Running a steel or metal processing factory in India comes with a unique set of pressures. You are constantly pushing for higher output. At the same time, you have to manage rising labor costs and ensure your workplace is safe. I've seen many factory managers struggle with their end-of-line packing. It’s often a manual, slow process that creates a major bottleneck for the entire operation. This inefficiency doesn't just slow down deliveries. It leads to damaged products, unhappy customers, and a constant risk of serious injury to your workers, which eats away at your profits. You know automation is the answer, but the big question is, which machine will actually pay for itself and start making you money?
The best coil packing line for an Indian factory is one that directly matches your specific needs in terms of production volume, coil dimensions, and desired level of automation. For high ROI, this often means choosing between a robust semi-automatic horizontal orbital wrapper for smaller mills or a fully integrated automatic packing line for high-throughput operations. The key is to find a solution that tackles your biggest costs—labor, product damage, and downtime—head-on.
Choosing the right machine is about more than just comparing price tags. A cheap machine that breaks down constantly or doesn't solve your core problems is a terrible investment. The real value, the true ROI, comes from understanding the long-term impact on your entire operation. It's about finding a partner who can help you analyze your needs and provide a solution that grows with your business. Let's break down how to find the perfect fit for your factory and maximize your return.
How Do You Calculate the Real ROI of a Coil Packing Line?
You're looking at a brochure for a new packing machine, and you see the price. It’s a big number. Your first thought is, "Can we afford this?" But the more important question is, "Will this investment actually pay off?" It’s easy to get stuck on the initial cost. You worry about spending capital without a clear and predictable return, making it difficult to get approval from your finance department or board. I want to show you how to look past the price tag. Let's calculate the real ROI by uncovering all the ways a new line will save and make you money.
To calculate the real ROI, you must look beyond the initial purchase price. The true calculation includes tangible savings like reduced labor costs, faster throughput, and lower packing material consumption. It also includes "hidden" gains from eliminating product damage, preventing worker injuries, and improving customer satisfaction. A simple formula is: (Total Gains - Investment Cost) / Investment Cost = ROI.
The initial cost is just one piece of the puzzle. A true ROI calculation tells a much bigger story about your factory's future profitability. It helps you justify the investment not as an expense, but as a strategic move to make your entire operation stronger, safer, and more efficient. Let’s dive deeper into what you should be measuring.
The Tangible Cost Savings
These are the numbers you can easily track and present to your management team. The most obvious saving is in labor. Let's say you currently have a team of four workers manually packing coils. They work an 8-hour shift, and your factory runs two shifts a day. An automatic line might only require one operator per shift to supervise the process. You can immediately see the reduction in labor costs. But it doesn't stop there. An automated wrapper uses packing material more efficiently than manual wrapping, reducing waste and lowering your consumable costs. Throughput is another huge factor. If your manual team packs 10 coils per hour and an automated line packs 30, you've tripled your end-of-line capacity. This means you can ship more products every day with the same or fewer people, directly boosting your revenue potential.
Metric | Manual Packing Process | Automated Packing Line | Tangible Savings |
---|---|---|---|
Workers per Shift | 4 Workers | 1 Supervisor | 3 fewer workers per shift |
Coils Packed per Hour | 10 Coils | 30 Coils | 200% increase in throughput |
Packing Material Waste | ~15% (uneven application) | ~2% (precise control) | ~13% reduction in material cost |
Time per Coil | 10-15 minutes | 1-2 minutes | Up to 90% time reduction |
The "Hidden" Gains That Boost Your Bottom Line
These benefits are harder to put on a spreadsheet, but they have a massive impact on your profitability. Think about product damage. A coil with a damaged edge from rough manual handling might have to be scrapped or sold at a discount. Even worse, it could be rejected by a customer, damaging your reputation. An automated line provides a consistent, protective wrap that virtually eliminates this kind of damage. Then there's safety. I've visited too many factories where workers risk back injuries lifting heavy packing materials or using manual strapping tools. A single serious injury can lead to huge worker compensation claims, increased insurance premiums, and low morale. Automation removes your workers from these dangerous tasks. This improved safety and product quality has a ripple effect. Your customers become more confident in your reliability, your employees are safer and more productive, and your brand reputation grows stronger.
The Indian Market Context
When calculating ROI for a factory in India, we must consider local factors. Labor costs in India are rising. Relying on manual labor is becoming a less sustainable strategy each year. Furthermore, the 'Make in India' initiative encourages manufacturing excellence. Competing on the global stage requires world-class efficiency and quality, which automation provides. Power supply can also be inconsistent in some industrial areas. So, choosing a machine with components that can handle voltage fluctuations is critical for avoiding downtime. The right supplier will understand these local challenges and recommend a machine built to withstand the demanding Indian industrial environment, ensuring your ROI isn't compromised by unexpected operational issues.
