On any busy construction site, managing materials is a constant challenge. Piles of rebar, bundles of pipes, or coils of steel wire can quickly become a logistical nightmare and a serious safety hazard if not handled correctly. You're trying to keep the project moving, but manual bundling is slow, inconsistent, and physically exhausting for your crew. This leads to costly delays, wasted labor, and a high risk of injuries from loads that shift unexpectedly or from the repetitive strain of the work itself. A single poorly secured bundle can cause a major accident, damage expensive materials, and bring your entire operation to a halt. The pressure is immense. But what if you could automate this critical process, ensuring every bundle is secure, your team is safe, and your timeline is protected?
The primary benefits of using a steel wire strapping machine in construction are a significant boost in safety, a dramatic increase in operational efficiency, superior protection of materials to prevent costly damage, and streamlined logistics for easier transport and storage. These machines automate a labor-intensive process, creating a more productive and secure work environment.
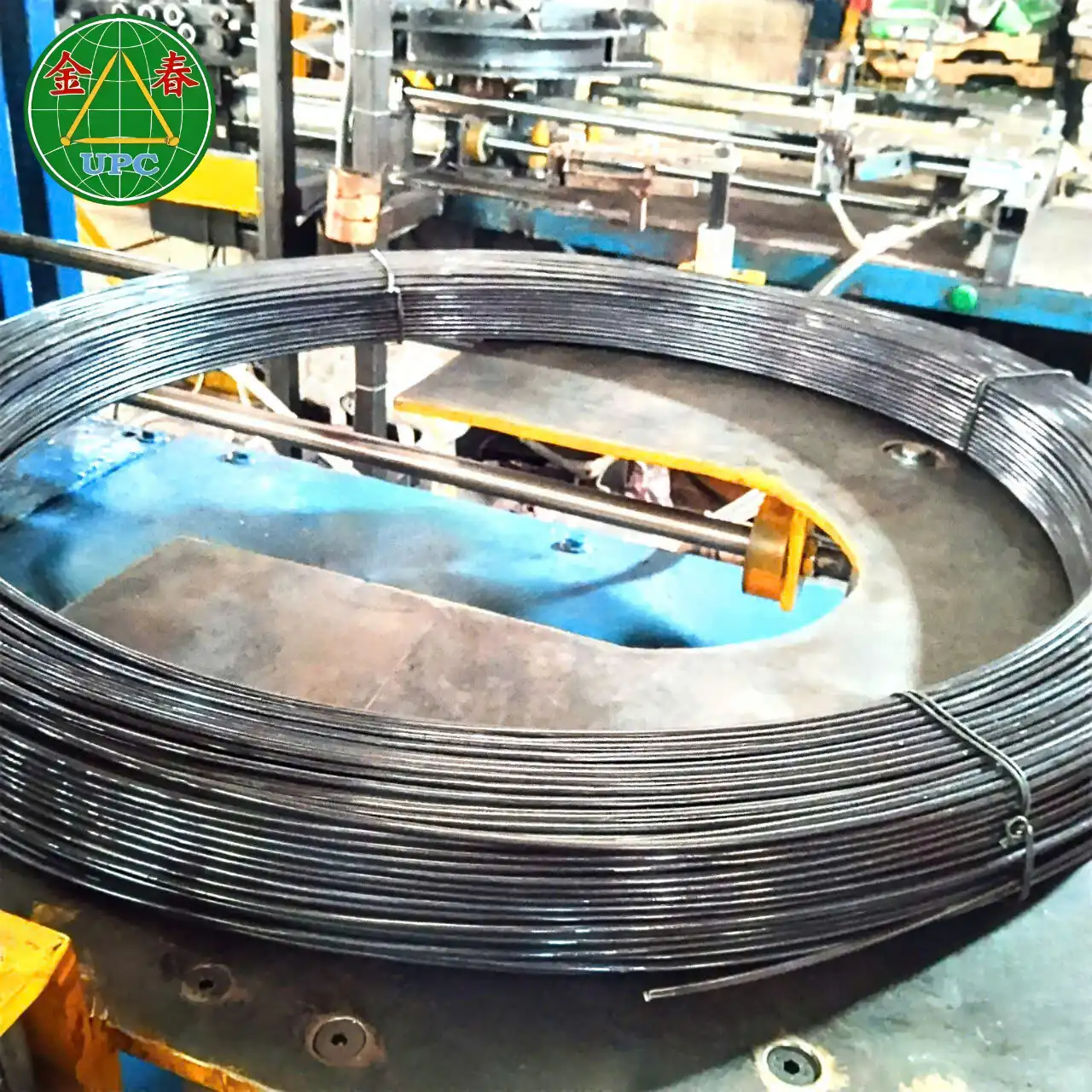
These benefits are not just small improvements; they represent a fundamental shift in how you can manage materials on site. By moving from manual labor to an automated solution, you address some of the most persistent problems in construction logistics. But to truly understand the impact, we need to break down each of these advantages. Let's look closely at how this technology specifically enhances safety, accelerates your project timelines, and protects your bottom line by eliminating material waste.
