (OD), width, and weight of your slit coils. This determines the size and strength of every component.
- Your Space: What is the available floor area? Are there any obstacles? The layout can be straight, L-shaped, or even U-shaped to fit your plant.
- Your Goal: What is your target packing speed? Do you need to weigh and label each coil? Do you need to stack them eye-to-sky or eye-to-wall?
Key Customization Options
Here are some of the common modules we can mix and match to build your line. Understanding these options will help you have a more productive conversation with a potential supplier.
Module | Function | Customization Considerations |
---|---|---|
Turnstile | Separates coils from the slitter | Number of arms (e.g., 2, 3, or 4 arms) based on your slitter's output speed and coil quantity. |
Coil Car | Transports coils | Can be floor-based or integrated with a downender. Load capacity must match your heaviest coils. |
Wrapping Machine | Applies protective film/paper | Ring size must accommodate your max OD. Can be equipped for stretch film, VCI paper, or both. |
Strapping Machine | Secures the coil or stack | Can perform radial (through the eye) or peripheral (around the circumference) strapping. Number of straps is programmable. |
Stacking Unit | Palletizes wrapped coils | Can use a vacuum lifter or mechanical clamp. Stacking height and pattern can be customized. |
Conveyors | Moves coils between stations | Can be chain or roller conveyors. The length and path are designed to fit your factory layout. |
Control System | Manages the entire line | Usually a PLC with a touchscreen HMI. Can be integrated with your factory's ERP system for data tracking. |
I remember a client in the steel service industry. They handled both narrow and wide slit coils. A standard line would have been inefficient. We designed a system with a wider conveyor and an adjustable wrapping ring that could efficiently handle their entire product range. This flexibility is what turns a good machine into a great investment.
What Should I Look for in a Supplier to Avoid Past Disappointments?
You've been burned before. You bought a machine from a supplier who made big promises during the sale but disappeared when you needed support. The equipment didn't perform as expected, and getting service was a nightmare. Now, you're cautious, and rightly so. Trust is hard to earn back.
To avoid disappointment, look for a supplier who is more than a salesperson. Choose a partner with deep, hands-on industry experience, like a former factory engineer or manager. They should offer comprehensive customization, provide transparent case studies, and have a proven track record of excellent after-sales support, including installation, training, and readily available spare parts.

This question is personal for me. It's the entire reason I started SHJLPACK. Before I owned my factory, I was an engineer on the factory floor. I was the one who had to deal with equipment that didn't work and suppliers who wouldn't answer my calls. I know your frustration, Michael, because I've lived it. When I finally got the chance to build my own business, I promised myself I would be the kind of partner I always wished I had.
Look for Real-World Experience, Not Just a Sales Pitch
Many equipment sellers have never worked a day in a factory. They can recite a spec sheet, but they don't understand the pressure of a production line stoppage.
- My Journey: I started as an engineer. I climbed the ladder. I eventually built and ran my own successful packing machine factory. I didn't just sell machines; I used them. I faced the same challenges you do: bottlenecks, safety concerns, and cost control. This experience is what allows me to see your problem from your perspective.
- What to Ask: When you talk to a supplier, ask them about their background. Have they solved a problem like yours before? Can they share a story about a difficult installation and how they handled it? A true expert will have stories, not just sales points.
A Partner in Problem-Solving
A good supplier doesn't start by showing you a machine. They start by asking questions. They want to understand your process, your pain points, and your goals.
- The Wrong Approach: "Here is our Model X, it's the best."
- The Right Approach: "Tell me about your current packing process. Where are the biggest delays? What are your safety concerns?"
This collaborative approach ensures the solution is tailored to you. It shows they are invested in your success, not just in making a sale. They should be willing to provide detailed layout drawings and work with your team to ensure a smooth integration.
The True Test: After-Sales Support
The relationship with your supplier truly begins after the machine is delivered. This is where many companies fail. | Key Support Areas | What a Poor Supplier Does | What a Good Partner Does |
---|---|---|---|
Installation | Ships the machine and leaves it up to you. | Sends experienced technicians to supervise installation and commissioning. | |
Training | Provides a confusing manual and says "good luck." | Provides hands-on training for your operators and maintenance staff until they are comfortable. | |
Spare Parts | Long lead times, hard to identify parts. | Maintains a stock of critical spare parts and provides clear documentation for easy ordering. | |
Troubleshooting | Unresponsive or slow to reply to technical issues. | Offers remote diagnostic support and has a clear process for service calls. |
I am building SHJLPACK as a knowledge-sharing platform for this very reason. I achieved my own success through this industry, and now I want to give back by sharing what I've learned. My goal is to help you make the right choice, whether you buy from me or not. I want to be a resource you can trust. Finding a supplier with this mindset is the key to a successful investment and a long-term partnership.
Conclusion
Automating your slit coil packing line boosts efficiency, enhances safety, and lowers costs. Find a partner with real-world experience to build a solution that truly solves your factory's specific challenges.