Your steel wire rewinding line is a critical part of your operation. But often, it's stuck in a poorly lit corner of the factory. I’ve seen it many times. Operators squint to see what they're doing, and the whole process slows down. These aren't just small delays. They lead to slow setup times, incorrect winding, and serious safety hazards as workers strain to see fast-moving wire. This situation costs you real money, wastes valuable time, and puts your team at risk. There is a simple but very powerful upgrade that can fix this: integrating targeted LED lighting directly with your rewinding machines. It is a key step toward better efficiency and safety.
To improve steel wire rewinding machine efficiency in low-light environments, you should install high-quality, durable LED lighting systems directly onto or around the machinery. This provides focused, bright, and consistent illumination. Good lighting allows operators to monitor the process clearly, reduce errors, speed up changeovers, and significantly improve workplace safety.

I know what you might be thinking. "Lights? Is that really the solution?" As an engineer who has built and run a factory, I can tell you that it is. I've seen it firsthand in dozens of facilities just like yours. The right lighting is more than just a convenience. It is a fundamental part of a high-performance production line. Let’s break down exactly why this matters so much and how you can get it right.
Why is proper lighting so critical for steel wire rewinding operations?
You invested in a powerful rewinding machine. You expect a certain level of output. But it's not meeting your expectations, and you can't figure out why. Your operators, who are skilled people, are making simple mistakes. They struggle during threading, miss surface defects on the wire, or misread the control panel. The problem might not be the machine or the operator's skill. It could be something as basic as poor visibility. Thinking of lighting as a critical operational tool, not just an overhead expense, is the first step to solving this. Proper lighting directly improves your quality control, your operator's speed, and your factory's safety.
Proper lighting is critical for steel wire rewinding because it directly affects an operator's ability to perform essential tasks accurately and safely. Good lighting enables quick visual inspection for wire defects, precise machine setup, and accurate monitoring of the winding process. It also helps with the clear reading of controls. All of these things combine to reduce errors, prevent accidents, and maximize the machine's uptime.
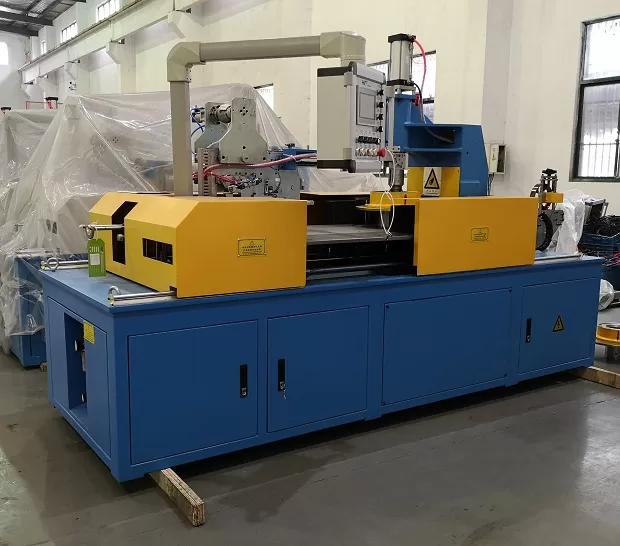
The Hidden Costs of Poor Lighting
When I visit factories, I often look for the hidden problems that drain profitability. Poor lighting is one of the most common ones. It creates costs that don't always show up on a spreadsheet until it's too late. Think about the specific tasks your operator performs on a rewinding machine every single day. Each one depends on clear sight.
- Threading the Wire: This is the first step in any job. In dim light, an operator has to fumble to guide the wire through a series of rollers and guides. This takes more time and increases the risk of mistakes that can damage the machine or the wire.
- Visual Quality Inspection: Your operator is your first line of defense against quality issues. They need to spot rust, scratches, or inconsistencies on the wire surface as it moves. In bad light, these defects are nearly invisible. The result is a bad coil that gets sent to a customer, leading to complaints and returns.