Which Entry-Level Automatic Machine is Best for Small to Medium Indian Steel Mills?
If you run a small or medium-sized mill, you might look at the giant, fully automated packing lines and think, "That's not for me." You see the complexity and assume the cost is far out of reach. This feeling leaves you stuck with the old ways: slow, labor-intensive manual packing that limits your growth. You watch larger competitors with more automation pull ahead, and you worry about being left behind. But I'm here to tell you that automation is not just for the giants. There is a practical, affordable starting point that can deliver a fantastic ROI without a massive initial investment.
For most small to medium Indian steel mills, the best entry-level machine is a semi-automatic horizontal orbital wrapper. This machine offers the perfect balance of automation and affordability. It dramatically increases packing speed and product protection while keeping the initial investment and operational complexity low, making it an ideal first step into automation.
This type of machine is a game-changer because it targets the most time-consuming and inconsistent part of the packing process—the wrapping itself. It allows a small team to achieve a level of speed and quality that would be impossible by hand. Let's look at why this is such a smart move for a growing mill.
The Semi-Automatic Orbital Wrapper Explained
So, what does "semi-automatic" mean? It means the machine handles the hard part, and your operator handles the simple parts. Your worker will typically load the steel coil onto the machine's infeed conveyor, often with the help of a C-hook or forklift. Once the coil is in position, the operator pushes a button. The machine then automatically feeds the packing material (like stretch film or VCI paper) and the wrapping ring orbits around the coil, applying a tight, even, and protective layer. After the wrapping is complete, the operator cuts the film and moves the finished coil to the dispatch area. The machine automates the slow, repetitive, and physically demanding task of wrapping, while your worker handles the straightforward loading and unloading. This simple division of labor is what makes it so efficient and cost-effective.
Key Features for the Indian Context
When I help a client in India choose a semi-automatic wrapper, I tell them to look beyond the basic function. Durability is everything. The machine needs to be a workhorse. Look for heavy-duty steel construction and high-quality components like a solid, well-engineered wrapping ring and durable conveyor rollers. The control panel should be simple and intuitive. Your operators should be able to learn it quickly without needing an engineering degree. I always recommend machines with PLCs from globally recognized brands like Siemens or Allen-Bradley. Why? Because getting service and spare parts is much easier, even in more remote industrial areas. A machine is useless if you can't get a replacement sensor quickly. A good supplier will have considered this and built a machine that is not only tough but also easy to maintain in local conditions.
A Real-World Example
I remember working with a medium-sized wire coil producer in Gujarat. They had a team of six people per shift just for packing. It was a bottleneck, and they were experiencing damage complaints from their customers. They invested in a semi-automatic orbital wrapper from us. The results were immediate. They reassigned four of the six packing workers to other productive areas of the factory. The packing time for a single coil dropped from over 10 minutes to just under 90 seconds. Their customer complaints about transport damage dropped to zero within three months because the machine wrap was so much more secure than their manual efforts. They calculated that the machine paid for itself in just 14 months through labor savings and eliminated product losses alone. This is the power of starting with the right piece of automation.
What Features Are Critical for a High-Throughput Coil Packing Line in India?
Your factory is big. You are producing a high volume of steel coils or wire every single day. But your finished products are piling up, waiting to be packed. Your packing station has become the single biggest bottleneck in your entire plant, restricting your overall output. This slowdown causes a chain reaction of problems: it creates storage chaos, delays shipments to important clients, and causes frustration for your entire production team. You know you need a fully automatic solution, but you need to be sure it has the right features to not just keep up, but to push your capacity even further.
For a high-throughput factory in India, a packing line's critical features go beyond just wrapping speed. You need a fully integrated system with automatic coil loading and unloading, an upender or tilter for orientation, integrated weighing and labeling, and a robust PLC control system. These features work together to create a seamless, hands-free process that maximizes speed and reliability.
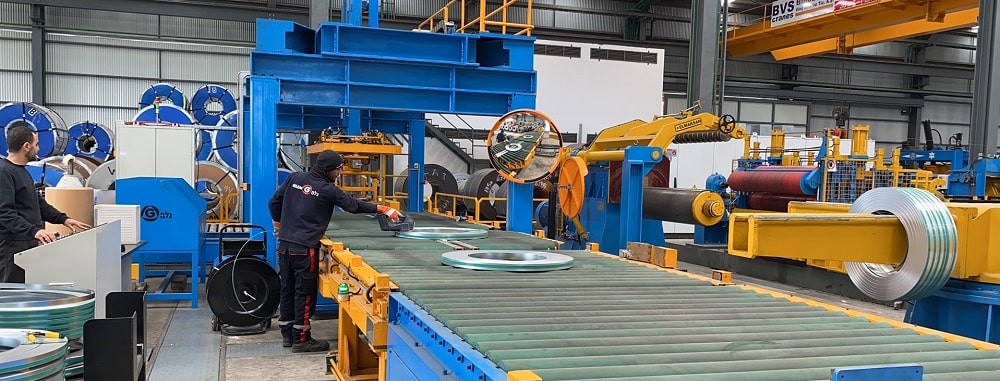
In a high-volume environment, every second counts. You can't afford to have a fast wrapper that is waiting for coils to be manually loaded. A true high-throughput solution is a complete system, not just a single machine. It's an investment in uninterrupted flow.
