Your steel wire coiling line runs every day. You see the output numbers, and they seem fine. But there's a nagging feeling that you could be doing better. You worry about the hidden problems you can't see and the sudden breakdowns that always seem to happen at the worst possible time. An unexpected stop on the production line creates chaos. The pressure builds, costs climb, and customers get impatient. You know that small inefficiencies, tiny delays, and minor quality issues are adding up, slowly eating away at your profits. What if you could see exactly what’s happening inside your machines, in real-time? This is what a good monitoring system does. It gives you the power to stop guessing and start making decisions based on solid data.
To enhance steel wire coiling machine performance, you must implement a real-time monitoring system. This system actively tracks essential operational data such as production speed, wire tension, motor temperature, and vibration levels. This allows you to identify production bottlenecks, predict maintenance needs before a failure occurs, and optimize the entire coiling process for maximum efficiency and minimal downtime.
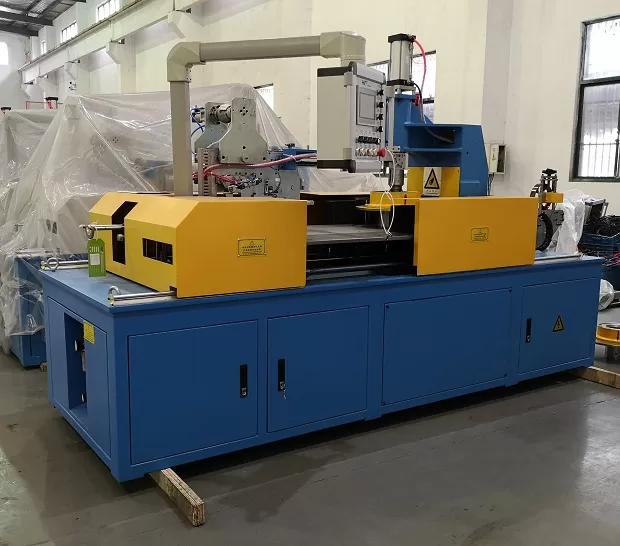
This might sound complex, but the idea is simple. It's about giving your machines a voice so they can tell you what they need. As an engineer who has built a factory from the ground up, I've learned that listening to your equipment is the key to a smooth and profitable operation. Let's dig into the practical side of this and explore what you should be looking at and why it matters so much to your bottom line.
What Key Metrics Should You Track with Real-Time Monitoring?
You've decided that monitoring your equipment is the right move. That's a great first step. But now you face a new problem: what data is actually important? It's easy to get overwhelmed by endless charts and numbers. Tracking the wrong metrics is just as useless as tracking nothing at all. You can end up with a flood of information but no clear path to action. This leads to frustration and makes you question the investment. The key is to ignore the noise and focus only on the data that directly impacts your factory's performance, quality, and costs.
For a steel wire coiling machine, you should focus on four primary types of metrics: production output, machine uptime, wire tension consistency, and key component health indicators like motor temperature and vibration. These metrics give you a complete and actionable overview of your machine's efficiency, the quality of your product, and its overall mechanical condition.
