Your coil packing line is the final gateway before your products reach the customer. But right now, it feels more like a traffic jam. Manual processes are slow, they are inconsistent, and they create a bottleneck that holds back your entire factory's output. Every delay at the packing station means you might miss shipping deadlines. This leads to frustrated customers and mounting pressure from management. You see your production teams working hard, only to be held back by an inefficient end-of-line process. It's a constant source of stress. But you can transform that bottleneck into a smooth, fast-flowing exit. By focusing on specific, targeted optimizations, you can significantly increase your packing throughput, often with less effort than you might think.
To optimize throughput on coil packing lines, Indian technicians should first conduct a thorough bottleneck analysis. Then, they need to strategically implement automation for wrapping and handling. It is also key to streamline material flow with integrated conveyance systems and ensure proper operator training and machine maintenance.

I have been in your shoes. I built my own packing machine factory from the ground up, and I know the pressure to get more products out the door every single day. I learned that it is not just about buying a new machine. It is about a smart, step-by-step approach to finding and fixing the real problem. This is how you build a system that works for you, not against you. Let's break down exactly how you can apply this thinking in your own facility.
Where Should You Start Looking for Bottlenecks in Your Packing Line?
You know your packing line is slow, but you are not sure exactly where the biggest problem is. Is it the wrapping machine itself? The strapping process? The labeling? Or is it the way the coils get to the station in the first place? Guessing is an expensive strategy. If you invest in a new, faster wrapper when the real issue is how you load the coils, you waste time and money, and the core problem remains. You feel stuck, constantly putting out fires without a clear strategy for improvement. The solution is to use a systematic approach. By breaking down the packing process into individual stages and measuring each one, you can pinpoint the exact source of your delay. This allows you to focus your efforts where they will have the biggest impact.
Start looking for bottlenecks by mapping your entire packing process, from the moment a coil arrives at the station to its final dispatch. Use a simple stopwatch to time each individual step: loading, wrapping, strapping, weighing, labeling, and unloading. The step that consistently takes the longest, or has the most idle time associated with it, is your primary bottleneck.
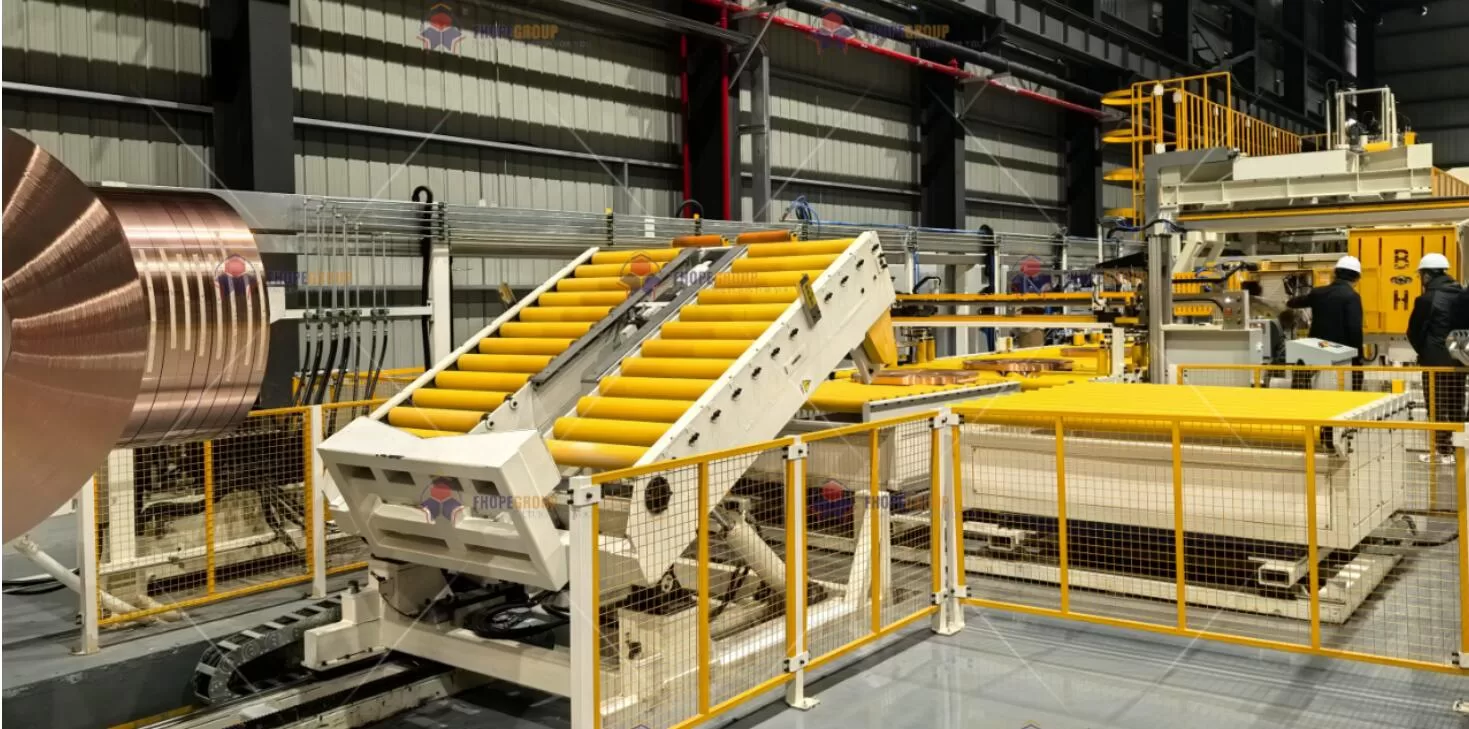
Breaking Down the Full Packing Cycle
To find the problem, you must first see the whole picture. Don't just look at the wrapping machine. Look at every single action that has to happen. I always advise managers to get a clipboard and a stopwatch and stand by the line. Write down every step. It usually looks something like this: Coil arrives via crane or forklift, it is positioned, it is lifted onto the machine, the machine wraps it, it is strapped, it is weighed, a label is applied, and then it is removed by a forklift. Each of these is a separate event. You need to know how long each one takes. When I did this in my own factory, I was shocked. I thought my machine was the slow part, but it turned out the time spent waiting for the crane to bring the next coil was almost double the wrapping time. The machine was idle more than it was working. That is where the real bottleneck was hiding.
