You’re staring at another pallet of steel coils, ready for shipment. But a familiar worry creeps in. Will they arrive at your client's facility in the same perfect condition they left yours? I’ve been there. As a factory manager, you face constant pressure to increase output and cut costs. The last thing you need is a call from an angry customer about rusted or damaged coils. This not only hurts your bottom line but also damages the reputation you've worked so hard to build. You know there has to be a better way to protect your products, a solution that doesn't just cover the coil but truly shields it from the hazards of transport and storage.
The best wrapping material for your steel coils depends on your specific needs, but a combination of VCI (Vapor Corrosion Inhibitor) paper or film for rust prevention and a durable outer layer like stretch film or woven fabric for physical protection is often the optimal solution. This multi-layer approach ensures your coils are safe from moisture, impact, and other damages during transit.

Choosing the right wrapping material is more than just a simple supply order. It's a critical decision that impacts your efficiency, your product quality, and your profitability. It's the first line of defense for your valuable steel coils. But with so many options available, from basic stretch film to advanced VCI materials, how do you know which one is right for your operation? Let's break down the most common materials. I'll share what I've learned from years on the factory floor, both running my own plant and helping clients like you find the perfect packaging solution. We'll look at the pros and cons of each, so you can make an informed choice that protects your products and your business.
Is Stretch Film the Most Cost-Effective Choice for Your Coils?
You see stretch film everywhere. It’s cheap, it's easy to get, and you probably already use it for other things in your plant. So, the question is natural: can I just use this for my steel coils and save some money? The temptation is strong, especially when you're under pressure to keep costs down. But I've seen factory managers make this choice, only to find that the initial savings disappear quickly. They start getting calls about surface rust or small dents on the coil edges from handling. The low cost of the film doesn't account for the high cost of a single rejected shipment or a lost customer.
Stretch film is a highly cost-effective material for providing basic physical protection, bundling, and stability for steel coils. It excels at containing the coil and protecting it from dust, dirt, and minor scuffs. However, it offers minimal protection against moisture and corrosion on its own, making it best used as part of a multi-layer packaging system for full protection.

Diving Deeper into Stretch Film
Stretch film, or LLDPE (Linear Low-Density Polyethylene), is fundamentally a containment material. Its main job is to hold things together tightly. Think about how it’s used to wrap pallets of boxes. It unitizes the load, preventing items from shifting. When applied to a steel coil, it does this job well. It can keep the outer wrap of the steel from unwinding and provides a decent barrier against dust and dirt in a warehouse.
The biggest issue is moisture. Standard stretch film is not a true moisture barrier. Tiny pores in the film can let water vapor pass through, and if the coil is wrapped in a humid environment, that moisture gets trapped against the steel surface. This is a perfect recipe for rust. I worked with a client in Mexico, a manager named Michael, who faced this exact problem. He was using a heavy-gauge stretch film, thinking it was enough. But his coils were often stored in a non-climate-controlled warehouse before shipping, and he was dealing with constant complaints about surface corrosion.
Another key point is puncture and tear resistance. While it seems strong, a sharp edge or a bump from a forklift tine can easily puncture or tear stretch film. For a heavy, valuable steel coil with sharp edges, this can be a major weak point. The tear can then spread, exposing a large area of the coil.
Let's break down its properties in a structured way.
Feature | Analysis for Steel Coils | Verdict |
---|---|---|
Cost | Very low initial cost per roll. Seems like a saving. | Good for budget-conscious primary wrapping. |
Containment | Excellent. Holds the coil tail down and keeps the shape tight. | Excellent for unitizing. |
Dust/Dirt Protection | Good. Creates a solid barrier against airborne particles. | Effective for clean storage. |
Moisture Protection | Poor. Not a vapor barrier. Traps humidity, which can cause rust. | Inadequate on its own. |
Puncture Resistance | Moderate to low. Vulnerable to sharp edges and impacts. | Risky for heavy coils or rough handling. |
Automation Speed | Excellent. Works very well with high-speed orbital wrapping machines. | Great for improving line efficiency. |
So, where does stretch film fit? It’s an excellent secondary layer. After you've protected the coil from corrosion with something else, you can use stretch film to add a final, tight, and cost-effective layer of containment. It works beautifully with automated wrappers, which helps solve the efficiency and safety problems that managers like Michael are trying to fix. By automating, you remove the slow, dangerous manual work and get a consistent, tight wrap every time.