From a Single Machine to a Complete System
A high-throughput line isn't just a wrapper; it's a series of machines working in perfect sync. The process typically starts with a heavy-duty conveyor that receives the coil directly from your production line. If the coil is in an "eye-to-sky" position, a coil tilter (or upender) will safely and automatically turn it 90 degrees to an "eye-to-side" position for wrapping. After passing through the orbital wrapper, the line might include an automatic strapping station for added security. Then, it moves to an integrated weigh-scale and a print-and-apply labeling system that puts all the necessary tracking information on the package. Finally, conveyors move the fully packed and labeled coil to an accumulation area, ready for pickup by a forklift. Each component is designed to eliminate manual intervention and hand off the coil smoothly to the next station.
Automation Features That Truly Matter
The "brain" of this entire system is the Programmable Logic Controller (PLC). A powerful PLC, like a Siemens S7-1200 or higher, is essential. It allows you to store "recipes" for different coil sizes and packing requirements. Your operator can simply select the product code, and the entire line—conveyors, wrapper, strapper—will automatically adjust its settings. This is crucial in a factory that produces a variety of products. Another critical feature is automatic material management. The system should be able to sense when a roll of stretch film is running low and alert the operator. The best systems even feature automatic film cutting and clamping, so there is zero operator action needed between cycles. For true factory integration, the packing line's PLC should be able to communicate with your factory's Manufacturing Execution System (MES) or ERP software. This allows for real-time data tracking, production monitoring, and inventory management.
Designing for the Realities of an Indian Factory
A high-throughput line in India must be tough. I design systems for my clients with the assumption that they will run 24/7 in a hot, dusty environment. This means using sealed bearings, protecting sensitive electronics in air-conditioned cabinets, and using robust motors that can handle potential power surges. The user interface on the HMI (Human-Machine Interface) screen should be intuitive, with clear graphics and the option for local languages to make operator training easier. We also need to consider the variability of packing materials sourced locally. The machine must have the flexibility to work effectively with slight variations in the thickness or tackiness of the stretch film. A rigid system designed in a lab won't survive long on the factory floor. It needs to be a resilient, adaptable workhorse.
How Can the Right Packing Line Reduce Hidden Costs like Product Damage and Worker Injury?
As a factory manager, you are an expert at tracking direct costs like labor, materials, and energy. But what about the hidden costs? These are the expenses that don't always show up clearly on a P&L statement but can quietly drain your profits. I’m talking about the cost of a shipment rejected due to damaged coil edges, or the massive financial and human cost of a serious worker injury. These incidents create huge financial liabilities and damage your company's reputation. You know these problems exist, but the solution might be more direct than you think. The right machine design can act as a powerful form of insurance against these expensive, hidden risks.
A well-designed packing line directly reduces hidden costs by engineering safety and product protection into the process. Automated features like coil tilters and conveyors eliminate dangerous manual lifting and handling, drastically cutting the risk of worker injury. At the same time, the precise, consistent tension of an orbital wrapper creates a protective cocoon around the product, preventing the edge damage that occurs during manual strapping and transport.
Investing in the right automation is not just an efficiency play; it's a proactive strategy to de-risk your entire operation. By removing the two biggest variables—human error and manual strain—you solve the root cause of these hidden costs.
The Safety Equation: Removing the Human Risk Factor
Let's be direct about the dangers of manual packing. Your workers are repeatedly lifting heavy rolls of packing material. They use manual tensioners for steel strapping, a task that can lead to repetitive strain injuries or dangerous strap snap-backs. The most hazardous task is often turning or handling the coils themselves. A moment's inattention while using a crane or forklift can lead to a catastrophic accident. An automated packing line systematically eliminates these high-risk touchpoints.
Manual Task | Associated Risk | Automated Solution |
---|---|---|
Lifting Material | Back strain, muscle pulls | Machine feeds material automatically |
Manual Strapping | Repetitive strain, strap lash-back | Automated strapping/wrapping |
Handling Coils | Crushing injuries, falls | Automated conveyors and tilters |
Working Near Moving Coils | Slips, trips, impact injuries | Safety fences and light curtains |
The automated line creates a controlled environment. Safety fences, light curtains, and emergency stops are standard. The machine does the heavy, dangerous work, and the operator becomes a supervisor, monitoring the process from a safe distance. This fundamentally changes the safety equation in your factory.