- Monitoring the Winding Pattern: A perfect, level wind is crucial for the next process. If the traverse guide isn't set up perfectly, you get uneven layers. An operator needs to see the coil building up in real-time to make adjustments. Shadows and dim light make this almost impossible.
Here is a simple breakdown of the difference it makes:
Task | Impact of Poor Lighting | Benefit of Good Lighting |
---|---|---|
Machine Setup & Threading | Slow, frustrating, high risk of errors. | Fast, accurate, reduced setup time by minutes per coil. |
In-Process Quality Checks | Defects are missed, leading to customer complaints. | Defects are spotted immediately, reducing scrap and rework. |
Monitoring Winding | Uneven winding, tangles, and poor coil shape. | Perfect, dense coils that are stable and easy to handle. |
Reading Controls/Gauges | Incorrect settings, misinterpreting warnings. | Clear readings, faster response to machine alerts. |
Beyond Visibility: The Psychological Impact
This is something many managers overlook. A poorly lit work area is depressing. It makes your team feel like their work area is an afterthought. I remember visiting a potential client's steel plant in Monterrey. Their rewinding section was in a dark, gloomy corner. The operators looked tired and morale was visibly low. They were making mistakes, and management was blaming them. I suggested that before they bought a new machine from me, they should try upgrading the lighting. They were skeptical but did it. Two months later, the manager called me. He said it was like having a new team. The operators were more alert, more engaged, and their error rate had dropped by over 20%. A well-lit space feels safer and more professional. It tells your employees that you care about them and their work environment. This simple change can boost concentration, reduce fatigue, and improve morale more than you can imagine.
What are the direct benefits of upgrading to LED lighting for your rewinding machines?
As a factory manager, you are constantly looking for investments that give you a clear return. Spending money on lighting might seem like a low-priority maintenance cost. It feels like just another expense. But what if that "cost" could directly reduce product defects? What if it could lower your energy bill and decrease the chance of a costly accident? Old, flickering fluorescent or dim high-pressure sodium lights are actively working against your production goals. They consume a lot of energy and provide poor-quality light. Upgrading to modern LED lighting is not a maintenance task. It is a strategic investment in efficiency, safety, and profitability with benefits you can actually measure.
The direct benefits of upgrading to LED lighting for rewinding machines include a big boost in energy efficiency, which leads to lower electricity costs. LEDs also offer a much longer lifespan and greater durability. This reduces your maintenance and replacement expenses. Most importantly, they provide superior light quality that makes things easier to see. This helps to decrease operator errors, reduce product waste, and improve overall safety in your plant.

Tangible ROI: Breaking Down the Numbers
As someone who built a factory from the ground up, I am obsessed with Return on Investment (ROI). Every dollar you spend must come back to you, preferably with friends. LED lighting is one of the easiest investments to justify because the numbers are so clear. Let's forget the technical jargon for a moment and talk about what this means for your factory's budget.
Your old metal-halide or fluorescent lights are energy hogs. They also generate a lot of heat, which is just wasted energy. In a hot climate like Mexico, that extra heat can even increase your facility's cooling costs. LEDs use a fraction of the power to produce the same, or even better, amount of light. This means an immediate and significant drop in your monthly electricity bill. Furthermore, the lifespan of an industrial LED is often 50,000 hours or more. A traditional bulb might last only a few thousand hours. This means you are not just saving on the cost of replacement bulbs; you are saving on the maintenance labor required to constantly change them, especially if they are in hard-to-reach places.