How Can Automation Improve Safety on a Construction Site?
Construction sites are filled with hazards, and material handling is one of the biggest sources of risk. Every time a worker has to manually lift, carry, or secure heavy and awkward materials like steel coils or rebar bundles, there's a potential for injury. We're talking about back injuries, deep cuts from strapping, or even crushing accidents. Think about one of your team members wrestling with a heavy bundle, trying to pull a strap tight with a manual tool. One slip, one moment of fatigue, and it can lead to a serious injury, triggering workers' compensation claims, project delays, and a loss of a valuable team member. This constant physical strain leads to exhaustion, and an exhausted worker is far more likely to make a mistake. The good news is that you can remove your team from this dangerous equation by automating the strapping process with a dedicated machine.
Automation drastically improves safety by taking over the most physically demanding and repetitive tasks, such as lifting, tensioning, and cutting steel straps. This removes the worker from direct contact with the most hazardous parts of the job, significantly reducing the risk of manual handling injuries like muscle strains, crush incidents, and cuts. The result is a fundamentally safer work environment for everyone on your team.

Deeper Dive: Pinpointing the Safety Gains
Let’s get more specific about how this automation translates into a safer site. The improvements are not just theoretical; they address concrete, everyday risks that managers like Michael Chen worry about constantly.
Eliminating Direct Physical Strain
The human body is not designed for the repetitive lifting and straining required to manually bundle heavy construction materials. This type of work is a primary cause of musculoskeletal disorders (MSDs), which includes everything from chronic back pain to shoulder and wrist injuries. A steel wire strapping machine does all the heavy work. The material is fed to the machine, which then applies the strap with thousands of pounds of force—a task that is impossible and dangerous to replicate manually. The operator simply pushes a button. This shift from intense physical labor to system supervision eliminates the root cause of many common construction site injuries.
Removing High-Risk Manual Actions
Beyond general strain, manual strapping involves several specific, high-risk actions. Tensioning a strap with a manual tool can be awkward, and if the tool slips, it can cause serious injury. Cutting steel straps creates incredibly sharp edges, leading to a high risk of deep lacerations. A fully automated machine contains these processes within a safety cage or guarded area. The tensioning, sealing, and cutting are all done mechanically, inside the machine, with no direct human interaction. This removes the risk of tool slippage, sharp edges, and unexpected load shifts during the securing process.
Creating a Controlled and Predictable Process
Humans get tired. They can get distracted. This variability can lead to inconsistent strapping—some too loose, some too tight. A loose bundle is a transport hazard, liable to shift or fall apart. A machine, on the other hand, is predictable. It performs the task the same way every single time, with the precise tension you set. This consistency creates a more controlled and reliable process, which is the foundation of a safe operation. You know every bundle leaving the machine is secured to the same high standard, eliminating the guesswork and human error that so often leads to accidents.
Safety Factor | Manual Strapping | Automated Strapping Machine |
---|---|---|
Ergonomic Risk | High (lifting, bending, pulling) | Low (supervisory role) |
Risk of Cuts | High (handling/cutting sharp straps) | Minimal (process is enclosed) |
Tensioning Hazard | Moderate (tool slippage, over-exertion) | None (automated mechanical process) |
Consistency | Low (depends on operator strength/fatigue) | High (precisely calibrated and repeatable) |
Worker Exposure | Direct physical contact with load | Indirect, from a safe distance |
What is the Impact of Efficient Strapping on Project Timelines?
In the construction world, time is money. Project delays are the biggest threat to profitability, and one of the most common and frustrating bottlenecks is material preparation and handling at the end of the line. When your crew and expensive equipment, like cranes and trucks, are sitting idle waiting for materials to be manually bundled and moved, the clock is ticking, and costs are piling up. This slow, manual process creates a serious ripple effect, delaying crane lifts, truck loading, and the final installation. You need your materials bundled and ready to go when they are needed, not an hour later. An efficient, automated strapping machine can break this bottleneck, speeding up your entire logistics chain.
Efficient strapping has a massive impact on project timelines by dramatically cutting down the time it takes to bundle and prepare materials for transport. This automation removes a major delay from your workflow, which leads to faster loading of vehicles, quicker movement of materials around the site, and ensures that your skilled crews are never left waiting for the supplies they need to do their jobs.