Protecting Your Product is Protecting Your Profit
Every time a coil is handled manually, it's at risk. A slight bump from a forklift tine can dent the edges. Straps applied too tightly can cut into the product. Inconsistent wrapping can leave areas exposed to moisture and corrosion during shipping and storage. These small damages add up to big losses. An orbital wrapper solves this. It applies stretch film with perfectly calibrated tension, creating a tight, uniform layer that absorbs impacts and seals out the elements. The wrap provides a full "cocoon" of protection, covering the vulnerable edges and faces of the coil completely. This level of consistent, high-quality packaging is simply not achievable by hand. The result? Fewer customer complaints, no rejected shipments, and a stronger reputation for delivering quality products every time.
The Long-Term Ripple Effect
The benefits of improved safety and quality extend far beyond a single prevented accident or saved coil. When your workplace is demonstrably safer, you attract and retain better employees. Your insurance premiums may decrease as your incident rate drops. Your sales team can confidently promise customers that products will arrive in perfect condition, which can be a powerful competitive advantage. When you reduce the hidden costs of damage and danger, you aren't just saving money. You are building a more resilient, reputable, and profitable business for the long term.
My Insights: Why a 'Total Solution' Approach Beats Buying Just a Machine?
Over the years, I’ve heard the same story from many factory managers. They bought a machine from a supplier who promised them the world. The salesperson was great, the price was good. But after the machine was delivered, the supplier disappeared. They were left with a piece of equipment that didn't quite fit their process, with a manual they couldn't understand, and no one to call when things went wrong. This experience makes you cautious, and it should. You're worried about making another expensive mistake and being left to solve complex integration and maintenance problems on your own. I know this feeling because I've been there. When I was building my own packing machine factory, I learned that success isn't about the machine itself. It's about the partnership and the expertise behind it.
A 'total solution' approach means you are not just buying a machine; you are gaining a partner who understands your entire operation, from the moment a coil comes off the line to the moment it's loaded on a truck. This partner helps with process analysis, layout design, integration, training, and long-term support. This comprehensive approach is the only way to guarantee the machine truly solves your core problems and delivers the maximum possible ROI.
Anyone can sell you a machine. A true partner helps you build a better business. They take the time to walk your factory floor, understand your bottlenecks, and talk to your operators. This is a fundamentally different approach from a "box-dropper" supplier who just wants to make a quick sale.
What a 'Total Solution' Really Looks Like
When I founded SHJLPACK, I built it on this principle. A total solution is a promise that we are with you for the entire journey. Here is what that process should include:
- Consultation & Analysis: It starts with a conversation, not a sales pitch. We need to understand your coil sizes, your daily throughput, your factory layout, your manpower, and your biggest pain points.
- Customized Design: There is no "one-size-fits-all" in this industry. The solution should be tailored to you. This might mean modifying a standard machine or designing a completely custom line to fit your specific space and process flow.
- Layout Planning: We don't just send you a machine. We provide detailed drawings showing how it will integrate into your existing factory layout, ensuring a smooth flow of materials and people.
- Installation & Commissioning: Our engineers come to your site to ensure the machine is installed correctly, connected to your utilities, and running perfectly.
- Operator Training: We don't leave until your team is confident and competent in operating and performing basic maintenance on the new line.
- Lifetime Support: This is the most important part. When you have a question or need a spare part years down the road, you know who to call. The partnership doesn't end when the final payment is made.
The Danger of a 'Box-Dropper' Supplier
A supplier who just wants to sell you a standard machine without understanding your context is a huge risk. Their machine might be technically sound, but it may not solve your actual problem. It might be too fast for your upstream process, or too slow for your output, creating a new bottleneck. Integrating it with your existing conveyors could become a nightmare of custom fabrication and wiring. And when a unique issue arises, their support team will just read from a script because they have no real understanding of how you use the machine. This is how a machine that looked like a bargain on paper becomes an expensive, frustrating problem on your factory floor.
My Commitment to You
I started my career as an engineer on the factory floor. I know the pressure to meet production targets. Later, I founded and built my own successful packing machine factory. I faced every single one of these challenges myself. I achieved financial independence because of what this industry gave me. Now, my mission with SHJLPACK is to give back. I don't want to just sell you a machine. I want to share my knowledge and experience to help you avoid the mistakes I made. I want to be the partner I wish I had when I was starting out. When you work with us, you get more than just steel and motors. You get a dedicated team committed to your success.
Conclusion
Choosing the right coil packing line is about finding a solution that delivers the best ROI by solving your biggest problems—efficiency, safety, and product damage—within a partner-based, total solution approach.