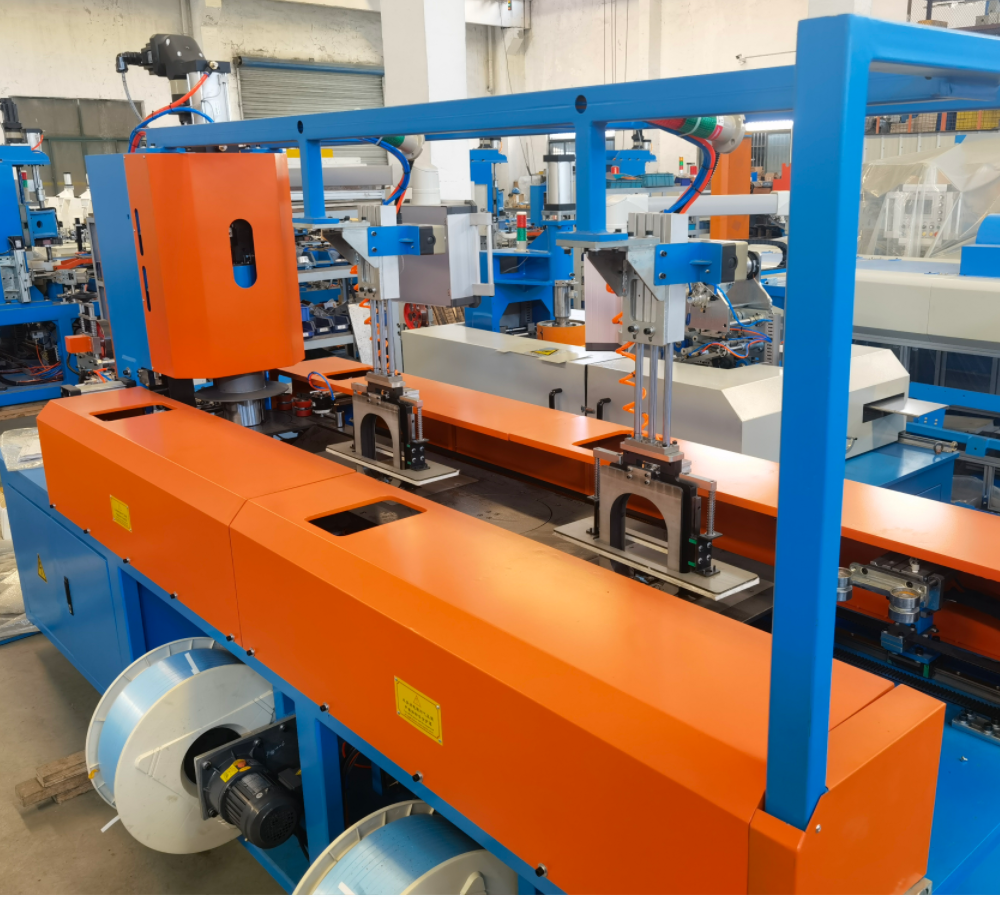
When I first started my own factory, I made the mistake of only focusing on one thing: coils per hour. It seemed logical. But I was ignoring the signals the machine was sending me. I learned the hard way that a holistic view is necessary. To truly understand performance, you need to look deeper.
Operational Efficiency Metrics
These metrics tell you how productive your machine is. They are the numbers that most managers look at first, but they need context from other data points.
- Production Rate (Coils/Hour): This is the most basic measure of output. A real-time tracker helps you see if your speed is consistent or if it drops during certain shifts or with specific materials.
- Machine Uptime/Downtime: This is more important than just speed. A machine that runs fast for an hour and then is down for two is not efficient. Monitoring uptime helps you see the true availability of your machine. You can tag reasons for downtime (e.g., 'material change,' 'mechanical fault') to identify recurring problems.
- Cycle Time: This is the total time it takes to produce one complete coil, including winding, cutting, strapping, and ejecting. Analyzing cycle time helps you pinpoint the slowest part of your process.
Product Quality Metrics
Bad coils are wasted money and can damage your reputation with customers. These metrics help you ensure every coil meets specifications.
- Wire Tension: This is critical. If tension is too low, the coil can be loose and telescope during handling. If it's too high, it can stretch the wire or even cause it to break, leading to dangerous situations and downtime. Real-time monitoring ensures tension stays within the perfect range.
- Coil Dimensions (Width/Diameter): A sensor can verify that each coil is the correct size. This automated check is far more reliable than manual spot-checks and prevents out-of-spec products from ever reaching the shipping dock.
Machine Health and Safety Metrics
These are the predictive metrics that save you from catastrophic failures and improve safety. They are your early warning system.
- Motor Temperature and Amperage: An overheating motor or one that is drawing too much current is a clear sign of strain. It could be due to poor lubrication, a worn-out bearing, or a problem with the material feed. Catching this early prevents motor burnout.
- Vibration Analysis: Every machine has a normal vibration signature. When a component like a bearing or a gear starts to fail, the vibration pattern changes. A sensor can detect this subtle change long before the human eye or ear can, giving your maintenance team weeks to prepare.
Here is a simple way to look at how these metrics connect:
Metric Category | Key Data Point | What It Tells You |
---|---|---|
Operational Efficiency | Production Rate | Are we meeting our output targets? |
Uptime vs. Downtime | How much time are we losing to stops? What are the main causes? | |
Product Quality | Wire Tension | Is our product consistent and stable? Are we at risk of telescoping or breaks? |
Coil Dimensions | Is every coil meeting customer specifications? | |
Machine Health | Motor Temperature/Amps | Is the machine's main driver under stress? Is a failure imminent? |
Vibration Levels | Are mechanical components like bearings and gears wearing out? |
By tracking these specific things, you move from just seeing the final output to understanding the entire process. This understanding is what allows you to make small adjustments that lead to big improvements in performance and profitability.