When Should You Use VCI Paper or Film for Corrosion Protection?
Your steel coils leave your factory looking pristine. But somewhere between your dock and your customer's facility, a silent enemy attacks: corrosion. It starts as a small patch of rust, but it can ruin the entire coil, leading to costly rejections and angry phone calls. You've tried everything—keeping storage areas dry, shipping faster—but the risk is always there, especially during long sea voyages or storage in humid climates. You feel like you're fighting a battle against the air itself. How can you guarantee your steel arrives as clean as when it was made?
You should use VCI (Vapor Corrosion Inhibitor) paper or film whenever your steel coils are at risk of rusting due to moisture or humidity. This is essential for coils that will be shipped over long distances, stored for extended periods, or exposed to fluctuating temperatures and humid environments. VCI provides active, long-term chemical protection against corrosion.

Diving Deeper into VCI Technology
VCI technology is not just a simple barrier; it's an active form of protection. The paper or film is infused with special chemical compounds. These VCI compounds sublimate, which means they turn from a solid directly into a gas. This gas fills the enclosed space within the packaging, creating a protective, invisible molecular layer on the surface of the steel. This layer blocks the electrochemical reaction that causes rust. It’s like creating a personal, anti-rust atmosphere for your coil.
When I first started my factory, this technology was a game-changer. We were shipping coils to a client in a coastal region with very high humidity. Using just paper and stretch film wasn't working. We were facing a 5% rejection rate due to rust, which was eating into our profits. After switching to a VCI paper inner liner, our rejection rate dropped to virtually zero on the very next shipment. The extra cost of the VCI material was nothing compared to the money we saved by eliminating rejections.
Now, you have two main choices: VCI Paper and VCI Film.
VCI Paper
This is often a kraft paper coated or infused with VCI compounds.
- Pros: It's strong and has some absorbent properties. If any condensation does form, the paper can wick some of it away from the metal surface, providing a dual-action benefit. It’s also tear-resistant and provides good cushioning against minor scuffs.
- Cons: It's opaque, so you can't see the coil surface without unwrapping it. It can also be bulkier and more difficult to handle for automated machines compared to film.
VCI Film
This is a polyethylene film that has the VCI compounds embedded directly into the plastic.
- Pros: It’s often transparent, allowing for visual inspection of the coil. It is also a moisture barrier in itself, preventing liquid water from getting in. It’s flexible, easy to use with automated equipment, and can be heat-sealed to create a perfectly airtight package.
- Cons: It doesn’t have the absorbent properties of paper. If moisture is trapped inside before sealing, it will stay there.
Feature | VCI Paper | VCI Film | My Recommendation |
---|---|---|---|
Corrosion Protection | Excellent (Active + Absorbent) | Excellent (Active + Barrier) | Both are great. Film is better for airtight seals. |
Physical Protection | Good (Tear-resistant, cushioning) | Fair (Can be punctured) | Paper offers slightly better physical durability. |
Moisture Handling | Absorbs some condensation | Acts as a complete barrier | Depends on the risk. Paper handles trapped moisture better. |
Ease of Use | Can be bulky | Flexible, good for automation | Film is generally easier for high-speed automated lines. |
Inspection | Opaque | Often transparent | Film wins for easy visual checks. |
The decision between VCI paper and film often comes down to the specifics of your product and your packaging line. For heavy coils with sharp edges, a tough VCI-coated kraft paper might be better. For a fully automated line where you want a perfectly sealed, inspectable package, VCI stretch film or a VCI gusseted bag is a superior choice. For someone like Michael, who needs reliability, VCI is not a luxury; it's a necessity for ensuring product integrity and avoiding those dreaded customer complaints.
Can Woven Belts or HDPE Sheets Handle Your Toughest Coils?
You run a heavy-duty operation. Your steel coils are big, heavy, and have sharp edges. A thin layer of film just feels inadequate. You watch your team manually handle these massive coils, and every time, you worry about safety and product damage. A forklift bumps a coil, and the wrapping tears instantly, exposing the edge. A strap digs in too deep during transport, denting the product. You need a packaging solution that is as tough as the environment it works in. You need something that provides brute-force protection against the realities of a busy factory floor and a rough shipping journey.