Deeper Dive: How Speed Translates to Profit
Let’s examine how this increased speed directly affects your project's schedule and budget. For a factory manager like Michael, who is under pressure to increase output, these efficiencies are not just nice to have; they are essential for growth.
From Hours to Minutes: Quantifying the Time Savings
The difference in speed between manual and automated strapping is staggering. Consider the process for a standard bundle of steel wire coils. A worker might take 10-15 minutes to locate the strapping, wrap it around the bundle, apply tension with a manual tool, seal it, and cut the strap. It's a multi-step, physically demanding process. An automated strapping machine can perform that entire cycle in under a minute. Now, multiply that time saving by the hundreds of bundles you process each week. The hours of labor saved are immense. This isn't just a labor cost saving; it's recaptured time that can be used for other productive tasks, directly increasing your plant's overall throughput without needing to hire more people.
The Ripple Effect on Site Logistics
The benefits of speed extend far beyond the strapping station itself. When bundles are prepared faster, the entire logistical chain moves more smoothly.
- Faster Loading: Trucks are not left waiting. Loading docks are cleared more quickly, allowing for more shipments per day.
- Optimized Crane Use: On a construction site, crane time is incredibly expensive. If bundles are ready and waiting, crane cycles can be tighter and more efficient, moving more material per hour.
- Simplified Inventory Management: With a consistent and rapid flow of bundled goods, tracking inventory becomes simpler. You reduce the chaotic piles of "work-in-progress" materials and create a more organized, streamlined flow from production to shipping.
This ripple effect means that an investment in one area—end-of-line packaging—can unlock efficiencies across your entire operation.
Process Step | Manual Strapping | Automated Strapping Machine |
---|---|---|
Preparation Time | 2-3 minutes (find tools, materials) | 0 minutes (machine is ready) |
Strapping Cycle | 5-10 minutes (wrap, tension, seal, cut) | < 1 minute (fully automated) |
Total Time per Bundle | ~10-15 minutes | ~1 minute |
Bundles per Hour | 4-6 | 50-60 |
Impact on Workflow | Creates a significant bottleneck | Creates a smooth, continuous flow |
How Does Proper Strapping Prevent Material Damage and Waste?
Nothing is more frustrating than having valuable materials damaged during transit or handling. When a bundle of steel arrives at its destination with scratches, dents, or other damage, it's a direct hit to your bottom line. I have talked to many factory managers who struggle with this. A steel coil with a dented edge might be rejected by the customer. A bundle of coated pipes with scratches might fail inspection. These problems often stem from improper strapping. If the straps are too loose, the materials can shift, rub against each other, and cause damage. If they're too tight, they can damage the product surface. It’s a constant battle that leads to customer complaints, wasted product, and lost profits. A professional strapping machine solves this by applying the perfect, consistent tension every time, creating a secure unit that protects the materials within.
Proper strapping prevents material damage by applying precise and consistent tension to create a tight, stable bundle. This controlled pressure stops individual items like pipes, coils, or bars from shifting, vibrating, or rubbing against each other during transport and handling. Since movement and friction are the primary causes of scratches, dents, and surface damage, a well-strapped bundle is a well-protected bundle.

Deeper Dive: The Economics of Damage Prevention
Preventing product damage goes straight to your profitability. For an operations director like Michael, reducing product loss is just as important as increasing production speed. Let's analyze how a machine accomplishes this.
The Science of Load Securement
Securing a load properly is about more than just wrapping a strap around it. It's about applying the right amount of tension to create a unified, stable mass. Manual strapping is highly inconsistent. The tension applied depends on the operator's strength, the tool they are using, and even how tired they are. The result is that some bundles are too loose and others are too tight. A strapping machine is engineered for precision. You can set the exact tension required for your specific product, and the machine will apply that same tension to every single bundle, without fail. This scientific approach to load securement eliminates the inconsistencies that lead to damage.
Protecting High-Value and Sensitive Materials
This is especially critical for finished or sensitive products. Think about architectural steel, pre-painted panels, or high-grade steel wire. The surface finish is part of the product's value. Even minor scratches or dents can lead to rejection by the client. A properly secured bundle from an automated machine ensures there is no internal movement. The items are held firmly in place, protecting them from the vibrations and shocks that are inevitable during shipping by truck, train, or sea. It's an insurance policy for the quality of your product, ensuring it arrives at its destination in the same condition it left your factory.
Reducing the Indirect Costs of Waste
The cost of a damaged product is not just the value of the material itself. The indirect costs are often much higher.
- Replacement Costs: You have to produce the order again, consuming more raw materials and production time.