How Does Real-Time Data Prevent Unscheduled Downtime?
There is nothing worse for a factory manager than a sudden, unexpected machine breakdown. The entire production line grinds to a halt. Your team is standing around, unable to work. Deadlines are now at risk, and you know that every minute of downtime is costing you money. The stress is enormous because everyone is looking to you for a solution. But what if you could know that a failure was likely to happen days, or even weeks, before it did? That is the true power of real-time data.
Real-time data prevents unscheduled downtime by enabling predictive maintenance. Instead of reacting to failures after they happen, monitoring systems track machine health indicators like vibration, temperature, and power usage. When the data shows a deviation from the normal baseline, it signals that a component is starting to wear out, allowing you to schedule a repair during planned maintenance before a catastrophic failure occurs.
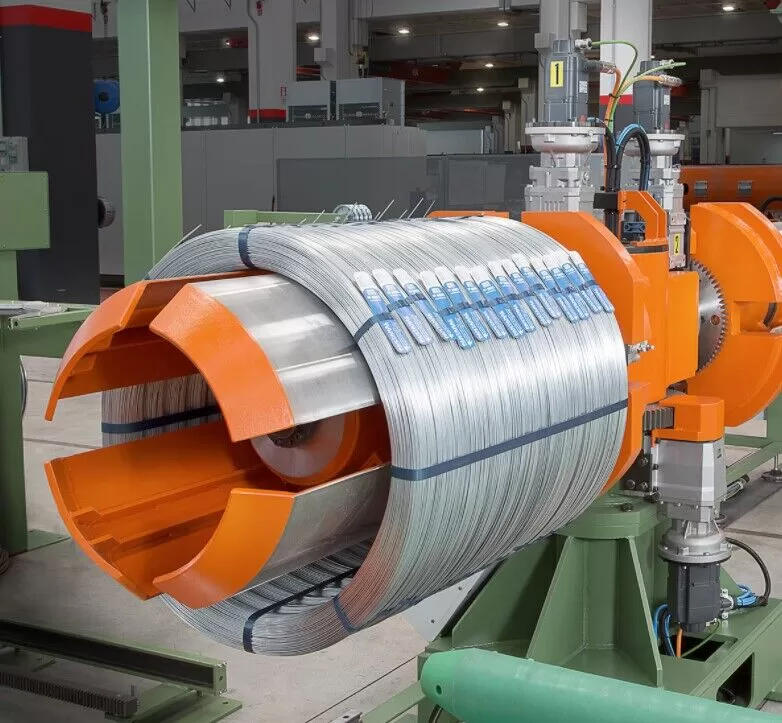
I remember a client, let's call him Michael, who ran a large steel processing facility. He was constantly fighting fires. His maintenance strategy was "if it ain't broke, don't fix it." As a result, a critical gearbox on his main coiling line failed without warning. The line was down for three days while they waited for a replacement part from overseas. The cost was astronomical, not just in repairs but in lost production and penalty clauses from his customers. After that incident, we worked together to install a monitoring system. Six months later, the system alerted him to rising vibration levels in a motor on another line. They inspected it during the next planned weekend shutdown and found a bearing that was about to disintegrate. A simple, low-cost repair prevented another three-day disaster. He shifted his entire maintenance philosophy after that.
Shifting from Reactive to Predictive Maintenance
Most factories operate on a reactive or preventive maintenance schedule.
- Reactive Maintenance: You fix things when they break. This is the most expensive and disruptive approach.
- Preventive Maintenance: You replace parts on a fixed schedule, whether they need it or not. This is better, but you often waste money by replacing perfectly good components or miss a part that fails prematurely.
- Predictive Maintenance (PdM): You use real-time data to predict when a part will fail and fix it just in time. This is the most cost-effective and efficient method. It maximizes component life without risking unexpected failures.
Identifying the Early Warning Signs of Failure
Your machines are constantly communicating. You just need the right tools to listen. Real-time sensors act as your ears, picking up on signals that are invisible to humans.
- Increased Vibration: This is often the first sign of a mechanical problem. It can indicate imbalance, misalignment, or wear in bearings and gears. A monitoring system can tell the difference between normal operational vibration and the unique signature of a developing fault.