Yes, woven fabric belts and HDPE (High-Density Polyethylene) sheets are specifically designed to handle the toughest steel coils. These materials provide superior puncture, tear, and impact resistance compared to standard films or papers. They act as a durable armor for the coil, especially protecting the vulnerable inner and outer diameters and the coil edges.

Diving Deeper into Heavy-Duty Materials
When standard materials aren't enough, you need to bring in the heavy armor. This is where materials like PP (Polypropylene) woven fabric and HDPE sheets shine. They aren't meant for corrosion protection on their own; their job is to be the tough outer shell that takes all the physical abuse.
I remember a client who manufactured high-carbon steel coils with extremely sharp, slit edges. They were using multiple layers of stretch film and cardboard, but the edges would still cut through the packaging during internal transport from the slitting line to the packaging area. Every damaged edge was a potential point of failure for their customer and a definite source of loss for them. We introduced a system that automatically applied a strip of HDPE to the outer diameter before the main wrapping process. This simple addition acted as an impenetrable shield for the edges, solving the problem completely.
Let's look at these two materials more closely.
PP Woven Fabric
This is a fabric made from interwoven polypropylene tapes. It's the same kind of material used for large bulk bags (FIBCs).
- Pros: It has incredible tear strength. Once a puncture happens, it doesn't propagate or "unzip" like a film. It's flexible and conforms well to the shape of the coil. It's also available with VCI and water-resistant coatings.
- Cons: It can be more expensive than film. Applying it manually can be slow and labor-intensive, making automation a key factor for efficiency.
HDPE Sheets
HDPE is a rigid plastic known for its high impact strength and durability.
- Pros: It offers the best protection against punctures and impacts. It's like putting a plastic shield on your coil. It’s completely waterproof. It's ideal for protecting specific, vulnerable areas like the outer/inner diameters or the sidewalls.
- Cons: It is rigid, so it doesn't conform to the entire coil surface as well as a fabric or film. It is typically used for specific parts of the coil (as ID/OD protectors) rather than as a full wrap.
Feature | PP Woven Fabric | HDPE Sheets/Plates | My Recommendation |
---|---|---|---|
Puncture/Tear Resistance | Excellent. Resists propagation. | Superior. Very hard to puncture. | HDPE is tougher, but Woven is more versatile as a wrap. |
Impact Protection | Good. Distributes impact force. | Excellent. Acts as a hard shield. | HDPE for direct impact zones. |
Flexibility | High. Conforms to the coil shape. | Low. It's a rigid material. | Woven for a full wrap, HDPE for targeted protection. |
Automation Suitability | Good. Works well with specialized wrapping machines. | Used in specific stations of a packing line. | Both can be integrated into an automated line. |
Cost | Higher than film, but justified by performance. | Cost is based on thickness and size. | The cost is an investment in preventing damage. |
For a factory manager like Michael, who is concerned about product damage during internal transit and shipping, these materials are problem-solvers. The key is not to think of it as just buying a tougher material. The key is to integrate it into a "Total Solution." An automated packaging line can apply VCI paper first, then wrap the coil with a tough PP woven fabric, and even add HDPE protectors to the edges, all without a single person having to manually lift or handle these heavy materials. This approach directly addresses the goals of increasing safety, reducing product loss, and boosting efficiency all at once.
What's My Take on Creating the Perfect Packaging Solution?
I’ve spent over 20 years in this industry. I started as an engineer on the factory floor, and later I built my own packing machine factory. I've seen firsthand what works and what doesn't. And I can tell you this: there is no single "best" wrapping material. The managers who succeed, like my client Michael is striving to, are the ones who stop looking for a magic bullet and start thinking about a complete system. They look for a partner, not just a supplier.
I remember the early days of my own factory. We were focused on the machines. A client would ask about materials, and we'd give them a generic answer. We learned a hard lesson. We sold a state-of-the-art wrapping line to a company, but they chose to use a cheap, low-grade VCI paper to save money. A few months later, they called us, frustrated that their coils were still rusting. They blamed our machine. I flew out to their plant. The machine was running perfectly, creating a beautiful, tight wrap. But the cheap paper wasn't releasing enough VCI vapor to protect the coil. They saved a few thousand dollars on material and, in return, got tens of thousands of dollars in rejected products.