- Shipping Costs: You have to pay to ship the replacement order.
- Labor Costs: Your team has to spend time dealing with the damaged goods, processing the complaint, and handling the new order.
- Reputation Damage: Most importantly, frequent damage issues can harm your relationship with your clients and damage your company's reputation for quality and reliability.
By investing in proper strapping, you are not just saving material; you are protecting your entire business from these cascading costs.
Damage Cause | Manual Strapping | Automated Strapping Machine |
---|---|---|
Inconsistent Tension | Common (leads to shifting or crushing) | Eliminated (precise, repeatable tension) |
Product Shifting | High risk if strap is too loose | Minimal risk due to secure bundling |
Surface Damage | High risk from friction/vibration | Low risk as movement is prevented |
Operator Error | A significant factor | Not a factor in the strapping process |
Why is Choosing the Right Supplier as Important as the Machine Itself?
So, you have analyzed the benefits and decided to invest in an automated strapping machine. That's a great first step. But now you face another critical decision: which supplier to choose? It can be tempting to just look at price tags, but I can tell you from experience that this is a huge mistake. I've spoken with many factory managers like Michael Chen who have been burned by this approach. They bought a machine from a supplier who was great at making the sale but disappeared when it came time for installation, training, or service. A cheap machine that breaks down constantly or doesn't truly solve your problem quickly becomes the most expensive piece of equipment you own. You are not just buying a machine; you are investing in a long-term solution. You need a partner, not just a seller.
Choosing the right supplier is critical because a machine is only as good as the expertise and support that stand behind it. A true partner provides a total solution. They start by understanding your unique operational challenges and then help configure the right equipment. They support you through installation, training, and provide reliable after-sales service to ensure your investment delivers long-term value and a strong return.
Deeper Dive: My Insights on Finding a True Partner
This is a topic I feel very strongly about, because it's at the core of why I started SHJLPACK. It's about more than just machinery; it's about sharing knowledge and building success together.
My Journey: From Engineer to Factory Owner
I wasn't always a machine builder. I started my career as an engineer on the factory floor. I know the daily pressure to meet production targets. I understand the frustration of dealing with equipment that isn't reliable and the constant worry about safety. I lived those challenges. When I took the leap and founded my own packing machine factory, I was on the other side, but the goals were the same. I had to build a successful business, and that meant every single machine had to be efficient, durable, and solve a real-world problem. My journey gave me a unique perspective. I don't just see a client; I see a fellow manager like Michael, and I understand the weight on his shoulders. This experience is the foundation of our slogan: "TOTAL SOLUTION FOR WRAPPING MACHINE." It’s a promise based on lived experience.
The Difference Between a Seller and a Partner
A seller is focused on one thing: closing the deal. They will show you a brochure, a list of features, and a price. Their job is to sell you a box. A partner starts the conversation differently. A partner asks questions: "What are your biggest production bottlenecks? What are your safety concerns? What kind of product are you handling? Let's talk about your current process." I remember a client in the steel industry who was experiencing damage to the edges of his steel coils during packing. A typical seller would have offered a standard wrapping machine. I went to his facility. I watched his process. We realized the problem wasn't just the wrapping; it was how the coils were being handled before and after. We designed a solution with a modified in-feed conveyor and a gentler off-loading system. That is the difference. That is what a "total solution" really means. It’s about solving the entire problem, not just one part of it.
What to Look for in a Supplier
When you evaluate a potential supplier, look beyond the machine itself. Look at the people and their experience.
- Do they have deep industry knowledge? Can they talk intelligently about your specific challenges in the steel or construction industry?
- Can they provide real case studies? Ask for examples of how they helped other clients with similar problems.
- What is their after-sales support plan? Ask them what happens when you have a problem. Who do you call? What is their response time? A machine is a long-term investment, and you need a partner who will be there for the entire journey.
My mission with SHJLPACK is to give back to the industry that gave me so much. I want to use my experience to help others avoid costly mistakes and build safer, more profitable operations. Choosing the right partner is the most important step in that process.
Supplier Type | The "Box Seller" | The "Solution Partner" |
---|---|---|
Focus | Making the sale, price point | Solving your specific problem |
Process | Shows you a product catalog | Asks questions, analyzes your workflow |
Expertise | General sales knowledge | Deep, hands-on industry experience |
Solution | Sells you a standard machine | Designs a customized, integrated solution |
After-Sales | Limited or hard to reach | A core part of the commitment |
Relationship | Transactional | Long-term partnership |
Conclusion
Ultimately, a steel wire strapping machine is more than an upgrade. It's a strategic investment in safety, efficiency, and the long-term health of your construction business.