- Rising Temperatures: Overheating is a clear sign of trouble. It can be caused by friction from worn parts, poor lubrication, or an electrical issue. An infrared sensor can spot a hot spot on a motor or gearbox long before it becomes critical.
- Changes in Power Consumption: A motor that suddenly starts drawing more electrical current to do the same amount of work is struggling. This indicates increased load, which could be from mechanical friction or a problem in the process itself.
Here’s a breakdown of common failures and the data that predicts them:
Potential Failure | Early Warning Sign (Data) | Actionable Insight |
---|---|---|
Bearing Failure | Gradual increase in high-frequency vibration. | Schedule bearing replacement at the next planned stop. |
Gearbox Wear | Specific vibration patterns and metal particles in oil. | Inspect gearbox and change oil. Plan for a rebuild if necessary. |
Motor Burnout | Consistently rising temperature and current draw. | Check for overload, poor ventilation, and electrical faults. |
Hydraulic System Leak | Drop in system pressure and increased pump cycle time. | Inspect hoses, fittings, and seals for leaks. |
Wire Breakage | Spikes in wire tension readings. | Check wire quality, decoiler, and tensioning system for issues. |
By using data to predict failures, you take control of your maintenance schedule. Downtime becomes a planned, efficient activity, not an emergency. This builds reliability into your entire operation and transforms your maintenance team from a fire-fighting crew into a proactive force for stability.
Can Real-Time Monitoring Improve Safety and Reduce Product Damage?
As a manager, you are responsible for your people's safety. You see them working hard around heavy, powerful machinery, and you know the risks involved. A single accident can have a devastating impact on an employee and their family, while also leading to high insurance costs, investigations, and a drop in team morale. At the same time, you have to protect your product. Coils that are damaged during the wrapping process due to improper tension or handling result in customer complaints, rework, and direct profit loss. These two issues—safety and product quality—are directly linked.
Yes, a real-time monitoring system significantly improves workplace safety and reduces product damage. It acts as a vigilant watchdog, alerting operators to unsafe conditions like excessive wire tension that could cause a dangerous snap. Simultaneously, it ensures consistent coiling parameters, which protects the integrity of the product by preventing common defects like edge damage and loose, unstable coils.

I've been in factories where the fear of an accident was palpable. Workers were hesitant and slow when handling heavy coils manually because they had seen colleagues get hurt. This is where automation guided by data makes a huge difference. I worked with a company that was struggling with high rates of back injuries from operators trying to manually adjust heavy coils. We installed an automated coiling line with sensors that monitored the coil's shape and position. The system automatically made micro-adjustments, ensuring a perfect coil every time. Not only did their product damage rate fall to nearly zero, but their injury reports also plummeted. The team was more confident, and the entire atmosphere on the factory floor improved.
Creating a Safer Work Environment
A monitored machine is a safer machine. The system is always watching for conditions that could lead to an accident, acting faster than a human ever could.
- Preventing Wire Snaps: One of the most dangerous events on a coiling line is a wire snapping under tension. It can whip out and cause serious injury. A real-time tension monitoring system can automatically slow or stop the machine if tension exceeds the safe limit, preventing the break from ever happening.
- Automating Dangerous Tasks: Monitoring is the brain behind automation. When sensors can confirm the position and status of a coil, you can use automated systems for tasks like cutting, strapping, and moving the finished coil. This removes the need for operators to place their hands near dangerous moving parts.
- Monitoring Guards and Sensors: The system can be configured to ensure all safety guards are in place and emergency stop sensors are functional before a machine will start. This provides a digital, foolproof checklist that enhances existing safety protocols.
Protecting Your Product Integrity
Every damaged coil is a loss. Real-time data helps you achieve a perfect coil, every time.
- Consistent Winding: The system maintains perfect tension and speed, creating tightly and evenly wound coils. This prevents "telescoping," where the center of the coil pops out during transport, and protects the delicate edges of the steel from being damaged.
- Error Detection: If the system detects an issue, like an inconsistent wire diameter from the supplier, it can flag the coil for inspection or stop the line. This prevents you from wasting time and energy wrapping a defective product.
- Traceability: Data from each coil (e.g., its production time, tension profile, final weight) can be logged. If a customer reports a problem, you can go back and look at the exact data from its production run to diagnose the issue. This helps resolve claims and improve your process for the future.