Here’s a practical comparison:
Feature | Traditional Lighting (e.g., Metal Halide) | Modern LED Lighting | Impact on Your Factory |
---|---|---|---|
Energy Use | High (e.g., 400W per fixture) | Low (e.g., 150W per fixture) | Drastic reduction in electricity costs. |
Lifespan | Short (10,000-20,000 hrs) | Very Long (50,000-100,000 hrs) | Fewer replacements, lower maintenance labor costs. |
Light Quality | Degrades over time, flickers. | Consistent, stable, flicker-free light. | Better visibility, fewer operator errors. |
Heat Output | Very High | Very Low | Safer to be near, may reduce factory cooling costs. |
Warm-up Time | Several minutes to reach full brightness. | Instant-on at full brightness. | No waiting, improved safety and productivity. |
The Safety Dividend
Now, let's talk about a return that is harder to put a price on but is incredibly valuable: the safety of your people. This is a huge concern for any manager like Michael. High accident rates lead to high insurance premiums and high employee turnover. Bad lighting is a direct contributor to workplace accidents. The flicker from old fluorescent bulbs can cause headaches and eye strain, making operators less attentive. Dim, shadowy areas hide tripping hazards like loose material or cords on the floor. On a rewinding machine, an operator needs to see moving parts, pinch points, and rotating equipment clearly. A moment of poor visibility can lead to a severe injury.
LEDs provide bright, even, flicker-free light. This instantly makes the work area safer. Operators can see potential hazards clearly and react faster. Better visibility reduces the physical and mental strain of a task, allowing them to stay focused and alert for longer. For me, investing in safety is always a wise decision. A single avoided accident can pay for the entire lighting upgrade many times over, not just in insurance costs, but in employee trust and morale.
How do you choose the right LED lighting for a harsh industrial environment?
You have decided to invest in LED lighting. That is a great decision. But a quick search online shows thousands of options, and it can be very confusing. Choosing the wrong type of light would be a complete waste of money. A standard LED light designed for an office or a store will not survive in your factory. The dust, vibration, potential for impacts, and temperature swings in a steel processing facility will cause it to fail quickly. You will be right back where you started, but with less money in your pocket. To avoid this, you need to select lighting that is specifically designed and built for industrial use. By focusing on a few key specifications, you can make sure your investment is durable, effective, and lasts for years.
To choose the right LED lighting for a harsh industrial environment, you must focus on key specifications. Look for a high IP (Ingress Protection) rating, such as IP65 or higher, to ensure it is protected against dust and water. Select fixtures that have a high IK (Impact Protection) rating for durability. Also, make sure they are rated for a wide operating temperature range and are certified as vibration-resistant.

Decoding the Specifications
When you look at industrial-grade lighting, you'll see a lot of codes and numbers. They might seem complex, but they are simple labels that tell you exactly what the light can handle. Knowing what they mean is essential for making a smart purchase.
IP Rating (Ingress Protection): This is one of the most important specs. It's a two-digit number. The first digit rates protection against solids (like dust), and the second digit rates protection against liquids (like water).
- IP65: The '6' means it's completely dust-tight. The '5' means it's protected against low-pressure water jets from any direction. This is a good minimum for a factory. It means you can wash down the equipment without worrying about the lights.
- IP67: This is even better. The '7' means the fixture can be temporarily submerged in water. This is excellent for environments with heavy wash-downs or high humidity.
IK Rating (Impact Protection): This tells you how much physical impact the light fixture can withstand. It's rated from IK00 (no protection) to IK10 (highly durable). In an environment with heavy machinery and moving parts, things can get dropped or bumped.
- IK08: This is a strong rating. It means the fixture can withstand an impact equivalent to a 1.7 kg mass dropped from 300mm. It protects against accidental bumps from tools or equipment.
Color Temperature (Kelvin) and CRI (Color Rendering Index):
- Color Temperature (K): This describes how "warm" or "cool" the light appears. For industrial tasks, you don't want a warm, yellow light (like 2700K). You need a neutral or cool white light, typically between 4000K and 5500K. This is similar to natural daylight and helps keep workers alert.
- CRI: This measures how accurately the light shows the true colors of objects. It's on a scale to 100. For general work, a CRI of 70 is okay. But for inspection tasks, where you need to see the difference between a shadow, an oil stain, and a spot of rust, you need a CRI of 80 or higher.