Simple Tools for a Powerful Analysis
You do not need expensive software or consultants to do this. A technician with a stopwatch and a basic spreadsheet can uncover huge opportunities for improvement. Create a simple table. List each step of the process in a column. In the next column, record the time it takes to complete that step. Do this for 10 or 20 coils to get a good average. A third column should be for "wait time." This is crucial. How long does the coil sit waiting for the next step to begin? How long does the wrapping machine sit idle waiting for the next coil? This "wait time" is pure waste, and it is often the biggest bottleneck of all. It represents lost throughput that you can reclaim without even buying a new machine.
The "Wait Time" Trap and What It Costs You
The slowest active process is not always the main bottleneck. The longest inactive period, or "wait time," is frequently the true culprit. For example, if your wrap cycle is 60 seconds but it takes an average of 90 seconds to remove the finished coil and load the next one, your real cycle time is 150 seconds. Your expensive machine is being starved. Your throughput is dictated by material handling, not the wrapper's speed. This is a common trap. Below is a simple table showing how to identify the issue.
Process Step | Manual Handling Time (Seconds) | Optimized Handling Time (Seconds) | Analysis |
---|---|---|---|
Wait for Coil | 45 | 5 | Bottleneck in old system. |
Load Coil onto Machine | 30 | 10 | Significant improvement. |
Wrap Cycle | 60 | 60 | Machine speed is the same. |
Strapping & Labeling | 25 | 25 | No change in this step. |
Unload Coil | 35 | 10 | Faster and safer removal. |
TOTAL CYCLE TIME | 195 | 110 | Throughput increased by 77%. |
As you can see, by focusing on the wait time and handling, the overall throughput is dramatically improved, even though the machine's wrapping speed did not change at all.
What Level of Automation is Right for Your Coil Packing Operation?
The word "automation" can be intimidating. It often sounds expensive and complex. You might not be sure if you need a fully robotic line or just a better, more efficient wrapping machine. I understand this concern. Choosing the wrong level of automation can be a disaster for your operations and your budget. If you over-automate, you can end up with high capital costs and maintenance headaches for a system you do not fully need. On the other hand, if you under-automate, you have spent money but have not truly solved your core efficiency and safety problems. The key is to carefully match the automation level to your specific needs. You must consider your throughput goals, your budget, and the skills of your team. It is about finding the "sweet spot" that gives you the best and quickest return on your investment.
The right level of automation for your coil packing depends on your production volume, the variety of your coil sizes, and your budget. For lower volumes or high product variation, a semi-automatic orbital wrapper is a huge upgrade. For high-volume, standardized production, a fully automatic line with integrated conveyors, strapping, and weighing systems will provide the best throughput and return on investment (ROI).