Here is a clear connection between the data you monitor and the problems you solve:
Problem to Solve | Monitored Data Point | How It Solves the Problem |
---|---|---|
High risk of worker injury | Wire Tension, Safety Guards | Automatically stops the machine in over-tension situations and ensures safety systems are engaged. |
Product damage (telescoping) | Winding Tension & Speed | Maintains consistent, even winding to create stable, dense coils that hold their shape. |
Customer complaints about quality | Coil Dimensions, Weight | Ensures every coil meets exact specifications before it leaves the factory. |
Inefficient manual handling | Coil Position & Status | Enables automation of handling and transport, reducing manual labor and the risk of drops. |
By using real-time data, you are not just making your process more efficient; you are building a fundamentally safer and more reliable operation. This reduces costs associated with accidents and product loss, and it creates a better, more secure environment for your entire team.
What is the Most Overlooked Aspect of Implementing a Monitoring System?
So, you've done your research. You've invested in a state-of-the-art monitoring system. The dashboards are live, displaying beautiful charts and real-time data from your coiling line. You feel a sense of accomplishment. But then, a few weeks or months go by, and you realize something frustrating: nothing has really changed. Production numbers are the same. The same minor issues keep popping up. Your team seems to be ignoring the alerts. The big ROI you were promised feels like a distant dream. This is an incredibly common trap, and it's the point where many great technology projects fail.
The single most overlooked aspect of implementing a real-time monitoring system is the human element. The technology itself is just a tool. Without properly training your operators and maintenance teams on how to understand the data, and, more importantly, empowering them to take action based on it, the system is nothing more than an expensive set of digital decorations on the factory wall.
I've seen this happen firsthand. Early in my career as a factory owner, I was convinced that technology was the answer to everything. I installed a sophisticated system and expected my team to immediately use it to solve problems. I was wrong. I would walk the floor and see alerts on the screen that had been ignored for hours. I got frustrated. I called a meeting and asked my lead operator why he wasn't stopping the line to fix the tension issue the system was flagging. His answer was a huge lesson for me. He said, "Vincent, you told us our main goal was to hit 50 coils per shift. If I stop the line to make a small adjustment, I might miss that target. No one ever told me that responding to these alerts was more important." He was absolutely right. I had given them a powerful new tool but had failed to change the culture or the instructions to support it.
It's About People, Not Just Pixels
The data on the screen is useless until a person uses it to make a decision. The goal isn't to generate charts; the goal is to trigger actions.
- Ownership: Who is responsible for watching the data? Is it the operator? The shift supervisor? The maintenance team? You must clearly define roles. For example, the operator is responsible for real-time alerts related to quality (like tension), while the maintenance team is responsible for long-term health alerts (like vibration).
- Understanding "Why": Don't just show your team a graph. Explain what it means. "When this vibration number goes up, it means the bearing is wearing out, and if we catch it now, we can fix it in 30 minutes. If we wait for it to fail, the line will be down for a full day." Context makes the data meaningful.
Building a Data-Driven Culture
You have to change the way your team thinks about their jobs.
- Empowerment: You must give your team the authority to act. If an operator sees a quality alert, they need to feel empowered to pause production and fix it without fear of being punished for "slowing down." This requires a shift from a "production at all costs" mindset to a "quality production at all costs" mindset.
- Incentives: Align your team's goals with the data. If your goal is to reduce downtime, then reward the maintenance team for the number of predictive repairs they complete, not just how fast they fix things that are already broken.
- Feedback Loop: Create a process for reviewing the data. Hold a brief meeting at the start of each shift to look at the key metrics from the previous shift. What went well? What alerts came up? What did we learn? This makes using the data a daily habit.
A Simple Action Plan for Your Team
- Assign Roles: Clearly state who owns which metric.
- Train on "What If": Go through scenarios. "What do you do if you see this alert?"
- Set New Rules: Create simple, clear rules. "If tension alert is red for more than 1 minute, pause the line and notify the supervisor."
- Celebrate Wins: When the team uses data to prevent a failure, celebrate it. Share the story. Show everyone the value of their vigilance.
The technology is the easy part. Changing habits and building a culture of proactive ownership is the real work. But when you get it right, that's when you unlock the true power of real-time monitoring.
Conclusion
Real-time monitoring transforms your coiling line from a black box into an open book. It boosts performance, prevents costly downtime, and improves safety for your team.