Mounting and Placement Strategy
Buying the right light is only half the battle. Where you put it is just as important. The goal is not just to make the area bright; it is to light the specific task your operator is performing. A common mistake is to hang a few big, powerful lights high up on the ceiling. This creates light, but it also creates shadows right where your operator needs to see.
A better strategy is to bring the light closer to the work. Think about mounting linear LED bars directly onto the machine's frame, aimed at critical areas like the traverse guide and the coil. You can use fixtures on articulated arms that the operator can move and position exactly where they need them. The key is to place lights in a way that eliminates shadows from the operator's body or from parts of the machine itself. A combination of general overhead lighting and specific, machine-mounted task lighting is the most effective solution.
My Take: It's Not Just About the Lights, It's About an Integrated System
Many factory managers I talk to see their problems in separate boxes. A slow machine is a machine problem. A safety issue is a training problem. An quality defect is an operator problem. But this way of thinking misses the bigger picture. Your factory is a single system where everything is connected. Adding a bright light to a poorly designed process is like putting a high-performance engine in a car with bad tires. You will get a small improvement, but you will not get the amazing results you are looking for. The real breakthrough happens when you stop seeing lighting as a simple add-on. You need to see it as an essential, integrated part of your machine's operational and safety system. This is the difference between a small fix and a true transformation of your production floor.
My core belief, based on my entire career as an engineer and factory owner, is that lighting should not be an afterthought. It should be a foundational component of your machine system design. The most effective solutions integrate task-specific LED lighting directly with the machine's controls and safety features. This creates an intelligent environment where light works with the machine. It can guide the operator, enhance safety interlocks, and provide clear visual feedback. This is how you turn a simple machine into a high-performance, safe, and efficient work cell. This is the philosophy behind our "TOTAL SOLUTION FOR WRAPPING MACHINE" slogan.
The SHJLPACK Philosophy: Intelligent Illumination
When we design a solution for a client, we don't just sell a machine. We analyze the entire process around it. With lighting, this means thinking beyond just brightness. We think about how light can actively help the operator and the machine work better together.
Imagine this for your rewinding line:
- Status Indication: The integrated LED lighting changes color based on the machine's status. A steady white light means normal operation. A flashing yellow light means the coil is almost full. A flashing red light, combined with an alarm, indicates an emergency stop or a fault. Your operator can understand the machine's status from across the room, just by looking at the light.
- Guided Operation: When the machine is stopped for a setup or coil change, a specific green or blue light automatically illuminates the exact path for threading the wire. It guides the operator's hands and eyes, making the process faster and error-proof.
- Dynamic Task Lighting: A linear LED light is mounted on a track that moves with the traverse guide. It always keeps the point of winding perfectly illuminated, with no shadows, allowing for constant quality control.
- Safety Interlocking: When a safety guard is opened, the main work lights turn off, and a bright red LED illuminates the hazardous area. This provides an unmissable visual warning that is much more effective than a small warning label.
This is what I mean by an integrated system. The lighting becomes part of the machine's PLC and its safety circuit. It's an active tool, not a passive utility.
A Story From My Factory
I want to share a quick story. When I was building my own packing machine factory, we faced this exact challenge. We had just invested in a brand-new, high-speed rewinder. But the output was disappointing. The operators were still slow during coil changes, which happened dozens of time a day. We could have blamed the operators. We could have called the machine supplier. Instead, we sat down and watched the process. The problem was visibility during the changeover.
So, we didn't just hang more lights from the ceiling. We brought our engineers and operators together. We designed a solution. We built low-profile, high-intensity LED bars directly into the machine's safety guarding. We linked them to the PLC. The moment the machine stopped for a coil change, the entire work area was flooded with bright, shadow-free light automatically. The result? The average time for a coil change dropped by 20% in the first week. That efficiency gain, repeated on every single shift, paid for the entire lighting project in less than three months. That is the power of an integrated, intelligent approach. It solves the real problem.
Conclusion
Integrated LED lighting is a strategic investment in efficiency, safety, and profit. Don't just add lights; integrate them into your system to truly transform your production line.