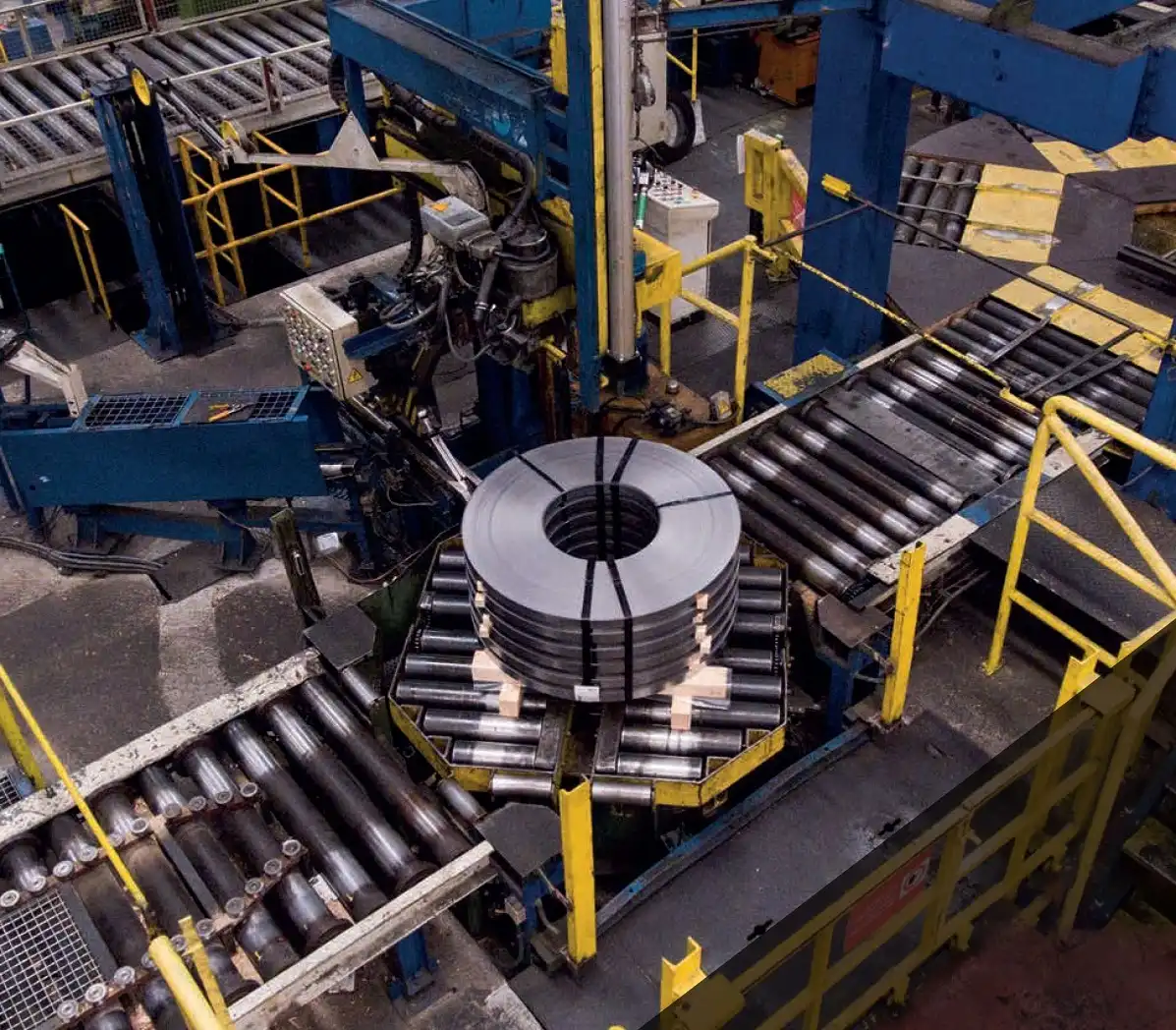
Level 1: Semi-Automatic Solutions
This is the perfect starting point for many factories. If you are currently wrapping coils by hand, a semi-automatic machine will feel like a revolution. Think about a factory that produces a moderate number of coils per day, but the sizes and weights vary a lot. A semi-automatic wrapper is ideal here. The operator loads the coil onto the machine, often with a simple jib crane or forklift. They start the wrap cycle with a push of a button, and the machine does the wrapping consistently and tightly every time. The operator then cuts the film and unloads the coil. The benefits are immediate: wrapping is much faster, the packaging quality is uniform, material consumption is reduced, and most importantly, it is much safer for the operator than walking around a heavy coil with a roll of stretch film. The initial investment is lower, making it an accessible first step into automation with a very fast ROI.