My professional take is that the optimal solution is almost always a multi-layered system designed specifically for your product, your environment, and your production line. It starts with an inner layer of VCI for corrosion protection, followed by a tough outer layer like PP woven fabric or stretch film for physical protection. The true key to success is integrating these materials into an automated packaging line to ensure safety, consistency, and efficiency.
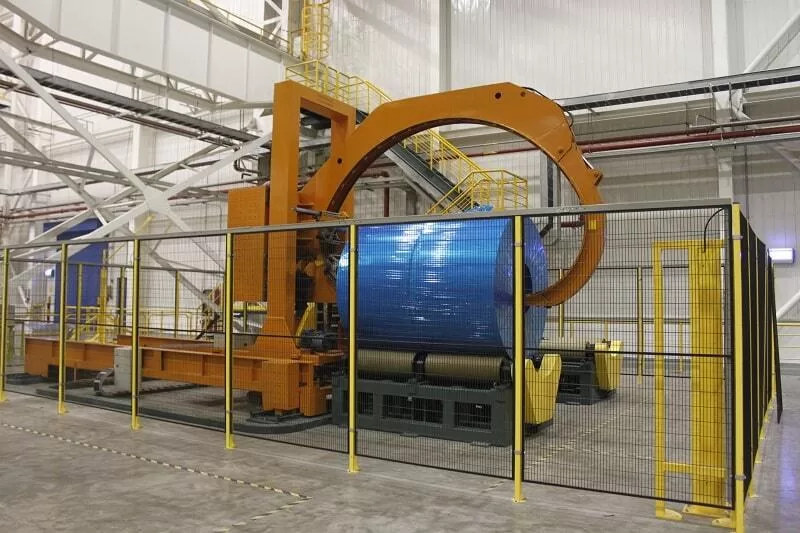
Diving Deeper: Building Your Total Solution
Thinking like an engineer, we need to design a solution, not just pick a product. A "Total Solution" considers every step and every challenge, from the moment the coil comes off the slitter to the moment your customer accepts it.
Step 1: Analyze the Core Problem
First, we must identify the biggest enemy. Is it rust? Is it physical damage? Is it a bottleneck in your workflow?
- For Rust: The non-negotiable first layer is high-quality VCI paper or VCI film. This is your active chemical shield. Don't compromise here. The cost is minimal compared to the value of the coil.
- For Physical Damage: If your coils are heavy and handled roughly, you need a tough outer layer. PP Woven Fabric is an excellent all-around choice. If you have specific problems with edge damage, integrating an HDPE protector application station into your line is the answer.
- For Efficiency & Safety: This is where the machine is critical. Manual wrapping is slow, inconsistent, and dangerous. An orbital wrapping machine can apply VCI and an outer wrap in seconds, perfectly, every time. It removes your workers from the dangerous job of handling heavy rolls of material around a massive coil. This directly addresses the safety concerns and high insurance costs that managers worry about.
Step 2: Design the Material Combination
The materials must work together. Here’s a typical high-performance combination I recommend to clients in the steel industry:
Layer | Material | Purpose | Why it Works |
---|---|---|---|
Inner Layer (1) | VCI Paper/Film | Active Corrosion Prevention | Creates a protective molecular layer on the steel. |
Outer Layer (2) | PP Woven Fabric | Puncture & Tear Resistance | Provides a tough, durable shell against physical abuse. |
(Optional) Edge Protection | HDPE Sheet/Plate | Impact Shielding | Protects the most vulnerable part of the coil from dents. |
(Optional) Final Layer | Stretch Film | Unitizing & Water Resistance | Adds a final, tight wrap to keep everything contained and clean. |
Step 3: Find a Partner, Not a Salesperson
This is the most important part. I founded SHJLPACK because I saw too many equipment suppliers who just wanted to sell a machine and walk away. They didn't understand the materials. They didn't understand the chemistry of corrosion. They didn't understand the daily pressures a factory manager faces.
You need a partner who has been in your shoes. Someone who can look at your entire process and say, "I see your bottleneck here, and I see your product risk there. Here is a complete solution—the right machine and the right combination of materials—that will solve those specific problems." A true partner helps you calculate the ROI, not just on labor savings, but on reduced product loss and improved customer satisfaction. This is how you don't just solve a problem; you create a competitive advantage.
Conclusion
Ultimately, protecting your steel coils requires a total solution. It's about combining the right anti-corrosion and physical protection materials with the right automation to ensure safety, efficiency, and quality.