Level 2: The Automatic Wrapping Station
This is the next logical step up and a very popular choice for medium-to-high volume operations. In this setup, the wrapping machine itself is fully automatic. It automatically senses the coil, feeds the packing material, wraps it according to a pre-set program, and then clamps, cuts, and seals the material on its own. The operator's main job becomes loading the coil onto the machine's infeed section and removing it from the outfeed section. This frees up the operator to prepare the next coil or handle labeling while the machine is working. This level of automation significantly boosts throughput because it removes the manual steps directly associated with the wrapping cycle. It creates a more predictable and rhythmic pace for the entire packing line. I've helped many clients transition to this level, and they often see their output per operator double.
Level 3: The Fully Integrated Packing Line
This is the ultimate solution for high-throughput factories where the packing line must keep pace with a fast production line. Here, we are not just talking about a single machine; we are talking about a complete, connected system. Coils arrive on an automated conveyor. An upender or tilter orients the coil correctly for wrapping without any manual intervention. The coil then moves into the automatic wrapping station. After wrapping, it continues on another conveyor to an automatic strapping machine, then to an in-line weighing and labeling system. Finally, it can be moved to a palletizing area or an exit conveyor for pickup. This system requires minimal human interaction, which maximizes both speed and safety. It is a larger investment, but for a factory producing hundreds of coils per shift, the ROI is clear and compelling. It solves the throughput problem permanently.
Automation Level | Labor Requirement | Throughput Capacity | Initial Cost | Best For... |
---|---|---|---|---|
Level 1: Semi-Automatic | 1 Operator (Active) | Low to Medium | Low | Factories transitioning from manual wrapping; high product variety. |
Level 2: Automatic Station | 1 Operator (Supervisory) | Medium to High | Medium | Dedicated packing lines needing consistent, higher speed. |
Level 3: Integrated Line | 0-1 Supervisor | Very High | High | High-volume production facilities needing maximum efficiency and safety. |
How Does Inefficient Material Handling Cripple Your Packing Throughput?
Imagine this scenario: you have invested in a fast, modern wrapping machine that can wrap a coil in under a minute. But your overall output is still disappointingly slow. You watch the line and notice that your new, high-speed machine often sits idle. It is either waiting for the next coil to be slowly brought over and positioned by an overhead crane, or it is waiting for a wrapped coil to be carefully moved away by a forklift. This is an incredibly frustrating situation. You invested in a high-speed machine, but your throughput is being strangled by what happens before and after the wrap cycle. It feels like owning a race car but being forced to drive it in city traffic. This stop-and-go inefficiency also dramatically increases the risk of product damage from clamps and forks, and it raises the potential for serious worker injury. The solution is to think of the packing line as a complete system, not just an individual machine. By integrating efficient and safe material handling, like conveyors and tilters, you can create a continuous flow that allows your wrapping machine to run at its full potential.
Inefficient material handling cripples throughput by starving your packing machine. When operators use cranes or forklifts to load and unload each individual coil, it creates significant "wait time" where the machine is idle. This stop-and-go process is the single biggest barrier to achieving a smooth, continuous, and high-speed packing operation.
The True Cost of "Stop-and-Go" Operations
The problem with using cranes and forklifts for material handling at the packing station goes far beyond the obvious slowness. There are hidden costs that many managers overlook. First is the machine idle time. Every minute your wrapper is waiting for a coil is a minute of lost production that you can never get back. Second is the cost of labor. You are paying one or two operators to be handlers, not producers. Their time is spent waiting on equipment and performing slow, repetitive movements. Third, and very important for steel and wire coils, is the risk of product damage. The edges of steel coils are very sensitive. Every time a forklift tine or a crane clamp touches the coil, there is a chance of dents, scratches, or deformation. This leads to customer complaints and rejected products. Finally, there is the immense safety risk. Maneuvering heavy, suspended loads in a busy area is one of the most dangerous jobs in a factory. An integrated system removes almost all of these risks.
Creating Continuous Flow with Conveyor Systems
The goal is to create a seamless flow of product through the packing station. The most effective way to do this is with conveyors. Imagine an infeed conveyor where an operator can stage three or four coils at a time. As soon as the wrapper finishes one coil, the next one is automatically moved into position. There is no waiting. The wrapper immediately starts its next cycle. While it is wrapping, the finished coil is moved onto an outfeed conveyor, ready for pickup. This creates a buffer on both ends of the machine, ensuring it can run continuously without interruption. I have seen factories double their throughput with this change alone. Different types of conveyors, like heavy-duty roller or chain conveyors, can be used depending on the weight and size of your coils. The principle is the same: keep the machine fed to keep it productive.
The Essential Role of Upenders and Tilters
For many products, especially steel coils that are stored with the core vertical (eye to the sky), they need to be turned on their side for wrapping. Doing this with a crane and slings is slow, unstable, and extremely dangerous. A hydraulic or mechanical upender (also called a tilter) solves this problem perfectly. The coil is placed on the upender, and with the push of a button, it is smoothly and safely tilted 90 degrees and placed directly onto the infeed conveyor. This one piece of equipment can eliminate one of the slowest and most hazardous steps in the entire packing process. It is a critical link in creating a truly automated and efficient material handling system.
Handling Method | Cycle Time Impact | Labor Intensity | Safety Risk | Product Damage Risk |
---|---|---|---|---|
Crane / Forklift | High (Stop-and-Go) | High (2+ Operators) | Very High | High |
Integrated Conveyors | Low (Continuous Flow) | Low (1 Supervisor) | Very Low | Minimal |
What is the Single Biggest Mistake Factories Make When Trying to Boost Throughput?
Over the years, I have talked to hundreds of factory managers and engineers. So many of them are focused on one number: the wrapping machine's RPM or its cycles per hour. They have been led to believe that buying the "fastest" machine on the market will automatically solve all their throughput problems. I have seen this happen time and again. A factory invests a significant amount of capital in a top-of-the-line, high-speed wrapper. They install it, and everyone is excited. But a month later, they check their numbers, and the overall output of finished goods per shift has barely improved. They spent a lot of money, but the bottleneck has simply moved somewhere else in the line. They focused on a single tool, not on the entire process. It is a costly and deeply demoralizing mistake. The biggest gains come not from focusing on machine speed alone, but from looking at the entire system. As I learned from painful experience when building my own factory, true optimization comes from balancing every step of the process to create a smooth, uninterrupted flow.
The single biggest mistake is focusing only on the wrapping machine's speed while ignoring the processes that happen before and after it. True throughput optimization comes from system integration—ensuring that coil loading, handling, strapping, and unloading can all keep pace with the wrapper to create a balanced, continuous line with zero idle time.
My Own Hard-Learned Lesson
When I first started my own factory, I made this exact mistake. I was young and I believed the spec sheets. I saved up and bought the fastest, most advanced packing machine I could possibly afford. I was proud of it. I showed the technical data to everyone. But when we installed it on the factory floor, the reality was very different. The machine was constantly waiting. It would finish a wrap cycle in 45 seconds and then sit idle for two minutes. It was waiting for a busy crane to bring the next steel coil. It was waiting for a forklift driver to finish another task and clear the finished pallet. My machine was fast, but my line was slow. It was a painful and expensive lesson that taught me the critical difference between a machine's theoretical capacity and a system's actual throughput. I learned that you don't ship spec sheets to customers; you ship finished products.
A Simple Rule: A Chain is Only as Strong as its Weakest Link
This is a simple saying, but it is the most important principle in manufacturing. It is called the Theory of Constraints. In a packing line, your total output is not determined by your fastest machine. It is determined by your slowest process—your bottleneck. If your wrapper can pack 60 coils an hour, but your forklift can only deliver 30 coils an hour to the machine, your line's maximum throughput is 30 coils per hour. Period. Spending more money to make the wrapper faster (say, to 80 coils an hour) will have zero effect on your total output. You have strengthened a link that was already strong. To improve the whole system, you must identify and strengthen the weakest link. In this case, that means fixing the material handling process.
A Balanced Line Always Beats a "Fast Machine"
The goal should not be to have the fastest machine. The goal should be to have the most balanced line, where every step is synchronized with the others to create a continuous, smooth flow. A slower, less expensive wrapper that runs without stopping will always produce more than a super-fast machine that is constantly waiting. A true partner and solution provider—which is what we strive to be at SHJLPACK—will help you analyze your entire system. We don't want to just sell you a machine. We want to help you find and fix your bottleneck, because that is what will actually help you grow your business. That is how I grew my own.
Metric | "Fast Machine" Focus | Balanced Line Focus |
---|---|---|
Primary Goal | Maximize the wrapper's RPM. | Maximize finished, shipped coils per hour. |
Investment Strategy | Buy the fastest possible wrapper. | Invest in fixing the bottleneck (which might be conveyors, a tilter, or a slower wrapper). |
Operational Result | The wrapper is often idle; the bottleneck just moves somewhere else. | Smooth, continuous flow; the entire line's output increases significantly. |
Return on Investment (ROI) | Often low and disappointing. | High and predictable. |
Conclusion
Optimizing your coil packing line is a journey of systematic improvement. Identify bottlenecks, choose the right automation, and integrate material handling to create a truly efficient, safe, and profitable operation.